
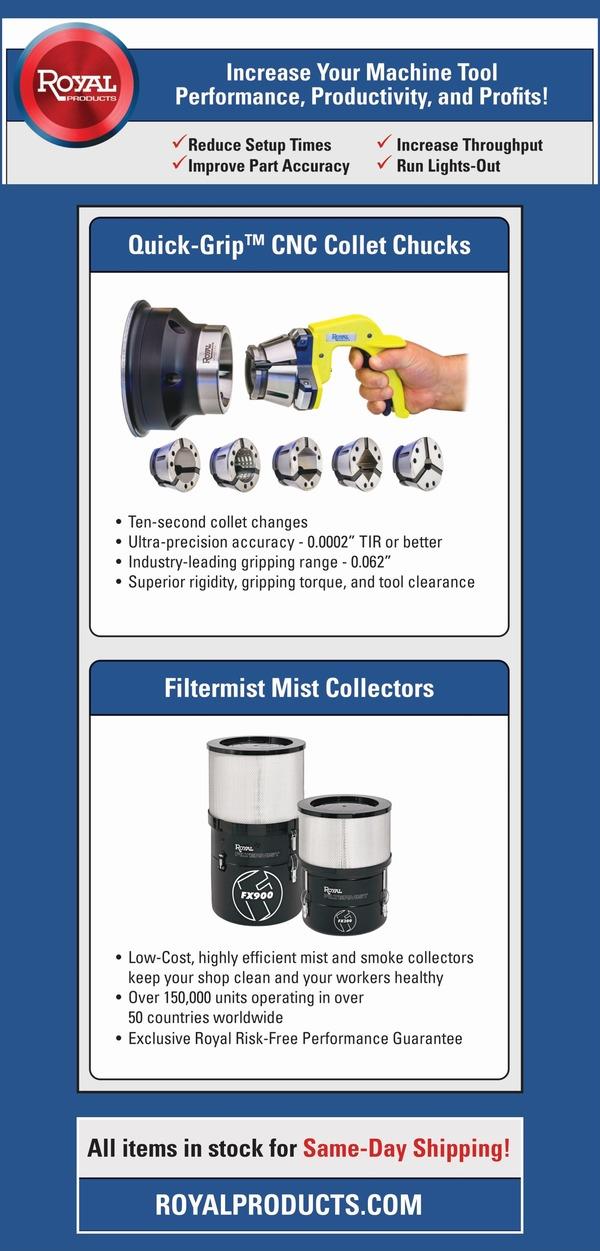
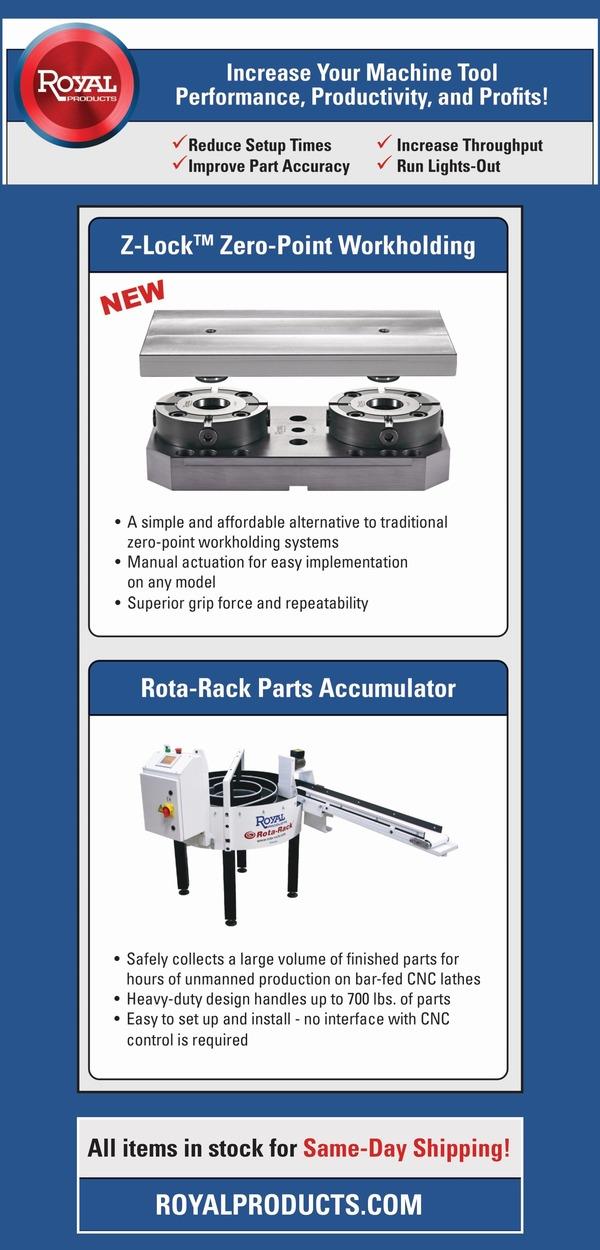

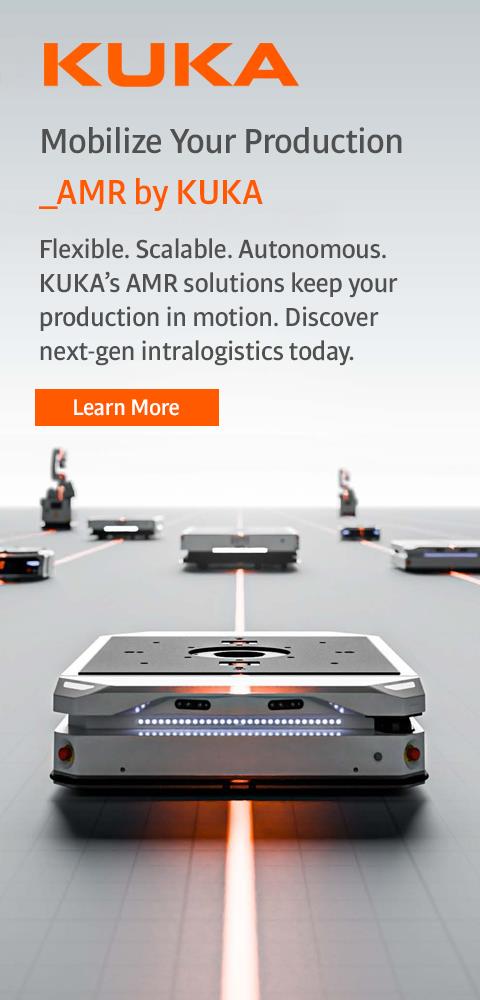
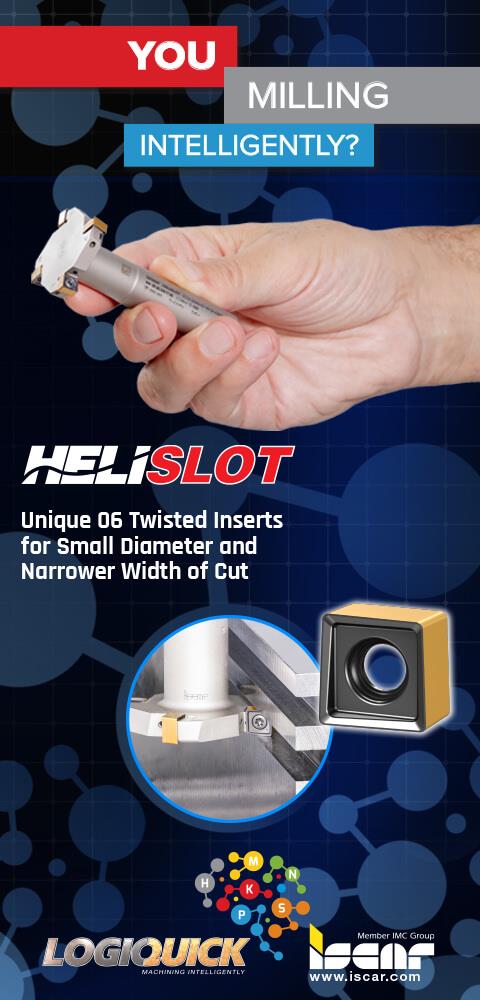
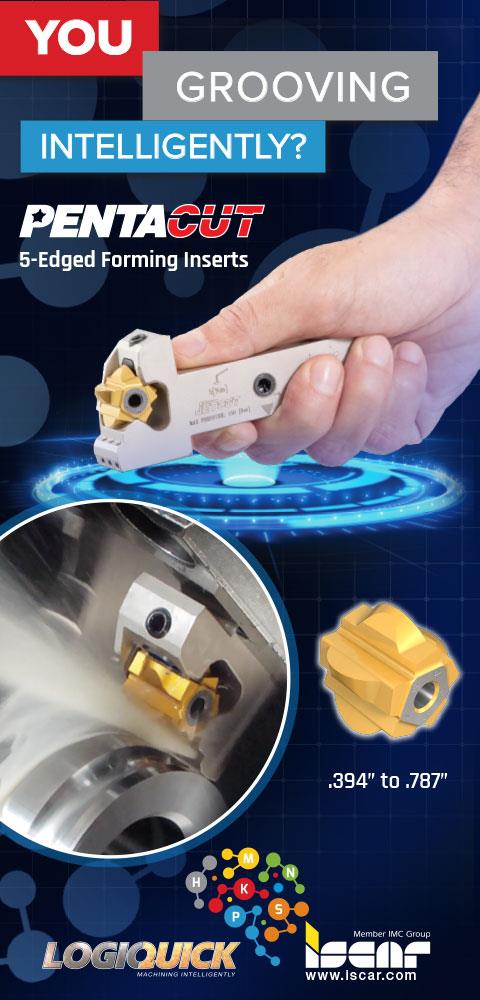
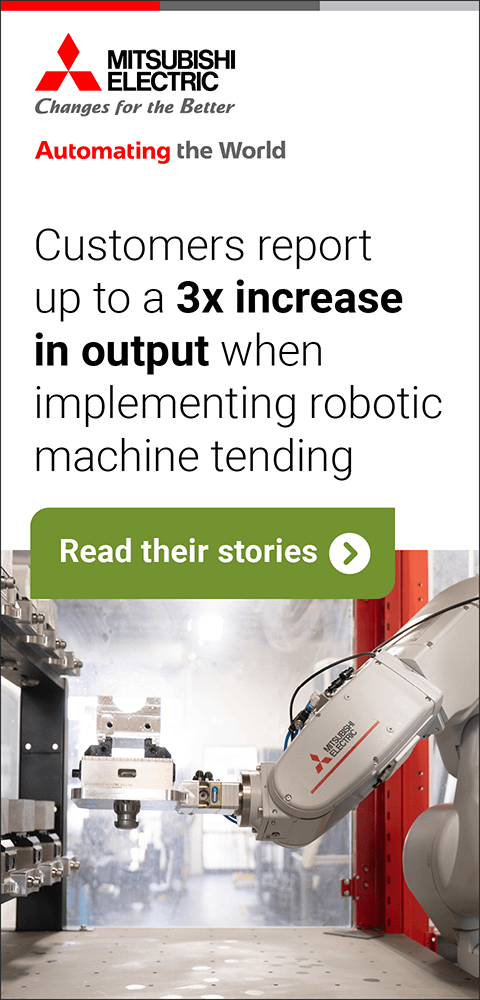
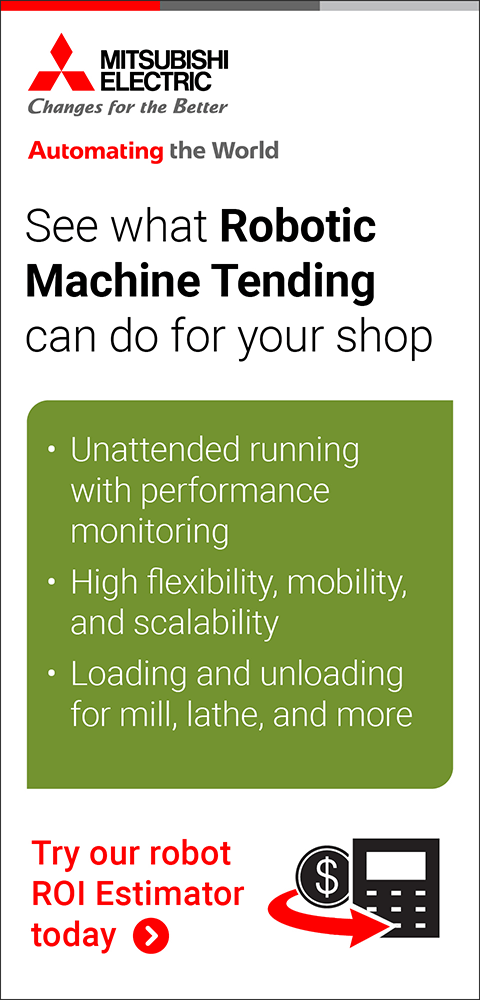
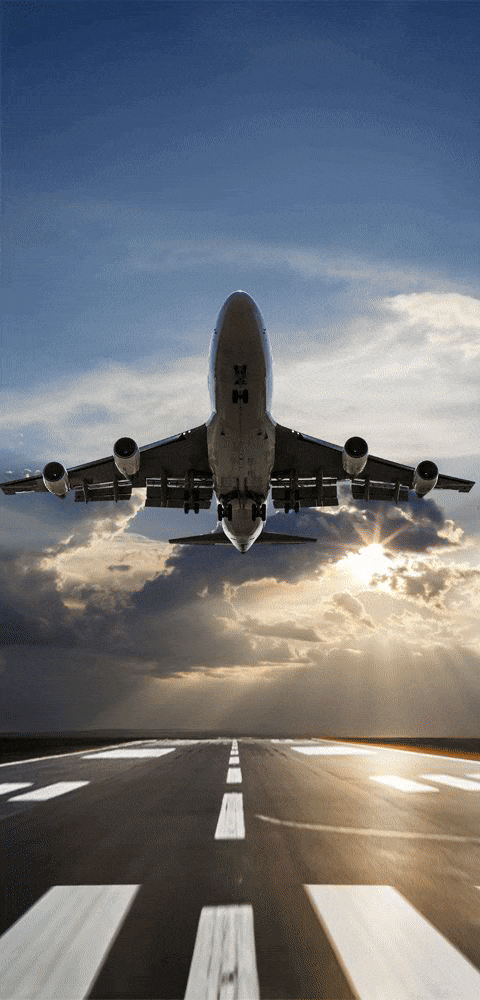
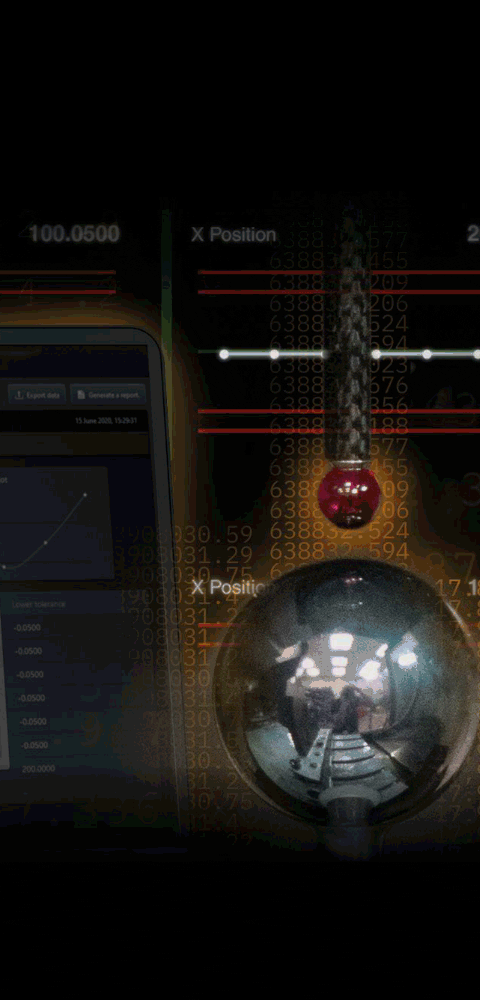
Transfer Crane Streamlines Powder Coat Oven Cure
March 1, 2016
TC American Monorail supplies a custom-configured LOWERATOR Transfer Crane with modifications to carry large loads directly into a 450 °F powder coat oven, without setting the load down. The crane design utilizes a special carrier that attaches directly to a large workpiece and travels with it through the assembly process, interlocking with strategically placed spur rails at various stations along the route. "The operator can engage positive mechanical rail interlocks in order to easily and safely transfer the load into separate bays for various operations, thus saving time and minimizing the potential for damage," said a company spokesperson.
This installation handles large steel weldments that would be difficult to transfer and set down repeatedly onto floor dollies for the various finishing operations involved. To handle the weldments, a 10 ton LOWERATOR crane was developed, with a bridge rail measuring 32' 10". First, the weldments travel through the various assembly processes. Then, they proceed to a series of finishing stations for blast clean/surface prep and drying. Lastly, they are run though a powder coat application, 450 °F oven cure and cool down. In each finishing station the weldment is transferred via interlocking spur rails to a separate bay for the pertinent operation. Once ready, the interlocking rails allow the load to rejoin the primary crane rail system and proceed to the next station. All of these operations are directed using a handheld wireless control. Since the carrier rail travels with the load through the entire process, the workpiece is never set down until the finished product has gone through final inspection and is ready for shipping. The LOWERATOR concept is designed to avoid unnecessary handling and potential operator injury. It also helps ensure uniform powder coat cure temperatures by eliminating the need for an oven roof slotted for an overhead hoist.
The LOWERATOR crane has 15 FPM lift speed and 18' of vertical travel. It uses a mechanical interlocking guide system to allow the load to swing freely when lowered and then automatically return to its home position when raised. This helps enable unimpeded operator access during the various work operations and secure re-attachment to the overhead rail for transfer to the next station. Other safety provisions include: overload limits, upper/lower travel limits, wire rope equalizers, backup manual control pendant and thermal protection. It also features a male/female rail interlock sensor that ensures two adjoining rails are properly aligned before they can be actuated.
Built for long service, the system utilizes end trucks rated for up to 19 tons and 50 FPM travel speed. The carrier rail is coated to withstand occasional exposure to cleaning chemicals and regular exposure to high temperatures. This is achieved by the use of epoxy paint, and bearings that utilize high-temperature non-silicone lubricants with drip pans to prevent load contamination. "The LOWERATOR's design streamlines the entire assembly process," said Josh Stern, TC American Sales Manager. "Its design features minimize unnecessary handling, damage and costs." The LOWERATOR crane system can be configured in many different ways to accommodate various requirements.
For more information contact:
TC American Monorail, Inc.
12070 43rd Street NE
St. Michael, MN 55376
763-497-7000
www.tcamerican.com
< back