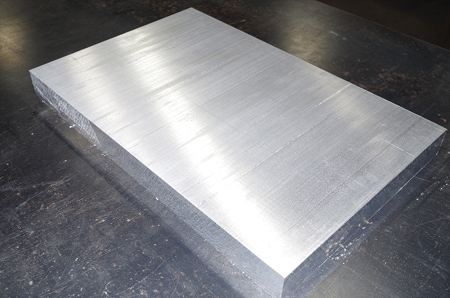
A block of aluminum prepped and ready for machining
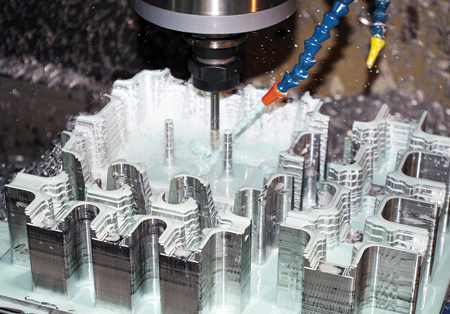
An EnviroPAK tooling component is machined
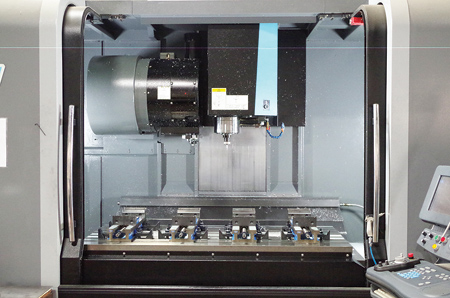
One of EnviroPAK's CNC machines
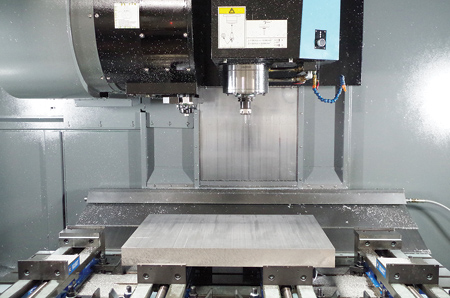
A block of aluminum secured with fixtures in preparation for machining
As the sustainable packaging market continues to grow, the design team at EnviroPAK has seen a surge in orders for molded pulp packaging. Molded pulp is a recyclable material that is produced completely from post-consumer recycled newspaper. In the last decade, more and more industries have turned to molded pulp as a sustainable packaging solution for products needing either protection from the bumps and bruises of shipping or organization within a given box dimension. With this rise in popularity comes a growing number tooling challenges that have to be conceptualized and executed by the design team. With the use of SolidWorks for CAD needs and SolidCAM for programming, the engineers at EnviroPAK have been able to keep up with demand through its state-of-the-art tooling and design department.
Most people think of two things when asked about molded pulp: egg cartons and the four-cup drink carriers from the drive-through. While these are both representative of molded pulp, they are not wholly representative of the packaging offered by EnviroPAK. Many of today's electronics are packaged in molded pulp, and most plumbing fixtures are protected by this sustainable, eco-friendly material. Customers are looking for packaging that offers protection, organization and in some cases, aesthetically pleasing enough to be displayed on retail shelves. Molded pulp is cementing itself as a viable option for thousands of applications across countless industries. And with 20-plus years of experience, the tooling and design department at EnviroPAK must keep up with demands.
When potential customers inquire about using molded pulp, EnviroPAK's first step is to create a CAD version of the molded pulp part within SolidWorks. This first step allows the customer to get a visual idea of what the molded pulp part will look like when completed. It also allows the EnviroPAK design team to make future revisions quickly and efficiently at the customer's request.
During this initial design phase, the EnviroPAK team works closely with the customer to determine the design intent of the project. What is the end goal of the part design? Is the part serving more as protection, organization or both? Does the part need to pass a drop test? How aesthetically pleasing does the design need to be? How many different SKUs need to fit into one part? These are all questions that need to be answered before moving forward with the design.
Once a virtual molded pulp part has been designed, it is sent electronically to the customer for approval. If a customer would like a physical representation of the design, EnviroPAK offers several possibilities. Using 3-D printed technology, the team can recreate the part with all of the critical dimensions of the design representation, allowing the customer to test the form, fit and functionality of the products within the part. Whatever the request, the design team works closely with the customer to ensure everyone is on the same page before moving into the tooling phase of the project.
After the EnviroPAK team receives customer approval, the tooling department begins designing the molds that will bring the conceptual design to reality. Depending on the size and the scope of the project, tooling design is generally completed within a week of customer approval, and machining and fabrication immediately follows.
Over the years, the tooling at EnviroPAK has had many different looks, eventually evolving into what it is today. Originally machined as a single piece of 6061 aluminum, today's tooling has become more modular to keep up with constantly changing customer demands. By designing and machining their molds to be assembled like a puzzle, the design and tooling teams are able to isolate and modify very specific areas without having to machine an entirely new mold.
This approach allows for a much faster, less expensive process. Customers are constantly adding new SKUs to existing product lines, and by using this modular philosophy, EnviroPAK is usually able to incorporate these new SKUs into the existing part design with minimum re-work to the molds.
Another mantra emphasized around EnviroPAK's tool shop is speed to market. The faster a design/prototype mold/transfer mold can be completed, the faster it can be used to produce tangible product. The faster that product can be placed in front of a potential customer, the more likely that project will continue to progress.
Depending on the geometry of the part design, the machining process can take anywhere from two to six weeks. Additionally, some of the molds machined by EnviroPAK are more than 4" in height. When this mold size is combined with an intensive geometry, a large mold base could take 35-40 hours to machine. All tooling components are finished with a more than adequate step-down, which provides a smooth enough surface for the cores to interlock during assembly.
After the machining process is complete and all components pass through quality assurance, they must be drilled and screened to create the porosity needed to form the pulp around them. The screening process involves wrapping all of the critical components in a single layer of stainless steel screen. While seemingly simple in description, this step is as critical to the process as any.
By combining a speed to market philosophy with a modular tooling approach, the tooling department at EnviroPAK has been able to consistently produce high-quality tools for more than 20 years.
Authored by Bill Kearns, Design and Tooling Manager, EnviroPAK Corporation
For more information contact:
EnviroPAK Corporation
4203 Shoreline Drive
St. Louis, MO 63045
314-739-1202
www.enviropak.com