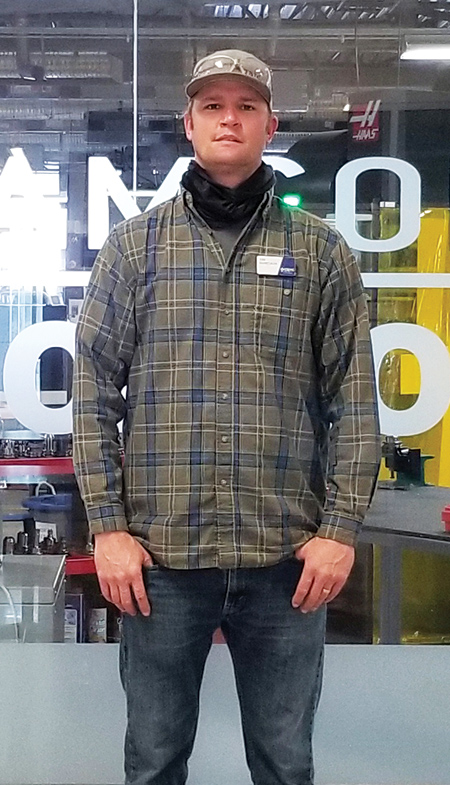
Tim Hemesath, Instructor, Precision Machining Technology Department, Texas State Technical College
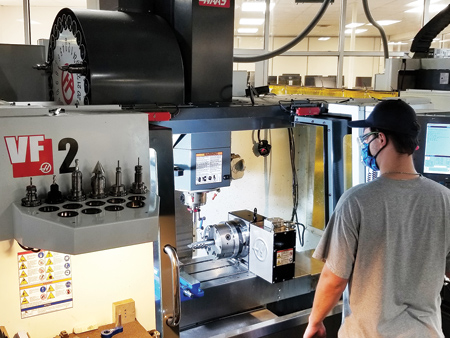
Student Camden Henry checks a part on a CNC machining center
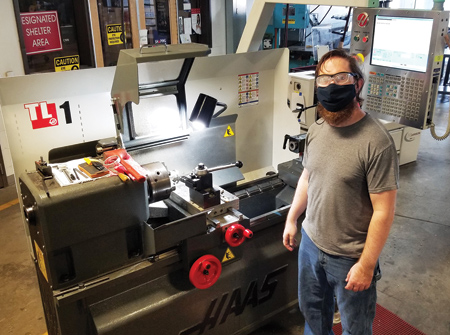
Student Brian Gannon works on a part on a CNC lathe
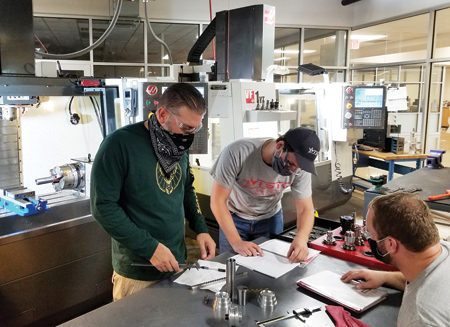
Students Camden Henry, Brian Gannon and Travis Miller compare notes for one of their CAD/CAM projects
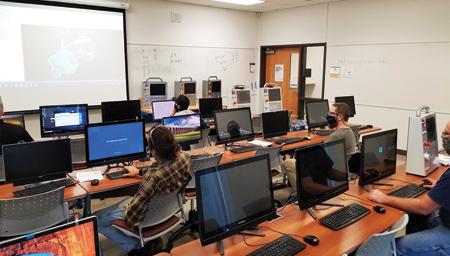
CAD/CAM lab at Texas State Technical College
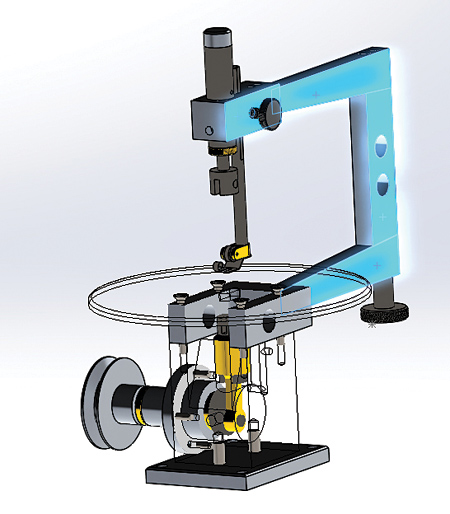
Screen shot of a second and third semester project, designed to display the students' machining skills
While COVID-19 may have shuttered many institutions and caused severe crimps in the learning curve at countless others, the Precision Machining Technology program at Texas State Technical College (TSTC), just north of Austin, has been able to develop a hybrid solution that has kept the machines humming and students learning throughout the pandemic. "We all realized pretty quickly that we had to work out a way to bring the students into the lab," said Instructor Tim Hemesath. "When it comes to machine tools, it is just like learning to ride a bicycle. You will never learn just by watching someone else do it. You have to get up on that bike and ride it yourself."
As for the "bikes," at TSTC, they have a full complement of manual mills and lathes, as well as rows of Haas CNC machining and turning centers. Because so much of the program centers on learning CAD/CAM systems, the lab offers 20 seats of Mastercam and SOLIDWORKS. "We split the class of 28 students into two groups of 14," said Hemesath, "to alternate in-home and in-lab days. They can do a lot of their CAD/CAM practice on their laptops at home, and on the days they come into lab, we all wear our face masks and practice social distancing. We are fortunate that when the machine tools were set up, they all happened to be anchored at least six feet apart. In the CAD/CAM area, we can plug the laptops and individual computer seats into a large screen so, again, we are socially distanced."
Hemesath has been teaching at TSTC for two years now but brings 19 years of experience into the classroom. Following his own graduation from TSTC in 1999 with an associate degree in mechanical engineering and a certificate in machining, Hemesath held several positions in manufacturing plants, including that of supervisor of 5-axis machining in a company that produced semiconductors. "I was looking for a change in environment," said Hemesath. "When I found out there was an opening for an instructor in the Precision Machining Technology program at TSTC, I jumped at the chance. There has not been one moment of regret for my decision. I have been able to couple my own experience with the latest teaching steps in the promotion of automated machining."
Students in Hemesath's classes range in age from recent high school graduates to people in their 40s and 50s looking to add to their skill set or even completely change careers. "We have companies of all sizes in our area, manufacturing a wide range of components and products in electronics, aerospace, medical device and even automotive industries," said Hemesath. "Tesla recently announced they are building a mega-plant in our neighborhood that will employ upwards of 5,000 people. We have an advisory board located in the college's Waco facility that provides guidance for our curriculum. They pass along the latest information regarding equipment we should be training on and the latest CAD/CAM capabilities needed in their plants."
The program starts out with manual machining for the first 15-week semester. This gives the students the ability to "feel" the relationship between the tool and the workpiece. "They get comfortable reading the dials for the X and Y axes," said Hemesath. "We also have some manual machines with digital readouts (DROs) so they can learn how to set datum points."
In the second semester, students get into the fundamentals of CNC controls. "We show them how to set G-codes that tell the machine where and how to move," said Hemesath, "as well as what H (tool length offset) and D (tool diameter offset) values stand for, and how to set multiple work offsets. Then we go into programming some 2D parts so they can understand the machine language and they are able to trouble shoot the program at the controls if they need to ramp the RPMs up, or slow down the feedrates, or increase the depth of cut for a drill, things like that. What they are doing is taking what they have learned on the manual equipment and bringing it into the CNC equipment. It is the start of a good understanding of the benefits of automated manufacturing."
During this semester, the students also begin learning SOLIDWORKS for their design work. "We take them from designing a simple extrusion to a simple protrusion," said Hemesath, "and progress all the way up to a full 3D assembly that they are required to make by the end of the third semester of the curriculum."
In the following semesters, the students really get into the "nuts and bolts" of CAD/CAM. "Their designs are imported into Mastercam to create the toolpaths that will be followed by the machine tools," said Hemesath. "I began using Mastercam for toolpaths back in 1999 in the various industries I worked in, and it is the software I use with my students. It makes sense to teach them the software they will probably be using once they graduate. To start, I set them up with the user interface. They click on the Mastercam icon and determine if the part is going to be a mill part, lathe part or both, and which operation needs to be done first to get the part complete and to specification."
"We also go into drafting, the views, the grids and show the axes," he continued. "The Work Coordinate System 9 (WCS) with Mastercam's Dynamic Machining goes over really well with the students. They can create a cross-section of a part, rotate it to the correct orientation, and then choose that plane in their parameter folder for the toolpath manager."
In the fourth semester, everything is brought together in a Machine Design course that Hemesath said is a capstone course for the students. "They are put together into project groups," he said," and they decide who will be the project manager, the designers and the programmers. They come up with ideas, based on their various hobbies, for complex assemblies. One example is a working gyroscope. While some of the parts are done on the manual lathes and mills, to prove retention of their manual skills, those to be done on the CNC machines are designed in SOLIDWORKS, imported into Mastercam, verified for fit, form and function, and machined on either a CNC mill or CNC lathe, with tolerances held to within two to five tenths. When you consider the 15-week time constraint we have to get the parts completed, Mastercam has really allowed us to nail it. Mastercam's Dynamic Machining features result in parts being made quickly and accurately by the students, while giving us a substantial saving in tooling. Without Mastercam, a lot of the projects the students depend on for their capstone grade would not be able to be completed."
Leaving TSTC with either an associate degree or certificate in precision machining technology, graduates quickly earn jobs within the many manufacturing companies in the area. "We have 95% placement success," said Hemesath, "with many of our students being offered jobs even before they graduate."
For more information contact:
Texas State Technical College
1600 Innovation Blvd. (CR 108)
Hutto, TX 78634
512-759-5900
www.tstc.edu
CNC Software, Inc.
671 Old Post Road
Tolland, CT 06084
800-228-2877
info@mastercam.com
www.mastercam.com