
Machining out the "cage" of a 718 Inconel Type "H" Style Back Pressure Valve, one of the last operations before the part is completed. This is performed on Cleveland Machine's Okuma MB-56VB with the rotary.
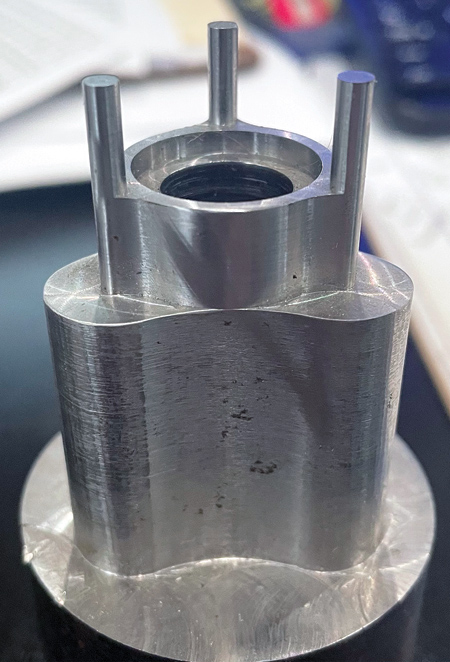
Parts Programmed in ESPRIT
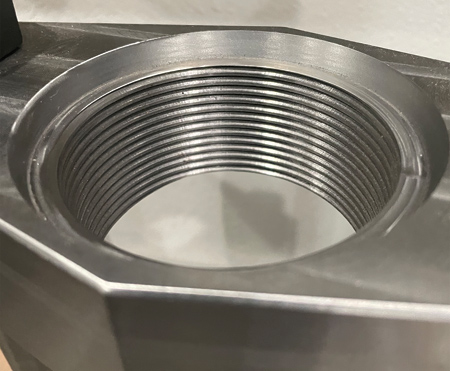
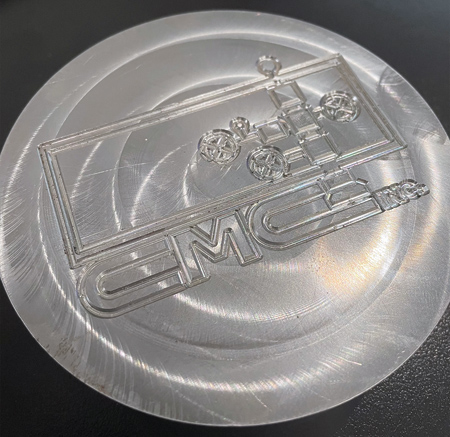
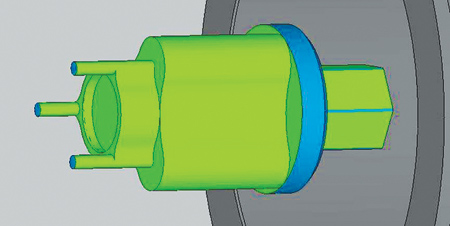
Milling contoured surfaces with the Okuma LB3000MYW Mill Turn. "ESPRIT allowed us to quickly create a program to produce these one-off parts for a local rancher," said Cleveland Machine Plant Manager, John Buckaloo. "He needed this tool and it was no longer being produced. We took a few measurements, created a solid model and produced the part in a matter of hours. This would not have been doable without ESPRIT."
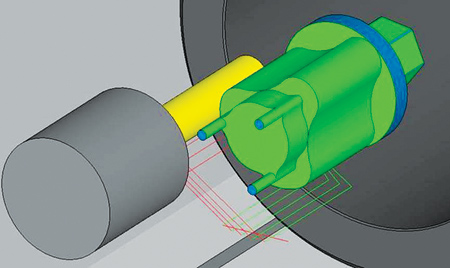
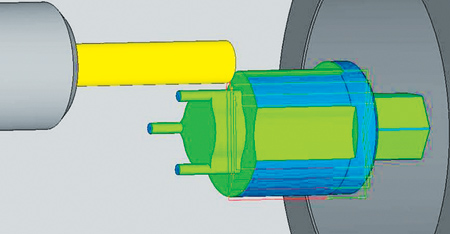

Cleveland Machine Company logo engraving in ESPRIT
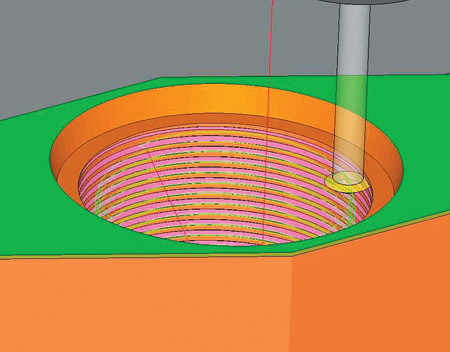
Cleveland Machine recently took on a R&D project that required a large female thread and, due to the inability to chuck up on it after the outside was machined, decided to attempt a thread mill. "ESPRIT picked up the thread size based on the I.D. of the hole, I altered the depths a little, and it literally made the program in minutes. After finding out how easy it is to program a thread mill using ESPRIT, it is likely we will start using this more on other parts that we have had to tap in the past," said Buckaloo.
Texas-based Cleveland Machine is a highly specialized shop that serves the state's major oil & gas industry. Cleveland Machine manufactures only type "H" back pressure and two-way check valves, which are installed in the wellhead to hold pressure during routine maintenance and repair of drilling equipment. Although the company limits its work to type "H" valves, each wellhead often requires hundreds or even more than 1,000 pieces-so efficiency is one of Cleveland Machine's top priorities.
On the Cleveland Machine shop floor, one can find an Okuma Captain L470 lathe, an Okuma Space Turn LB4000EX lathe, an Okuma Genos L400E lathe, an Okuma MX-55 mill with rotary, a Leadwell MCV-1100i mill with rotary, two Okuma LB3000 MYW mill-turns and an Okuma MB-56VB mill.
Although the shop features an impressive lineup of machine tools, programming them has not always been smooth sailing. Cleveland Machine's Plant Manager, John Buckaloo, described some initial pain points: "We had issues with programming our first Okuma mill-turn, specifically the live tooling aspect and picking up with the sub-spindle. Although it is relatively simple to manually program those, ESPRIT was critical when the time came to contour surfaces and machine awkward radii."
Buckaloo and the Cleveland team first encountered ESPRIT at a Hartwig open house in Houston, and they were immediately struck by its efficiency. "Victor, from ESPRIT reseller Shape Design Technologies, did a great job of showing us the software and touting the power of good post-processors," said Buckaloo. The timing could not have been more opportune. "Once we saw ESPRIT in action and talked with Victor, it was clear that ESPRIT would be the best option for effectively programming our mill-turns."
In the years since first implementing ESPRIT, the program has lived up to Buckaloo's initial expectations. "We use ESPRIT for programming helical movements, rotary milling and especially engraving," he said. "Lately, I have been using engraving quite often. This is nearly impossible to do without some sort of CAM software."
Engraving was non-existent prior to ESPRIT. The team largely used a dot-peen, low-stress stenciling machine for maintaining traceability within the facility. "ESPRIT made it very easy to import a DWG of our logo, scale it to the workpiece I need, animate and create code," said Buckaloo. "It is quite literally that easy to engrave now. I never even attempted to program a logo before as I knew it would be thousands of lines of code utilizing many radii-a recipe for an alarm that would be impossible to trace."
Buckaloo added, "ESPRIT outputs flawless code to our mills time and time again. We recently performed our first thread mill operation. Without ESPRIT, I would have been clueless on how to proceed with programming this."
In addition to helping streamline the programming process, ESPRIT now plays a valuable role in R&D at Cleveland Machine, too. "I use ESPRIT any time I design a new item, as well as when programming the Okuma mill-turns," said Buckaloo. "We are a production shop producing the same pieces over and over again, for the most part. Many of our programs were created years ago. Lack of a CAM software limited our abilities in creating newer items or performing any kind of R&D. ESPRIT allows us to attempt R&D projects much quicker due to the ease of producing programs. Before, we did not want to attempt some projects due to the sheer difficulty in manually programming. ESPRIT solved that problem altogether."
As Cleveland Machine continues to fulfill the evolving needs of the oil & gas industry, Buckaloo is confident that ESPRIT will keep the future bright. "Whether making one-off pieces or large-volume R&D creations, ESPRIT has saved us a tremendous amount of programming time and has also prevented quite a few machine crashes," he said. "We will likely continue to make the same parts we make now, but we intend to branch out as our capabilities increase. ESPRIT, in conjunction with new machines and machine technology, is necessary to help us complete that goal."
For more information contact:
Cleveland Machine Co., Inc.
9350 FM 1725
P.O. Box 793
Cleveland, TX 77328
281-592-6549
clevelandmachine@sbcglobal.net
www.clevelandmachine.com
ESPRIT CAM
1150 Avenida Acaso
Camarillo, CA 93012
805-388-6000
esprit@dptechnology.com
www.espritcam.com