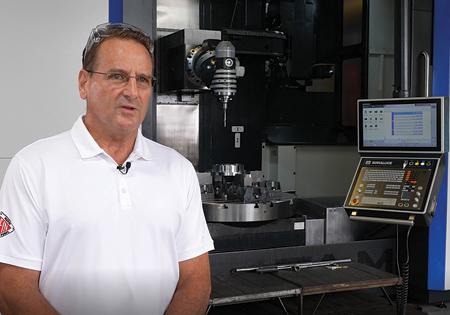
Jim Kinneary, President of Coffin Turbo Pump
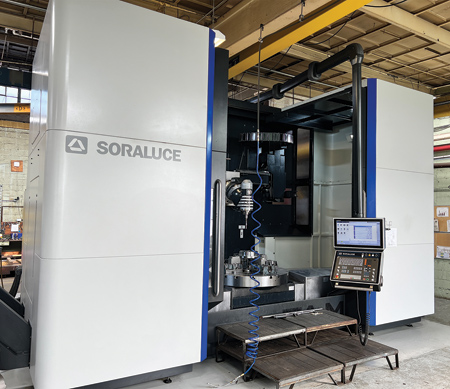
Soraluce TA-M-25 multitasking machining center at Coffin Turbo Pump
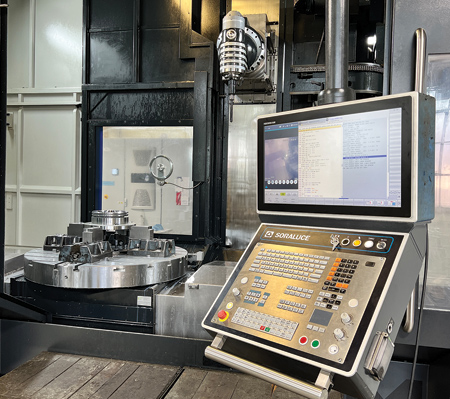
Work area inside the Soraluce TA-M-25 with a 1.2 meter integrated rotary table
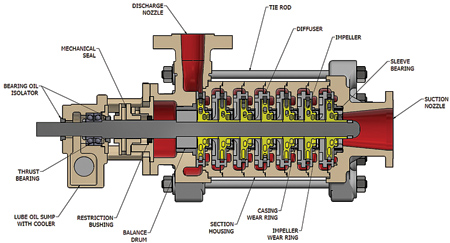
Cutaway of a Coffin Turbo DSR Ring Section Pump
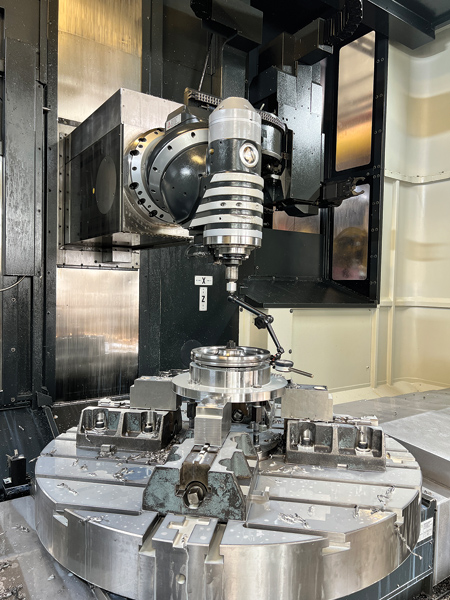
9" turbine wheel machined inside the Soraluce TA-M-25
Coffin Turbo Pump has realized a 35% to 40% reduction in machining time with the recent addition of a Soraluce TA-M 25 multitasking machining center, according to Jim Kinneary, President and CEO of Coffin Turbo Pump. The Soraluce is the largest investment made in over 20 years at Coffin Turbe Pump and, "it is a game changer," Kinneary said.
The Soraluce TA-M 25 is a versatile multitasking machine with a 1.2 m (47.24") integrated mill/turn table driven by 65 kW drive motor, with 3150 Nm torque and capable of a maximum turning speed of 400 RPM. For milling, the table provides full contouring capability and 0.001° indexing. The main spindle is powered by an inline motor located in the ram providing direct drive power to the head and spindle.
The machine includes the Soraluce H220T automatic indexing universal multitasking head, which provides 0.001° indexing in the vertical and diagonal joints. The spindle has maximum speed of 5,000 RPM and ISO 50 BIG PLUS taper.
Additional specifications include:
- 2,500 mm X-axis longitudinal travel
- 1,200 mm Y-axis ram cross travel
- 1,500 mm Z-axis vertical travel
- Rapid feedrate of 25,000 mm/min on all axes
- HEIDENHAIN TNC 640 CNC.
Complex pump housings that previously required up to 10 set-ups on multiple machines can now be done in as little as two set-ups, on the Soraluce. Operations performed on the single multitasking machine include milling, turning, broaching and even grinding.
Due to the machine's work envelope, the company machines not only its entire range of pump housings, but has also moved the forging for the turbine wheel that goes into the pump onto the Soraluce. The turbine wheels range from 22" diameter down 9" diameter, and all are now machined in just two set-ups with a high level of precision.
"What we have found is that the precision of the turbine bucket groove-the groove that holds the buckets into the turbine wheel when it is rotating at very high RPM-is so precise when it comes off the Soraluce the assembly time has been reduced as well as the variation of the types of buckets," said Kinneray.
The material being machined on the steam end of the turbo pump has a Brinell hardness of about 206, and the tolerances that need to be achieved fall within a thousandth of an inch. Even at this high level of precision, Kinneary confirms the machine is more than capable.
Marcos Guevara, the CAD/CAM specialist programmer at Coffin Turbo Pump, noted the benefits of the Soraluce Dynamic Active Stabilizer (DAS+), which has reduced chatter and increased tool life, further reducing vibrations during machining. According to Guevara, they do a lot of interrupted cuts, so the DAS system has been a big help.
Soraluce DAS+ provides active dampening throughout the entire range of machine travels. Other Soraluce advanced technologies included in this machine are: Dynamic Head Calibration, Adaptive Control, Chip Breaker and Virtual C-Axis. The machine is also equipped with the Soraluce Grinding Upgrade for Multitasking machines. The grinding upgrade includes special telescopic covers, special modification for the multitasking head to adapt an external pipe to provide coolant to the wheels, grinding cycles in the CNC, wheel dressing system and additional scrapers to protect the linear guides.
"We do the pine trees, these are grooves where the buckets are installed. We will do broaching of the key ways. We will drill and treadmill and we will be grinding the taper board on the part. In the past, every operation was done in a different machine, but now we have only one set-up time and we will achieve that probably under an hour," said Guevara, "The times savings is significant."
Coffin Turbo Pump recently launched a new product line called the DSR line of pumps, which is a more commoditized piece of equipment. Given the increased level of competition the DSR line will face, the reduced set-up times and increased throughput offered by the Soraluce are critical to its success. "We are able to compete and we have successfully launched that new product line," said Kinneary.
Coffin Turbo Pump has a long history in manufacturing highly engineered boiler feed pumps for various industries, including the nuclear industry, power generation, offshore oil and gas and the marine industry. Coffin's history began in 1925 when J.F. Coffin designed a boiler feed pump for steam locomotives, which gradually moved into the marine industry. At one point, 80% of all ocean going, large ships carried Coffin steam turbo pumps.
For more information contact:
Coffin Turbo Pump
326 South Dean St.
Englewood, NJ 07631
800-870-4701
info@coffinpump.com
www.coffinpump.com
Select Machining Technologies
910 Day Hill Road
Windsor, CT 06095,
256-508-0805
www.selectmachiningtech.com