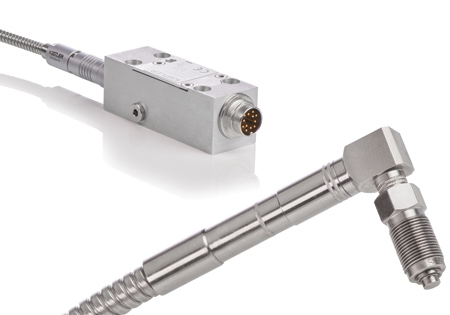
The 4004A miniature melt pressure sensor from Kistler allows for measuring pressure and temperature directly in the hot runner at up to 350°C.
Kistler offers Type 4004A piezoresistive melt pressure sensor. Featuring a front diameter of 3 mm, this sensor can be operated directly in injection nozzles and small extruders. It can measure pressure and temperature in direct contact with the plastic melt. The 4004A is equally ideal for use with hot runner systems in injection molding and in additive manufacturing.
"The plastics processing industry is following a clear trend: intelligent molds, injection molding machines and 3D printers are supplying users with the maximum possible information about the process. As well as enhancing transparency, this allows ongoing optimization of the production process," said a company spokesperson.
The spokesperson continued, "But now, Kistler offers the innovative 4004A melt pressure sensor. With an operating and measurement range of up to +350 °C, it can be used directly in the hot runner to deliver precise measurements of pressure and temperature in injection nozzles and extruders. Due to its ultra-compact dimensions-its frontal diameter is merely 3 mm-this sensor can also be installed in small nozzles with no critical changes to injection behavior."
For the two different applications, the 4004A features two separately calibrated pressure ranges that offer high accuracy: up to 2,500 bar for the hot runner in injection molding and up to 1,000 bar for additive manufacturing (AM). "The measured melt pressure can be used to control the plant in order to optimize the flow behavior of the plastic melt," said Dr. Robert Vaculik, Head of BU Plastics at Kistler. "If the process parameters remain constant but there are changes in the pressure signal, that would suggest possible anomalies-deposits in small nozzles, for example, wear in the mechanics or melt backflow. Process monitoring with this degree of accuracy was never possible until now."
The sensor allows easy access to its internal key parameters via Transducer Electronic Data Sheet (TEDS). Due to a sensor diaphragm made of hardened steel and its IP65 degree of protection, the 4004A can be used for applications involving fiber-reinforced plastics. It can also be operated without problems in the medtech and food packaging sectors-no media such as oil or mercury are used to transmit the signals.
The temperature-compensated pressure signal can be accessed via the analog output or the sensor's RS232 interface, so it can be acquired and visualized with measuring equipment such as the ComoNeo process monitoring system by Kistler.
Vaculik concluded: "With this innovation, we are offering our customers a digital measuring chain for hot runner and AM applications-the key to smarter monitoring of the melt flow in hot runner systems as well as AM systems."
For more information contact:
Kistler Instrument Corp.
30280 Hudson Drive
Novi, MI 48377
248-668-6900
sales.us@kistler.com
www.kistler.com