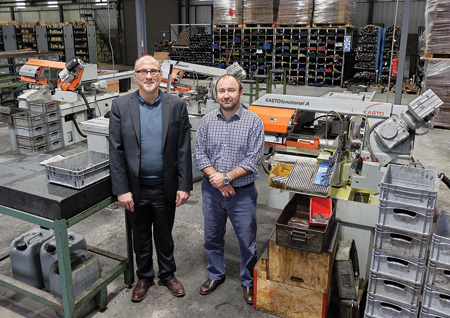
(l-r) John Bairner and Benjamin Stirling, joint proprietors of Tasman Industries, in the company's new warehouse in Rufford Road, Stourbridge.
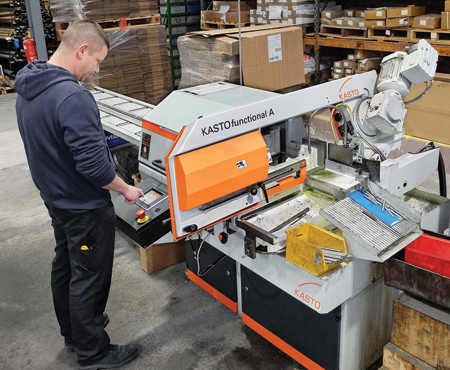
The Kasto control has touchscreen operation and a built-in database of cutting speeds and feeds to suit all materials in the warehouse.
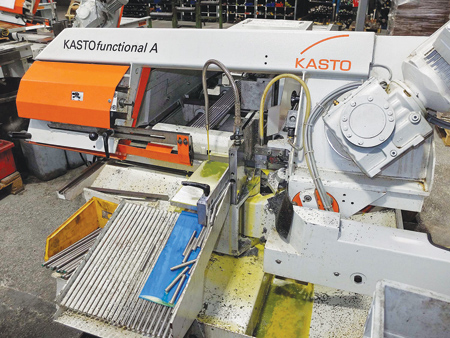
One of the KASTOfunctional A bandsaws cutting 316 stainless steel all-thread bar stock into batches of several thousand.
One of the UK's leading providers of light engineering components, Stourbridge, England-based Tasman Industries, has acquired two automated pivoting-bow bandsaws from Kasto, the most recent of which was delivered in December 2016.
The bandsaws have transformed the efficiency with which the firm cuts bar material, which consists of an array of metal types and sizes up to large batches of several thousand. For smaller runs, say 50-off, it relies partly on a similar semi-automatic saw installed by Kasto earlier last year.
Tasman specializes in supplying shaft keys, key steel, shaft collars, taper and slotted pins, precision dowel pins, screws and many more products in sizes spanning a few square millimeters in cross section up to 125 mm diameter, 100 mm x 50 mm and 75 mm square. Materials range from steels, including stainless, through nickel alloys and titanium to copper alloys, aluminum bronze, phosphor bronze and brass.
Established in 1988, the company is currently owned and managed by equal partners John Bairner and Benjamin Stirling. They oversee a complex manufacturing and distribution business involving sourcing raw material and products from all over the world and shipping it to 3,500 customers, 800 of which are active in any given month. Ranging from blue chip multinationals to individuals repairing lawn mowers, Tasman's products are mainly in the UK but can be found as far afield as New Zealand.
Complicating these activities is the fact that only half of output is standard, the remainder being made-to-order specials supplied to customer specifications. These require a combination of milling, turning, grinding, laser cutting, heat treating and plating, carried out by around 1,200 subcontractors, only half of which are in the UK. It is truly a global operation.
The only machining performed at Tasman's warehouse in the West Midlands is straight and miter cutting of 200 metric tons of bar material per year. The backbone of this function consists of two KASTOfunctional A pivoting-bow automatic bandsaws and a KASTOfunctional U semi-automatic model. They are of solid construction with a robust, torsion-free welded base capable of cutting material to a maximum of 260 mm round/square. Stock can be miter cut to the left at up to 45° and to the right at up to 60°.
"We tried moving to automatic sawing a few years ago with the purchase of a circular saw from another manufacturer, but the blade kept breaking and the hydraulics leaked," said Bairner. "Overall it was not a good experience. We went back to using a pair of semi-automatic bandsaws, one of which we still use, but could see the benefits of automation for longer runs.
"In 2014 we decided to go down the automatic bandsaw route and installed the first KASTOfunctional A with a roller infeed table, having been impressed with a demonstration at the company's Milton Keynes, Buckinghamshire, showroom.
"The machine proved so accurate, reliable and productive that we added the semi-automatic U version during the first half of 2016 and a second fully automatic model at the end of the year.
"One bandsaw feature that impresses me is that the material is fed accurately by a ballscrew drive, as used for axis positioning on mainstream machine tools, rather than via a leadscrew or a hydraulic cylinder."
Bairner said he also likes the user-friendliness of the Kasto touchscreen control, which allows easy programming of the next cutting job. A built-in database saves time by automatically selecting the correct band speed and rate of downfeed to suit the type and size of material to be cut.
As cutting volumes increase, Bairner will consider buying a bundle clamp for one of the KASTOfunctional A's to increase sawing efficiency further when processing bar of smaller cross section. This could happen sooner rather than later - at the start of 2017 Tasman introduced a subcontract cutting service whereby it will saw to length and miter cut stock for other companies in the Midlands.
To prepare for this and other initiatives, in November 2016 Tasman bought a new 25,000 sq. ft. premises in Rufford Road, Stourbridge, that is five times larger than its previous facility nearby. The company has also introduced a new business-to-business system on its website (www.keysandpins.com) so customers can order standard products online.
As a consequence, the firm will be able to spend more time on the made-to-order manufacturing side of its business, which it believes to be the main area for growth. Quality will continue to be at the heart of its activities, not only through ISO 9001 accreditation but extending to reliability of service and fast turnaround backed by full lot traceability, certificates of conformance and test reports.
For more information contact:
Tasman Industries, Ltd.
+44(0)1384 634461
www.keysandpins.com
KASTO Inc.
3002 Venture Court
Export, PA 15632
724-325-5600
sales@us.kasto.com
www.kasto.com