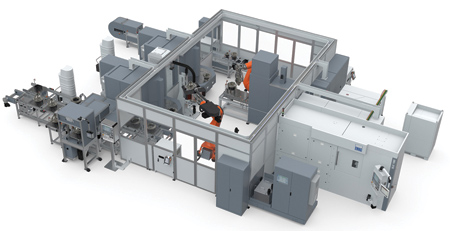
"Developing holistic production systems based on laser welding is what makes EMAG LaserTec unique in the market," said a company spokesperson.
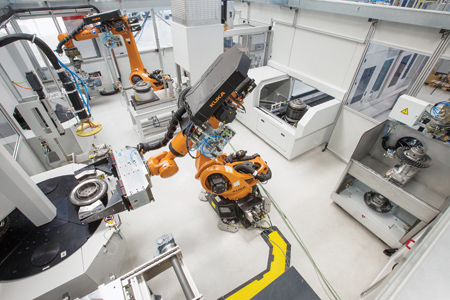
The line is engineered to provide a perfectly timed sequence for truck differentials.
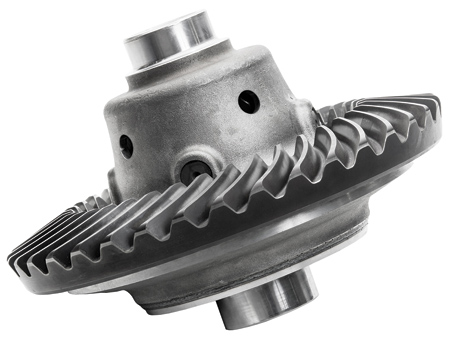
The parts weigh up to 287 lbs. and have a diameter of up to 24".
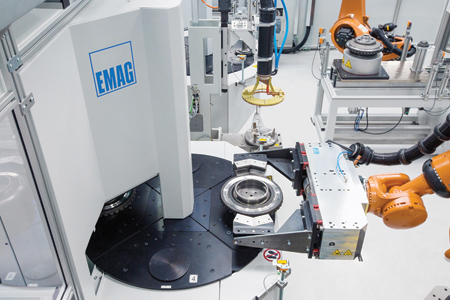
Housing parts, such as ring gears, are cleaned on the newly developed EMAG laser cleaning machine in preparation for the machining operation.
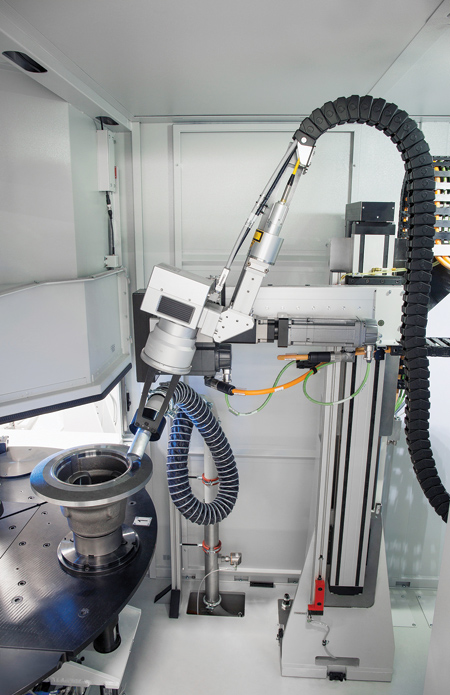
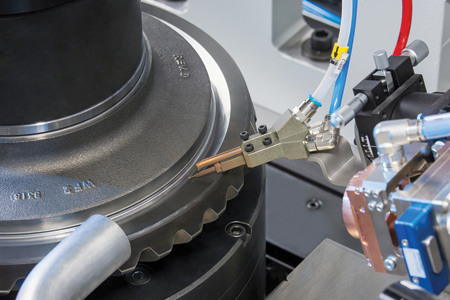
A robot loads the ELC 160 by EMAG. Two weld seams are all it takes to close the housing and join the ring gear with the housing.
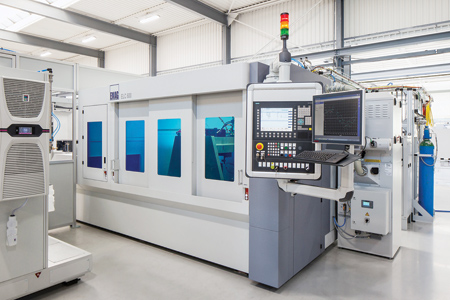
When "lightweight design" is used in regards to automobile production, it typically refers to passenger cars, rarely commercial vehicles. However, there is an enormous amount of potential for weight reduction and cost savings when considering the large, heavy parts needed for drivetrain in trucks.
Recently, a supplier in North America demonstrated the possibilities and benefits that a complete laser welding production system from EMAG LaserTec can provide. The commercial vehicle specialist currently uses an EMAG production system that welds three different parts together to manufacture a large truck differential-eliminating approximately 40 costly screwed connections. What type of processes take place in this production line?
A Shell Commercial Vehicle Study predicts that the number of commercial vehicles on the road will continue to rise, very quickly, until 2040. The study says that the number of new registrations in Germany each year will increase from the current 290,000, all the way up to 344,000, and that the rolling stock of vehicles will reach nearly 3.5 million in 2040 (currently 2.9 million). We will also continue to see the same push for energy efficiency in an effort to achieve climate goals, as well as political pressure on manufacturers to develop vehicles that are more economical. Based on this, a system that will allow manufacturers to achieve a lightweight design in the commercial vehicle sector will be a game-changer.
Many truck manufacturers have naturally been focusing on well-established light weighting systems from the passenger vehicle sector, which have allowed for substantial cost savings along with considerable decreases in weight-and that is precisely where laser welding comes into play. For years, laser welding has been essential in the development of drive train workpieces for passenger vehicles. Welded joints now replace screwed connections in many places. Even if a workpiece cannot be made lighter, it can be produced more cost-effectively by eliminating expensive screwed connections. For instance, some modern double-clutch transmissions have no less than 16 laser weld seams on the various transmission wheels, the double clutch and the differential. With that in mind, it is not surprising that a North American supplier to commercial vehicle manufacturers called EMAG LaserTec.
The experts, headquartered in Heubach, Germany, specialize in the development of complete laser welding systems. "The customer knew us, since they already use a variety of EMAG machines in other application areas. Their goal is to produce a considerably lighter and more cost-effective, large-sized truck differential. This is an ideal task for us, even though we are implementing it for the first time in the truck sector," explained Dr. Andreas Mootz, Managing Director of EMAG LaserTec. "Having a high level of expertise as a system provider was an absolutely crucial factor for the customer. We develop complete process chains revolving around laser welding, which in principle simplifies planning at the customer end and simultaneously guarantees safe and effective processes."
Cleaning, Pressing, Welding and Checking in a Single Line
A perfectly timed sequence becomes apparent for truck differentials. It consists of three individual parts before production starts: two housing parts and the ring gear. These each weigh up to 287 lbs. and have a diameter of up to 24". The detailed sequence is as follows:
- After being fed by two separate loading stations, the two housing parts and the ring gear run through an EMAG laser cleaning system-a new in-house development that looks and feels like a standard machine. The process is fast and removes all residues, such as coolants or preservatives, using a focused laser beam.
- Robots then remove the parts from the laser cleaning machines. The ring gear is first preheated with induction heating and is then transported to the joining station (preheating is performed using a low-frequency generator by EMAG eldec). The two halves of the housing are directly fed into the joining station and press-fitted together with the ring gear. The process is performed under force/path monitoring.
- The subassembly is now ready for welding-a robot loads it into the EMAG ELC 600. After axial clamping, the housing is closed, and the ring gear is joined with the housing using two welds.
- An EMAG ultrasonic testing system automatically checks the quality of the welded joint-a key step in the process that is just as important as the machining of the workpiece.
Within 12 months, the development of this process was completed. The specialists at EMAG LaserTec had to overcome a number of process-related challenges during this time-after all, the weld seams are cast steel/case-hardened steel connections with great depth, which are welded with an 8 kW (11 HP) solid-state laser and with welding additives. The whole system consists of two laser cleaning stations, a heating station, a joining station, the ELC 600 and the ultrasonic testing station, which are interlinked with complex feeding technology and two industrial robots.
A Unique Position in the Market
"This development project perfectly illustrates how we work," said Mootz about the holistic laser production system. "We always start out with the workpiece and its integral parts to develop the matching process with optimal timing and control. This results in customized solutions that provide productivity and process reliability."
EMAG LaserTec has experience in transmission and drive components, having delivered more than 160 ELC systems in total.
Authored by EMAG
For more information contact:
EMAG L.L.C.
38800 Grand River Ave.
Farmington Hills, MI 48335
248-447-7440
info@usa.emag.com
www.emag.com