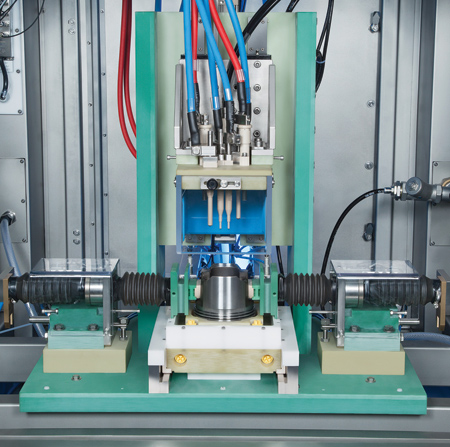
The ECM drilling unit for pistons. The ECM drilling process is safe and requires no post-treatment.
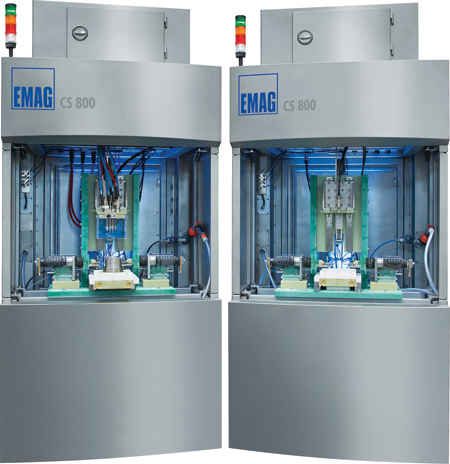
View of a complete ECM cell for the drilling process.
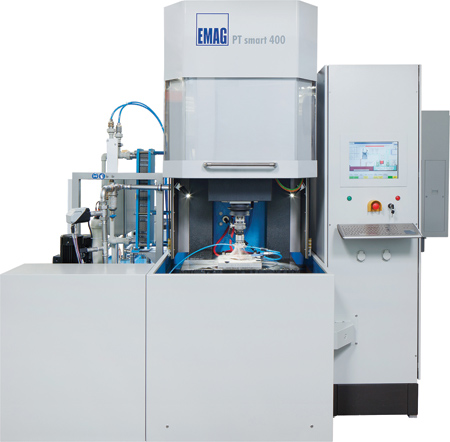
The ECM laboratory machine PTsmart can be found at the laboratory facility in Gaildorf. On it, detailed preliminary studies establish the feasibility of the process, while other EMAG staff determine the cost-benefit ratio of ECM in comparison to other methods.
"Downsizing the engine has been a dominating trend in the automotive industry for years," said an EMAG spokesperson. "Cylinder capacities are forever shrinking, while the application of turbocharging increases the pressure of the fuel/air mixture. This affects all components involved. Take, for instance, the piston. The extreme stress this component is put under in the modern engine calls for an improved cooling system. For the drilling of necessary bores, engine builders are increasingly using electro-chemical machining (ECM) technology offered by EMAG. This non-cutting production technology is designed to radically simplify the whole process."
The development of an innovative piston design with improved cooling system presented a considerable challenge for the production planner of one sub-supplier in particular. How was he to drill the holes in the piston in one efficient, large-volume process? The use of classical boring processes was causing a problem with the removal of the chips, because it proved very difficult to clean out the relevant cooling zones with absolute process integrity.
"The customer came to EMAG with this problem, originally thinking of using our ECM deburring process," said Peter Loetzner, President and CEO of EMAG L.L.C. "However, this idea supplied the impetus for the design of a machine that uses our innovative ECM process intelligently in the drilling of complex bores."
Ideal for Difficult Bore Transitions
"It should not come as a surprise that machine builders from southern Germany rely on the ECM method for this application," said the spokesperson. "The process is completely non-cutting. That means no ridges or burrs - ideal conditions for homogenous bore transitions. The fact that a number of bores can be drilled simultaneously on the same workpiece (and, if required, even on a number of workpieces at the same time), ensures that the technology scores highly when it comes to speedy processing."
During ECM, a DC or pulse source polarizes the workpiece as positive (anode) and the tool as negative (cathode). An electrolyte solution that runs between the two removes metal ions from the workpiece. There are neither mechanical nor thermal stresses involved. Because the shape of the tool cathode represents that of the hole to be drilled, material will only be removed at the desired points.
Simplifying the Production Process
At its ECM laboratory in Gaildorf, its headquarters, the EMAG experts from ECM tested the efficiency and the accuracy of the drilling process on the piston beforehand. The detailed preliminary studies carried out here do not only assess the general feasibility of the application - for instance, through material testing and by establishing the viability to hold given tolerances and to ensure reproducibility - EMAG also checks the economic viability of the ECM process compared to other processes. Based on the results of these checks and tests, they are able to quote actual cycle times and to define the machine concept most suitable for the component in question. This gives the customer a chance to assess whether the ECM process is the optimal solution for his or her particular production requirement.
"This is surely a central aspect of the quality of our work. We, of course, offer all of these accurate preliminary studies to our customers," said Loetzner.
"That the sub-contractor decided, on completion of the series of tests, in favor of the innovative ECM technology, has a lot do with the simplicity that ECM adds to the machining process," said the spokesperson. "The process chain is noticeably shorter than with traditional machining methods. How? The burr-free ECM drilling process can be added at the end of a process chain, performed on hardened components, if necessary, and requires no post-treatments."
"This brings an enormous advantage to the whole production solution," said Loetzner. "In the end, it means that the customer saves himself the expense of having to buy a deburring machine and, at the same time, reduces the production area requirement."
Passenger Car Sector
These and other advantages (for instance, minimal tool wear and total absence of adverse thermal effects on the workpiece) brought the success story of the ECM drilling process in the commercial vehicle sector to the attention of the passenger car sector. As a result, EMAG engineers developed, on request of an international automotive company, a tailor-made solution for the precision machining of camshafts. "The oil holes on the shaft can be drilled with precision and minimum tool wear using the ECM process," said the spokesperson. "The search for fuel-efficient engines also changes the design of their integral components. Conventional drilling methods often come up against insurmountable limits. ECM stands for the simplification of the process chain."
"The ECM process is usually found at the end of the process chain and rounds it off cleanly, efficiently and without complications. It can be a very persuasive argument," said Loetzner.
Aircraft Industry
The ECM process is also being used in the aircraft industry. "The ECM process has been used here successfully for years," said the spokesperson. Engine parts, blades and blisks are being finish machined using the ECM method. It makes for consistently good surface finishes. An extreme challenge is posed by materials such as Inconel. This tough nickel-based alloy can be cut only at the cost of heavy tool wear and extremely long cycle times, disadvantages that also apply to the drilling operation. A central engine part in Inconel has a large number of holes to be drilled. Until recently, the whole operation of the relevant chip removal process took more than 40 hours.
"Using ECM drilling technology, we can shorten the cycle time to approximately 10 hours. That represents a quantum leap for our customer's production," said Loetzner.
"Not only does this technology simplify the whole production process for pistons, camshafts, crankshafts and other components with complex bores and demanding geometry, it also helps to keep investment costs low," continued Loetzner. "Electro-chemical metal removal guarantees excellent component quality and low cycle times. We are convinced that these advantages will win out."
According to EMAG, five advantages of ECM drilling include:
- Simplicity: no ridge and burr formation, and consequently no need for chip removal
- Stability: The microstructure is not damaged by thermal influences
- Speed: Multiples of bores (and workpieces) can be machined simultaneously, requiring no subsequent deburring
- Flexibility: The process can be used both in hard and soft processing chains
- Savings: The life expectancy of the boring cathode is high; high tooling costs for deburring are avoided.
For more information contact:
Kirk Stewart
Sales Director
EMAG L.L.C.
38800 Grand River Ave.
Farmington Hills, MI 48335
248-966-4703
kstewart@emag.com
www.emag.com
SOUTHWEST
TX, OK, LA
Ric Lorilla
Regional Sales Manager
EMAG L.L.C.
248-595-1530
rlorilla@emag.com
AR
Steve Cox
Regional Sales Manager
EMAG L.L.C.
248-752-2298
scox@emag.com
SOUTHEAST
VA, NC, SC, E. FL, E. GA
Dave Fitzgerald
Regional Sales Manager
EMAG L.L.C.
248-595-1117
dfitzgerald@emag.com
MS, TN, AL, W. GA, W. FL
Steve Cox
Regional Sales Manager
EMAG L.L.C.
248-752-2298
scox@emag.com
NORTHEAST
WV
Dave Fitzgerald
Regional Sales Manager
EMAG L.L.C.
248-595-1117
dfitzgerald@emag.com
ME, NH, NY, PA, MA, RI, CT, NJ, DE, MD, VT
Troy Martz
Regional Sales Manager
EMAG L.L.C.
248-938-2430
tmartz@emag.com
MIDWEST
S. IN, OH, KY
Mark Comeaux
Regional Sales Manager
EMAG L.L.C.
248-938-2097
mcomeaux@emag.com
ND, SD, NE, KS, MN, IA, MO
Bill Konetski
Regional Sales Manager
EMAG L.L.C.
612-804-0857
bkonetski@emag.com
IL, N. IN
Tod Petrik
Regional Sales Manager
EMAG L.L.C.
248-470-2646
tpetrik@emag.com
WI, Chicago
Joe Thompson
Regional Sales Manager
EMAG L.L.C.
248-880-0233
jthompson@emag.com
MI
Mark Ashworth
Key Account Manager
EMAG L.L.C.
248-826-4242
mashworth@emag.com
WEST (none, use HQ)