
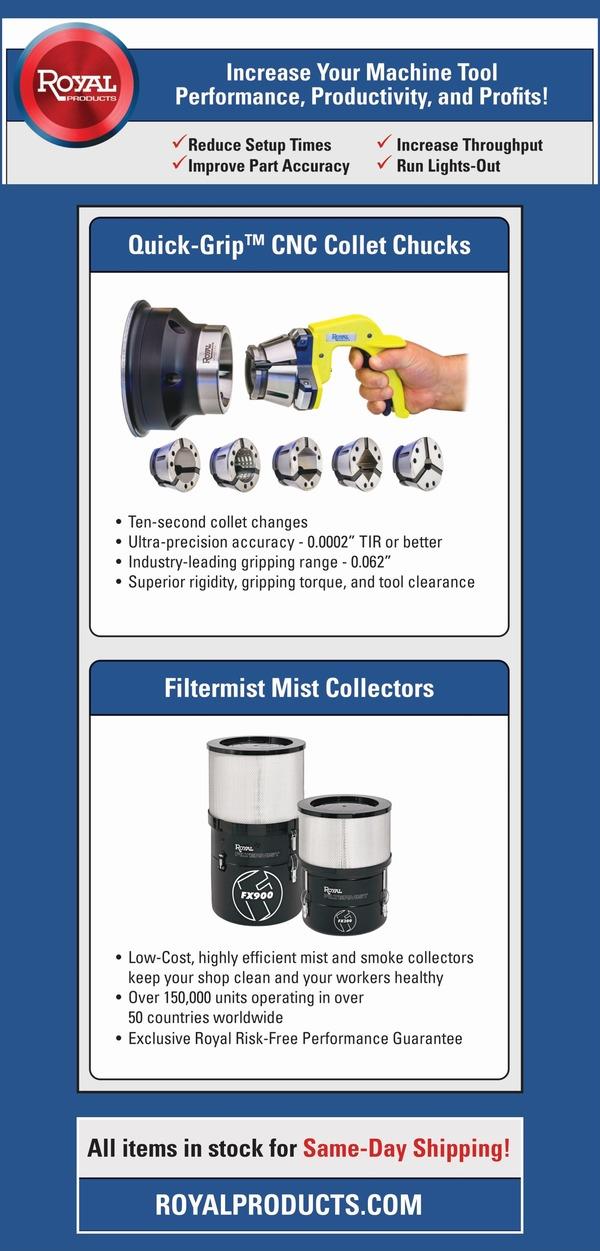
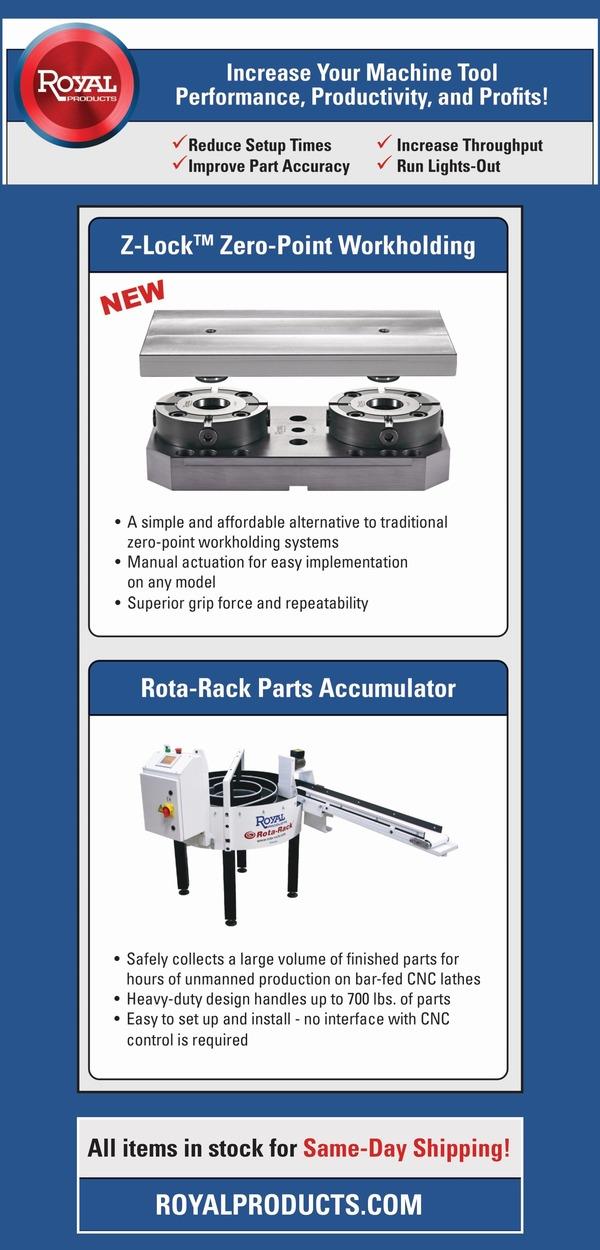

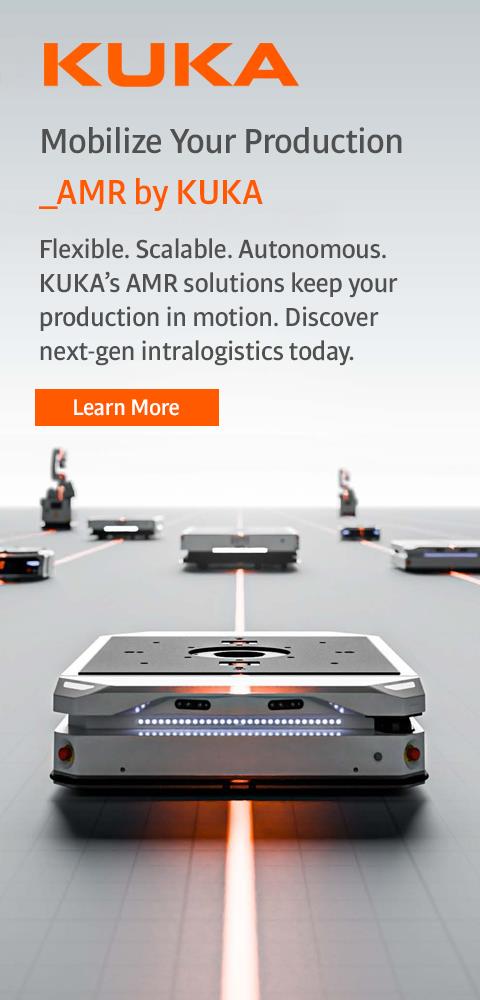
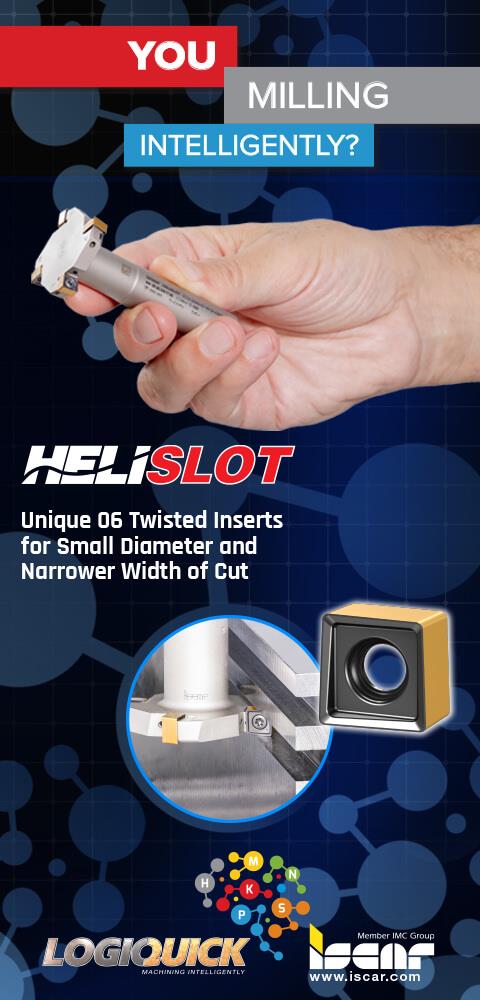
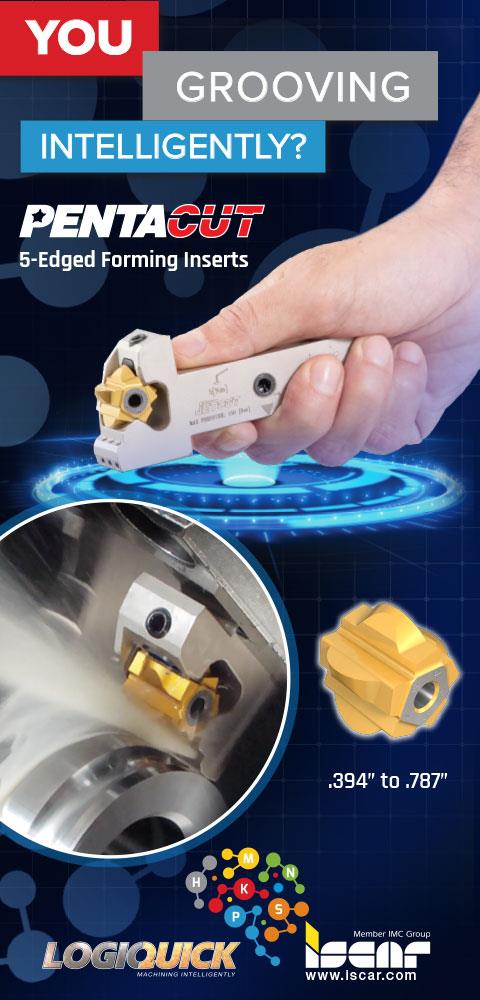
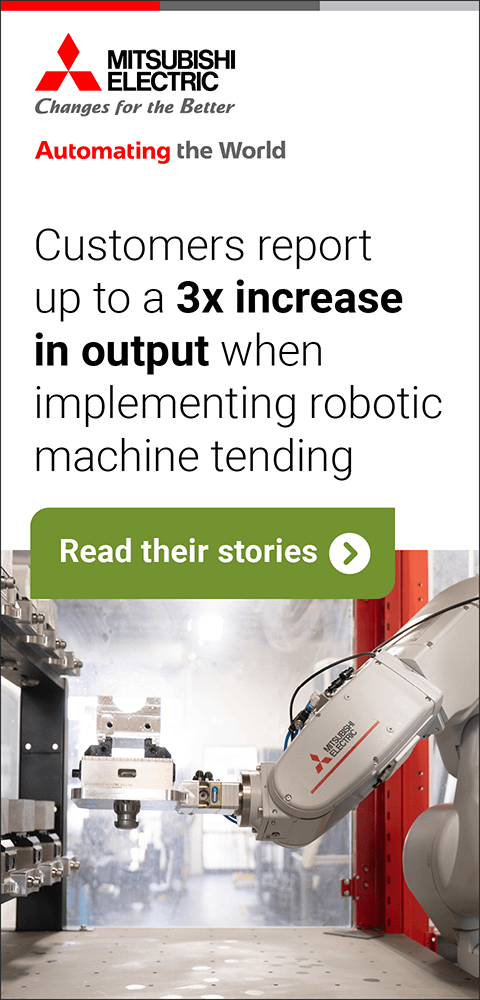
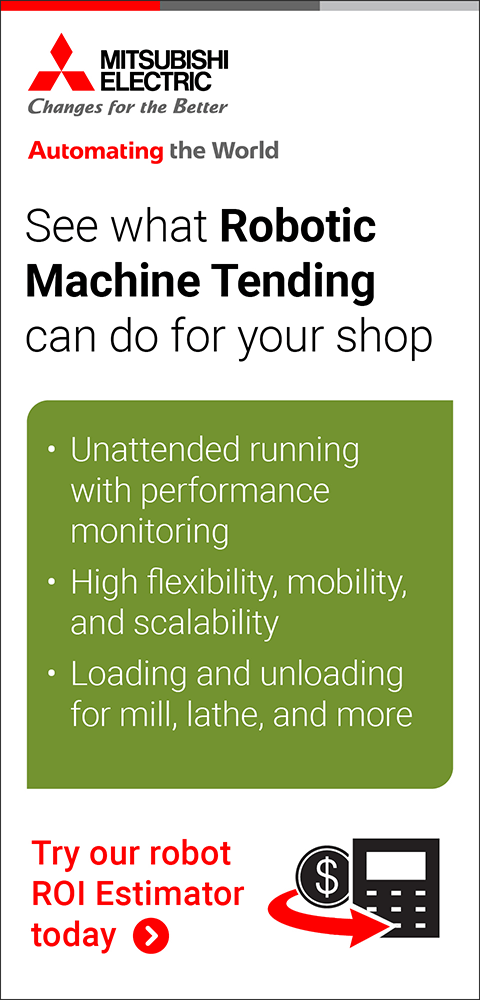
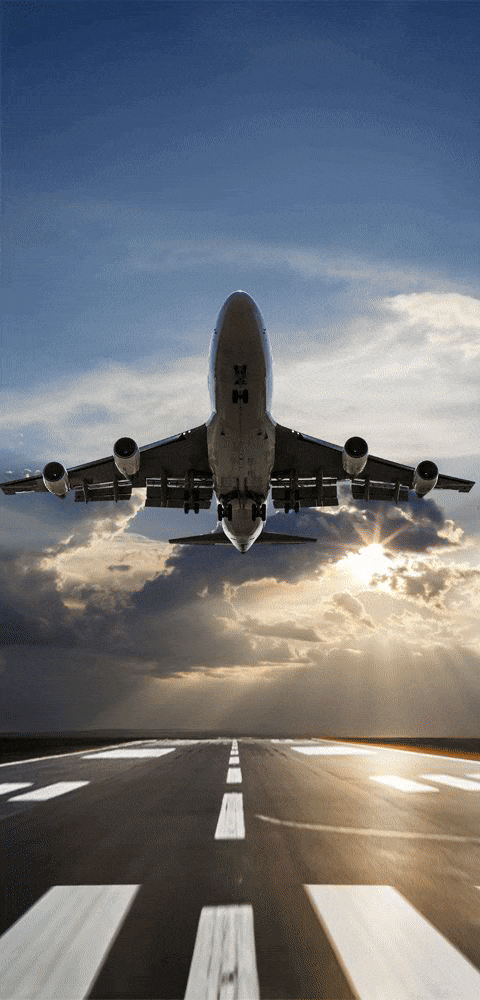
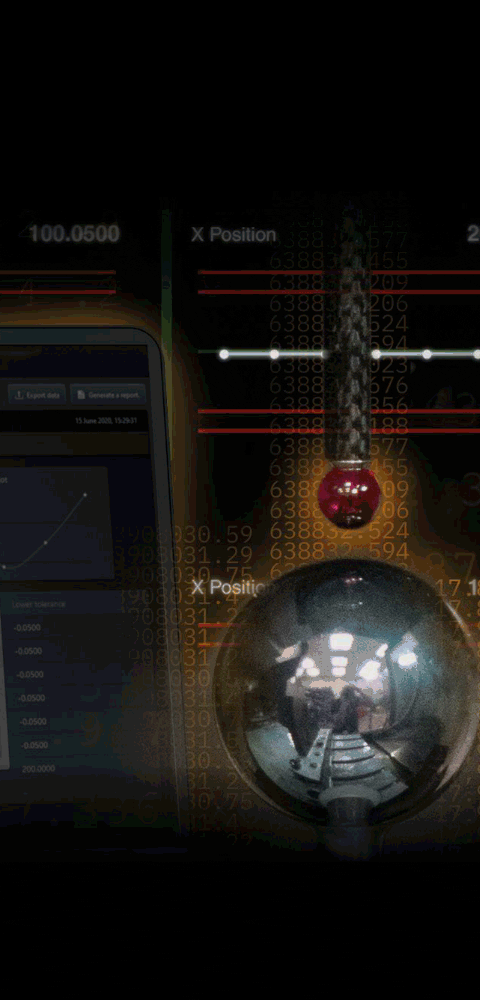
9-Axis Mill-Turn Center Achieves Double-Digit Output Improvements
April 1, 2017
Designed and built by the Starrag Group for the machining of medical and surgical components, the Bumotec s181 is a 9-axis mill-turn center featuring a second live tool workstation that generates up to 40,000 RPM milling to complement the 90-position automatic tool changer that serves the 11 kW, 6,000 RPM main HSK-40 spindle.
"This second workstation increases productivity by up to 40% by enabling up to five live tools to cut the rear side of one part while the main tool spindle simultaneously cuts another part," said a company spokesperson. "To ensure optimum productivity levels are maintained there is also an integrate tool breakage monitoring system."
Utilizing linear drives and high-level thermal stabilization to achieve 2.5 micron machining accuracies, the s181 is designed to perform as a single set-up machine. Additionally, with water-cooled axes, the machine has a 90-tool magazine, including grinding discs up to 80 mm diameter to accommodate all processing possibilities. The machine handles a maximum bar size of 3 mm diameter. Since it is a modular design it can be equipped with a range of productivity options, such as auto part loading to complement the choice of parallel jaws, tailstock, collet system or multiple workholding units, making lights-out manufacturing viable. Medical component manufacturers find the 37.7 sq. ft. (3.5 sq. m) footprint conducive to their plant environment.
End-user feedback has reflected process improvements such as:
- Producing stainless steel surgical instrument in four minutes compared with nearly seven minutes on a single-station machine
- Producing femoral balls in a single set-up and machining the cobalt chrome unit from bar stock to a surface roughness of Ra 0.04 micron
- Machining intervertebral implants in one piece from implantable peek with no burrs, which includes inserting x-ray marker pins without manual intervention - reducing cycle time by 22% compared to a sliding head machine and producing the finished unit in 9.38 min. compared to 12 min. (without pin insertion)
- Machining hip stem rasps from 48 mm diameter stainless steel bar stock in 1.4 hours compared to 2.3 hours on a standard vertical machining center.
For more information contact:
Starrag USA Inc.
North American Headquarters
Skyport Business Park
2379 Progress Drive
Hebron, KY 41048
859-534-5201
ussales@starrag.com
www.starrag.com
< back