
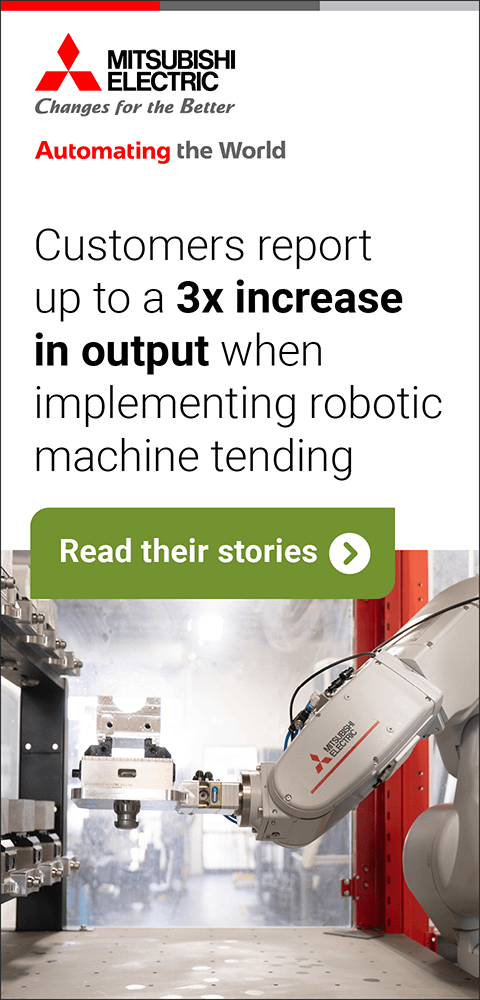
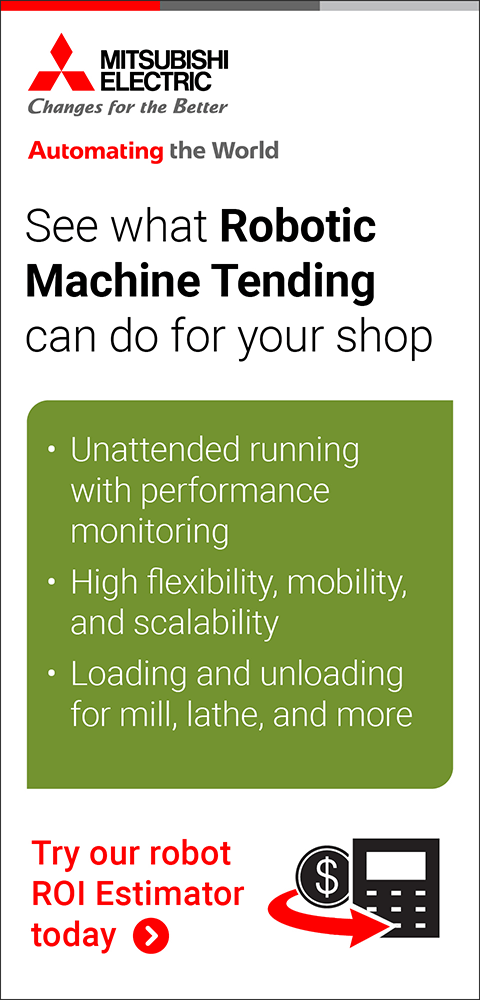
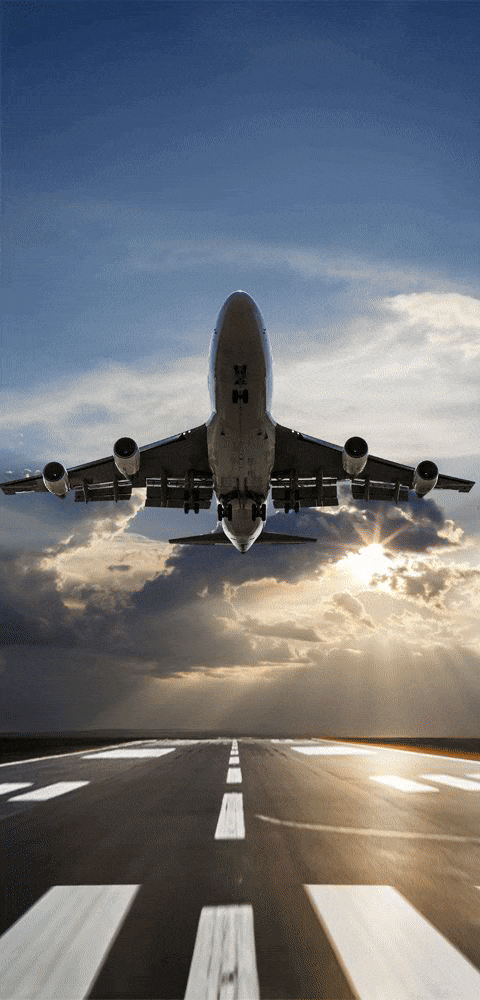
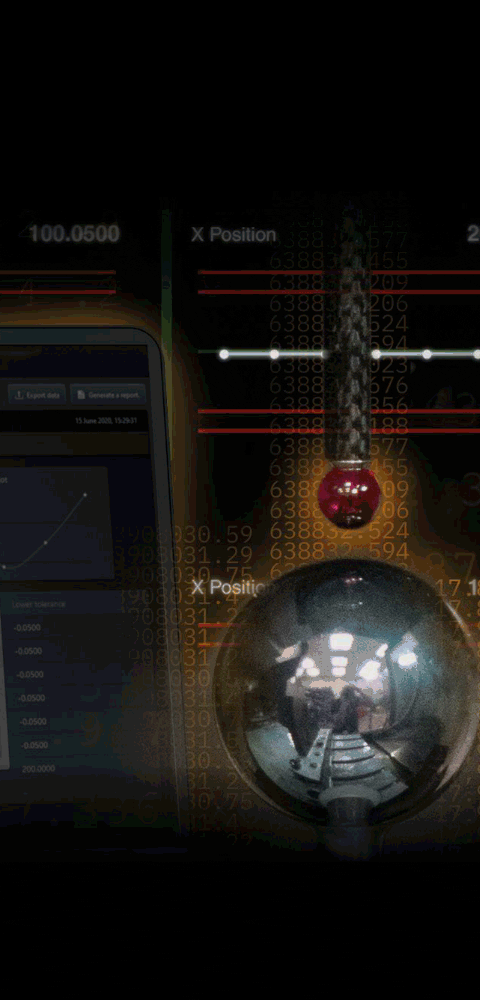
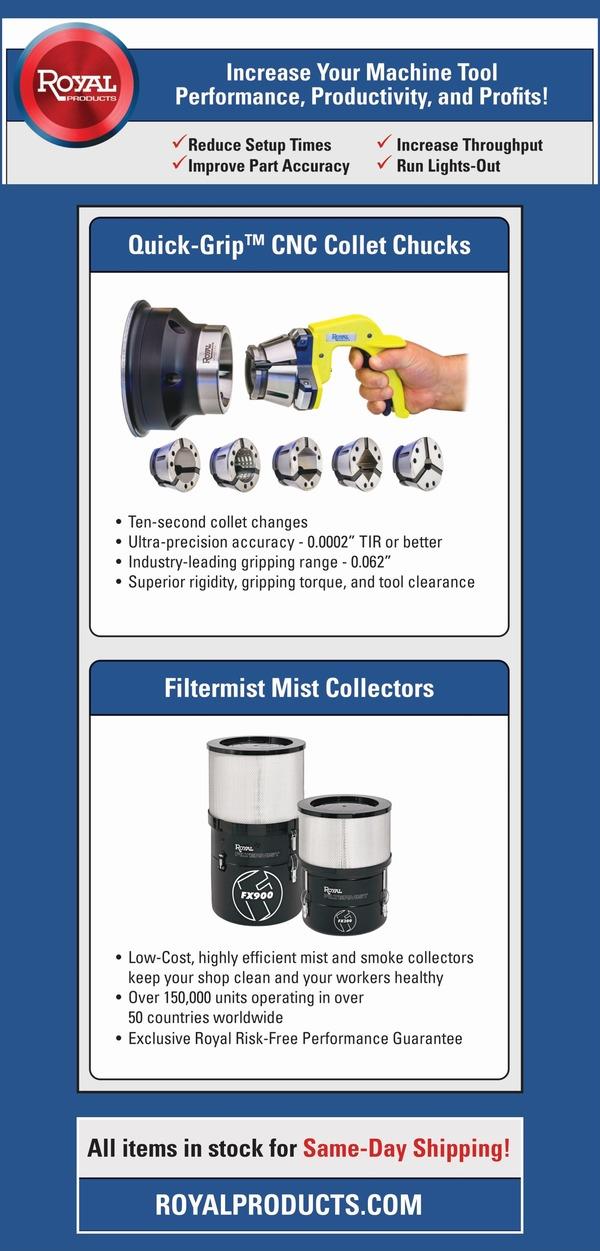
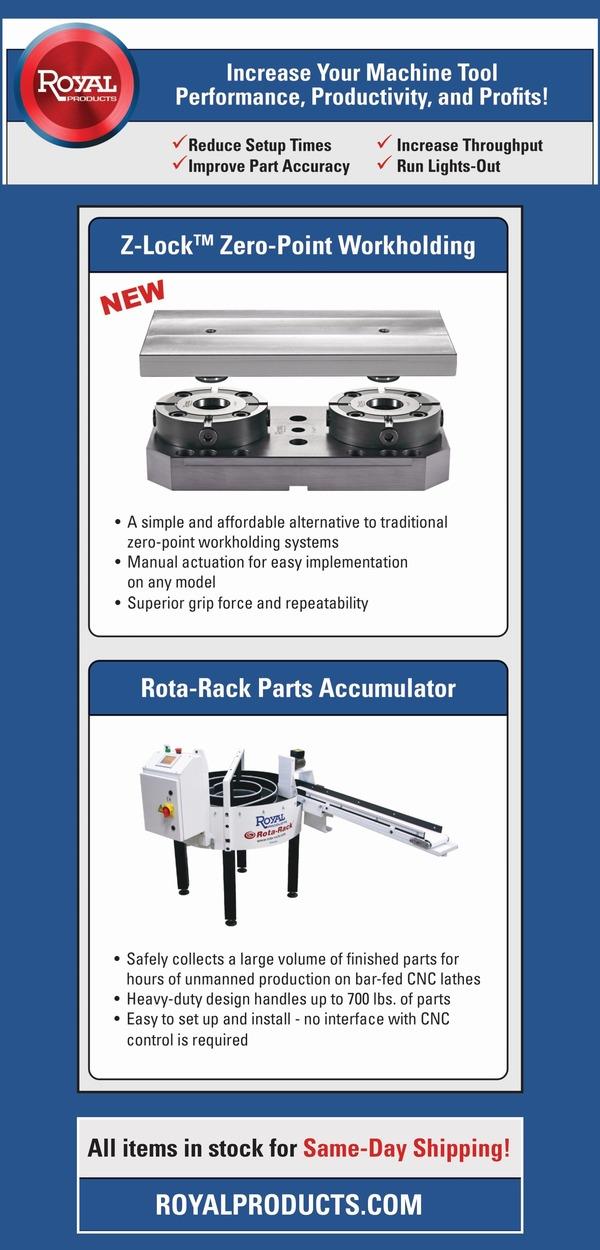

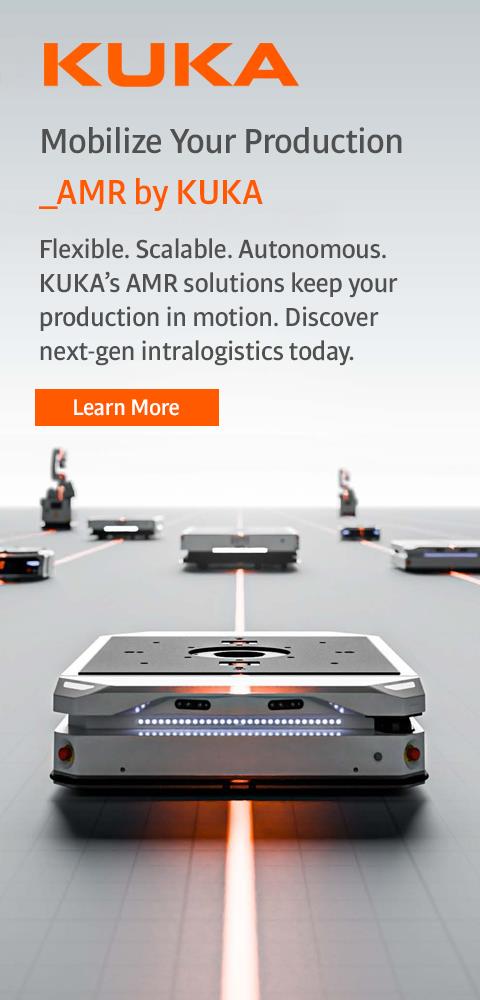
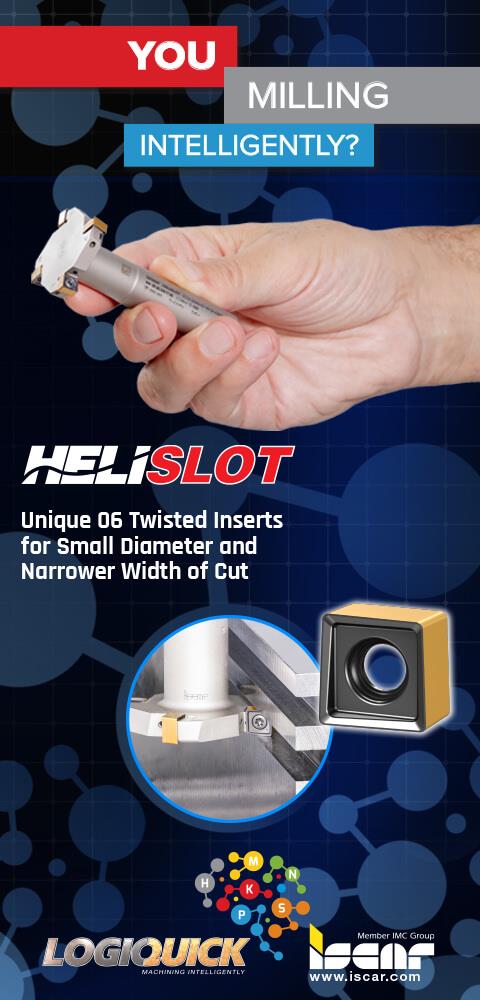
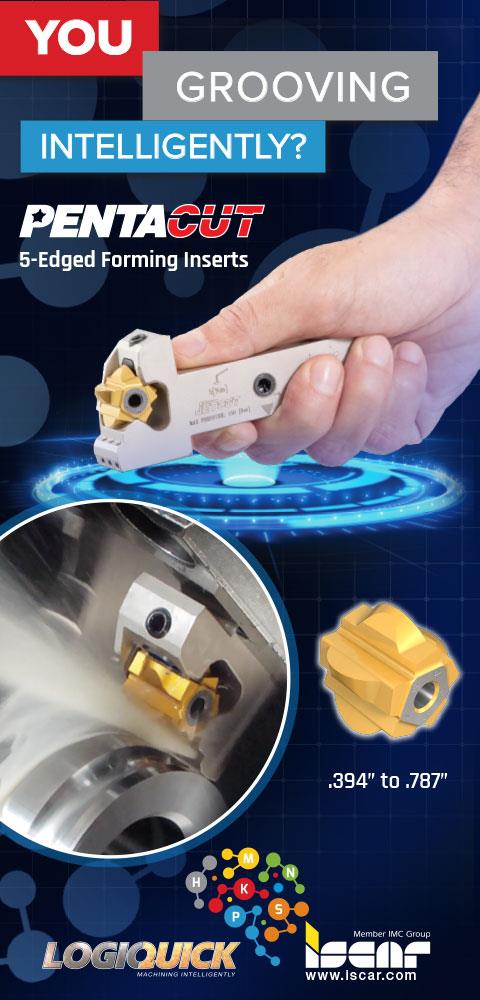
How to Form Your Own Inserts Using Thermal Drilling Tools
April 1, 2017
Formdrill, manufacturer of thermal drill bits explains the thermal drilling process. "It is possible to form your own inserts from the same part's material at a cost of about $.01 (one cent) - for the smaller diameters," said a company spokesperson. "This one cent is to be compared to the cost of added nuts, inserts or nipples and the labor to weld or install them. Resulting joints are as strong as, or stronger than, the equivalent diameter welded nut."
It is possible to perforate metal using friction. The main benefit of the process is that the material, that would normally be cut using the conventional drilling process, is used to form a bushing that triples the material thickness. This bushing can then be tapped to form your own insert, and be used instead of welded nuts, threaded nipples and inserts. These built-in inserts can be formed in UNC, UNF, NPT metric threads in steel, stainless, aluminum and copper from .032" to 1/2" thicknesses. The process can be used in drill presses, milling machines or CNC systems with the recommended horsepower and spindle speeds.
Arne Van Der Steen, President and CEO, Formdrill, stated: "Typical savings can be as much as $2 per joint since there is no need to cut the hole, clean the burrs, buy the nuts or nipples, weld them, clean the weld slags in the threads and test for leaks. When you multiply the $2 savings per joint times the millions of holes drilled per year, it is easy to cost-justify its implementation."
Another benefit of the process is that parts can also be designed with thinner and lighter materials. Lighter parts save fuel when they are part of moving vehicles. Thinner parts also save scarce materials and can significantly reduce the cost of the product.
For more information contact:
Formdrill USA, Inc.
4118 N. Nashville Ave.
Chicago, IL 60634
773-290-1040
info@formdrill-usa.com
www.formdrill-usa.com
< back