
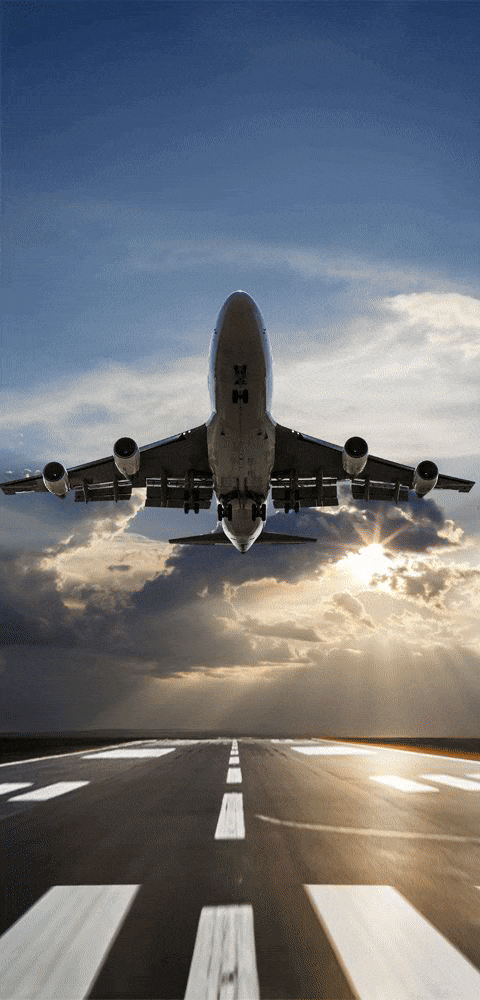
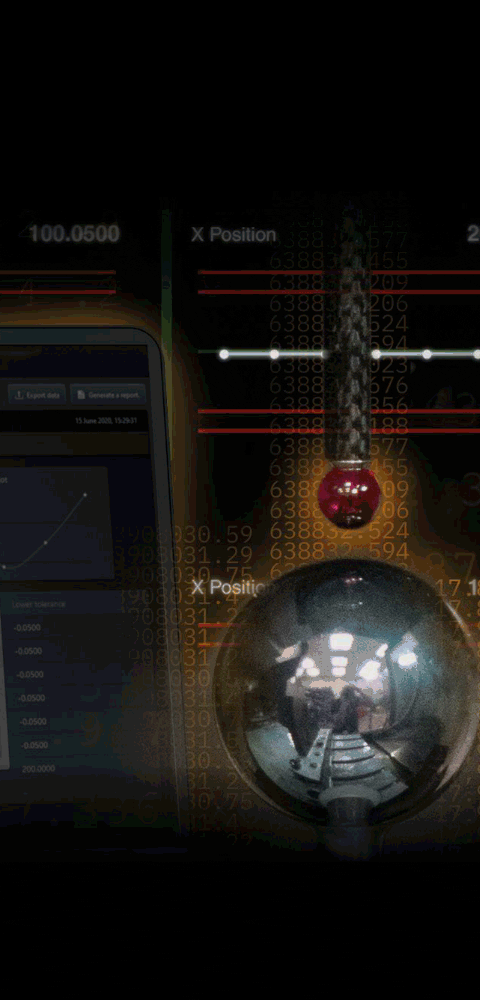
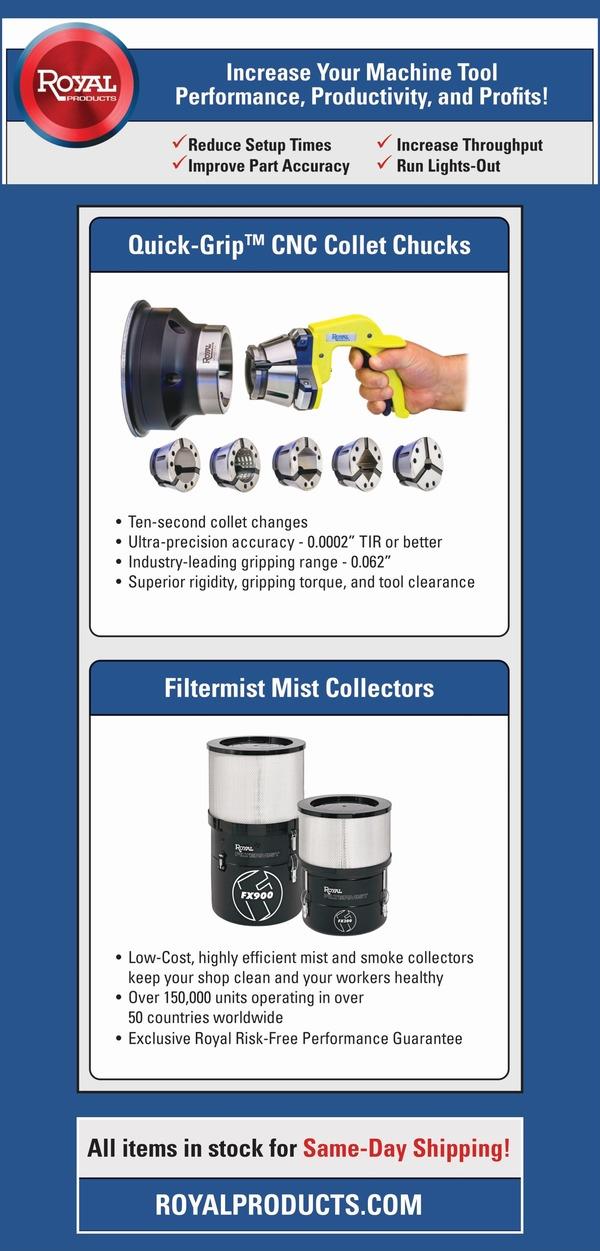
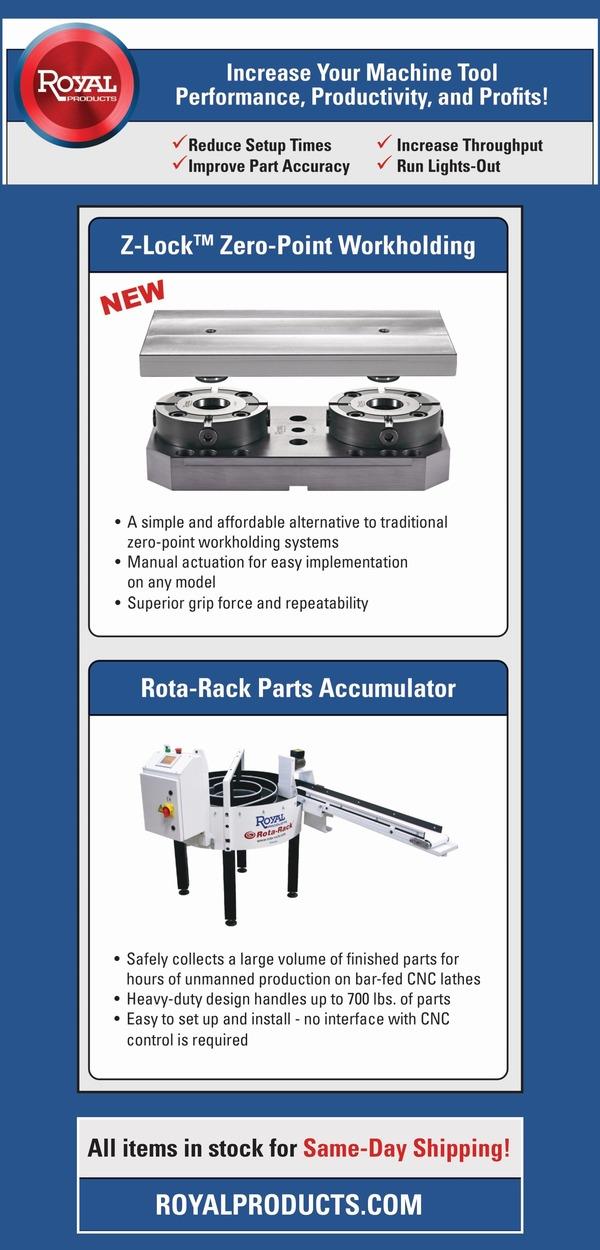

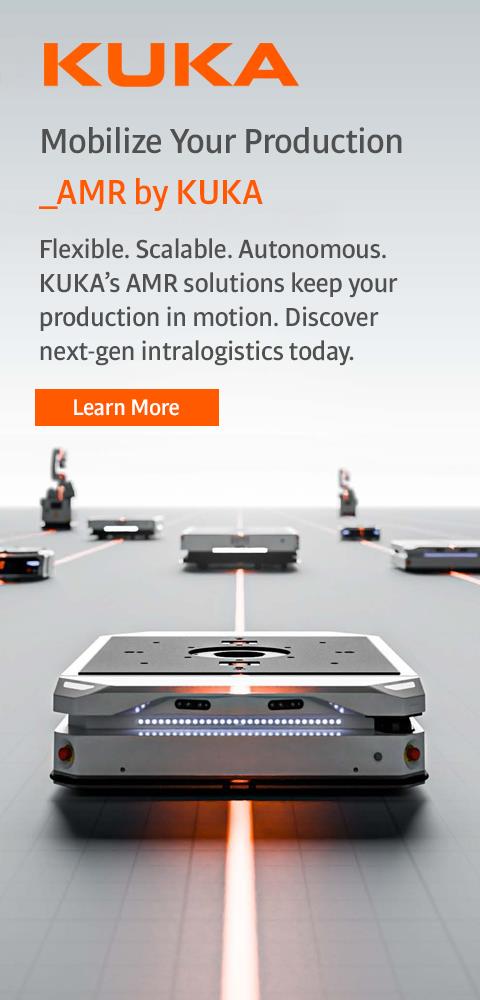
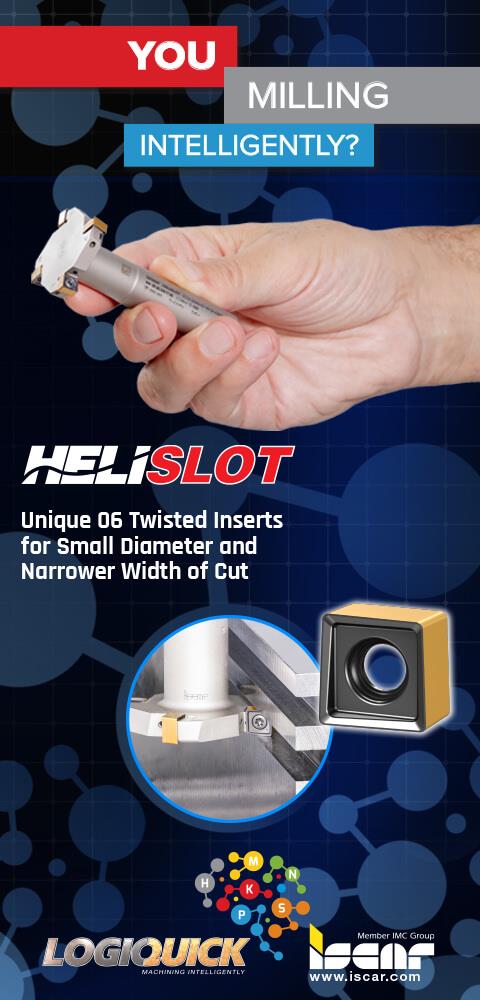
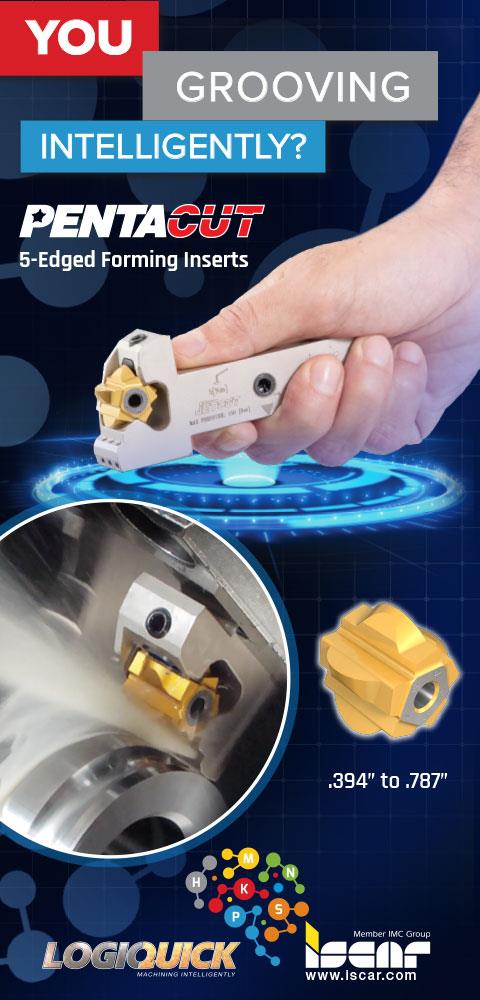
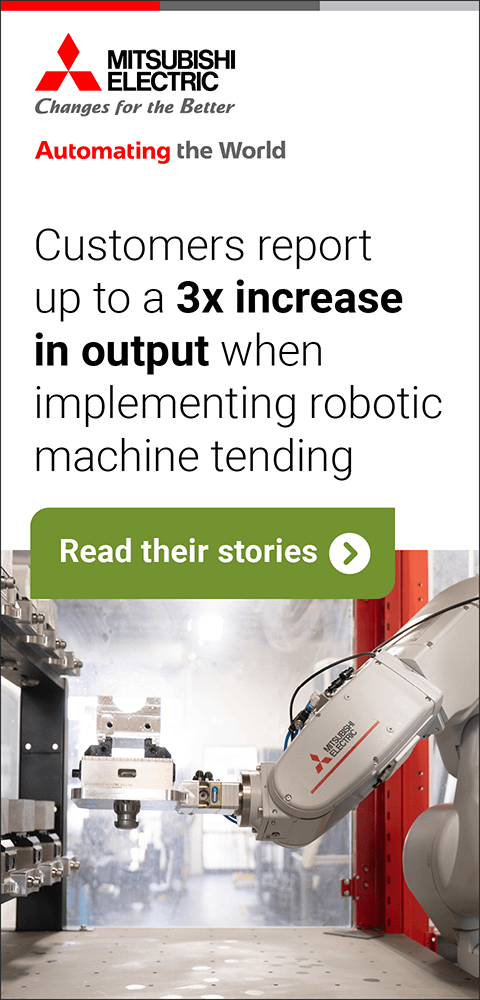
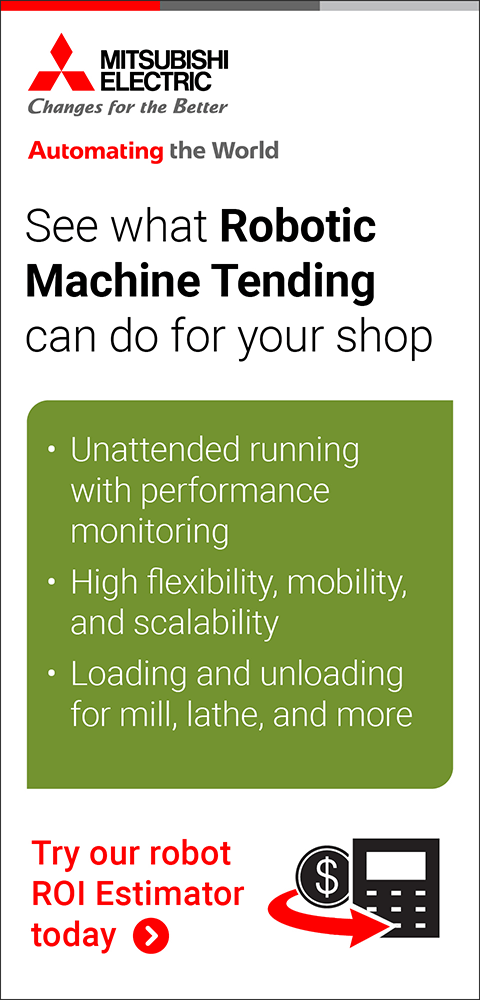
Solid Carbide End Mill for High Productivity
May 1, 2021
Kennametal has introduced an expansion to the HARVI I TE series, the HARVI I TE four-flute ball nose end mill. "Designed for highly productive 3D roughing and finishing operations, it delivers lower machining cost through maximum metal removal in a broad range of materials," said a company spokesperson.
The HARVI I TE ball nose end mill features a proprietary relief. In the most critical area-the ball nose section-a wavy contour shapes the rippled relief, which provides improved coolant flow into the cutting zone.
"The rippled relief enables higher feeds and speeds as well as increased depth of cuts by advanced vibration damping and lower cutting forces," said the spokesperson. "On the outer diameter, the relief changes its shape and turns into the eccentric faceted relief. The eccentric faceted relief provides exceptional edge strength, geometric accuracy and lower cutting forces and makes this end mill series very versatile."
Other geometry advancements of the square end styles-including a twisted end face, chip gashing and a variable helix angle-have also been engineered into this new solid carbide end mill.
The HARVI I TE ball nose end mill is available in two different lengths, both with a diameter range from 2 mm to 20 mm (1/16" to 1"). The regular length is suitable for 3D copy milling operations, while the long version offers sufficient length-of-cut (up to 4sD) for many applications, including shoulder milling when wall and floor finishing is required.
For more information contact:
Kennametal Inc.
525 William Penn Place
Suite 3300
Pittsburgh, PA 15219
800-446-7738
www.kennametal.com
< back