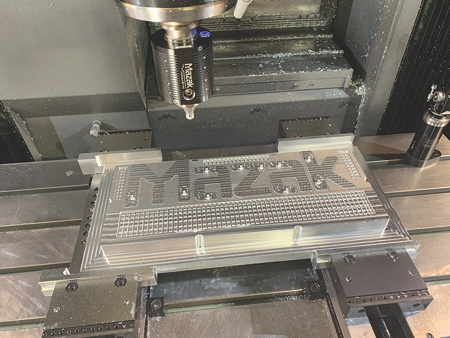
The vacuum table is a lithium battery containment assembly ported to serve a dual function as a heat exchanger assembly. This assembly was joined using FSW on a Mazak vertical mill using our proprietary Hybrid FSW technology. Although this part was designed by Mazak for demonstration purposes, it is like those assemblies designed to contain and cool batteries in electronic vehicles.
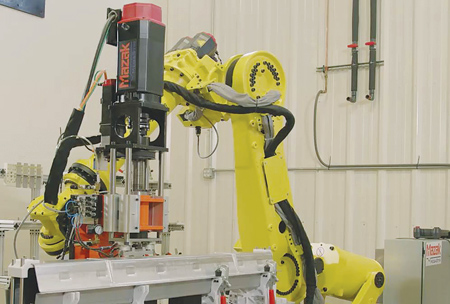
Mazak MegaStir Friction Bit Joining
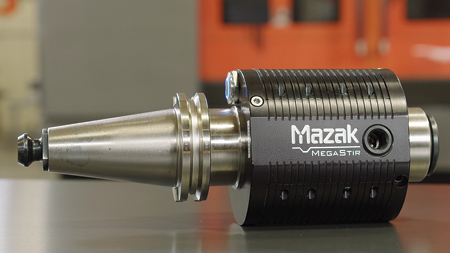
Mazak MegaStir diamond FSW, an intelligent FSW toolholder. Mazak?s patented diamond FSW tools come thermocouple ready to monitor temperature and are available in standard or customized versions for unique, customer-driven applications.
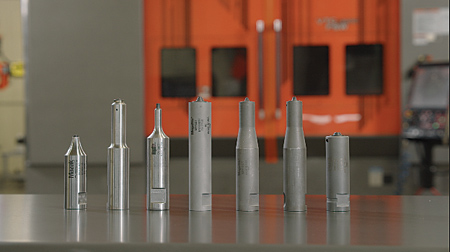
Tools utilizing polycrystalline diamond used in the Friction Stir Welding process
Invented some three decades ago as more of a theoretical experiment than a practical application, friction stir welding (FSW) has evolved as a leading joining and forging technology driven by the need for production of lighter, stronger components in almost every manufacturing sector. From automobiles to aerospace and consumer electronics, FSW provides a highly efficient method of joining metals with low melting points such as aluminum, copper and brass that would be difficult to weld using a standard fusion process.
FSW employs a cylindrical shoulder tool with a profiled pin that is rotated and plunged into the joint of two pieces of metal. The friction generated by the downforce of the spinning tool plasticizes the metal before it reaches its melting point. No filler wire or shielding gas is needed as the plasticized material moves to the toolholder's trailing edge where it is forged and then cooled to a solid. Rotation, force and friction are the only components of FSW.
Joints are formed well below the base metal's melting point, which almost invariably results in a metallurgical bond superior to that of fusion welding. Standard steel pin FSW creates full-penetration, defect-free welds for several kilometers with lower setup time and consumables cost, improved safety and from any position or orientation.
Stirring up EV Battery Tray Production
Aerospace manufacturers initially seized on FSW in the late `90s as a method for producing large aluminum components without weld defects. More recently, FSW has become instrumental in the automobile industry's transition from internal combustion engines (ICE) to electric vehicles (EV), which places a premium on manufacturing increasingly lighter components. Aluminum, aluminum alloys and exotics now play a significant role in that sector, posing unique challenges to metal joining applications. This industrial transition also provides a timely introduction of some of the latest manufacturing technologies with FSW being in the forefront of adopted technologies.
Used in a variety of lightweight EV component fabrications, FSW is especially suited to battery trays and their complex cooling systems required for optimum battery performance. Battery temperature is maintained with integrated cooling channels or tubes throughout the tray, which sits low in the vehicle and in many cases runs from axle to axle. While subtractive milling is used to create shallow channels in the floor of the tray, FSW is an efficient method of bonding cover plates to the assembly.
Mazak's MegaStir system efficiently integrates FSW with subtractive machining for multitasking versatility on the same machine. This hybrid platform provides the ability to join assembly components on the same machine with the same operator and consolidates factory floor footprints while decreasing capital expenditures.
For this process, an intelligent FSW toolholder can be pulled from the tool magazine of a Mazak vertical or horizontal machining center to perform FSW operations. The toolholder collects temperature, Z-axis load data and other information to enable operators to manage the FSW process. FSW software available through Mazak's MAZATROL Smooth CNC allows real-time monitoring of FSW's three main processes - plunging, traversing and extracting.
A Diamond for the Rough
With the need for manufacturing of more exotic lightweight alloys, comes the demand for tools that can efficiently and cost-effectively machine them.
Mazak continues to innovate in the FSW world, developing wear-resistant solid diamond FSW pin tools suited for high production applications and challenging alloys. Mazak MegaStir diamond FSW pin tools utilize polycrystalline diamond to provide effective thermal conductivity for improved weld surface finishes and allow for higher spindle speeds to lower operating costs and boost productivity.
The diamond pin tools are designed specifically for joining demanding aluminum alloys such as AA 5083, a corrosion-resistant alloy used extensively in shipbuilding, and can provide superior welds for up to 30 kilometers. Even in neutron-absorbing Metamic, a metal matrix of Al 6061 reinforced with nuclear grade boron carbide, Mazak MegaStir diamond FSW tools provide a few kilometers of tool life where only meters were previously obtained. Mazak's patented diamond FSW tools come thermocouple ready to monitor temperature and are available in standard or customized versions for unique, customer-driven applications.
Turning up the Heat
For applications involving the forging of high melting point metals such as steel and stainless steel, titanium, nickel and nickel alloys, FSW tools must have exceptionally high thermal conductivity and a high degree of toughness. Mazak MegaStir high-temperature FSW tools incorporate polycrystalline cubic boron nitride (PCBN) for thermal stability and hardness. The PCBN with binder tool material mix has shown to be an outstanding material for high melting point metal FSW applications.
Friction Bit and FSSW for Spot-On Application
Joining dissimilar metals in modern automotive manufacturing is now common practice. In lieu of spot welding and other traditional piercing processes such as riveting, Mazak has developed MegaStir Friction Bit Joining (FBJ). A proprietary spot-welding technique, FBJ uses a consumable bit that is plunged into the two materials to be joined and rotated to generate heat that will fuse all three together in seconds. The bit design and patented process promote even flow from the top material to the bottom material in a smooth, simultaneous piercing and stirring action for solid-state joining.
Friction Stir Spot Welding (FSSW) can also be accomplished by focusing FSW characteristics on a single spot on the workpiece. Diamond FSSW tools are available for low-temperature applications, and for high-temperature joining such as that encountered with steel, MegaStir tools come with a smaller steel toolholder and separate PCBN and composite metal matrix tips.
Retrofitting: Back to the Future
For shops with existing Mazak machining centers seeking to expand their capabilities, FSW multitasking versatility can be achieved by retrofitting with a Mazak MegaStir FSW Aftermarket Kit that allow for joining capability on an existing subtractive machine. The kit includes an FSW Intelligent Toolholder that is compatible with a wide range of standard or custom pins and IIoT wireless gateway that provides seamless communication between the toolholder and MAZATROL Smooth CNC.
As compact weight-saving designs for economy and efficiency continue to proliferate throughout the industry taking aluminum applications ever further, evolving FSW tools and technology will allow manufacturers to expand the capabilities while achieving increasing levels of cost efficiency and productivity.
For more information contact:
Mazak Corporation
P.O. Box 970
Florence, KY 41022-0970
859-342-1700
www.mazakusa.com