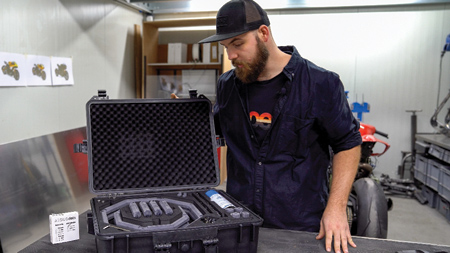
The modular set is housed neatly arranged in a carrying case.
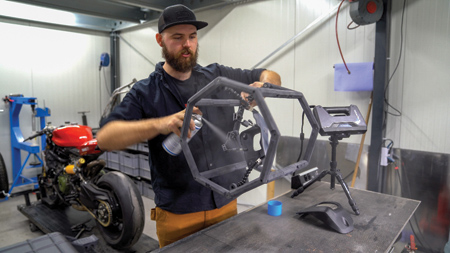
The assembled frame and fixed part are matted with the scanning spray AESUB blue.
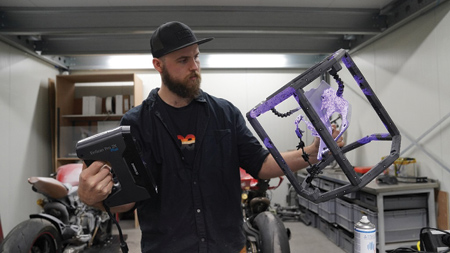
The reference points known as AESUB dots are placed on the frame. As a result, the parts do not need to be glued.
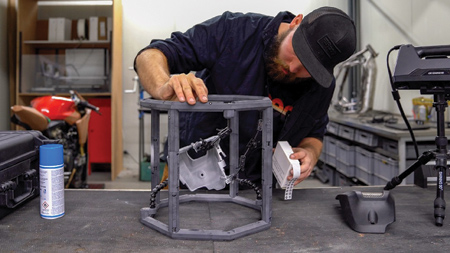
The part is matted and can therefore be scanned easily. The matting layer sublimates after around one hour, which means the part does not need to be cleaned.
"If component parts are to be measured all the way round, specialized equipment is needed," said an AESUB spokesperson. "For small parts, fixed, customized devices are often too pricey. That is why there is now a modular reference frame available which, in combination with reference markers and a scanning spray, offers a suitable alternative."
A modular frame from AESUB consists of approximately 30 individual components from which a measuring device with a diameter of 200 mm or 300 mm is assembled within just a few minutes. Its constituent elements are black, and hence, suitable for scanning tasks. They are produced from aerospace material and are only half the weight of comparable aluminum components. Due to additive manufacturing (AM), the plug-in and screw connections are directly integrated, which means that the components can be screwed or fitted together without the need for tools. The set is housed neatly in a carrying case. It saves space and is particularly suitable for mobile use.
The height of the frame is based on the size of the part. The components present in the set permit a maximum set-up height of 300 mm. With add-on sets, the frame height can be extended in increments of 100 or 200 mm. The part to be measured is held within the frame by hinged brackets.
"For orientation purposes, most scanners require reference points, which are generally glued directly onto the parts," said the spokesperson. "But depending on the nature of the surface, removing them may be problematic and may damage the part. With larger parts, there is the risk that individual points are missed."
With the reference frame, it is no longer necessary to glue the parts because the points are applied directly on the frame. Hence, they can also be used as a reference for all further parts. By means of the reference frame and the points, the dimensions of the part can be captured in one all-round scan-rapidly and precisely.
"Since the contours of black parts are barely visible, scanners often find them hard or impossible to detect," said the spokesperson. "Equally difficult is the measurement of shiny and reflective parts. With transparent surfaces, the scanner light is not reflected by the part but passes through the surface. Hence the structure cannot be captured."
"Reflective surfaces are similarly problematic as they do not reflect the light but focus it," continued the spokesperson. "And the surface structure is also crucial to the measurement result. For example, big indentations cause reflections on the walls, thereby influencing the light pattern. The interference manifests itself in the scan as "artefacts" or inaccurate data."
To help ensure error-free data collection, shiny, reflective or black parts are prepared prior to the scan. A scanning spray is the easiest way to do this.
"However, the disadvantage of many conventional scanning sprays is that they contain pigments and also titanium dioxide, which is a health hazard and is reputed to have carcinogenic effects, for example," said the spokesperson. "More and more companies are stopping their use of conventional sprays. A further shortcoming is that the spray layer sticks stubbornly to the surfaces and is difficult to remove. It is not uncommon for parts to be damaged or even become unusable from being cleaned.
"With these newly developed scanning sprays from AESUB, these disadvantages are a thing of the past," added the spokesperson. "They contain no pigments, and there is no risk from titanium dioxide. What is more, the applied layer evaporates automatically, meaning no cleaning of the measured objects is needed."
After spraying, a homogenous white layer is generated within a few seconds, which produces high contrast values on the surface. The scanner can now detect the structure without a problem. The layer thicknesses of the AESUB spray are between 1µ and 15µm. The matting layer is touch-dry, which means that the parts can also be handled and repositioned during the scanning process. The sublimation times of the AESUB sprays vary between 4 and 12 hours depending on the spray variant.
The AESUB spray and dots are a handy addition to the reference frame. The reference points can be placed on the object to be measured both before and after spraying with the AESUB scanning spray. The reference points stick to the spray layer and can be easily removed.
For more information contact:
AESUB
info@aesub.com
www.aesub.com