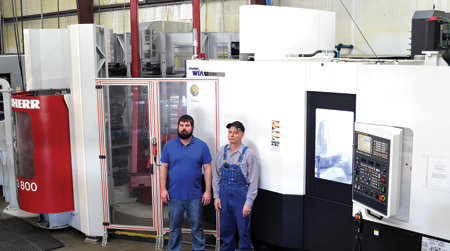
(l-r) Nathan Dietz and Mike Jantzen, machine operators at Technics 2000
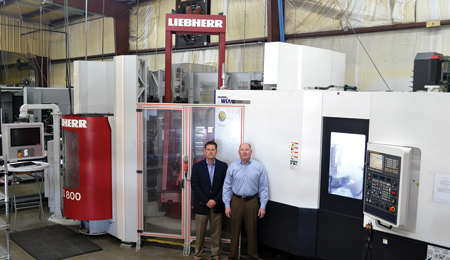
(l-r) Steve Cross and Phil Cross, Owners, Technics 2000
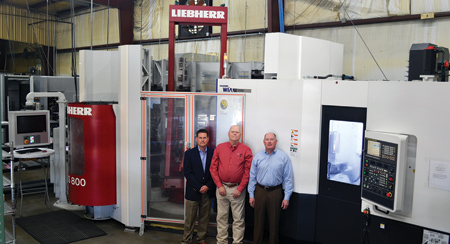
(l-r) Steve Cross, Owner, Technics 2000; Steve Davis, Owner, SMT Co.; Phil Cross, Owner, Technics 2000
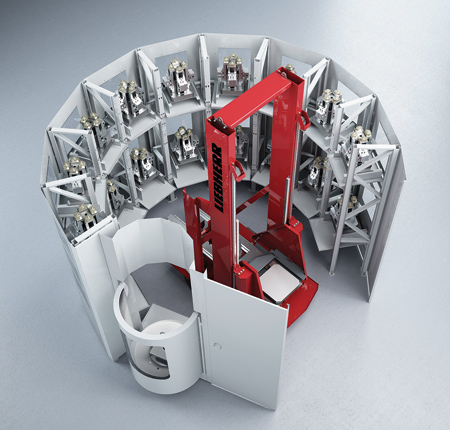
Liebherr Rotary Loading System (RLS)
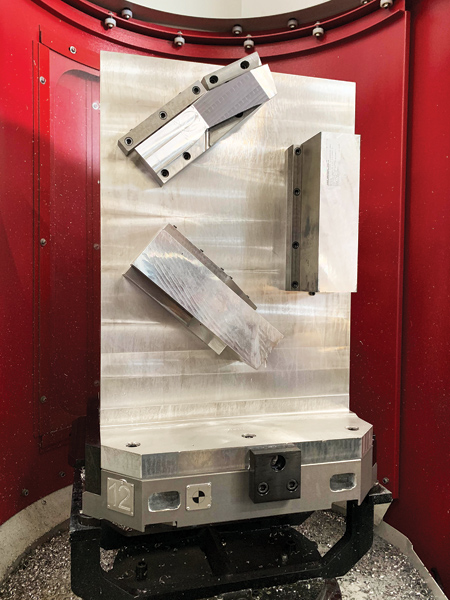
A pallet inside the RLS.
"Our challenge as a machine shop with a large book of work in the aircraft industry is to expand our capacity in a tight labor market," said Steven Cross, Owner, Technics 2000, Olathe, KS. Technics 2000 has been in business for 40 years serving both industrial and the aviation market place. With two buildings, the company knows it has to be efficient with labor and floor space.
"Technics' goal is to increase our spindle utilization by moving items from stand-alone horizontal machining centers to HMCs with integrated automation, allowing our employees to take on new work and challenges," said Cross.
"Over the years," continued Cross, "we have added machining centers, have been fortunate enough to have a stable workforce and have found new employees capable of running the new equipment. In our growth, we are slowly running out of floor space. Technics has considered palletized systems since the 1990s, but most of them were a combination of complexity and cost that did not always make sense with our work."
Which is why Steven decided to call on his local machine tool source, SMT, a dealer serving Kansas, Missouri, Iowa and Nebraska.
"SMT Owner Steve Davis and his staff have always had a good feel for what machinery we could use to profitably handle our work," said Cross. "In addition, Steve has always known of our desire to automate our work to be more efficient. Steve presented the Liebherr pallet system in the fall of 2017. It immediately appealed to us due to its compact footprint and attractive total cost."
"When Technics decided to expand with another horizontal machine and wanted to add a pallet system to the machine, they came to us," Davis reported. "Because they already had several Hyundai WIA 500 mm horizontals, it was decided that the HS5000i would be the best choice. This machine had proven to be very reliable, and was a good fit for the aerospace parts they would be machining due to its 120-tool magazine, NC-4 tool measuring/tool breakage detection and tool life management system."
The next step was to find a pallet system that would not be just an expensive material handling unit, but rather one that would support the management/scheduling of parts, programs, fixturing and tools. The other requirement was for the pallet system to be flexible and expandable while having a small footprint. SMT set out to find the best fit for the customer, which led them to a system on display at IMTS-the Rotary Loading System (RLS) 800 by Liebherr Automation Systems Co.
"Of our three available families of pallet handling systems, the RLS was the first choice for this application," said a Liebherr spokesperson.
The RLS 800 pallet pool features one load/unload station and 21 pallets. The circular design with two and three levels of pallet stocking stations gave Technics the capacity and flexibility needed to run second and third shifts unattended, plus it took up the least amount of floor space of all of the systems considered.
The RLS provides 800 kg load capacity on a O 600 mm pallet system. As a system, it provides complete tool, production, pallet and fixture management. Its compact design also allows the maximization of pallet locations within restricted space.
The integrated cell control software by SOFLEX provides Technics with the tools needed to manage production time, program storage, tooling set-up and fixtures. One of Technics 2000's favorite features is the capability to monitor the entire system from remote locations.
According to Liebherr, the SOFLEX cell controller is user-friendly, offers integrated order planning and can be expanded as operations demand, for example, to add functionality to suit varying batches and increasing volumes of mixed or new parts. The software calculates production times, monitors tool life, optimizes production schedules, analyzes throughput and more, supporting lights-out operations.
In the basic version, NC program and tool management remain on the machine, while the cell controller manages pallets and production planning. This allows operators to continue working in a familiar machine environment. Short commissioning time, high acceptance and fast production start-up are key benefits.
For the Technics order, Liebherr Automation Systems had the RLS in stock in Saline, providing a four-month delivery. The system shipped to Olathe to SMT for integration with the Hyundai WIA HS 5000. Engineers from Liebherr worked with SMT to integrate all aspects of the system.
Since installation in June 2018, Technics has been able to load 75% of the pallets. Thirty parts and families of parts were reprogrammed to fit on the system. Technics employees were trained on the Liebherr system, and re-programmed all of the chosen parts.
"Using the RLS to extend a machine's running time makes investing in an additional machine completely unnecessary in certain cases," said the Liebherr spokesperson. "This solution is more effective than marginal increases in productivity that could result, for example, from optimizing CNC programs or the tools of machines that are manually fed or partly automated. One or two machining centers can be docked to the system."
For batch sizes of one and above, the RLS provides considerable efficiency potential. The operator can use the machine's running time to perform other production tasks-set-up costs thus do not enter into the machine costs/hour equation.
"Optimum machine utilization and reduced staffing requirements result in decreased unit costs of up to 20%, so the investment can pay for itself in less than two years," said the Liebherr spokesperson. "Moreover, the system improves delivery capability and facilitates rapid, flexible responses to changes in customer demand."
The Liebherr system uptime has been exceptional with a manageable learning curve for both SMT and Technics. Technics is now able to run production at night and load the remainder of fixtures and parts during the day, achieving approximately 17 hours a day in production.
"Liebherr's training was some of the best we have seen," Cross said. "They did not leave until all questions were answered and the system was running smoothly. Liebherr and SOFLEX offered training before and after the machine's installation and are still available any time a question comes up." Liebherr also provided expert design of the pallet crane installation.
For Liebherr Automation Systems Co., this was an important project. The project took root at a Hyundai WIA open house during a meeting with Davis and Greg Gilbert, Liebherr Area Sales Manager. Kevin Heise, Liebherr Area Sales Manager and Project Manager, explained, "It expanded our footprint in aerospace manufacturing and expanded our presence in Kansas. We look forward to many more installations of this efficient pallet system."
For more information contact:
Technics 2000 Inc.
870 N Jan Mar Ct.
Olathe, KS 66061
Liebherr Automation Systems Co.
1465 Woodland Drive
Saline, MI 48176-1259
734-429-7225
info.lgt@liebherr.com
www.liebherr.com
Hyundai WIA Machine Tool
450 Commerce Blvd.
Carlstadt, NJ 07072
201-987-7298
marketing@hyundai-wiamachine.com
www.hyundai-wiamachine.com
Steve A. Davis
SMT Company
15250 S. Keeler St.
Olathe, KS 66062
913-764-2788
steve@smtco.biz
www.smtco.biz