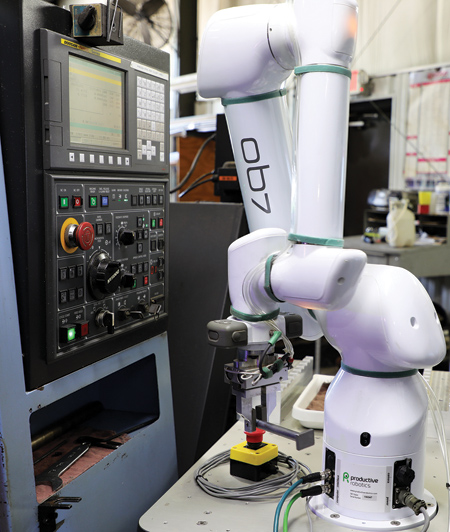
There were several compelling reasons why B.I.C. chose the OB7, including: ease of use; teaching (versus programming); all-around flexibility from machine to machine; 7 axes rather than 6; dedicated and responsive engineering; integration and service support from Absolute Machine Tools; product is made in America.
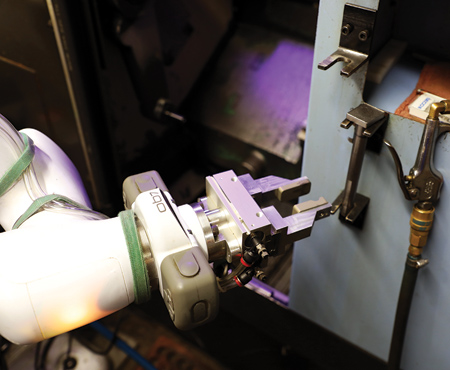
The OB7 cobot places the workpiece in a part staging bracket just prior to inserting it into the CNC lathe.
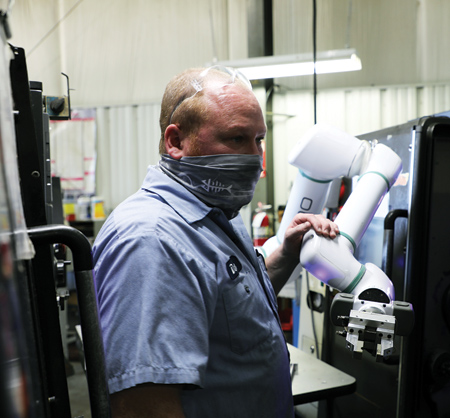
Cell and machine operator David Farris has become one of the resident experts on the cobot at B.I.C. Precision. Now he is free to work on less taxing and more interesting tasks in and outside the cell. He said the OB7's 7th axis J3 arm/wrist has allowed much greater maneuverability and flexibility in the cell.
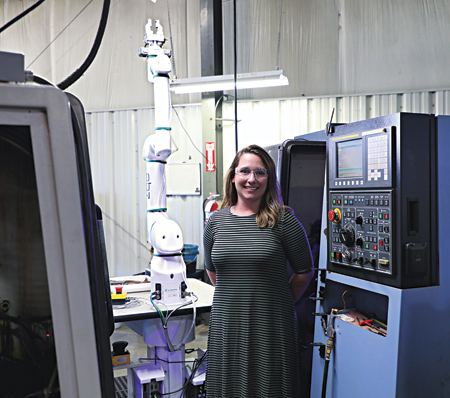
Sarah Burns, Business Operations Manager at B.I.C. Precision, was instrumental in choosing the OB7 cobot from Absolute Machine Tools. The OB7 solved the company's concerns of worker fatigue, space constraints and repetitive tasks and raised productivity by at least 20%.
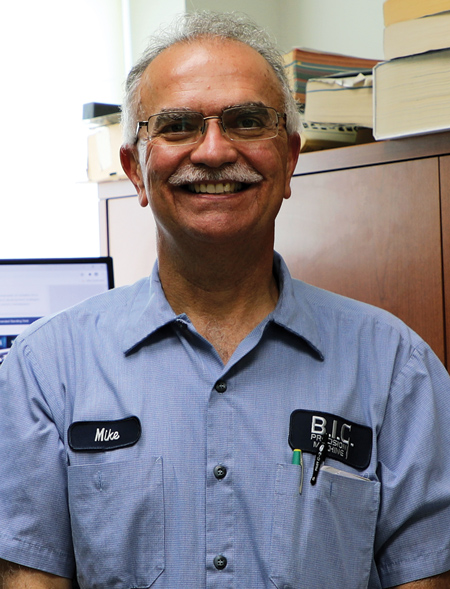
Mike Bellamy established B.I.C. Precision with his brothers in 1997. In 2008, they moved to a 21,000 sq. ft. facility in Blanchester, OH, with plenty of land for future expansion. The company specializes in precision parts for essential industries such as railroad, oil and gas, food processing, medical and electronics.
B.I.C. Precision is a contract shop in Blanchester, OH, and a top tier contract supplier of components for essential industries such as food processing and packaging equipment, railroad transportation, oil and gas, electronics and medical. The Bellamy and Burkhart families established the business in 1997 in a 4,000 sq. ft. shop in Goshen, OH. In 2008, the company moved to its current location and has expanded over the years into what is now a 21,000 sq. ft. factory, with ample surrounding land for future growth. B.I.C. employs almost 40 people.
"In addition to possessing the skills and knowledge to produce quality parts, the founding members also infused the company with the family's faith-inspired values of honesty and compassion for others," said a company spokesperson. "That is one of the prevailing reasons why B.I.C. installed an OB7 collaborative robot (cobot) servicing a turning center cell."
The OB7, manufactured by Productive Robots, is sold and supported in North America by Absolute Machine Tools.
"One of the shaft-like parts we process in our CNC turning center cell requires tens of thousands of parts each year," said Sarah Burns, Business Operations Manager at B.I.C. "That is a lot of repetitive motion on a human body. Standing there in a tight space, bending, twisting between the two machines, taking one part in, another part out, doing the finishing details and inspecting. The whole scenario was just too taxing on the body, not to mention the boredom of doing tasks over and over. And, when people are bored, they can make mistakes. Mistakes can lead to accidents and scrapped parts. It is just human nature; it happens to all of us. We needed a solution."
After doing research on various options to counteract the human toll, the company chose the OB7 cobot, which they have fondly named "Coby."
There were several compelling reasons why B.I.C. chose the OB7. According to the company, the top ones were: ease of use; teaching (versus programming); all-around flexibility from machine to machine; 7 axes rather than 6 (the OB7 is the only cobot on the market with the 7th axis "wrist" motion); dedicated and responsive engineering; integration and service support they receive from Absolute Machine Tools; product is made in America.
"That was the final seal of approval stamp for us," said Burns. "We are patriots here, and it means something to us that we are supporting another U.S. manufacturer."
The application for the OB7 cobot at B.I.C. is loading and unloading parts in the cell. The cell is comprised of two lathes with only 38" of space between them. Rather than eliminating the operator's job, as is often the concern from workers, B.I.C. simply re-allocated the operator's tasks to loading the parts into the cobot's pick-up tray and inspecting the parts when they are finished. According to Burns, this long run of parts requires almost 100% inspection of several dimensional features.
"We still need a person in the cell, but he is doing the more interesting, easier-on-the body sorts of tasks and is free to run other machines," said Burns, "Our worker's comp claims have reduced significantly. Additionally, Coby never gets bored, so scrap is a lot less now. We track productivity data, which is up at least 20% in the cobot cell. On a long part run, that adds up to a notable profit improvement.
"Our operators who cover that cell are much happier," continued Burns. "Before installing the cobot our people would work in the cell begrudgingly. Some were very clear about not wanting to work in there at all because of the mundane tasks they had to perform and the cramped workspace that was uncomfortable and potentially dangerous. Near the end of the work week, you could see the boredom and fatigue on their faces. But now with Coby as their buddy in there, that mentality has completely changed."
Burns noted that B.I.C. has been able to maintain workers compensation claims at zero for that area, reduce employee complaints and cut scrap rates by almost half.
Naturally, as with any new technology installed in manufacturing operations, there was some initial operator intimidation with the cobot. However, according to Burns, it did not take long for a couple of individuals at B.I.C. to become the resident cobot experts. One is a machine operator, Dave Farris, and the other is a college student, Preston Griffin, who is studying engineering and also had some CNC programming knowledge.
"It is important to note here that this line of cobots does not require conventional methods of coding or programming," said the spokesperson. "Shop personnel 'teach' the cobot tasks by simply using the hand controls on the EoAT (end-of-arm-tooling) and dropping and dragging icons on the touchscreen control tablet. Custom job functions for complex or repetitive tasks can be created, labeled and saved for future recall. The OB7's computer controls all axis joints and components, and network ports are locked to prevent unauthorized access."
"To help with the integration, we had Absolute Machine by our side every step of the way," said Burns. "We cannot say enough about their knowledge and support, from introducing us to the concept of a cobot, to its successful implementation, to assisting during the occasions when we need some fine-tuning, to today. It is an on-going partnership."
The spokesperson noted, "One thing it can do that no other cobot can is rotate its 'wrist' (the J3 arm) with a full, true, 7th axis of motion." The J3 arm joint provides the flexibility to operate in a confined space and reach around obstructions, such as a machine tool's sliding door. In B.I.C.'s case, the extra axis in the J3 arm allows them greater flexibility with positioning the two CNC lathes in the cell. It allows the operator to still have access in between the two machines to do maintenance, change inserts and more. Machine operator Dave Farris said, "It is that 7th axis that made all the difference in giving us greater maneuverability in this cell."
Tempering any indication that the application itself at B.I.C. was easy, all involved agree that theirs was a rather sophisticated set-up. The machines are complex to program and require skills to set them up to run in a long production mode. Additionally, the shaft-type parts machined in the cell play a critical role in the transportation industry. They are made of a proprietary stainless-steel material and certain dimensions feature a very tight tolerance, such as the thickness dimension.
"Even though our cell set-up was on the more challenging side, installing and implementing the OB7 into this cell was more straightforward than we expected it to be," said Burns. "So, for companies that may have less sophisticated applications, it will be even easier for them to implement this solution."
With operator safety being one of the main drivers for installing the OB7, B.I.C. opted for a Safety Laser (Lidar) Scanner to help prevent collisions and also allow the cobot to run at higher speeds. B.I.C. also opted for a larger gripper to better accommodate its wide range of workpieces that are processed in the cell.
To sum up all of the benefits the OB7 has provided, B.I.C. Burns said, "There are many benefits, some direct and some indirect. Definitely I would list the operator happiness factor, lower injury claims, greater productivity of at least 20%, more parts being made, fewer scrapped parts, improved part quality, faster delivery times and more competitive pricing when we quote on new jobs. It will likely open doors to new opportunities to quote on jobs that we would not have before. Coby has done so much for us, and Absolute has been such a great partner, that we will not hesitate to add more OB7s in our operations when it makes sense to do so."
For more information contact:
B.I.C. Precision
3004 Cherry Street
Blanchester, OH 45107
937-783-1426
www.bicprecisionmachine.com
Courtney Ortner
Absolute Machine Tools, Inc.
7420 Industrial Parkway
Lorain, OH 44053
800-852-7825 / 440-960-6911
sales@absolutemachine.com
www.absolutemachine.com