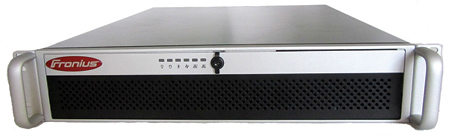
WeldCube, the documentation and data analysis system by Fronius, makes accurate and continuous quality assurance possible for up to 50 welding current sources.
The WeldCube solution from Fronius is based on an industry PC (IPC) with integrated software, which is used to connect up to 50 power sources via the network. The system is compatible with all digital Fronius series, with resistance spot welding system DeltaSpot and with intelligent welding device platform TPS/i. This enables the user to document and evaluate a wealth of data, including current, voltage, wire speed, welding speed and time, arc and dynamic correction, and job numbers during manual and robot-aided welding processes. This data is visualized in order to achieve an accurate analysis, then output via a Web browser, which enables the results to be accessed conveniently from any computer or mobile device.
"Due to plug & play, installing the WeldCube is easy," said a company spokesperson. "Once the system is up and running, virtually zero maintenance is required to keep it running. Fronius further develops this technology by providing updates that users can install themselves. Individual adjustments and programming are not a problem either because the standard functions can be upgraded by means of different packages offering a variety of new features. As a result, customized solutions tailored to meet the customer's exact requirements can be implemented."
The actual values for each power source can be documented both in relation to the machine and overall and in real time. The user is also able to continually monitor and evaluate additional and consumption data relating to gas, wire and energy consumption, for example. Set values, such as job data, can also be observed and recorded by the system for the entire service life of a welding system. When used in combination with Fronius' new TPS/i welding device platform, it is also possible to edit jobs and make comparisons across power sources. All of the values can be exported in different file formats or printed out from the IPC directly.
A range of analysis tools is available for fast and reliable troubleshooting, enabling Fronius customers to monitor the quality and output of their welding processes and, if necessary, optimize them. Continuous data analysis can also prevent production downtime and increase safety. "Different service packages ensure that the user gets a system that has been installed 100% correctly, is perfect for them and has a high level of availability - and that they can operate it without any difficulty," said the spokesperson.
For more information contact:
Fronius USA LLC
6797 Fronius Drive
Portage, IN 46368
219-734-5701 / 877-FRONIUS
sales.usa@fronius.com
www.fronius.com