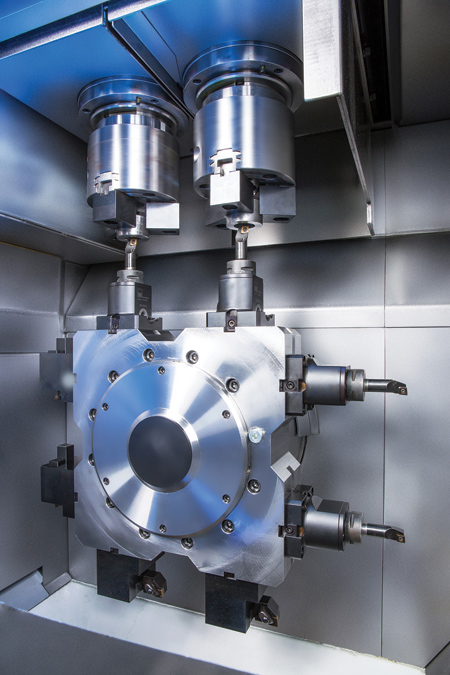
The two pick-up main spindles pick up two identical workpieces outside the machining area. The machining on the inside is done simultaneously with the EMAG turret (VDI 30 / BMT 45 interfaces)
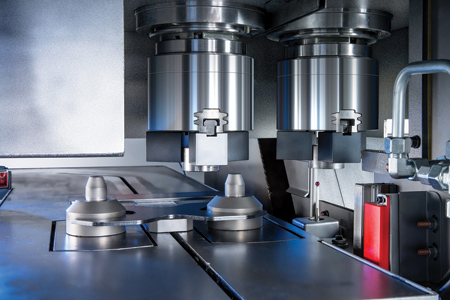
Optionally, a measuring probe is available outside the machining area. It is installed between the machining area and the pick-up stations. Measurements are thus carried out in a time-saving manner on the way to loading/unloading.
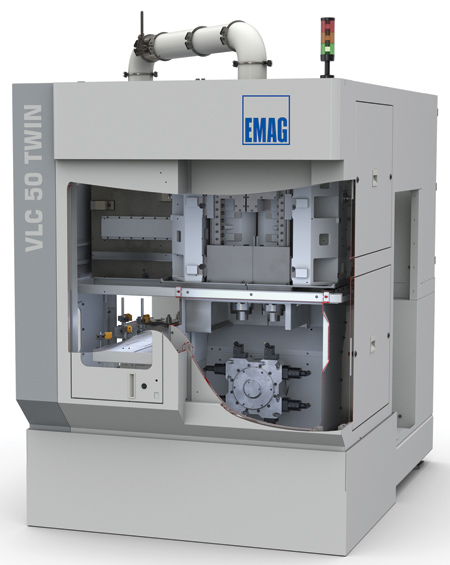
The competition between automatic torque converter and dual-clutch transmissions has been dominating transmission manufacturing for years. Now, torque converter systems are again increasing in importance. For one, they are still considered to be more comfortable, compact and strong. Secondly, some manufacturers rely on this technology for the design of modern hybrid drives. As a result, the quantities of central converter components such as planetary and sun gears are expected to increase significantly - with the (virtually self-evident) essential requirements of extreme machining precision and high pressure on costs.
EMAG is currently demonstrating how the upstream mechanical engineering sector is technically implementing these requirements with the VLC 50 TWIN double-spindle pick-up turning center for gear components up to 75 mm (3") in diameter - a productive solution for the large-scale production of planetary and sun gears. This machine manufactures two identical components simultaneously in the same machining area. In addition, direct distance measuring systems in the X-axis, recirculating roller guides and an innovative linear motor provide flexibility as well as repeatability and long-term accuracy. Integrated into complete manufacturing lines, this system provides economical production of a wide range of transmission components.
For decades, transmission manufacturing has been among the most innovative areas of automotive production. Established technologies such as dual-clutch transmissions and 9-speed automatic systems are representative of the tremendous pace of development in the industry. Over the next few years, the integration of new plug-in, full or mild hybrid systems will present additional challenges for management. We can anticipate that modern transmissions will get smaller and lighter, but will have more gear speeds and thus more geared components. As a result, components will have to be manufactured in increasingly large-batch sizes with increasing levels of precision necessary - an ideal requirement profile for the gear specialists at EMAG. Over the past couple decades, the company has been a driving force behind the evolution of transmission production with numerous innovations in mechanical engineering. The VLC 50 TWIN turning center for gear components up to 75 mm (3") in diameter is the latest chapter in this history of innovation, as Peter Loetzner, President and CEO at EMAG L.L.C., said, "Here we have really combined all the decisive productivity factors for this area of application: this cost-efficient machine guarantees high output quantities coupled with short non-productive times, while maintaining extreme precision and process reliability. The entire system is specifically tailored to the production of planetary and sun gears."
Two Main Spindles for Maximum Output
First of all, the basic technical configuration is very important. The VLC 50 TWIN has two directly driven, water-cooled pick-up main spindles (9.9 kW / 136 Nm at 40% duty cycle), that pick up two identical workpieces, simultaneously, to be processed in the machining area with the same clamping operation. Since both the headstocks for this machine move independently of each other, the diameter and the length of the two components can be corrected independently. The virtually wear-free linear drive in the X-axis ensures that the process is highly dynamic. The system has an acceleration of 8 m/s2 and is thus much more versatile than a screw-spindle drive. In combination with a direct distance measuring system, it also provides extreme machining quality. Generously dimensioned linear guides (size 45) with recirculating roller guide rails and the stable machine base made of Mineralit polymer concrete provide the required stability. Optionally, a measuring probe is available for installation between the machining area and the pick-up stations. Measurements can then be performed in a time-saving manner on the way to loading/unloading. The VLC 50 TWIN is available with FANUC 31i.
Overall, users of the VLC 50 TWIN benefit from extreme productivity: the average chip-to-chip time is just under 5 seconds and the total cycle time for turning a 38 mm (2") diameter planetary wheel is no more than 12 seconds (with a machining time of 24 seconds and two working spindles). "In this way, the output volumes will of course increase massively, and unit costs will decrease just as dramatically," summarized Loetzner. For this, it is very important that EMAG can integrate this technology into complete manufacturing solutions at any time by means of its proprietary TrackMotion automation system. This results in multi-technology production lines for the complete machining of a wide range of gears, rolling bearing rings or cams. The entire system is characterized by low downtimes and high process reliability. "We break down the machining process for a component into sub-processes that are easy to handle," said Loetzner. "The entire machining operation is performed by modular machines from EMAG. In OP 10 and 20, for example, two VLC 50 TWINs are used to machine two sides of the blank (soft-turning). In OP 30, we mill the gear teeth using an EMAG hobbing machine. Finally, in OP 40, deburring, press-deburring or the chamfer cut are also performed with EMAG technology. The TrackMotion system provides speed between the sub-processes." Users always benefit from the system's small footprint because the vertical EMAG design ensures consistently minimized machine footprints. Especially for lines consisting of several machines, the seemingly small space savings grow into a huge advantage. Additionally, the pick-up specialists have achieved some extreme values with the VLC 50 TWIN. With a footprint of only 4.59 sq. m (49.4 sq. ft.) for the basic machine (without chip conveyor and automation), is very compact, even for an EMAG turning center.
Great Market Potential
The fact that the specialists see exciting market potential for their new turning center is based on a number of factors, including the price-performance ratio. "We focus on consistent cost controlling throughout the entire development process and on standardized components. This has allowed us to significantly reduce the price per spindle," emphasized Loetzner.
The VLC 50 TWIN can be used in a large variety of applications. In addition to planetary and sun gears, it can also be used for turning roller bearing rings, flanges, sleeves or cams, for example. "The user will always benefit from these decisive factors: short cycle times, high precision, small footprint and an price-performance ratio for their investment. In combination with our TrackMotion automation, the VLC 50 TWIN is an ideal system solution for the increasing competition in transmission construction," concluded Loetzner.
For more information contact:
Kirk Stewart
Sales Director
EMAG L.L.C.
38800 Grand River Ave.
Farmington Hills, MI 48335
248-996-4703
kstewart@emag.com
www.emag.com
SOUTHWEST
TX, OK, AR, LA
Eric Klenner
Regional Sales Manager
EMAG L.L.C.
248-595-1530
eklenner@emag.com
NM
Shane Cross
Regional Sales Manager
EMAG L.L.C.
248-207-5365
scross@emag.com
SOUTHEAST
MS
Eric Klenner
Regional Sales Manager
EMAG L.L.C.
248-595-1530
eklenner@emag.com
AL, GA, FL, NC, SC, E. TN, VA
Dave Fitzgerald
Regional Sales Manager
EMAG L.L.C.
248-595-1117
dfitzgerald@emag.com
W. TN
Mark Comeaux
Regional Sales Manager
EMAG L.L.C.
248-938-2097
mcomeaux@emag.com
NORTHEAST
W. PA, WV
Mark Comeaux
Regional Sales Manager
EMAG L.L.C.
248-938-2097
mcomeaux@emag.com
NY, PA, DE, MD, NJ, CT, RI, MA, VT, NH, ME
Kevin Gadde
EMAG L.L.C.
248-938-2430
kgadde@emag.com
Portions of NY and PA
Jeff Moore
Regional Sales Manager
EMAG L.L.C.
519-835-8425
jmoore@emag.com
MIDWEST
OH, KY, IN
Mark Comeaux
Regional Sales Manager
EMAG L.L.C.
248-938-2097
mcomeaux@emag.com
W. MI
Peter Vandersluis
Regional Sales Manager
EMAG L.L.C.
616-307-7401
pvandersluis@emag.com
E. MI
Mark Ashworth
EMAG L.L.C.
248-826-4242
mashworth@emag.com
ND, SD, NE, KS, MN, IA, MO
Bill Konetski
Regional Sales Manager
EMAG L.L.C.
612-804-0857
bkonetski@emag.com
IL, WI
Joe Thompson
Regional Sales Manager
EMAG L.L.C.
248-880-0233
jthompson@emag.com
WEST
WA, OR, CA, NV, ID, MT, WY, UT, CO, AZ
Shane Cross, CMTSE
EMAG L.L.C.
248-207-5365
scross@emag.com