
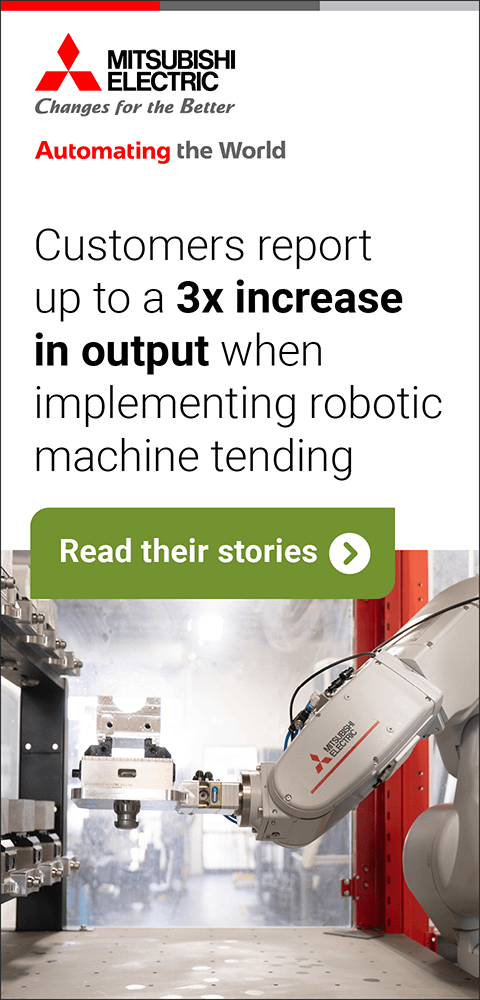
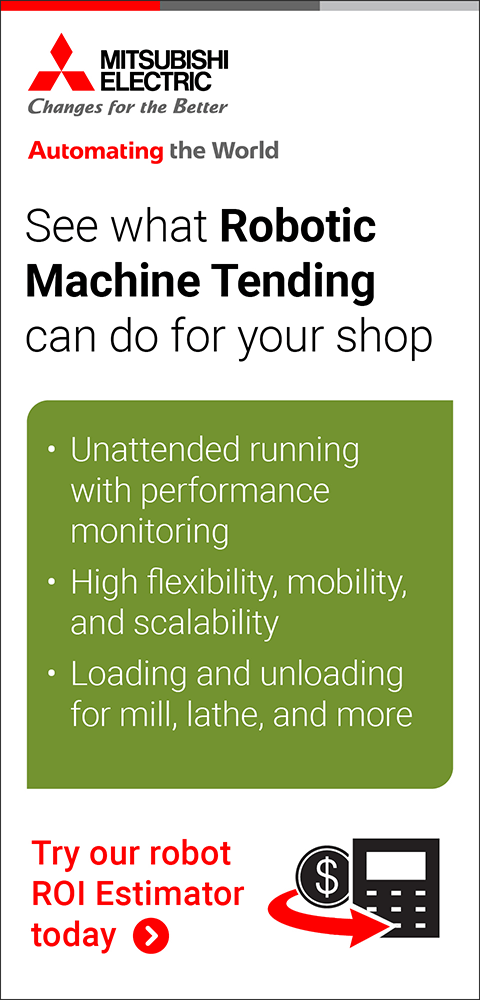
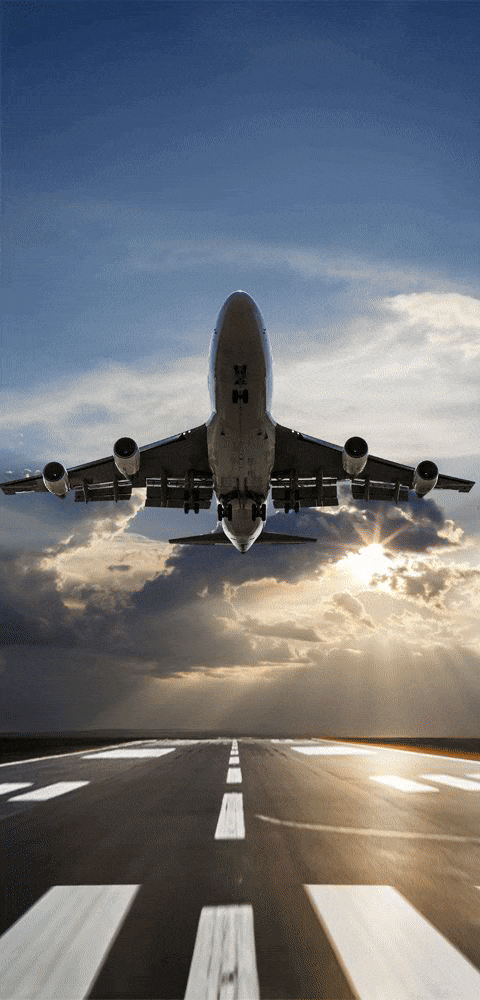
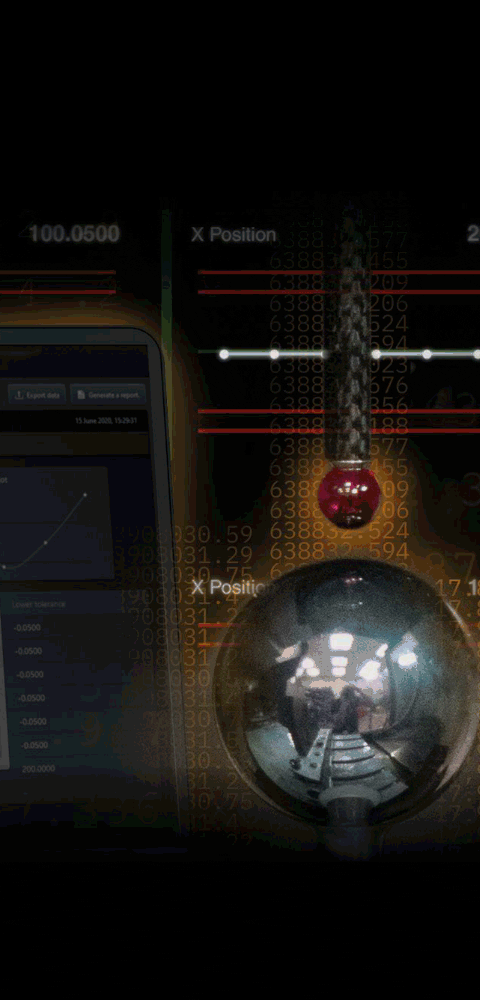
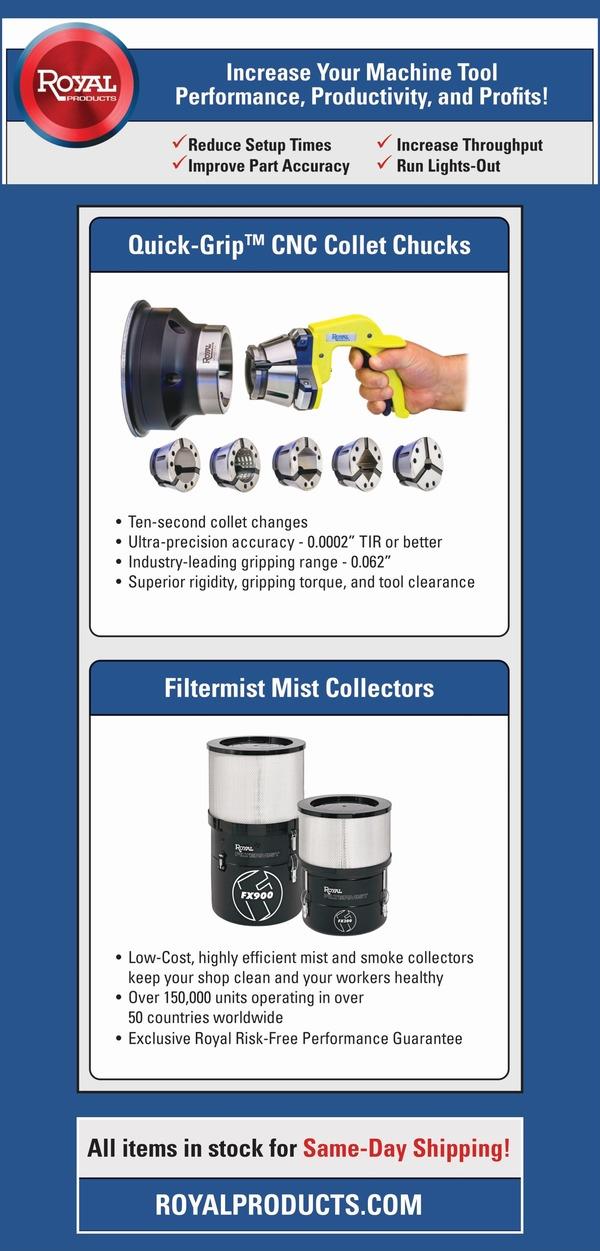
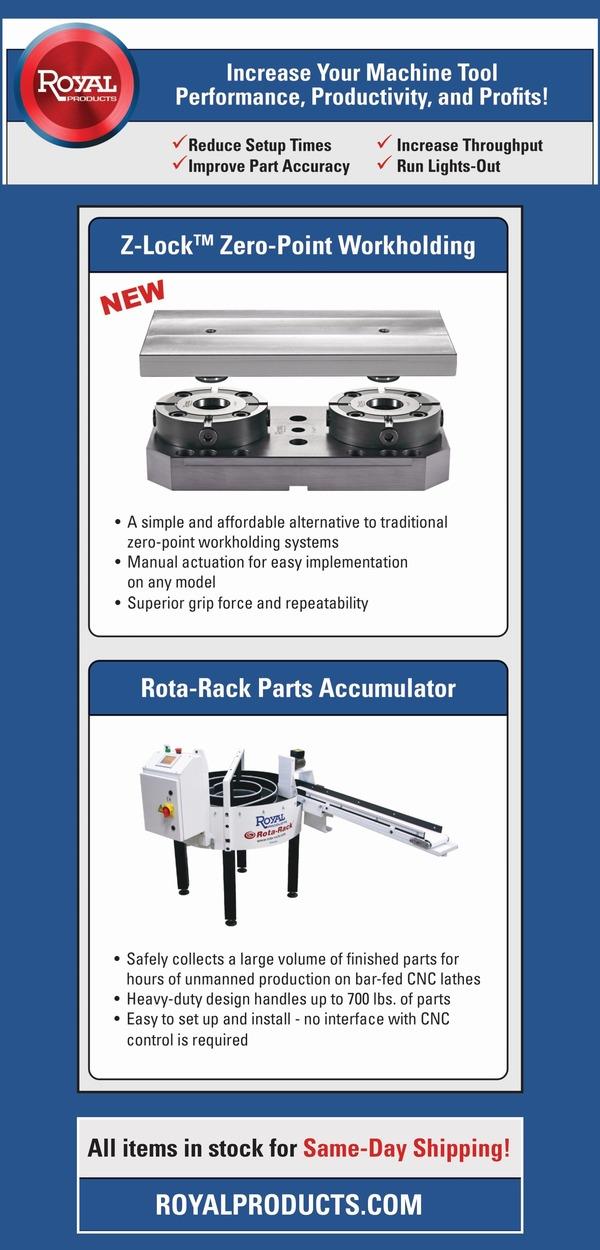

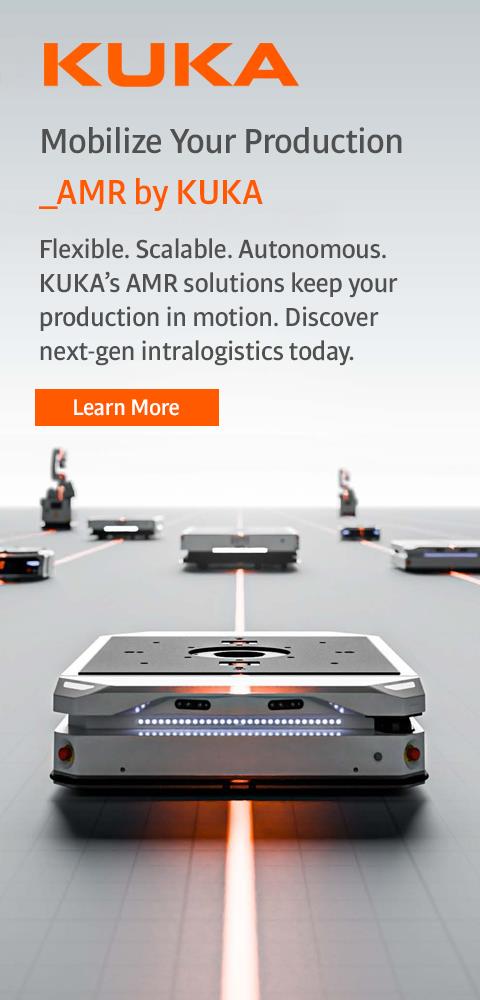
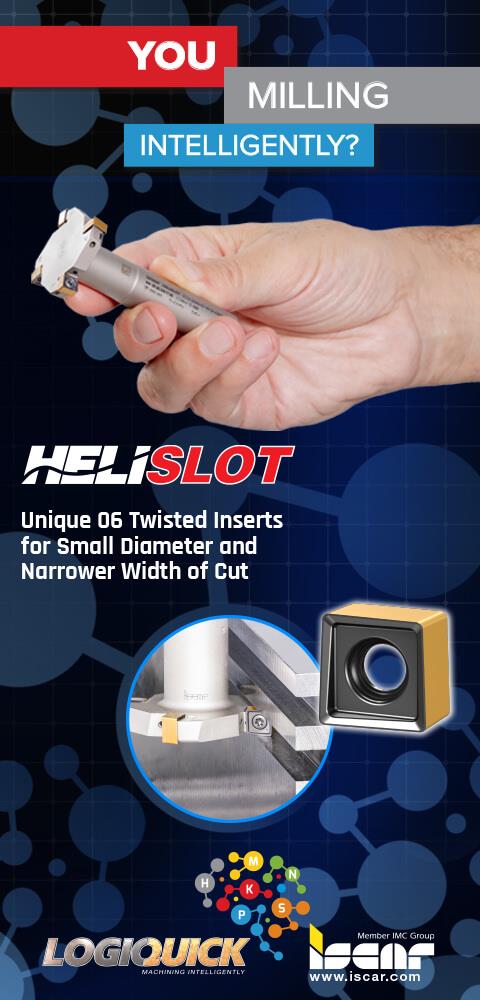
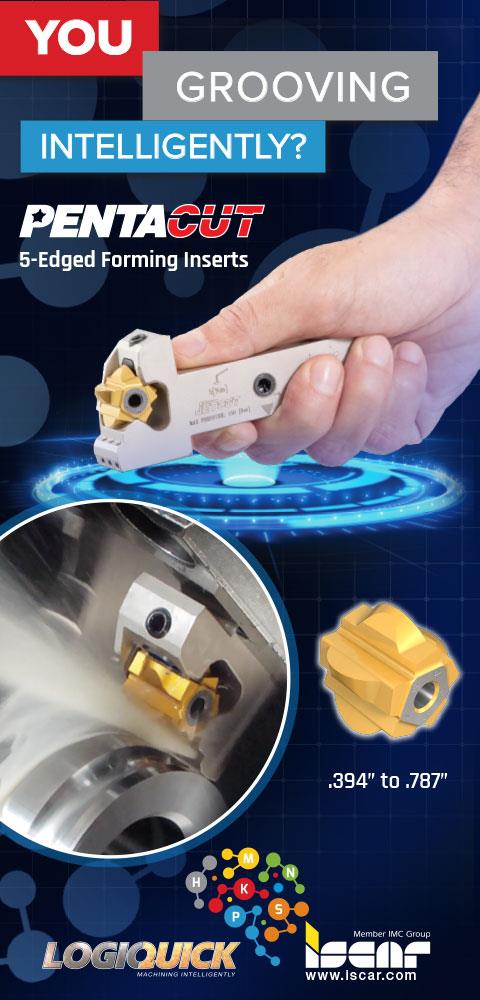
Innovative Process for Hard-Coated Brake Disc Production
May 1, 2023
"Alongside tire wear and the combustion of fossil fuels, brake abrasion contributes to the high particulate pollution caused by vehicles with combustion engines and electric or hybrid drives," said an Erwin Junker Machinery spokesperson. "The automotive industry needs innovative technical solutions to reduce this contamination."
A series process, in which laser cladding provides brake discs with high-quality corrosion protection and a wear-resistant hard coating, is now available to reduce brake-related particulate emissions. This innovative hard coating process is designed to provide high-quality anti-corrosion and wear resistance.
JUNKER offers the JUDISC brake disc coating and grinding innovation, allowing optimum friction pairing and reduced particulate emissions. During the grinding process, the brake disc is simultaneously ground on its parallel sides with two opposing grinding wheels. This state-of-the-art manufacturing process achieves flatness and precise axial runout, and the coating thickness deviation is reduced.
Highlights include:
- Short cycle time
- Optimal turn-key solution for coating and grinding
- Highly productive grinding process
- Tooling costs per brake disk at benchmark level
- Exact parallelism and axial runout
- Minimum thickness deviation (DTV)
- Low media consumption costs
- Reduced heat due to innovative grinding process leads to minimal distortion
- Closed loop between coating system and grinding machine.
Technical data for the JUDISC machine:
- X-axis travel: 200 mm
- Z-axis travel: 650 mm
- Grinding wheel diameter: 500 mm
- Grinding wheel width: 90 mm
Technical data brake disc:
- Friction lining outer diameter: min. 220 mm, max. 500 mm
- Total width: max. 150 mm
- Weight: max. 30 kg.
For more information contact:
Erwin Junker Machinery, Inc.
2541 Technology Drive, #410
Elgin, IL 60124
847-488-0406
info@junker-usa.com
www.junker-group.com
< back