

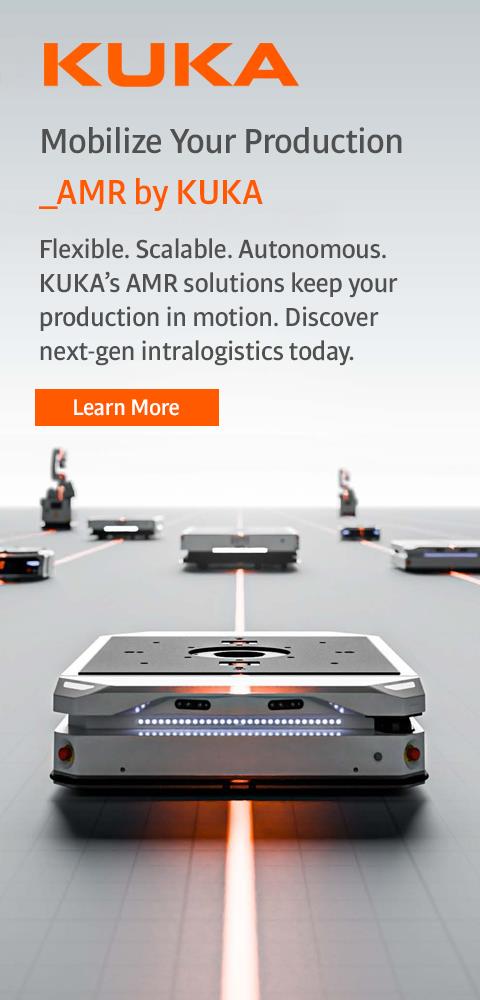
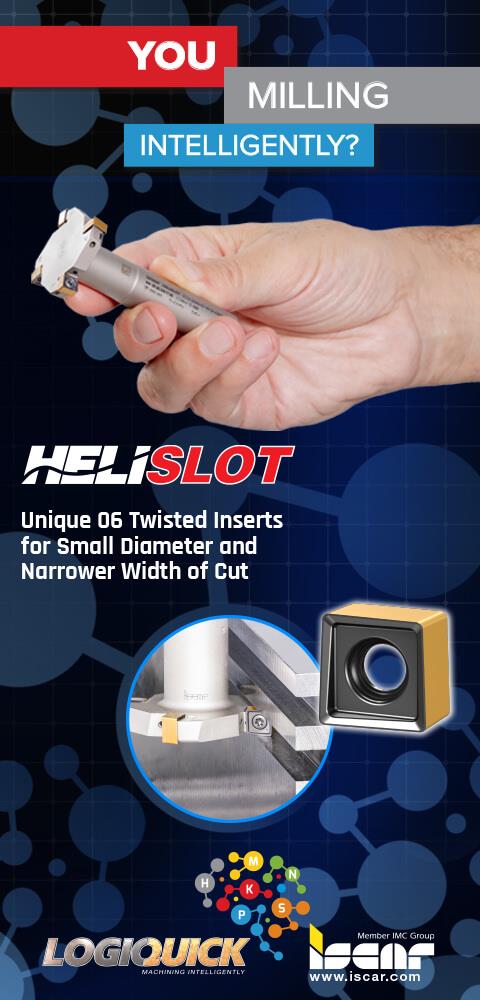
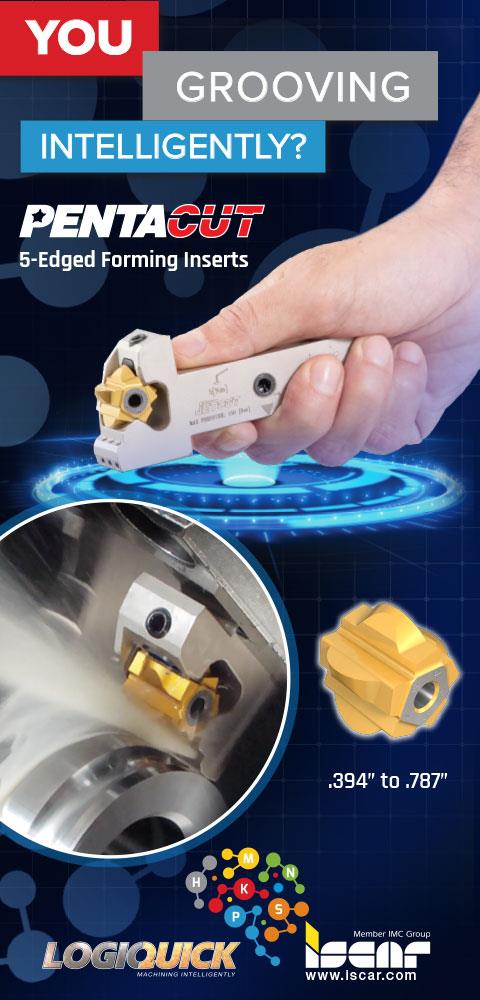
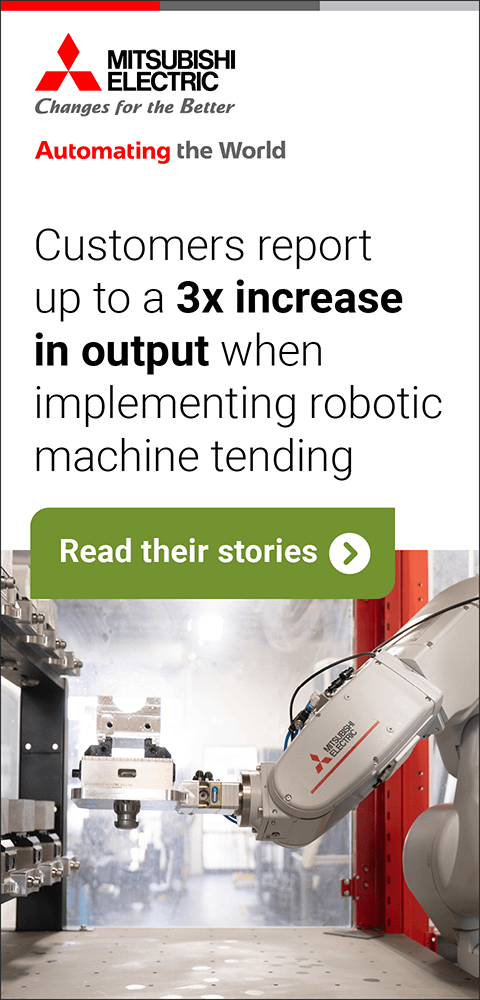
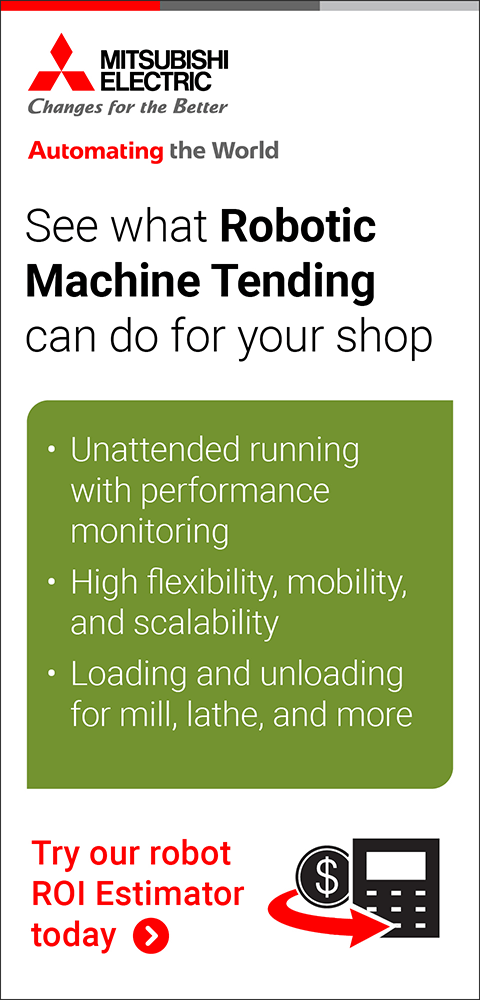
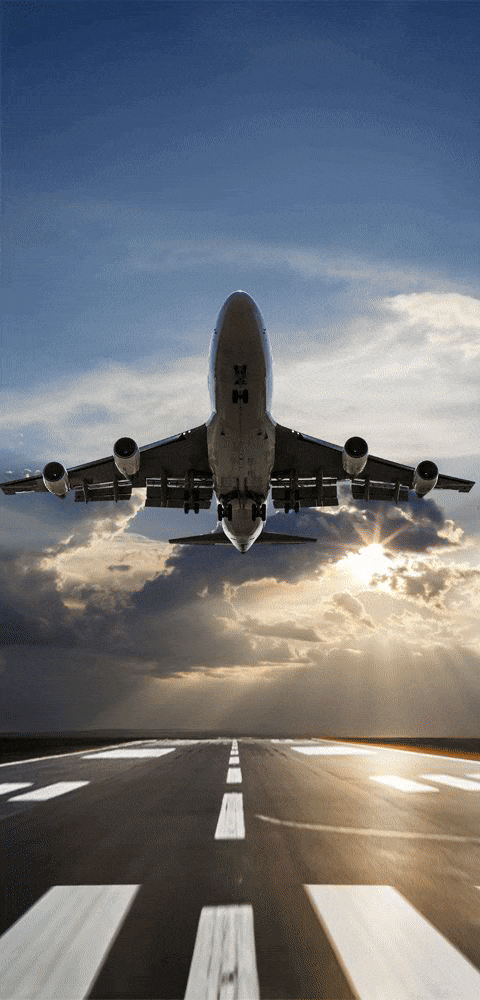
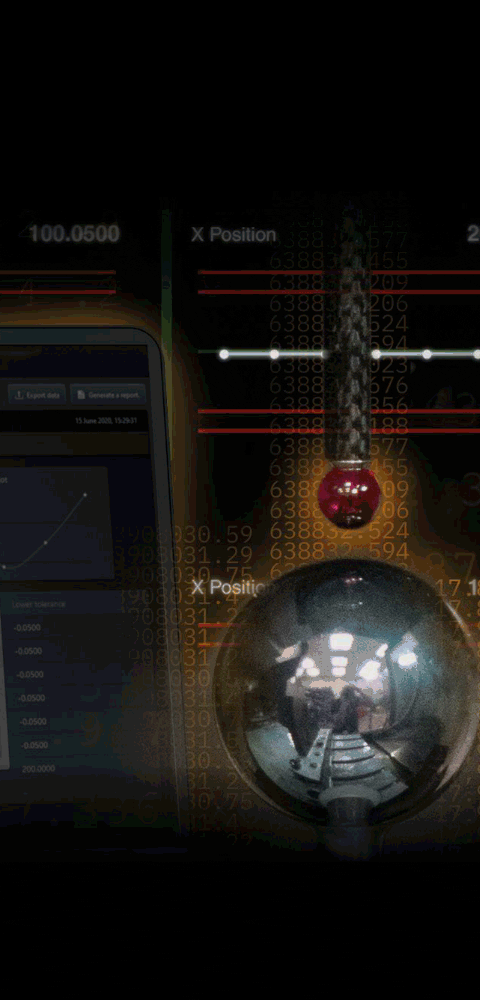
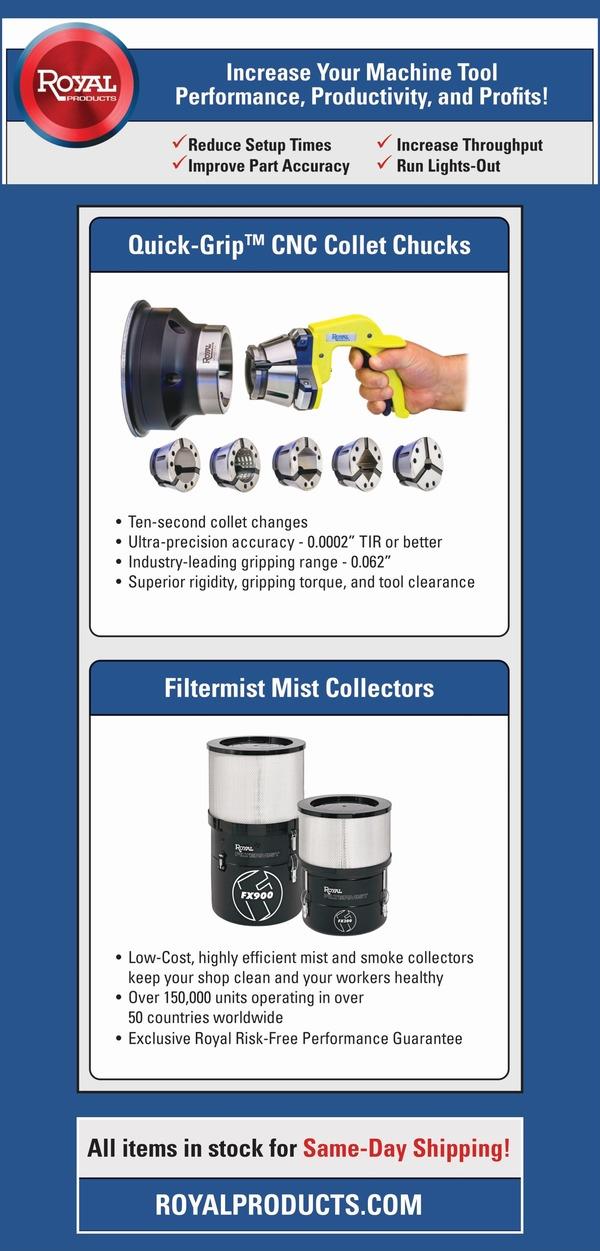
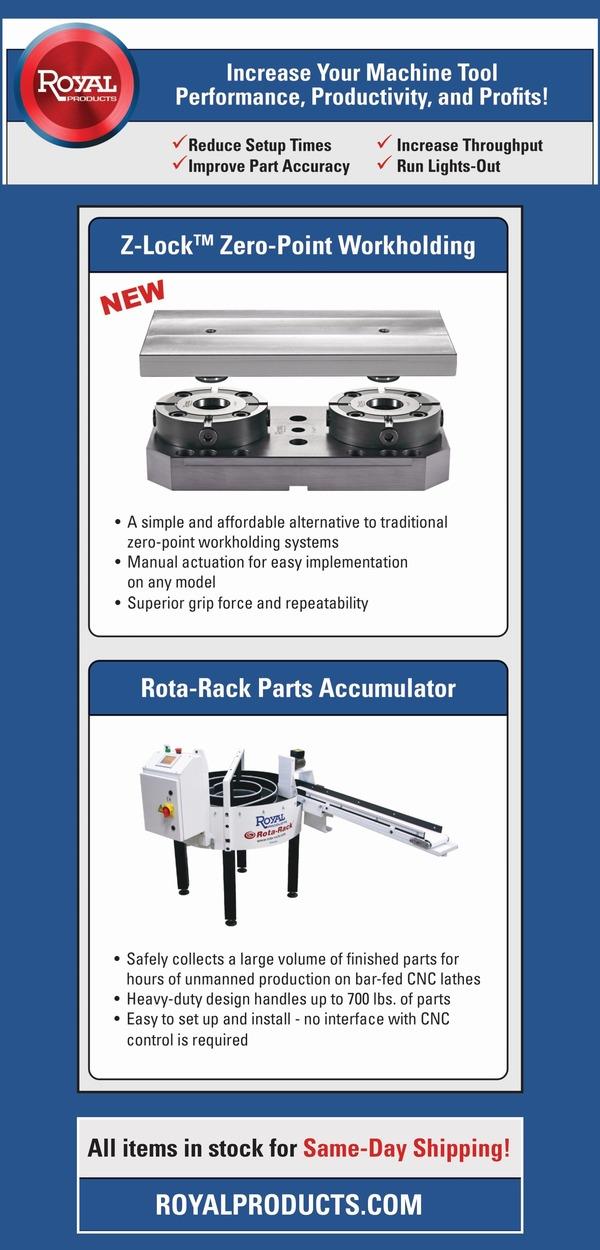
Pro Shrink Tubechiller with Pyrometer Technology Coil
May 1, 2023
The Speroni Pro Shrink Tubechiller is a combination shrink and cooling system. After the shrink process, the enclosed tube of the chiller automatically lifts from the unit's base, encompassing the tool. As the tube rises, it fills with coolant to cool down the hot tool. While the tube is moving up, the coil moves back to the start position. For large toolholders or special materials, such as stainless steel, interchangeable coils are available.
The Speroni Pro Shrink Tubechiller comes standard with Pyrometer Technology Coil. The pyrometer technology in the shrinking unit ensures that only the necessary temperature is applied during the shrinking process. The temperature of the shrink chuck is continuously measured during the inductive heating process. As soon as the shrink chuck has reached the predefined temperature, the heating process stops automatically. Overheating of the toolholder is impossible.
The Speroni Pro Shrink Tubechiller 1100 provides shrink range of ".188" to 1.260" ("3 mm to 32 mm) for carbide shanks and ".236" to 1.260" ("6 mm to 32 mm) for HSS shanks.
Shrink holders can be shrunk several thousand times without affecting runout, clamping force or accuracy. The temperature of the shrink fit chuck is continuously measured during the inductive heating process. Once the shrink chuck has reached the predefined temperature, the process stops, eliminating the potential to overheat the chuck.
Additional features include:
- Navigation menu
- Graphic visualization of the shrinking and cooling process
- Simple parameter input with USB
- Operator-defined parameter lists
- Avoid operating errors through individual menu configuration
- Industry 4.0 ready through ethernet interface and data exchange.
For more information contact:
BIG DAISHOWA Inc.
2600 Huntington Blvd.
Hoffman Estates, IL 60192
888-TOOL-PRO / 224-770-2999
bigdaishowa@us.bigdaishowa.com
www.bigdaishowa.com
< back