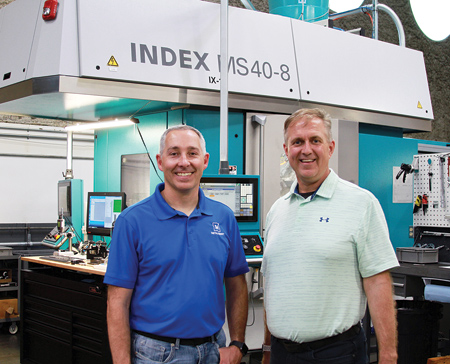
Chad Oswald, Director of Engineering, and Scott Harms, founder and President, pursue implementation of new technologies to maintain MetalQuest's competitive advantage.
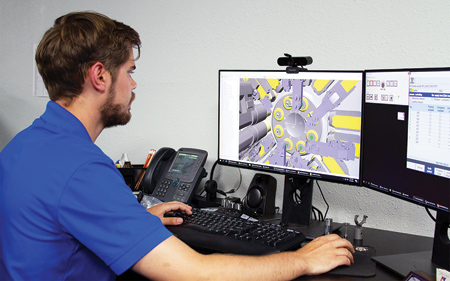
Ryan Broeder, Manufacturing Engineer, uses Virtual Machine to create, simulate and optimize part programs for MetalQuest's INDEX MS40-8 CNC multispindle.
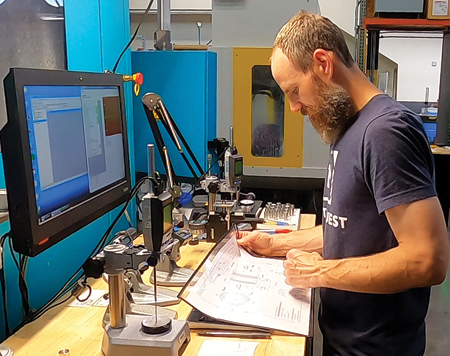
Michael Massong, CNC Operator, inspects parts at the station MetalQuest created to accommodate faster inspections due to the MS40-8's shorter cycle times.
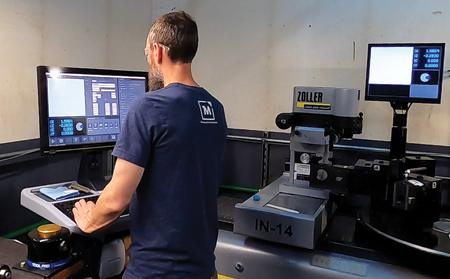
The MetalQuest team is dedicated to doing everything possible to maximize machine uptime, so tools are preset off of the MS40-8 to streamline changeovers.

This component produced for the firearms industry provides an example of the type of part MetalQuest has identified as optimal for running on its MS40-8 CNC multispindle.
Recognized regionally and nationally for its commitment to innovative manufacturing practices, MetalQuest Unlimited prides itself on never backing down from an opportunity to improve. Founded in 1996, the company has experienced 26 years of steady growth that recently culminated in opening a second manufacturing facility in Hayden, ID, half a country away from its flagship location in Hebron, NE. Built around the capabilities of its INDEX CNC multispindle lathe, the new location is strategically located to capitalize on serving West Coast companies that need mid-to-high volumes of complex parts.
Founder and company President Scott Harms started the company after growing up on the family farm, where they had a government surplus mill and government surplus lathe that were used to perform repair work. While obtaining an associate degree in machining from a local trade school, Harms began to envision a manufacturing facility that used automation and efficiency to allow workers to produce far higher volumes of parts than was the norm at the time.
"I had just turned 22 and succeeded in starting the company, basically, because I was too young to realize I could not do it," said Harms. "My first machine was a 3-axis lathe with live tooling, so a multitasking machine before the term 'multitasking' was really being used. The distributor did not want to sell it to me, and I had to convince him why it was the right machine for what I wanted to build."
Armed with a machine that empowered him to produce relatively high quantities of complex parts, Harms started building the business. Within six months, the company had grown enough to hire its first employee and invest in a second machine, a vertical machining center. A year later, two more 3-axis lathes had been added to the mix, both with subspindles. In the early days, each machine corresponded to hiring a new employee. The focus was on building a mix of technology and talent that could achieve dramatic productivity gains.
"One of the early jobs that really demonstrated our philosophy was a small hydraulic part that our customer was running through five different operations," said Harms. "It was complex, with a bunch of angled holes. Our team came up with a way to do it on one machine in one set-up. We have built a business out of figuring out smarter ways to make challenging parts."
Over the years, MetalQuest incorporated more advanced automation into its operations, with 15 robots now powering unattended production at its Hebron plant. Then, in 2019, the company undertook the most recent shift in its technological capabilities by investing in an INDEX MS40-8 CNC multispindle lathe.
"We started looking at multispindles at IMTS 2010," said Chad Oswald, MetalQuest's Director of Engineering who has been with the company since 1999. "Every IMTS, it was like going to the Porsche dealership. Multispindles are a sight to behold, and we would go to the INDEX booth just to watch the machines and talk to their team. Eventually, we started to see how much sense one would make for us."
MetalQuest's experience incorporating a CNC multispindle illustrate the guiding philosophies that have allowed the company to achieve sustained success. When Harms and Oswald describe both the general approach to business and the experience of adopting and integrating a wholly new technology, some very obvious parallels emerge.
Invest in Capabilities Needed for the Business You Want, Not the Business You Have
Since its inception, MetalQuest has approached technology acquisitions as a strategy for moving forward, not a mere exercise in meeting current demand. That philosophy served them well in selecting the model and features they wanted in their first CNC multispindle.
"When we purchased the machine, the work we were going to put on it could be run with a 6-spindle model, but we could see how some of the complex parts we wanted to win would be better served by an 8-spindle model," said Harms. "We looked at every option and asked if it was something that we could see making a difference, not on the work we were going to start with, but on the work we wanted to bring in over the next several years."
This foresight proved its value when one of the company's customers approached it with a need to scale up production of a family of firearms components. MetalQuest had previously been producing approximately 500 parts per week on a dual-spindle, dual-turret lathe. Due to increased demand, the customer was now requesting more than five times that.
Had MetalQuest purchased a 6-spindle machine, the family of complex parts would not have been able to have been completed on the multispindle. Even with the 8-spindle machine, the company ended up using every slide and tool position on the machine, as well as creating a new tool position with a double holder.
On the dual-spindle, dual-turret lathe, cycle times for the parts ranged between 7.5 and 8 minutes. On the multispindle, they dropped to between 55 and 65 seconds. Without the capabilities of the 8-spindle machine, MetalQuest would have lost the job to a competitor.
Provide Total Solutions, Partner with Companies That Do the Same
MetalQuest takes pride in providing its customers with complete solutions and looks to partner with suppliers who do the same.
"At the highest level, we have a customer who has outsourced everything in a product family to us," said Harms. "We source the raw material, manufacture the parts, build about 3,000 assemblies per week and package them. That is for over 700 top line assembly part numbers. We have always focused on providing solutions instead of parts."
The company relied on a similar level of service from INDEX when incorporating their MS40-8 multispindle. In addition to the machine, MetalQuest purchased a bar loader and a copy of INDEX's Virtual Machine, which provides a fully customized digital twin of a physical machine to streamline programming, set-ups, training and troubleshooting. They also had INDEX's applications engineering team provide a turn-key solution for the family of parts originally destined for the machine.
"INDEX delivered a complete turn-key solution, ready to make parts on day one, to our shop floor," said Oswald. "They then provided the highest level of training we have ever received from a supplier. We had a week of onsite training for our operators and programmers, followed by a week of Virtual Machine training at their headquarters. Their approach helped to guarantee our success."
Build Processes That Get the Most out of Your Technologies
Throughout its history, whenever MetalQuest has adopted a new technology, it has spent significant time planning out all of the supporting processes that will be necessary to get the most out of it. With the multispindle, that meant adapting to ensure that ancillary processes could support dramatically increased throughput.
"We knew coming in that we were immediately going to be making parts that used to take 90 seconds in 13 seconds," said Oswald. "One, that meant our operator needed to be able to inspect parts much faster. Two, we did not want that machine down a second longer than it needed to be, because the opportunity cost of downtime is so high."
The company designed a station at the machine specifically to facilitate faster inspections. To ensure maximum uptime, programmers completely set up and prove out jobs on the Virtual Machine platform, and then all tools are preset on a Zoeller presetter. When it comes time to change over the machine, a team takes a pit crew approach to setting things up, resulting in the machine being up and running as much as possible.
Empower Your People
"From day one, when I was just an ambitious 22-year-old at a 3-axis lathe, this company's focus has been on investing to maximize each person's contribution," said Harms. "The MS40-8 is just the latest example of that. It is in our DNA."
Visitors to MetalQuest can easily spot the signs of this philosophy. Automation is present throughout the facility, and there is a clear imperative to invest in advanced, user-friendly equipment that allows operators to make uncommonly large quantities of parts.
"The labor shortage and cost of labor are the biggest challenges American manufacturers are facing today," said Harms. "That puts us in a great place. We have an extensive infrastructure of automation and technology, and it has never taken a single job from our company. Instead, we have used it to get rid of the repetitive, labor-intensive tasks that most people do not want anything to do with. We have built a team of innovative thinkers and are always ready to invest in the technology they need to be more effective."
MetalQuest's approach has provided it with 26 years of success that show no sign of slowing. The company initially rented a facility for its Idaho operations while awaiting construction of a dedicated facility. In just over a year, business grew to the point where need dictated moving to a significantly larger interim facility. At IMTS 2022, the company placed an order for a second MS40-8 for use at this location. Today, the company stands poised to capitalize on the reshoring trend and reaching a larger customer base, all by continuing what it has been doing since it opened its doors in 1996: understanding and implementing advanced technologies that empower people to make complex parts with incredibly high productivity.
For more information contact:
MetalQuest Unlimited, Inc.
1410 Dove Road
Hebron, NE 68370
402-768-3800
www.metalquest.net
MetalQuest Unlimited, Inc.
675 W Capstone Court
Hayden, ID 83835
INDEX Corporation
14700 North Pointe Blvd.
Noblesville, IN 46060
317-770-6300
sales@index-usa.com
us.index-traub.com