

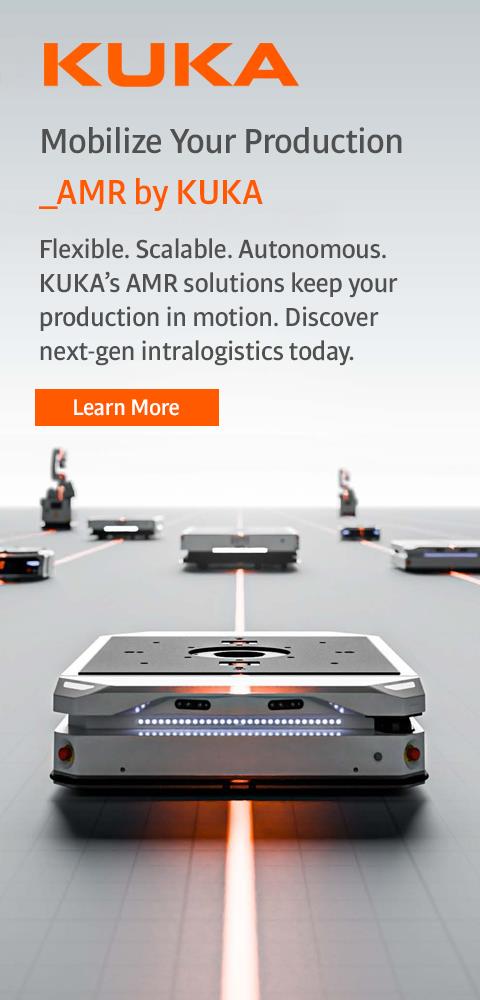
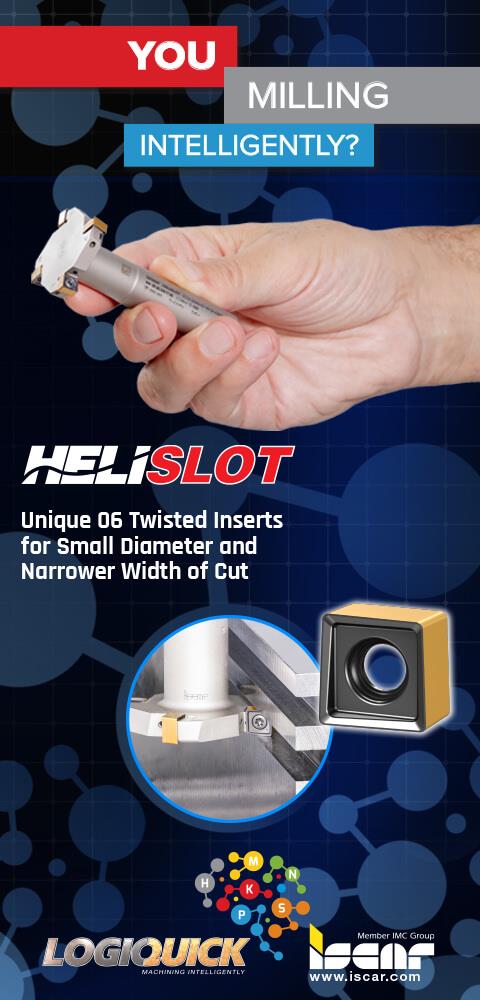
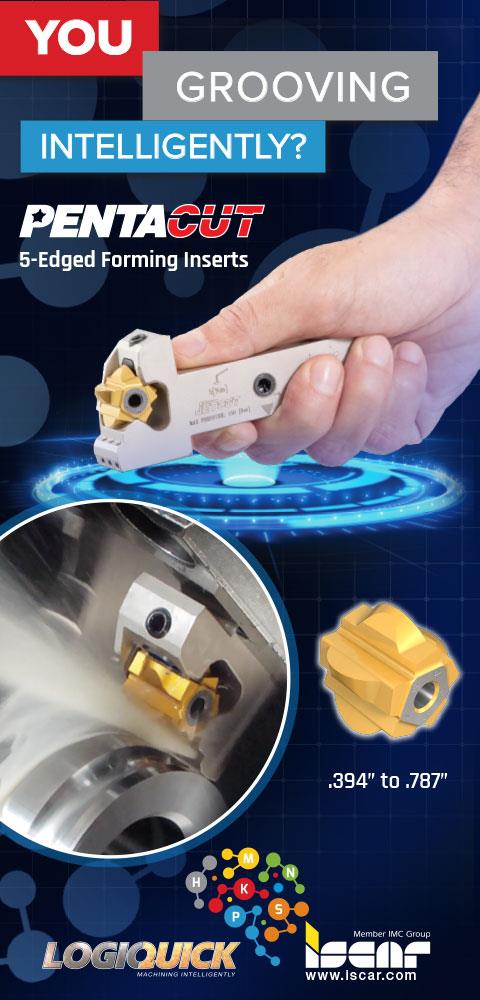
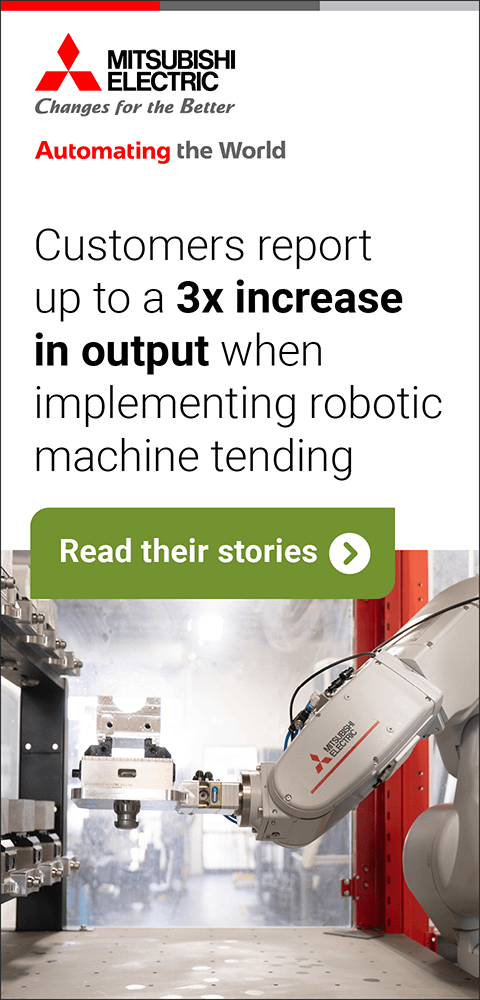
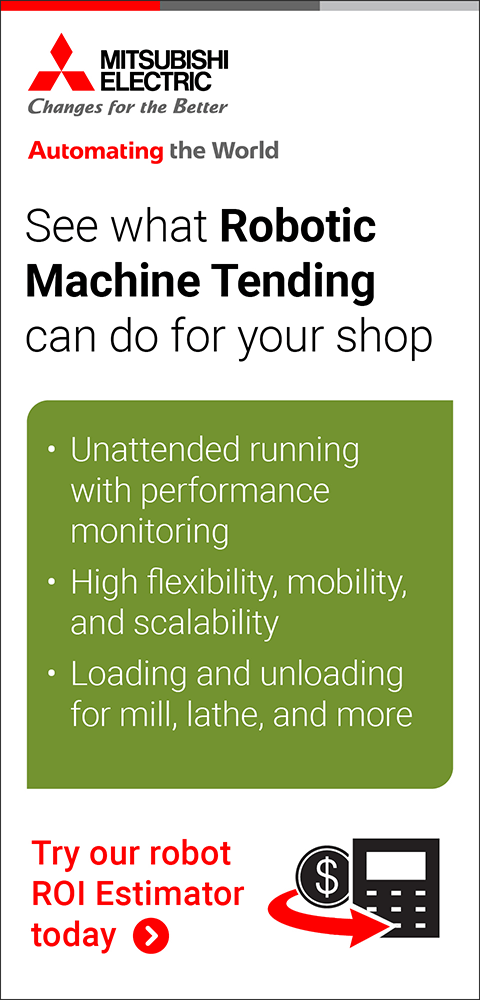
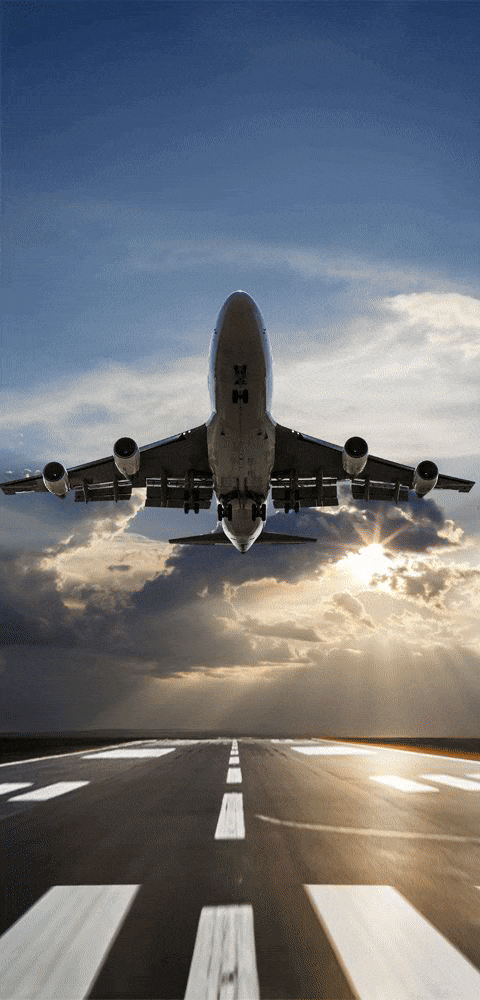
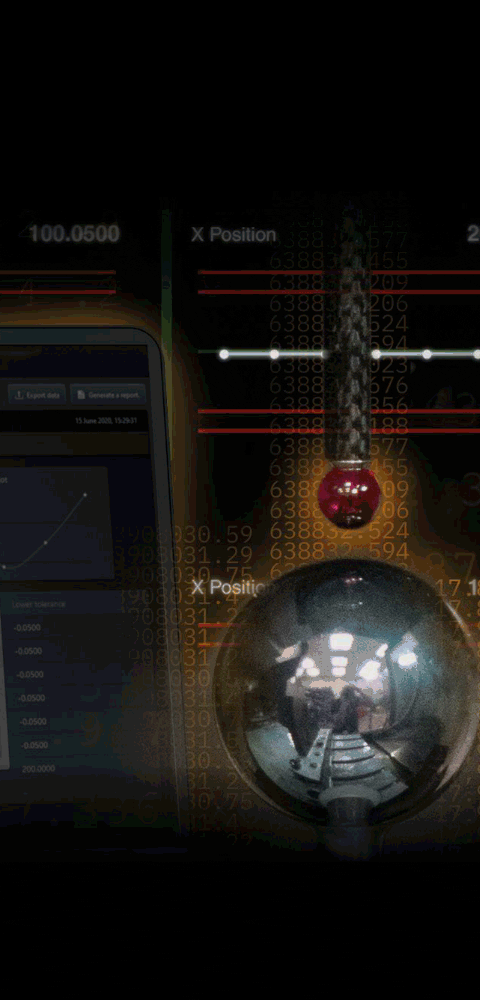
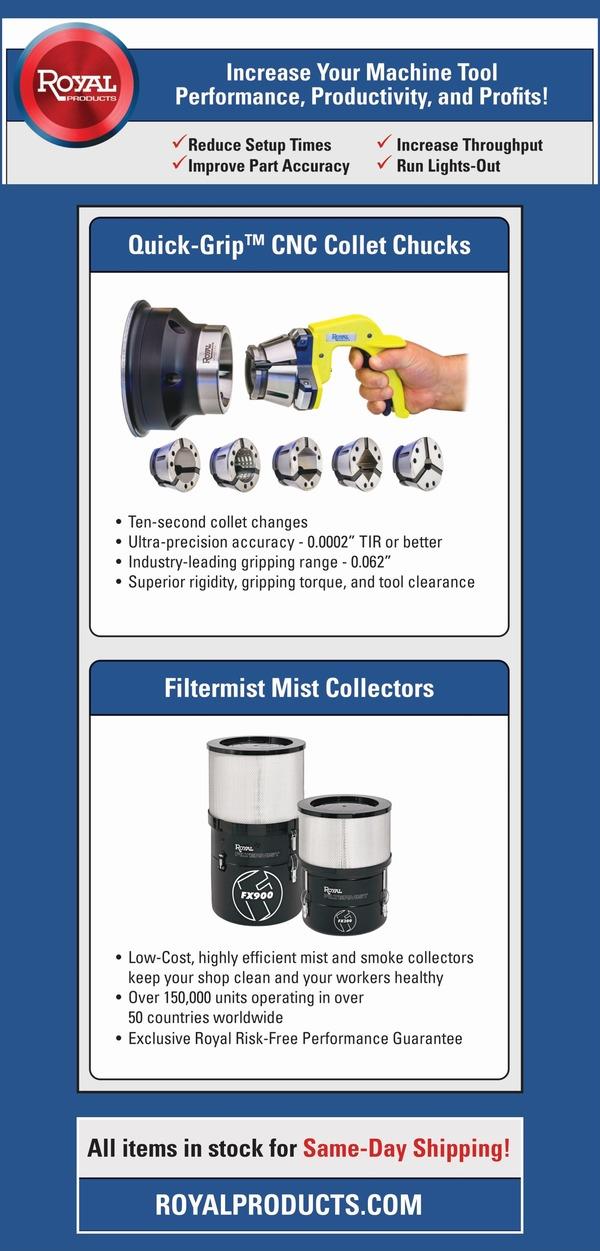
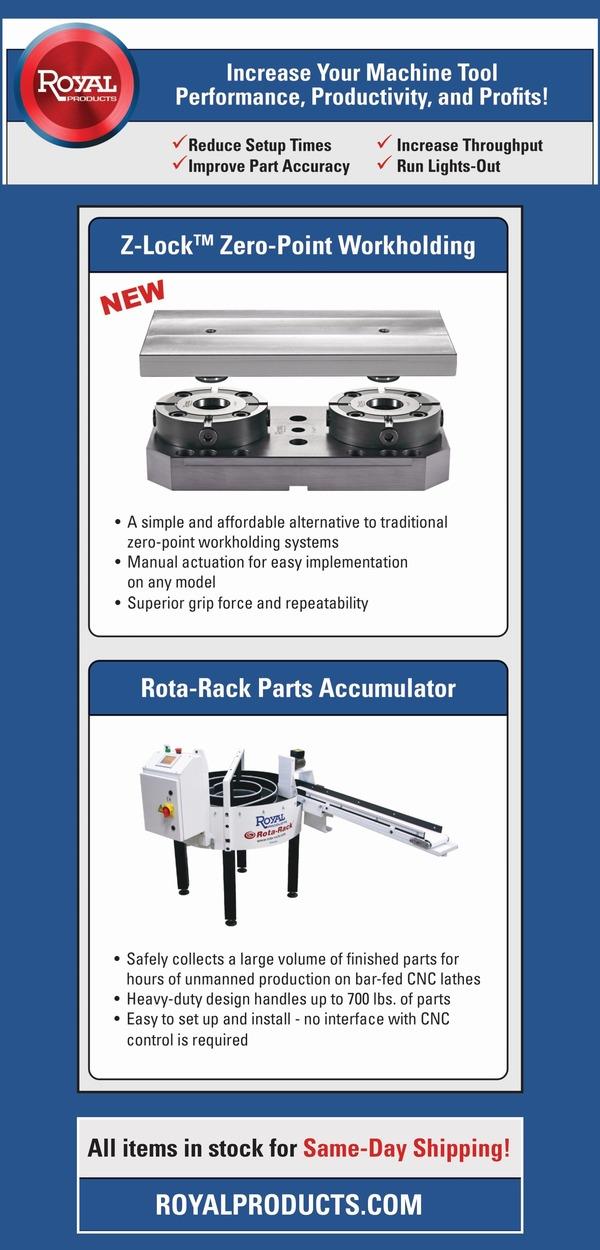
Multi-Operational Turning Milling Centers
January 1, 2019
Litz Hitech has launched a series of integrated production machines that combine a turning center and a vertical machining center (VMC) to form the TM2500 and TM2500S. This multitasking series features the combined processing technology of turning and milling, making it capable of single-mounting based high-precision machining, suitable for making small and complex geometry components prevalent in medical and measurement devices.
The TM series is designed to reduce equipment and labor costs, power consumption and cycle times all while decreasing shop floor space. "Achieve an even higher return on investment with the TM2500S, featuring dual spindles to reduce part handling and increased Z-axis travel as compared to the TM2500," said a company spokesperson. Both spindles come with a built-in motor for turning and milling functions as well as an exclusive C-axis lock system for stable positioning accuracy.
TM Series machines feature an orthogonal rail structure for X, Y and Z axes, and a larger working range which decreases production interference normally caused by the collision of the chuck and tool tip. The TM2500 has 22" of Z-axis travel, and comes standard with a tailstock. The TM2500S includes a sub-spindle and 42" of travel in Z to allow for longer workpieces. Both come with 4,500 RPM 29 HP turning spindles and 2.5" diameter bar capacity. The milling spindle has a +/- 120° B-axis tilting head with 29 HP 12,000 RPM HSK-63T tools (CAPTO C6 is optional). The machines are equipped with a Siemens 840D control, with the FANUC 31i-B5 being an option for the TM2500.
For more information contact:
J2 Machine Tool Group
814-807-2113
info@j2machinegroup.com
www.j2machinegroup.com
< back