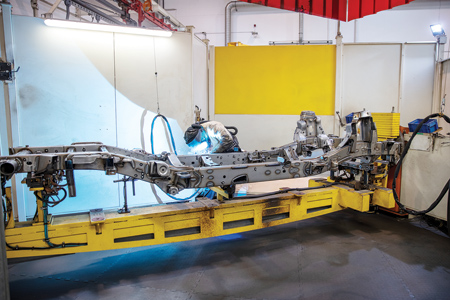
4.2 meter long chassis frame of the Mercedes G
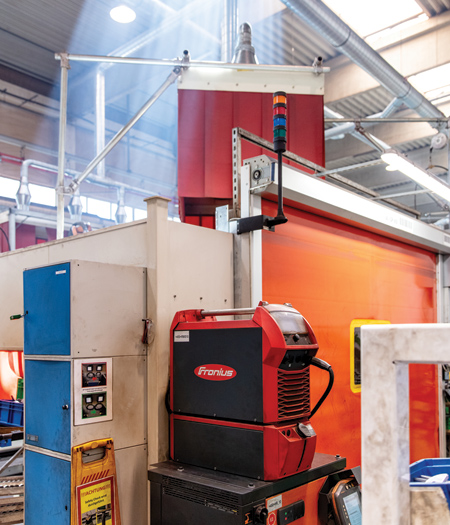
Autonomous production in the welding cell
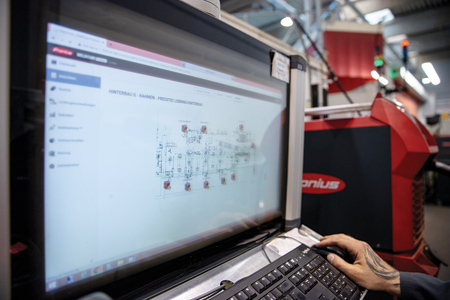
Welding data management with WeldCube Premium
"If we take a look at production processes in the premium automotive segment, we often find that OEMs and Tier 1 companies work hand-in-hand with their sub-suppliers during the design and development of the line," said a Fronius spokesperson. "Magna Presstec relies on high-tech welding technology from Fronius for quality assurance and optimization of its production processes." Magna Presstec produces high-quality chassis and structural components made from aluminum and steel for customers that include VW, Audi, BMW, Daimler and Porsche.
The Mercedes G is one of the most capable of all-terrain vehicles, yet is practical enough for everyday use. Its extended ground clearance and built-in deep wading capabilities are designed to handle extreme off-road conditions. Pulling force and a long service life have to be guaranteed when the G is subjected to violent impacts at high speeds on rough terrain, so the quality of the welds has to be of the highest standards.
The steel we use is primarily in sheets 2-4 mm thick, which are joined together using 657 welds," said Kurt Hartmann, Manager of the Quality Assurance and Welding Supervision division for frame production of the Mercedes G range. "The total weld length per frame is 76 m. The biggest welding challenge for us is to build up the 4.2 m long chassis frame layer by layer, while always remaining within the customer's specified tolerances and maintaining the required top level of quality.
This placed varying requirements on the joining technology when tooling up the production line. To generate the required stability in the solid frame, high arc stability with perfect penetration was essential. The stringent quality requirements also called for as little distortion as possible and controllable heat input. For productivity reasons, high weld speeds were also needed.
"The Pulse Multi Control (PMC) process from Fronius was able to totally satisfy our requirements," said Hartmann. "This meant we had to have the modular TPS 500i welding platform. Intuitive operation and the straightforward interface to the robot gave us precisely the package we needed. We currently have 36 of these welding systems on the Mercedes G line. We also have some TPS 320i systems for any manual welding we need to do for quality control purposes."
The production line extends over more than 100 m and is autonomous to a large extent. The coordinated robot systems work seamlessly together, enabling a fully assembled G frame made up of many individual parts to leave the hall every 10 minutes.
The production process takes places in three sections: the front and rear of the frame are produced at the same time. A team of workers starts by tooling up the welding units. Then, in the cells, the components are joined using welding robots. A handling robot picks up the completed components, transports them to the next cell and places them in position. At the end of each section is a cell to which the workers have no access. This is sometimes used for welding long welds, but also for cooling or as a complex station for squeezing, for example, which involves nesting the lower shells with the upper shells of the side members, moving them into position and welding them under pressure.
In the substructure the final production section the front end and rear end are brought together and the frame takes on its striking form. The final work steps consist of punching decoupled connecting points for the chassis. In addition, a drawn arc welding operation fires 192 studs into the frame. The quality of the welds is then checked, any welding spatter removed and the welds reworked as necessary. Finally, robot-controlled laser systems take precise measurements of the frame and check that it meets all the required quality criteria.
This complicated procedure demonstrates that it is not just about welding at Magna Presstec. To be able to ensure the high degree of automation and high quality for the G line, the focus right from the outset was on the integration of monitoring and data analysis tools for welding processes. The automotive sub-supplier was looking to cooperate with joining specialists whose systems and solutions facilitated the total digital traceability of the welding processes.
With its WeldCube Premium software package, Fronius was for the first time able to install a comprehensive welding data management system in the production facilities of a Tier 1 supplier, and to demonstrate the benefits of the various software systems being used.
Hartmann said, "WeldCube Premium is an important pillar of our quality management system, as the complete traceability of every single weld is incredibly important to us." Trained operators at the quality control stations are presented with the most accurate information on their terminals. Locations picked out by Fronius WeldCube are subjected to a detailed visual inspection and reworked if necessary. Only then is the G frame released for the next stage in the process. The gathered data are then fed back to help optimize the automated welding processes.
WeldCube Premium charts every millimeter of the weld, making it a simple matter to analyze the cost of consumables such as gas and welding wire. Yet it has much more potential, for example predictive maintenance the ability to order wearing parts and other materials in good time and in sufficient quantities.
"Predictive Maintenance with WeldCube Premium was able to uncover areas of potential savings, for example by having the welding management system specify precise maintenance intervals," said Hartmann. "We are always kept fully informed about the condition of contact tips, torch bodies, welding torches and wirefeeders, which means we know exactly when to service the equipment to avoid faulty welds, rework or the scrapping of components."
Magna Presstec was already a user of the Fronius Central User Management (CENTRUM) system, which it uses in quality management. CENTRUM is where user and welding permissions are centrally managed. Welders use a smart card to identify themselves to the welding system, ensuring that only specially trained operators are allowed to work with the relevant parameters another way of eliminating potential sources of error.
Christoph Pangerl, Fronius Key Account Manager for Magna, said: "The insights gained from the cooperation with Magna Presstec were extremely valuable, as we were able to feed them directly into our product development. It has also allowed us to make our software solutions accessible to a much broader customer base."
For more information contact:
Fronius USA LLC
6797 Fronius Drive
Portage, IN 46368
219-734-5500
sales.usa@fronius.com
www.fronius.us