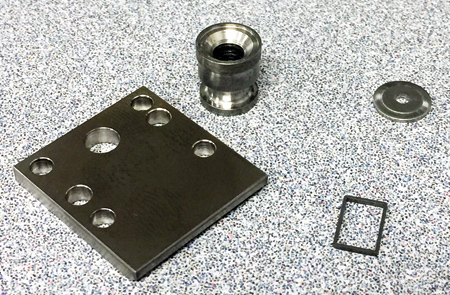
(clockwise from top)
- Cup seal: Lap one side to 0.4265" +/- 0.001" and a surface finish of 4 Ra
- Resonator for a microphone: Lap one side to a pocket depth of 0.004" +/- 0.0005"
- D Kovar metal frame for electronic circuitry (0.370" x 0.240"): Lap both sides to 0.027" 0.001"
- Nozzle mounting plate: Lap and polish both sides to a size of 0.125" +/- 0.005" while also maintaining the counter bore depth of +/- 0.005", with polished sides to a 6 Ra / "bright finish"
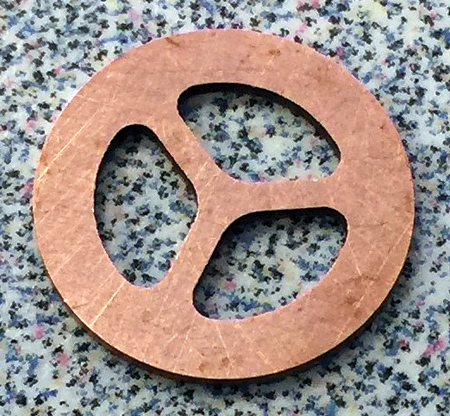
A copper washer part, 1/2" diameter and 0.034" thick, that is lapped and polished on both sides to a 16 Ra or better and a thickness of no less than 0.026"
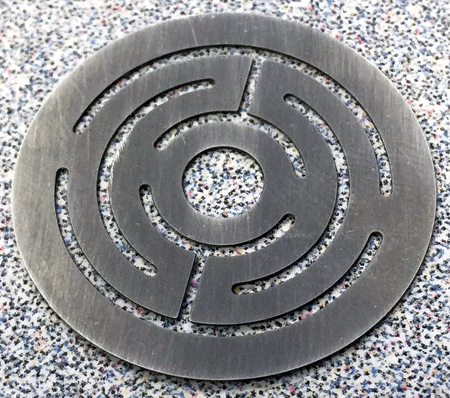
A stainless steel part, 1-1/4" diameter and 0.015" thick, lapped to 0.012" +/- 0.0003" with a surface finish of 32 Ra
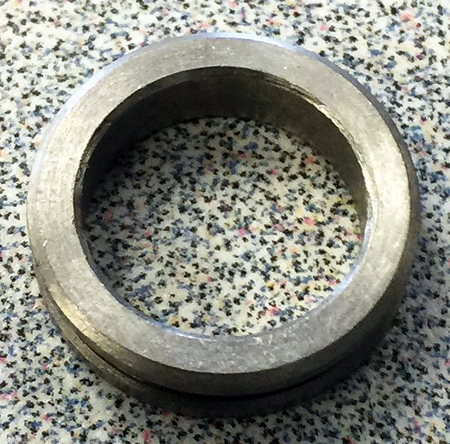
A steel spacer with a diameter of 0.687" that was flat honed to the customer thickness designation within +/- 0.0001"
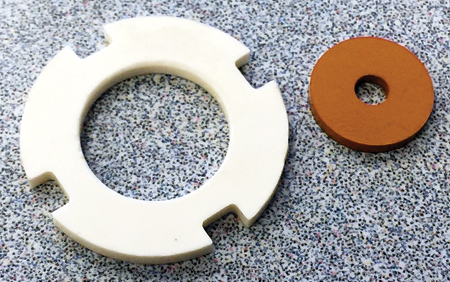
(l) A ceramic washer lapped to 0.100" +/-0.002" thick while maintaining the surface finish of 15 Ra or better
(r) Meldon 7001 washer lapped to 0.071" thick with a 0.002" flatness and parallel
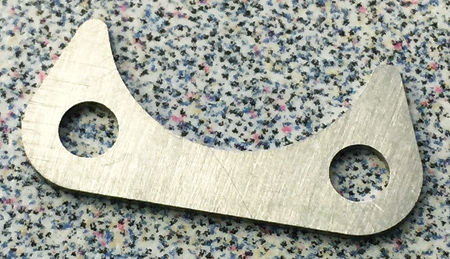
A steel transmitter shim that is flat honed to a thickness tolerance of +/- 0.0005". The part is 0.850" x 0.450" and the thicknesses vary based on the customer's requirements
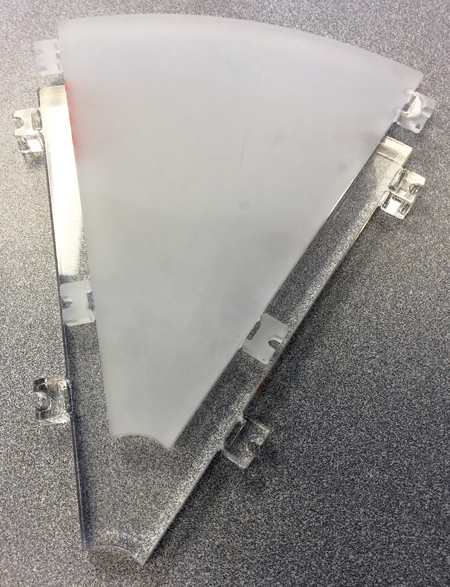
A large acrylic triangular window that is lapped to a TIR of ≤0.0015"
Flat lapping, a precise finishing technique, has been around for centuries. Lapping, named for the Loose Abrasive Polish (or "LAP") process it employs, is based on the grinding power of a free grain in an emulsion. While the actual process is quite straightforward, it has become a sophisticated process capable of producing extremely fine surface finishes.
What is Lapping?
Lapping is a precision process or combination of processes used to provide flatness, parallelism, size and surface finishes to extremely demanding tolerances. The process is a manufacturing method that employs particles of an abrasive material to remove stock from a surface. It is comparable to sanding or grinding, except that sanding and grinding use abrasives that are fixed (bonded abrasives), whereas lapping employs abrasives that are suspended in a liquid carrier and are free to move about. Lapping is sometimes referred to as Free Abrasive Machining.
Lapping and fine grinding processes are used where the surface finish, flatness or parallelism of the workpiece must be held to very close tolerances. Lapping can achieve a flatness rating of one millionth of an inch (0.000001"), parallelism tolerances of ten millionths of an inch (.00001") and surface finishes to 0.6 Ra using special handling and tooling techniques.
"Flat lapping is a superior manufacturing process for finishing materials, and is employed for its excellent economy and when other methods will not produce the precision and quality level required," said Joe Dominski, owner of Abrading Methods, Inc. in Elgin, IL.
Abrading Methods, which has been based in the same Elgin location for over 30 years, is the pioneer in high stock removal flat lapping and polishing. The company's original founder had more than 25 patents for the lapping and measuring equipment that still drive the industry today.
Abrading Methods can achieve flatness tolerances of 12 millionths (0.000012"), parallelism of fifty millionths (0.00005") and finish of 6 Ra on a volume production basis. "We can achieve tolerances at the limits of the lapping process (down to one millionth of an inch) on a case-by-case basis," said Dominski.
Abrading Methods' success is due to the inherent accuracy of its processes, simple workholding methods and large batch sizes. "Our primary business function is contract lapping of flat surfaces. We use specialized equipment and proprietary processes to perform these services for piece-part and production quantities," said Dominski. "Our goal is to be the premier provider of precision contract finishing services which we continuously work toward by focusing on the customer and delivering the finest finished components."
Flat Surface Finishing Solutions
Flat surface finishing solutions can entail various processes, depending on the application. For Abrading Methods, these processes can include double- or single-sided lapping, fine grinding and polishing.
Double-sided machining is recommended when processing is required on both sides of a part, or when there is a need for precise thickness, parallelism or flatness on both sides of the part. Typical applications include:
- Precision computer components
- Gage blocks
- Precision spacers
- Slitter knives and spacers
- Thin, brittle materials
- Bimetal pump swash/wear plates
- Cutting inserts
- Precision piston rings
- Automotive sensing devices
- Hydraulic gear pump components.
Single-sided high-speed lapping allows a competitive alternative to grinding with better finished part quality, according to Dominski. Typical applications that are ideally suited to single-sided lapping include:
- First surface referencing for subsequent operations
- Small, thin or hard to hold workpieces
- Fuel injector components
- Any sealing face/surface
- Gear and rotary pumps
- Slitter knives and spacers
- Valve plates and bodies
- Ceramic, glass, powdered metal, metal injection molding, carbide, titanium, molybdenum, stainless steel, Inconel and other hard to machine materials
- Hard coat anodized surfaces
- Extrusion, CNC and screw machine cut-off sizing.
Precision fine grinding (also called flat honing) is a process that was introduced in the late 1980s. "This process achieves a superior surface finish when compared to conventional grinding, and also provides faster stock removal than traditional lapping processes," said Dominski. "This type of finishing is best suited to products requiring a high stock-removal rate, but where traditional grinding would provide too rough a surface finish, or where precise tolerances are required."
Typical applications for precision fine grinding include:
- Metal injection molded parts
- Powdered metal (sintered) parts
- Seals
- Valve components
- Carbides and cutting inserts
- Precision piston rings
- Automotive sensing devices
- Hydraulic gear pump components.
Polishing is the most desirable choice when a superior surface finish is required. "Surface finishes can be achieved with polishing that are superior to any other method," said Dominski.
Typical applications for polishing include:
- Precision computer components
- Silicon wafers
- Optical components
- Static and dynamic sealing components.
Abrading Methods provides lapping, free abrasive machining, flat honing, fine grinding, polishing, burnishing, precision fine grinding as well as special deburring and cleaning techniques to process flat surfaces.
"While our primary focus is contract flat lapping, we provide added value to our customers by providing all other related services, such as cleaning, tumble deburring, sorting, certification, packaging and traceability," said Dominski. "In some cases, we perform complete part manufacturing. We provide certificates of conformance for our finished goods when requested."
For more information contact:
Abrading Methods, Inc.
1011 Davis Road
Elgin, IL 60123
847-742-6776
sales@lapping.com
www.abradingmethods.com