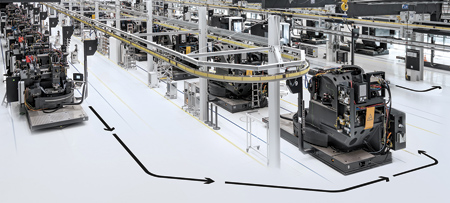
Digital and automated: the flow assembly with 34 AGVs in the new monoBLOCK Excellence Factory at DECKEL MAHO Pfronten increases productivity by 30%.
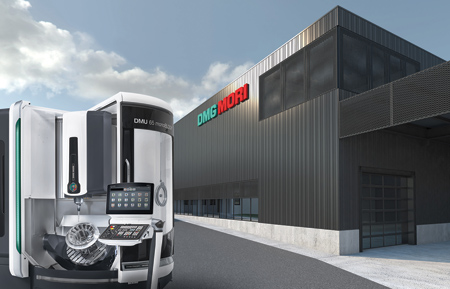
In the new monoBLOCK Excellence Factory at DECKEL MAHO Pfronten, up to 1,000 customer-specific solutions of the monoBLOCK 5-axis machining centers are now being produced.
DMG MORI has announced a new assembly concept. The production of its monoBLOCK 5-axis machining centers takes place at the new 4,000 sq. m Excellence Factory at DECKEL MAHO Pfronten, Germany. The flow assembly with an automated guided vehicle (AGV) transport system results in a productivity increase of 30%. This is also to the customers' benefit.
"Investments in innovations are the only way out of the crisis. Therefore, we are also automating and digitizing our internal value chain," said Christian Thönes, Chairman of the Executive Board of DMG MORI AKTIENGESELLSCHAFT.
The heart of production in the new monoBLOCK Excellence Factory is an AGV transport system. The AGVs move the machines autonomously through the assembly stations at a continuous speed of 45 mm/minute. Optical navigation using the latest laser scanning technology ensures a continuous process. As of now, the complete model mix of the monoBLOCK series including all series with palette changer (DMC) and mill-turn table (FD) is built in a flow assembly in 34 cycles, starting with basic assembly, geometry, machine cabinet and lastly the final inspection.
"Today, our new monoBLOCK Excellence Factory in Pfronten already demonstrates what tomorrow's production will look like. Using modern automation and digitization solutions, we consistently realign our locations to the production of the future," explained Michael Horn, Executive Board Member of DMG MORI AKTIENGESELLSCHAFT. "The driverless AGV transport system is perfectly integrated into the digital value chain of our production site. Compared to rail systems, the AGVs are a much more flexible solution, hence optimizing the production infrastructure."
The AGVs can also be freely navigated via remote control. The flexible timing of the machines ensures an uninterrupted and trouble-free flow during the assembly process, according to the company.
Complete Model Mix-Highly Flexible
With cycle times of just two and a half hours, every monoBLOCK machine can now be assembled in just seven days. This corresponds to a reduction by 30%. This increases capacity at the site from 600 to 1,000 monoBLOCK machines per year. "Our goal was to increase space efficiency and to be able to produce the complete model mix of the monoBLOCK series in a highly flexible, waste-free and even more productive way," said Reinhard Musch, Managing Director of DECKEL MAHO Pfronten.
Working in the monoBLOCK Excellence Factory has also undergone future-oriented changes: "We got our specialists involved in the design process of our monoBLOCK Excellence Factory from the very beginning, thus significantly improving all processes with regard to ergonomics and creating an optimal working environment to support our highly qualified specialists," explained Musch.
Digital Assembly Supported by TULIP
The new monoBLOCK Excellence Factory also sets new standards in terms of digitization. TULIP is an important component in the flow assembly. The U.S. start-up's software enables users without programming skills to create their own applications quickly and intuitively. With the help of the no-code platform, DMG MORI has developed an app solution that shows employees the necessary assembly information for each cycle with machine-specific work plans. Assembly processes of newly implemented equipment or special options are aided by detailed drawings, pictures and video instructions.
TULIP also helps with upholding quality standards: "Interactive checklists and inspection plans document the entire assembly process in real time and ensure continuous quality control during assembly," said Musch. Information is available in the TULIP app in real time along the entire value chain. There is a connection to the existing ERP system in place as well as a network right through to the suppliers.
Horn summarized: "The high demand proves that monoBLOCK machines are an important component of our portfolio. With the monoBLOCK Excellence Factory, DMG MORI has created a basis for further advancing production processes and offering short delivery times with a full product mix. The new monoBLOCK Excellence Factory offers us and our customers so many advantages that we will also transfer this concept to other plants."
For more information contact:
DMG MORI - Americas Headquarters
2400 Huntington Blvd.
Hoffman Estates, IL 60192
847-593-5400
Service Hotline:
855-DMG-MORI (364-6674)
us.dmgmori.com