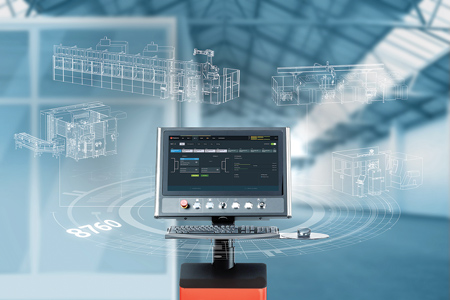
Image credit: Gladiathor/iStockphoto
The new version of Fastems' Manufacturing Management Software (MMS) integrates both automated and non-automated processes into digital manufacturing management, bringing together three application areas in a single manufacturing software platform: pallet-based automation, automation of direct part handling with robots and work cell operations for standalone machines and other manual manufacturing operations.
Topi Judén, Head of Product Management - Digital Products for Fastems, said, "With the new version of MMS, we introduce a new level of control for direct part handling automation. Also, we are offering an easy way of scheduling work queues and resource needs for non-automated production phases and thus extending full transparency, control and visibility to all manufacturing operations."
MMS as a pallet automation cell controller includes an extensive set of features developed for the direct part handling solutions. Now the MMS software platform offers advanced production management functionality for robotized machine tending applications. "Easy introduction of new workpieces is important for achieving today's manufacturing requirements. The new MMS platform includes functionalities for part process plan definitions through the graphical user interface. Together with parametric robot programs and coordinate based part location management, the need of robot programming is minimized and PLC programming can be avoided," said a company spokesperson.
The new MMS version also offers predictive and adaptive scheduling for automated production by industrial robots. "This is the base for the entire planning process, plus MMS adds manufacturing resource planning with the indication of missing resources such as cutting tools, raw materials, NC programs and the like. This gives the full 'look ahead' view for operators to execute the planned production to enable proactive operation, leading to greater output," said the spokesperson. The new MMS manages order-based production in the robot cell with manufacturing batches. The ability to produce several different workpieces simultaneously in different lot sizes increases flexibility. Also, information about the required fixturing and clamping elements on the machine tool are now available, and the new MMS manages these as set-ups. It can schedule the set-up changes for the machine tools and, depending on the application, is even capable of changing the set-up automatically with the robot.
Further, with the latest MMS version, it is possible to plan and control the aspects of manufacturing that are not automated with robots or FM systems. As a result, the MMS software closes the gap between the automated and manual manufacturing processes. For example, the operator of a standalone machine tool receives a precise work list and instructions via the MMS about which steps are required for production and receives timely information, such as when a set-up, materials, tools, etc. must be ready.
The new MMS combines three previously separate manufacturing facets in a single software solution that links all relevant processes. The manufacturing processes in the individual areas can be planned, forecasted, controlled and monitored separately or in combination as required. This allows the full transparency of manufacturing operations by providing a detailed overview of the entire production process. MMS users will therefore not only find it easier to plan the production and the resources required for it as a package, but also be able to control it more effectively and adapt flexibly to future orders.
For more information contact:
Fastems, LLC
9850 Windisch Road
West Chester, OH 45069
866-702-0611
info.fastems@fastems.com
www.fastems.com