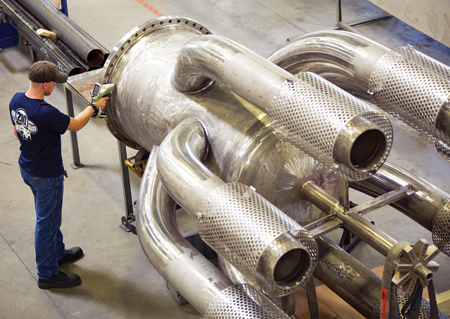
Portable analytical devices enable on-site quality control for a wide variety of metals and alloys. Handheld XRF (HHXRF) and handheld LIBS (HHLIBS) devices eliminate the need for time-consuming and costly laboratory testing
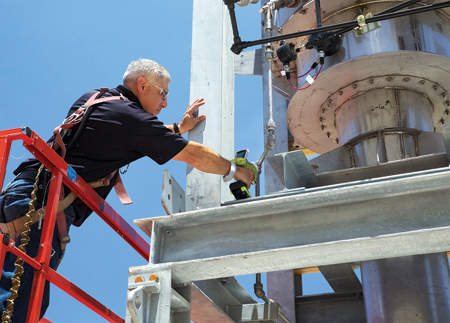
Lightweight HHXRF devices-such as the Thermo Scientific Niton XL5 Plus Handheld XRF Analyzer-feature a powerful X-ray tube to offer laboratory-standard material analysis at any point during the manufacturing process.
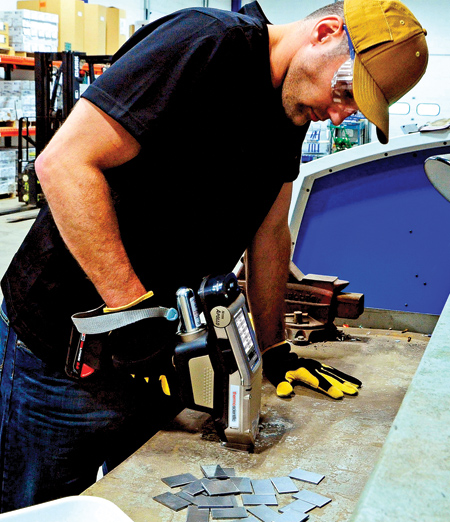
HHLIBs analyzers-like the Thermo Scientific Niton Apollo Handheld LIBS Analyzer-offer manufacturers versatile applications for their quality control procedures.
Quality control (QC) is a critical aspect of manufacturing, especially when the materials produced need to withstand severe conditions and mechanical stress. While manufacturers traditionally relied on destructive sampling and time-consuming, costly off-site laboratory testing, advancements in technology have revolutionized elemental analysis. Handheld devices employing X-ray fluorescence (XRF) and laser-induced breakdown spectroscopy (LIBS) have emerged as powerful tools for on-site analysis of metals and alloys, redefining QC processes.
Reshaping QC
Advanced engineering industries-including the aerospace, automotive, oil and gas and power generation sectors-rely on a variety of metals and alloys capable of operating under harsh conditions and withstanding significant mechanical stresses. For instance, the blades in gas turbines work constantly at high speed and under extreme temperatures, so it is crucial that manufacturers of these components ensure that the materials used in construction meet precise specifications to guarantee safety and performance. Efficient and accurate QC is essential, as any deviation from the intended product composition can have serious downstream implications.
Historically, QC procedures relied on sending samples to a laboratory for analysis. Unfortunately, this approach is not only destructive, but also time consuming-it can take several days to receive the results-and expensive. These issues led to the development of novel technologies that can be used on-site to deliver immediate results. Handheld XRF (HHXRF) and handheld LIBS (HHLIBS) devices eliminate the need for time-consuming and costly laboratory testing and allow manufacturers to operate with confidence and without interruption. These instruments are lightweight, compact and ergonomically designed. This makes them useful for analyzing materials even in hard-to-reach spots, allowing the use of ladders or rope-access methods while still ensuring full analytical capability for positive identification of metals and alloys.
Emerging Technologies for Precise Elemental Analysis
XRF and LIBS serve as complementary techniques in the QC process but differ in their underlying principles and applications. For instance, XRF uses a miniaturized X-ray tube to irradiate the sample, stimulating the emission of element-specific radiation known as X-ray fluorescence, which can then be detected and digitized to accurately determine the elemental composition of the material. In contrast, LIBS relies on powerful laser pulses to create a plasma on the surface of the sample material, causing each element present to emit a characteristic light signature. This light is detected by an optical spectrometer and used to identify which elements make up the sample, as well as to measure their individual concentrations.
Selecting the Appropriate Technology
Manufacturers must consider various factors-such as the sample type, the need for carbon analysis and adherence to specific regulations-when choosing an appropriate QC technology. On the one hand, LIBS measures light in the visible and ultraviolet (UV) spectrums, offering superior sensitivity for lighter elements, such as carbon. It also offers superior spatial resolution, enabling analysis of small areas through a focused laser beam. On the other hand, XRF excels at detecting heavy elements and can cover greater areas due to the divergence of the X-ray beam, making it more suitable for bulk analysis. XRF is also entirely nondestructive and requires no sample preparation, whereas samples analyzed by minimally destructive LIBS devices may require some surface grinding to achieve optimal results. Both technologies can distinguish between similar materials and identify alloy grades by comparing compositions to recognized international standards like ASTM International, AISI, German DIN, Chinese GB and many others.
Applications of HHXRF
HHXRF analyzers can identify all types of nonferrous metals and alloys, and they are sensitive enough to detect elements as low as atomic number 12 (magnesium). The technology is also especially well-suited to differentiating between various grades of stainless steel, even those with very similar composition. For example, it can distinguish between grades 301, 303, 304, 321 and 347 stainless steel, each of which have distinct applications. This makes HHXRF an ideal technique for analyzing the composition of many different materials at various stages of manufacturing, including ensuring the integrity of materials received from suppliers, as well as for high-stress applications, where subtle differences in composition can have significant consequences.
The technology is also particularly valuable in the automotive and aerospace industries, which rely on metal coatings to improve properties such as resistance to corrosion, wear and heat. HHXRF ensures that coatings are consistent and within the desired thickness range, preventing manufacturing issues and potential product failures. It is also widely used in the mining and exploration industries for on-site analysis of ore samples-allowing for real-time assessment-and in archaeology, where it is used for elemental analysis of artifacts without inflicting damage, providing valuable insights into their compositions and origins.
A Closer Look at HHLIBS
LIBS devices also have versatile applications; they mainly aid in analyzing low alloy steel and stainless steel and are ideal for measuring carbon concentrations. When it comes to stainless steel analysis, LIBS technology can differentiate between the L and H grades of 316 or 304 stainless steel, which differ by just a few hundred parts per million (PPM) of carbon. It also excels at measuring equivalent carbon content (CE) in low alloy steels, a vital indicator of a material's susceptibility to cold-cracking, which makes it an essential tool for assessing material compatibility prior to welding. The CE value depends on the concentrations of carbon, as well as other alloying elements also measurable using LIBS. These additional elements include silicon, chromium, vanadium, manganese, copper and molybdenum.
Using HHXRF and LIBS to Improve Manufacturing
HHXRF and HHLIBS technologies have transformed QC processes in manufacturing. These handheld analyzers bring laboratory capabilities to the production line, offering reliable, rapid and precise on-site analysis of material composition. The choice of device and technology depends on several factors-such as the specific application, sample type, elements of interest and regulatory compliance-but both methods can also be used in combination to provide comprehensive material identification. Ongoing improvements in XRF and LIBS technologies promise even better accuracy and expanded elemental detection in the future, empowering manufacturers in the aerospace, automotive, oil and gas, power generation and mining industries to uphold high quality standards, reduce costs and boost overall operational efficiency.
For more information contact:
For more information on these products, go to thermofisher.com/niton.
Authored by Mathieu Bauer, Senior Application Scientist and Associate Product Manager, Thermo Fisher Scientific
For more information contact:
Mathieu Bauer
Thermo Fisher Scientific
mathieu.bauer@thermofisher.com
www.thermofisher.com/niton