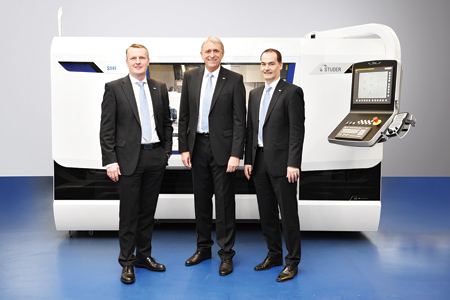
(l-r) Gerd König, COO of the Cylindrical Grinding Technology Group; Fred Gaegauf, CEO of STUDER, SCHAUDT and MIKROSA; and Jens Bleher, Managing Director of STUDER and CSO of the Cylindrical Grinding Technology Group.
United Grinding recently held its Motion Meeting 2017 at its headquarters in Thun, Switzerland. This annual meeting offers the company's global distributors hands-on experience in the latest technology offerings from United Grinding as well as an introduction of the newest products and developments. The company also shares its focus areas for the near future.
"We make our customers more successful by responding to their requirements," said Fred Gaegauf, CEO of STUDER, SCHAUDT and MIKROSA, at the annual meeting. "To do this, you first have to understand the customer's individuality. Easier said than done, in a time when the complexity of processes is steadily increasing and customer requirements are also growing significantly. And yet the three companies (STUDER, SCHAUDT and MIKROSA - all part of United Grinding) achieve this, due to their flexibility in production and constant pursuit of innovation. It is for good reason that STUDER, SCHAUDT and MIKROSA are global leaders in the industry with their products. We are well on track, even if we have not met all our targets. To this end, we have invested heavily in our production technology and have reduced processing times, which ultimately also benefits our customers."
United Grinding focuses on strengthening its core competencies along the entire value chain and has invested around $40 million in its plants during the last few years. New buildings have been added and new machine tools have been installed and networked based on optimized logistical criteria. The company has integrated central manufacturing processes into its own value creation chain to ensure high process stability. At the same time they have founded their own Six Sigma Academy with the internal PuLs philosophy, based on the Lean Six Sigma method. This enables the employees to shape their own working culture and to constantly examine and improve processes and systems. As an internal cross-function initiative, PuLs focuses on applying best practices in every aspect of the company's business from sales to applications support to training and preventive maintenance.
An example: The introduction of flow-line assembly at STUDER. Due to the implementation of flow-line assembly in 2015, processing times in final assembly have been reduced by up to 50%, process stability has been significantly increased and quality risks have been significantly reduced. "We strive to achieve perfect processes, so that we can provide excellent products and services. We want to impress our customers with our effectiveness," said Gerd König, COO of the Cylindrical Grinding Technology Group. During the next few years the company will continue to focus on expanding the existing locations and will continue to invest heavily.
In order to maintain the innovation leadership of United Grinding in the future, the focus will be on the following projects, according to the company:
- Industry 4.0: The fourth industrial revolution concerns the digitalization and networking of machines with their environment. United Grinding is focusing on the acquisition of machine and process data. The goal is predictive maintenance. The aim is to avoid unexpected downtimes for customers and to make production more plannable and efficient.
- Smart Sensors: United Grinding will develop active, autonomous sensors to fully measure and also actively support the grinding process.
- Universal Series: Following the successful market launch of the completely revised internal grinding machine series, STUDER is continuing to work on issues that make the customer more successful.
- Cooling Lubricant: In cooperation with IRPD AG, which operates in 3-D printing/additive manufacturing, STUDER is developing coolant nozzles for laminar flow conditions. This allows the lubricant to be accurately directed into the grinding slot, so that the optimal cooling effect is achieved at the desired location.
- STUDER-WireDress: This enables complex geometries to be produced efficiently and with high cutting ability. It helps to reduce process times and make the customer more successful. "We were able to reduce grinding wheel wear by 75%," confirms a United Grinding customer.
For more information contact:
UNITED GRINDING North America, Inc.
510 Earl Blvd.
Miamisburg, OH 45342
937-859-1975
info@grinding.com
www.grinding.com