

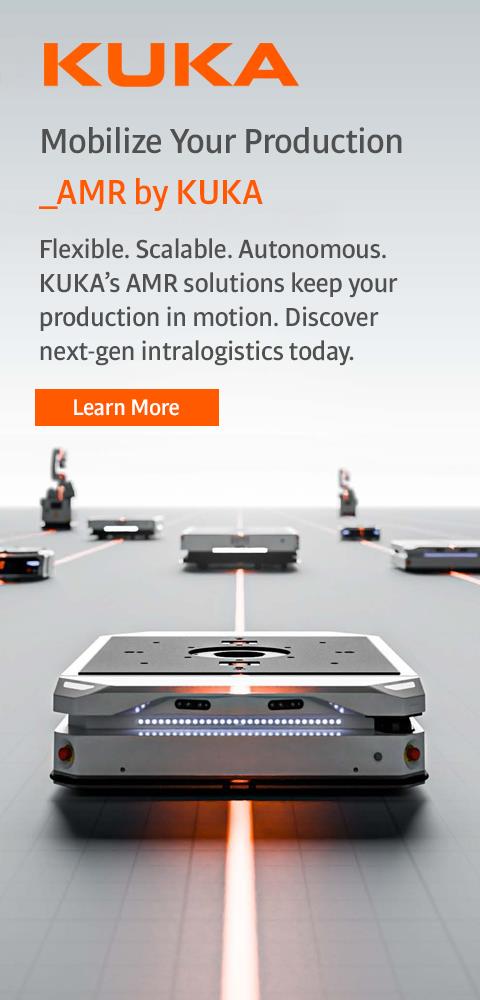
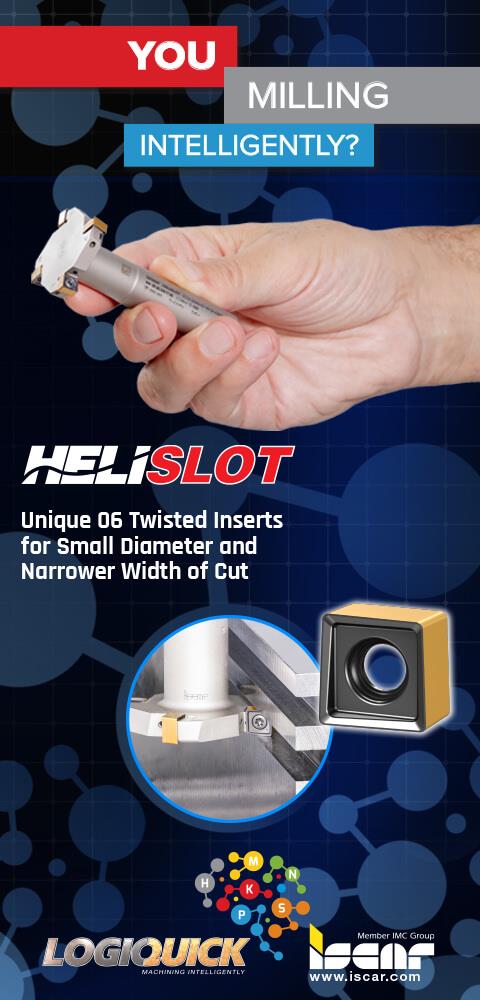
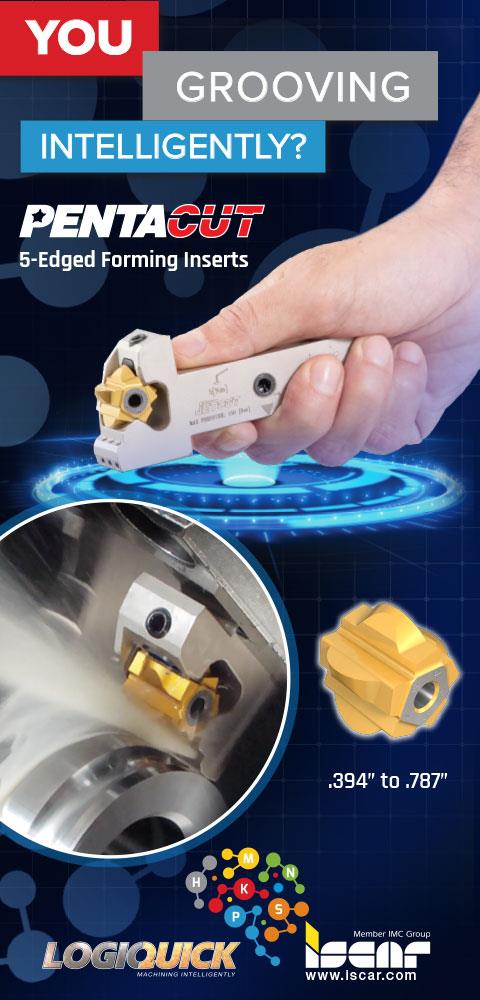
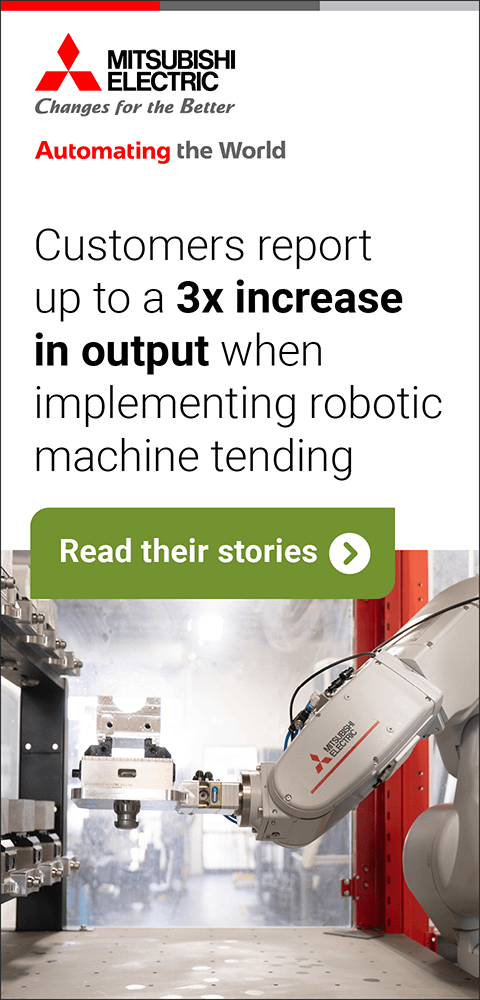
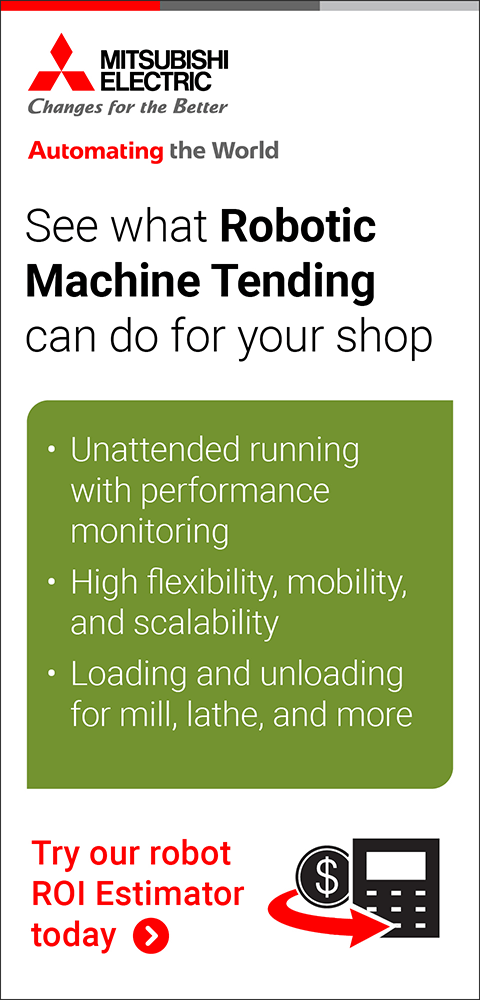
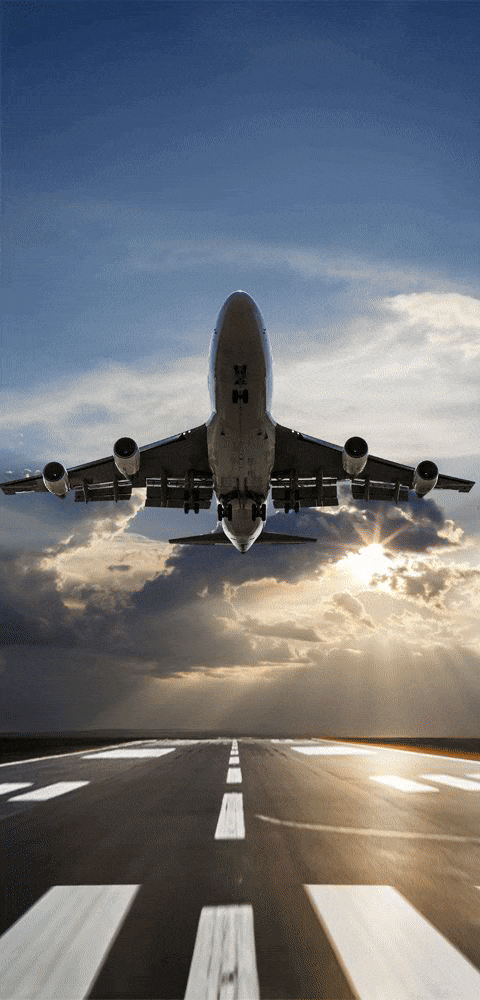
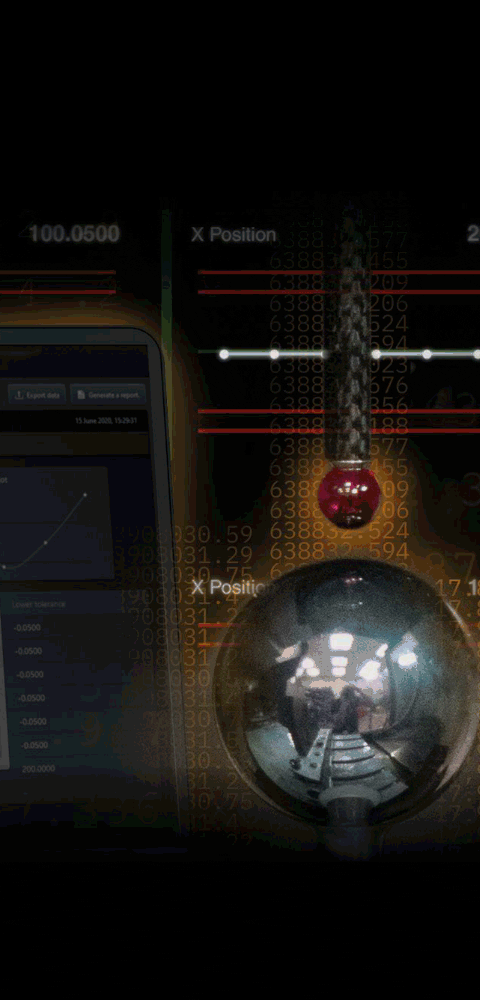
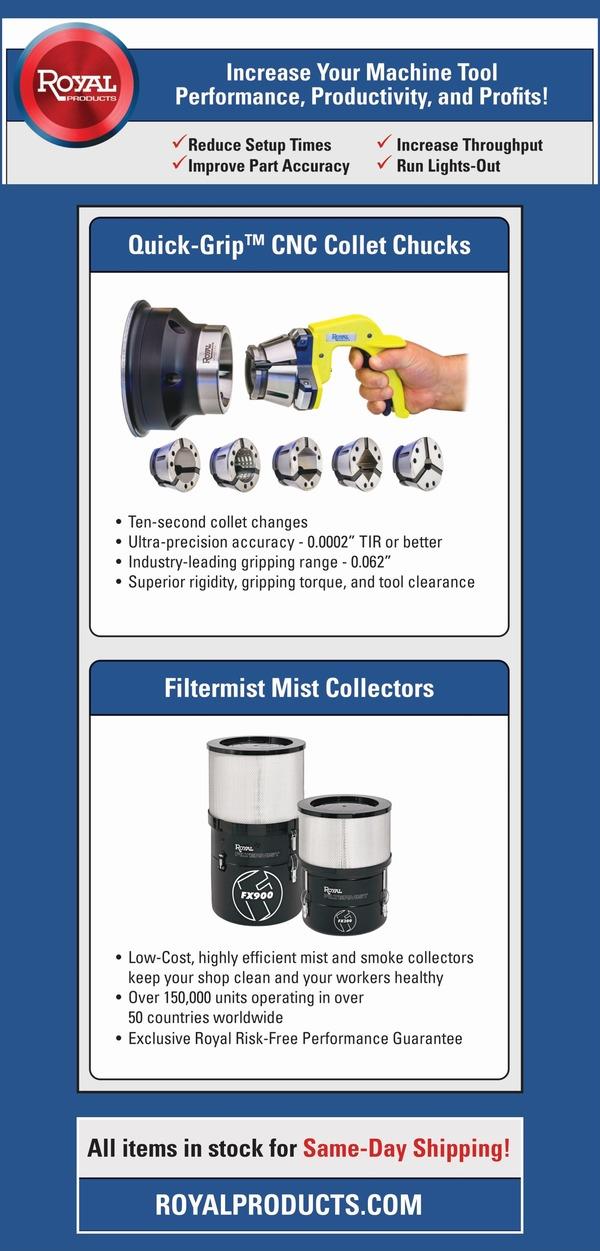
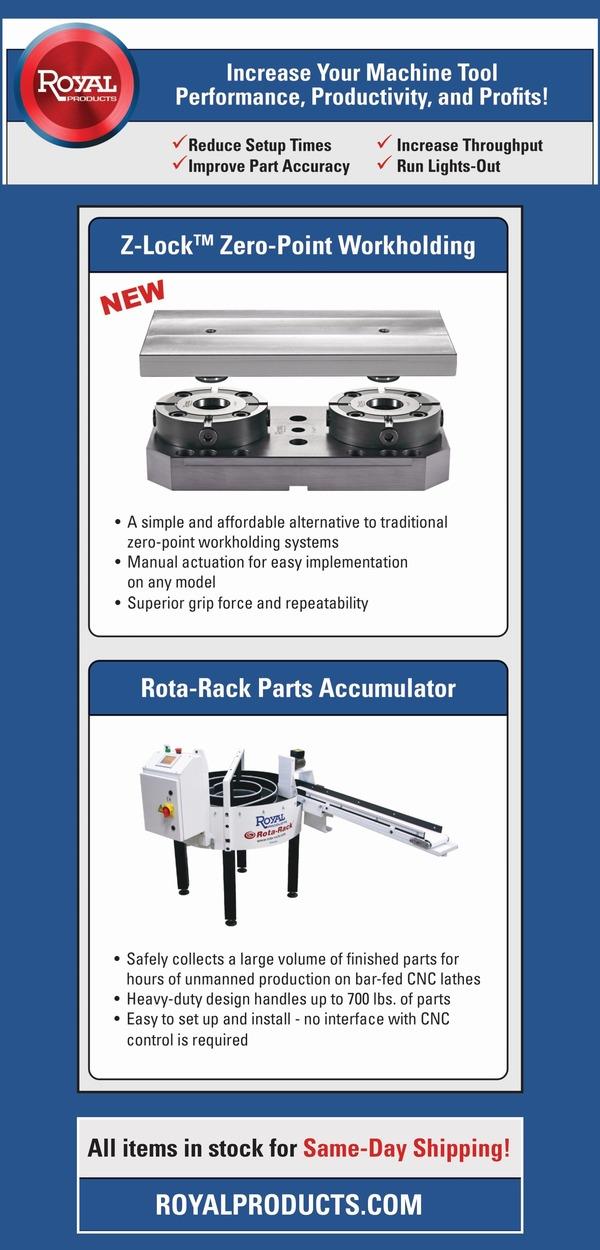
Sustainable eMotorcycles Using Industrial Origami Robotics Technology
May 1, 2022
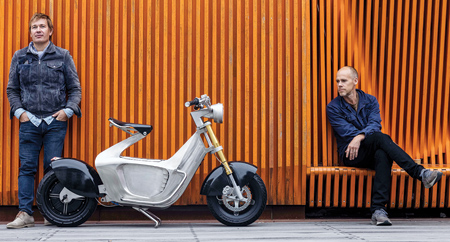
Stilride Founders Tue Beijer Jonas Nyvang
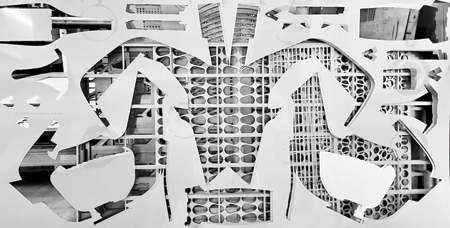
STILFOLD production
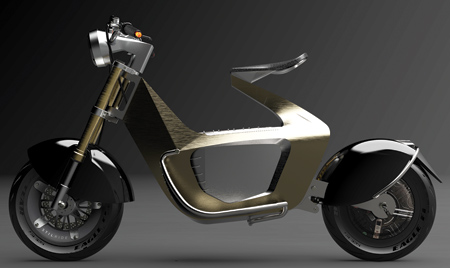
Stilride SUS1 eScooter GOLD
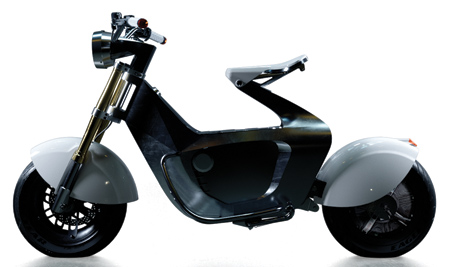
STILRIDE SUS1
Swedish technology and design start-up STILRIDE has raised over $3 million to produce sustainable electric motorcycles and scooters using a groundbreaking process dubbed "industrial origami." The manufacturing technique involves robots that are able to fold single sheets of recyclable steel into intricate, lightweight and durable new structures-significantly reducing the environmental impact of production. This process is being used to create the chassis and body for a fleet of next-generation eMotorcycles that will be made available to consumers in Europe later this year.
STILRIDE's pioneering industrial origami technology, called STILFOLD, is the brainchild of best friends Tue Beijer and Jonas Nyvang, whose backgrounds include industrial design and engineering. With STILRIDE, the duo aim to reimagine how high-performance electric-mobility products are manufactured and distributed using cutting-edge steelwork, advanced robotics and ambitious design.
The injection of funding will be used to bring the start-up's first product to the mass market: the Sport Utility Scooter One (SUS1). Unlike traditional scooters, which consist of a tubular frame and plastic body, the SUS1 is constructed by folding sheets of stainless steel over curves, much like origami. Not only does this result in a durable body and distinctive aesthetic, but it also requires fewer raw materials and reduces labor costs. Compared to a traditional scooter, the SUS1 requires 70% fewer components, drives a 25% reduction in labor costs and a 20% reduction in material costs, according to the company.
To reduce the product's carbon footprint, the company is aiming to create a production process that allows steel sheets to be flat-packed and shipped to local factories across Europe, where they will be folded and fitted with a hub motor and battery pack. Already, the climate impact of developing the SUS1's chassis is 50% lower than that of traditional scooters, the company noted.
For more information contact:
STILRIDE
partner@stilride.com
www.stilride.com
< back