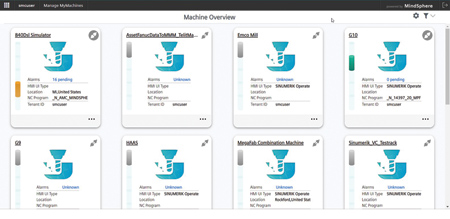
With Manage MyMachines, users can increase the productivity, reliability and availability of their machines on the factory floor. No matter where they are located, a machine's status, its operating mode and program status can be quickly ascertained through this Mindsphere cloud-based application.
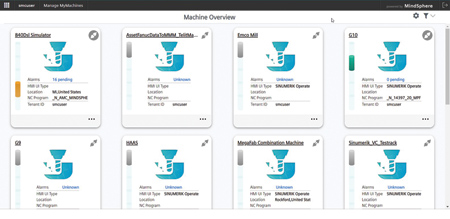
Siemens offers its digitalization portfolio to the metalforming and additive manufacturing (AM) communities.
"Our goal is to maximize the productivity of a machine by highlighting areas of improvement. Key Performance Indicators (KPIs) directing a company's operations are nothing new, but the way you get there has changed dramatically," said Pre-Sales Consultant, Steve Fruehe.
The machine builder or end-user sets the goals - and the machine hardware and software, working in tandem, collect and store the data in the cloud or on a local server. The experienced production and quality control personnel, who know the hierarchy of data and understand its use, big or small, can then work with Siemens to create and customize a series of apps to pull data points, extract the most important information and display them on various devices, whether on-site or remote, to give authorized personnel the ability to take corrective actions. This includes establishing predictive maintenance schedules and plotting the performance of a globally installed base of machines or a series of production lines, for further analysis or even future design modifications.
"That seems like a lot, but with Mindsphere and or our Analyze MyPerformace application, the customer has the ability to calculate KPIs such as OEE, machine availability, line performance and quality as referenced to set standards," said Fruehe. The system can be used to monitor machines, production and even physical assets at a company to better achieve production optimization.
As data points are analyzed, corrective actions can be more efficiently executed, through the combination of edge technology, servo positioning with PLCs, CNC program interfaces plus the drives, motors and mechanical components on the machine or line.
Fruehe continued, "Customers can bring their manufacturing process to us and we can help them select the most appropriate solutions. Clearly, the solution for a global OEM will not be the same as it is for a local fabrication shop, but the guiding principle is actually the same - namely, how do you want to gather the data, prioritize it, put it into an accessible format and use it to make things run better."
By offering a flexible suite of products, software and services, the optimum solution can be derived. Loud-based application loading speeds are getting faster at a significant pace, approximately 10x in the last nine months. Though cloud-based systems are not for everyone, usually owing to multi-nationals who operate their own cloud and very high-security application environments where IP concern is paramount.
"Our Mindsphere application, Manage MyMachines, is really the flagship of our digitalization portfolio, as it can visualize the status of a single machine in a manufacturing shop or a globally installed base of machines located on factory floors around the world," Fruehe said. Comparisons of machine run vs. idle time can be made by the week, the shift, the entire plant or the production monitored in a similar fashion.
For more information contact:
John Meyer
Siemens Industry, Digital Industries
Drive Technologies - Motion Control
390 Kent Avenue
Elk Grove Village, IL 60007
847-640-1595
cnc.marketing.us@siemens.com
www.siemens.com/manage-mymachines