

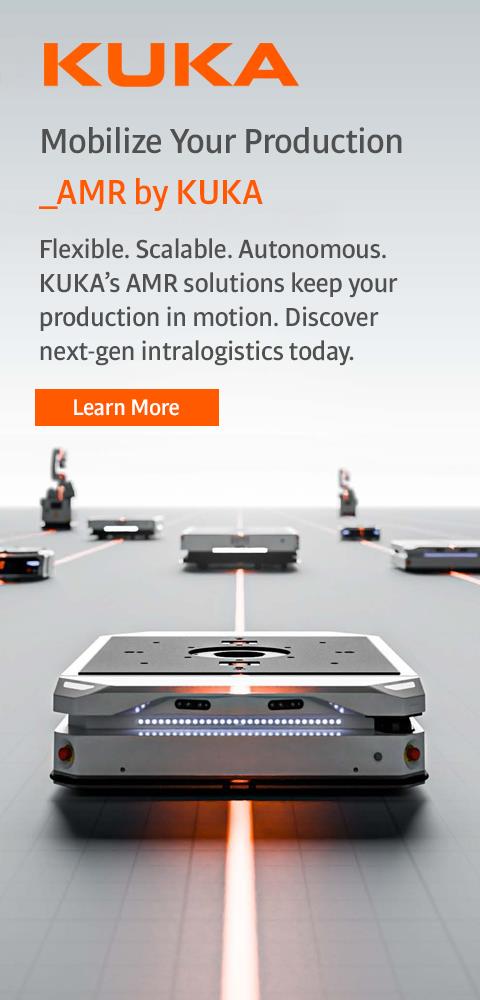
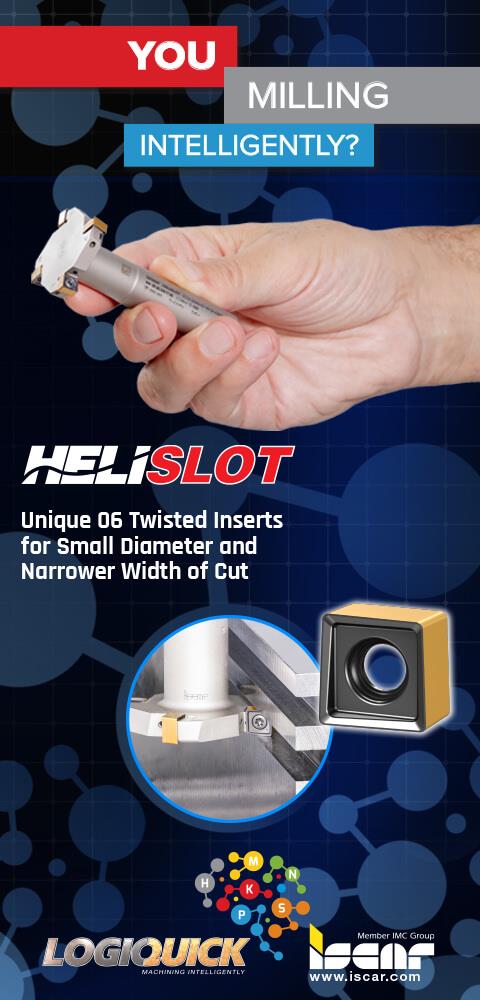
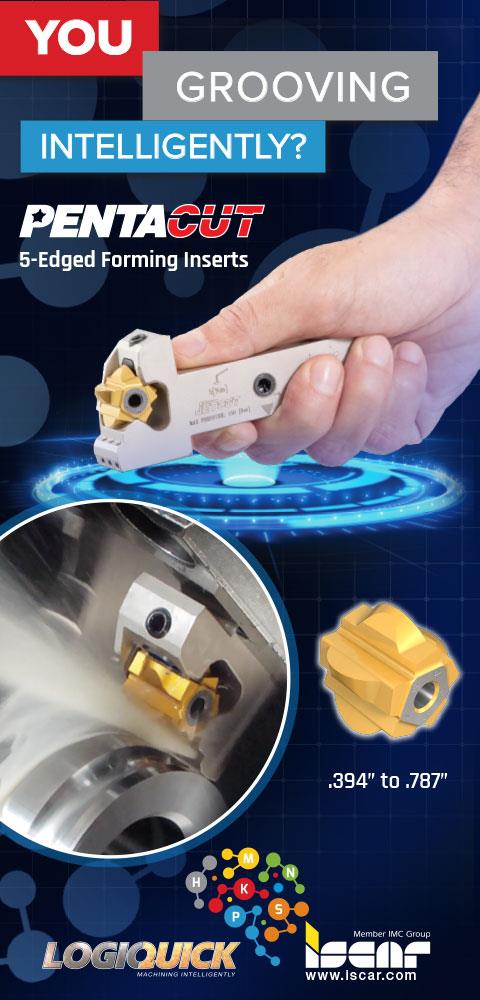
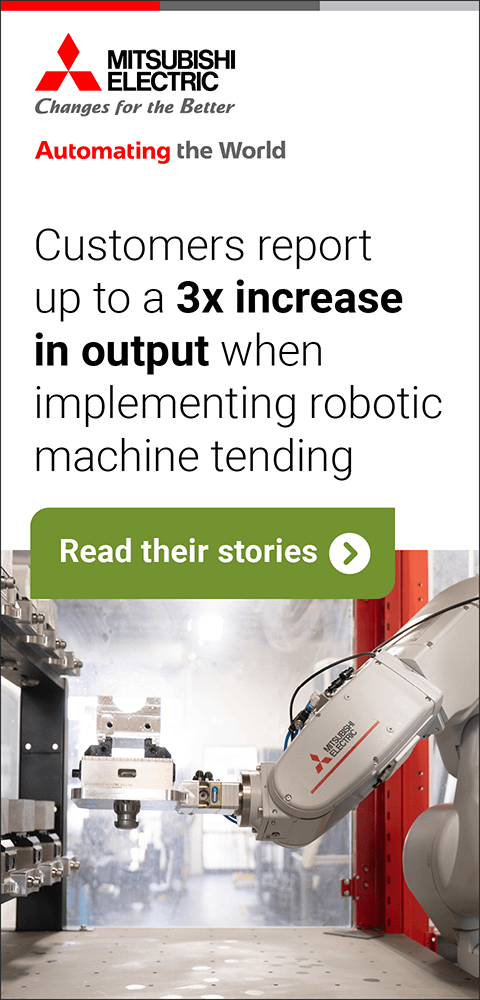
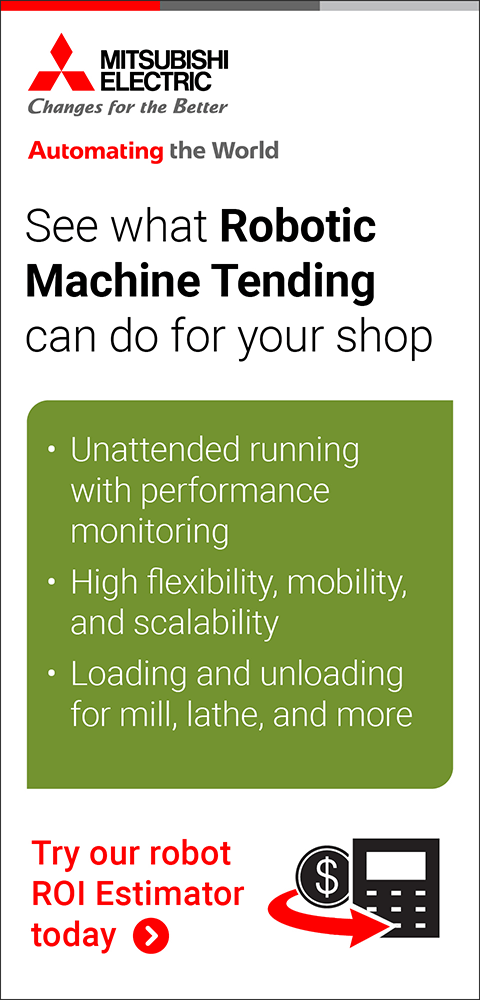
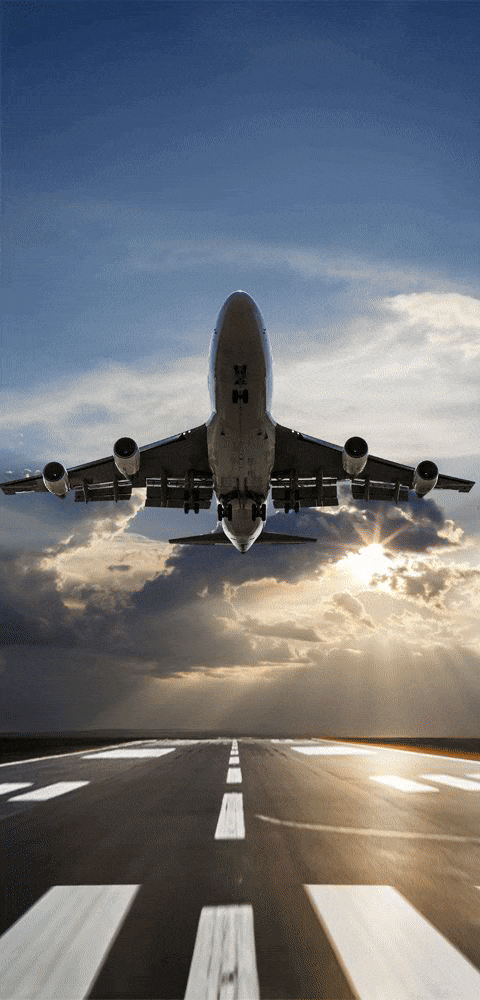
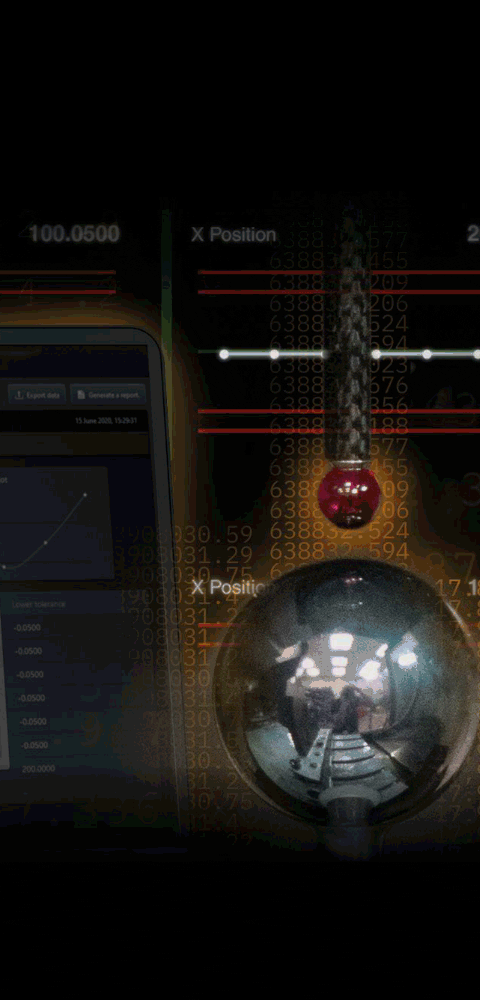
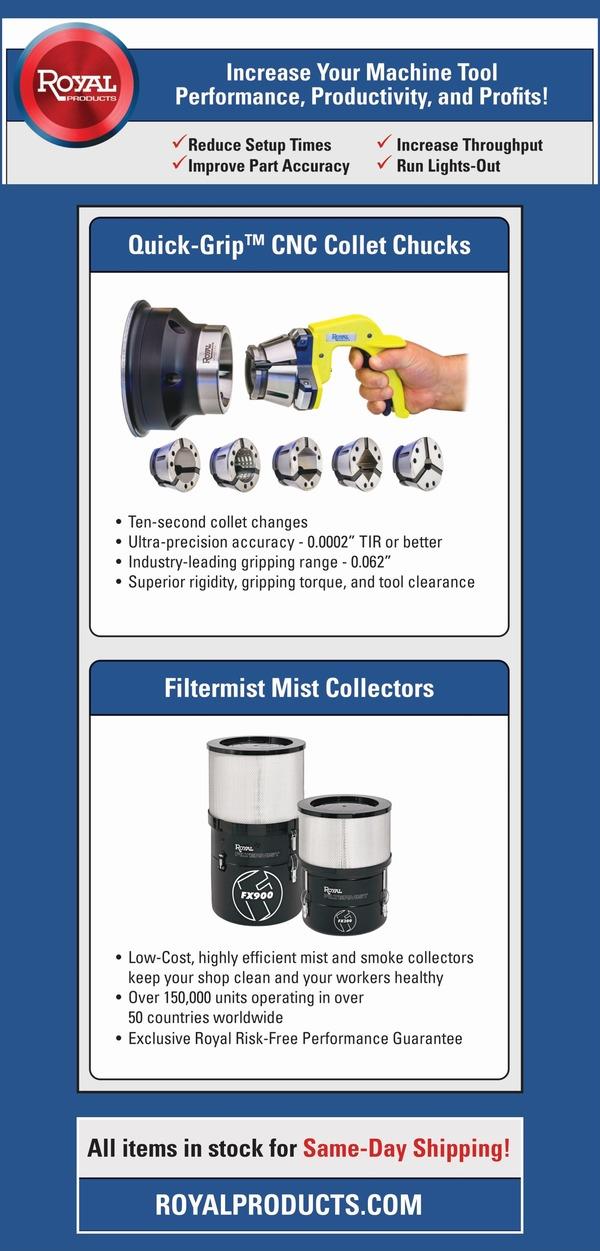
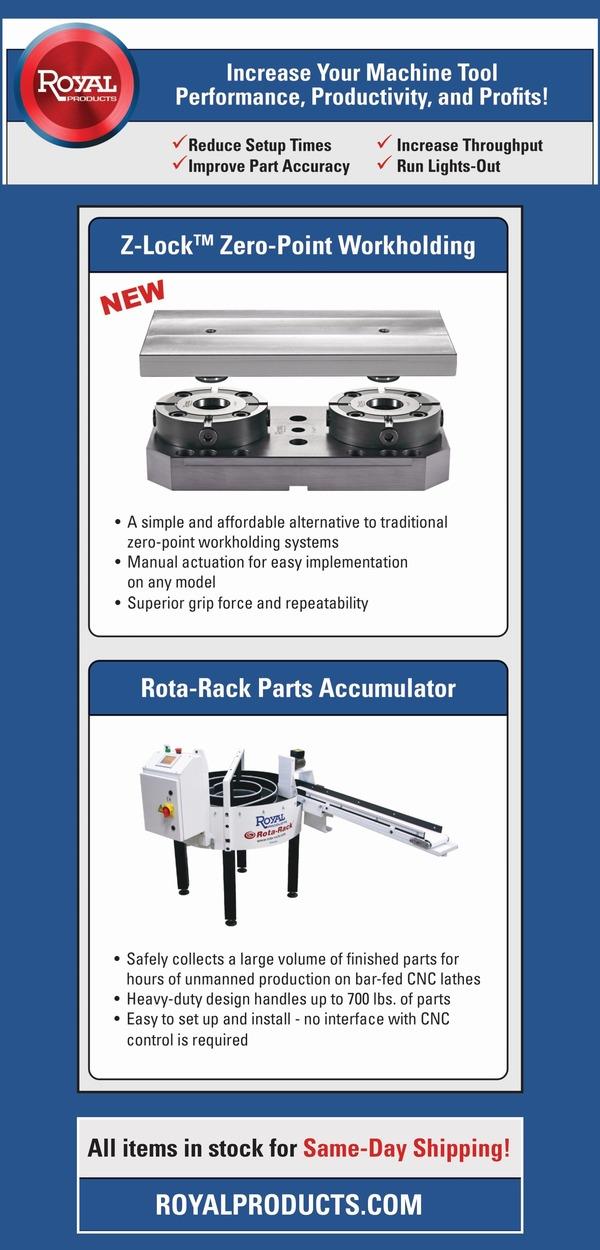
Die Sinker for Micromachining Electronic Components
July 1, 2019
GF Machining Solutions offers the AgieCharmilles FORM S 350 die-sinking electrical discharge machining (EDM) solution. The machine features breakthrough generator technology and accuracy-enhancing thermostabilization that allow electronic component manufacturers to keep pace with increased consumer demand.
A sturdy C-axis construction and cast-iron frame provide high stability and force reduction, which helps maintain a precise spark gap between the part and the electrode. Regardless of part weight or dielectric volume, the machine is designed to deliver consistent accuracy. Integrated linear glass scales preserve long-term repeatability and eliminate the need for recalibration as well as any errors found in traditional screw systems due to backlash and wear.
"The AgieCharmilles FORM S 350's latest-generation Intelligent Power Generator (IPG) excels in superfinishing and precision applications," said a company spokesperson. The IPG overcomes common challenges when using copper electrodes, including wear induced by electrical discharge multiple reopening. "As a result, GF Machining Solutions' EDM can machine up to 40% faster and reduce corner wear by 50% over standard EDMs," added the spokesperson.
The machine's discharge circuit for spark erosion power modulation and the flexibility to maximize material removal offers enhanced levels of quality and efficiency; for the finest details, the spark gap can be reduced to just a few microns. Embedded technologies optimize electrode usage and positively impact profitability through extended electrode life, shorter machining times and reduced downtime.
A dual thermostabilization system cools and circulates pulsating air through the machine's cabin to maintain a stable temperature and ensure extreme precision.
With an X/Y/Z travel of 31.1" x 20.9" x 11.8" (790 mm x 530 mm x 300 mm), the FORM S 350 handles workpieces up to 31.1" x 20.9" x 13.8" (790 mm x 530 mm x 350 mm).
For more information contact:
GF Machining Solutions LLC
560 Bond St.
Lincolnshire, IL 60069-4224
847-913-5300
www.gfms.com/us
< back