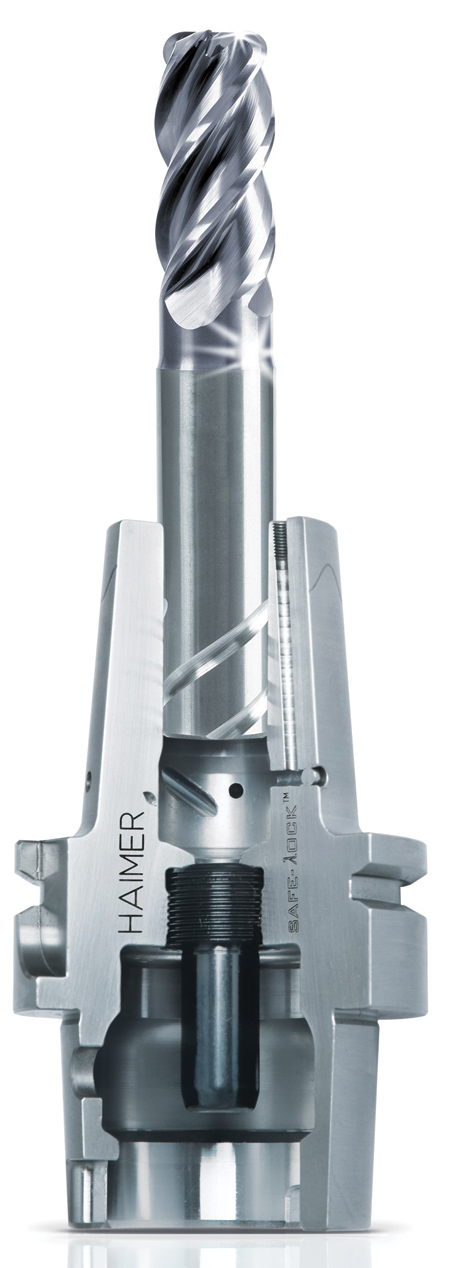
"In the manufacturing world today, it has become critical to run CNC machines at faster speeds and feeds in order to be globally competitive," said a HAIMER spokesperson. "In addition, many are machining more difficult to machine materials and are utilizing modern high-helix cutting tool technologies and programing techniques. However, because of these increases in speeds and feeds, new cutting tool designs, new programing techniques and difficult materials, most friction based toolholding systems allow the cutting tool to micro creep, which is when the cutting tool moves slightly and can pull out of the holder. Prior to the Safe-Lock creation, the only way to try to solve this problem was using a side lock (or Weldon flat) cutting tool and toolholder. Due to the side clamping of the Weldon system, the tool is pushed off center, which causes reduced tool life, poor runout accuracy of up to 0.05 mm and therefore insufficient workpiece surface finishes and part accuracies. Also, the holder assembly is unbalanced by nature, causing companies to reduce their feeds and speeds-essentially giving away potential productivity."
HAIMER responded to this problem by inventing Safe-Lock. Safe-Lock is an EDM form in a shrink fit holder. When the operator shrinks the holder to insert a cutting tool, it engages the Safe-Lock form, which includes the grooves on the back end of the cutting tool and a matching EDM form in the holder in the rear of the bore.
"With about 20 licensed cutting tool manufacturers providing the Safe-Lock grooves on the back of their cutting tools as a standard, this feature-combined with HAIMER toolholders' runout accuracy-leads to low vibration and efficient machining," said the spokesperson. "HAIMER Safe-Lock provides, in addition to the pull out security, a very high runout accuracy of < 0.003 mm. Only Safe-Lock allows a maximum metal removal rate combined with absolute process reliability and precision. Due to the increased cutting depths and feeds, the metal removal rate can be increased by up to 100%, and to a similar degree tool wear decreases due to the excellent runout and balance characteristics."
While Safe-Lock was created in response to the issues heavy-duty machining had to face daily, Safe-Lock initially made a name for the aerospace and energy industries. However, cost and time savings are not solely restricted to typical aerospace applications and have also been found in milling applications. "In particular, customers utilizing the modern high efficiency dynamic milling strategies available from CAM software companies have found Safe-Lock to be an absolute necessity," said the spokesperson.
The spokesperson continued, "With Safe-Lock, machinists experience 100% cutting tool security and highly accurate clamping, due to a form fit clamping combined with an accurate friction fit of shrink fit or high precision collet chuck technologies with Safe-Lock. Also, there is no loss of accuracy, no tool pull out, no spinning of the tool and no damages on workpiece or machine."
For more information contact:
HAIMER USA
134 E. Hill Street
Villa Park, IL 60181
630-833-1500
haimer@haimer-usa.com
www.haimer-usa.com