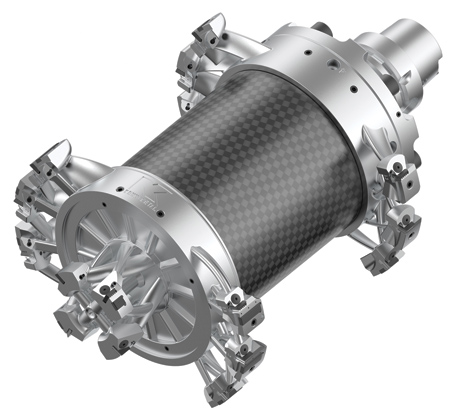
A 3D printed stator bore tool with carbon fiber body weighs 7.3 kg.
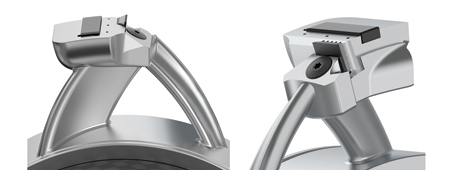
Airfoil shaped arms with through coolant and RIQ reaming technology. Complex internal and external features are enabled by AM.
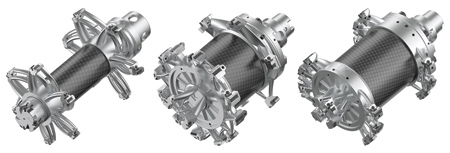
First-generation design (9.5 kg) on the left, and latest tool design variants (less than 8 kg) on the right for hassle-free tool changing.
Kennametal has introduced its next generation 3D printed stator bore tool for machining aluminum engine housings for electric vehicles.
This latest version of the tool features a newly designed arm structure, a larger center tube made of carbon fiber, and a further weight reduction of greater than 20% over the original design. The complex tool is capable of machining three large diameters in just one operation, saving set-up time and machining time for automotive component manufacturers and delivering high accuracy and surface qualities.
"As our automotive customers expand their offerings of hybrid and electric vehicles, we continue to respond to their need for lighter weight tooling solutions. By leveraging advanced manufacturing techniques like 3D printing, we have reduced weight a further 20% over the first-generation tool, while improving chip control and increasing tool rigidity-innovations that help our customers machine faster and more efficiently," said Ingo Grillenberger, Product Manager, Kennametal.
Machining three diameters in one operation, the stator bore tool helps ensure the alignment and concentricity of the machined surfaces while reducing cycle time. The lightweight 3D printed combination tool enables a faster tool change and spin-up even on less powerful machines. The surface specifications and component tolerances are achieved without constraints.
Hassle-free chip removal is accomplished by means of airfoil shaped arms with through coolant to help provide precise coolant supply to the cutting edges and guide pads. "This would be difficult or impossible to economically produce with traditional manufacturing, but 3D printing enables complex internal features," said a spokesperson. "Additionally, the Kennametal RIQ reaming system features easy diameter adjustment and a trouble-free set-up of new inserts."
For more information contact:
Kennametal Inc.
525 William Penn Place
Suite 3300
Pittsburgh, PA 15219
800-446-7738
www.kennametal.com