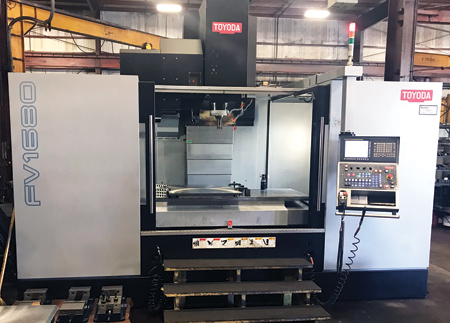
The Toyoda FV1680 machines AR450 wear plates.
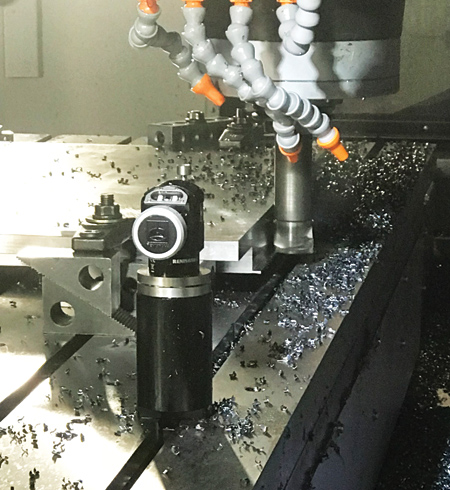
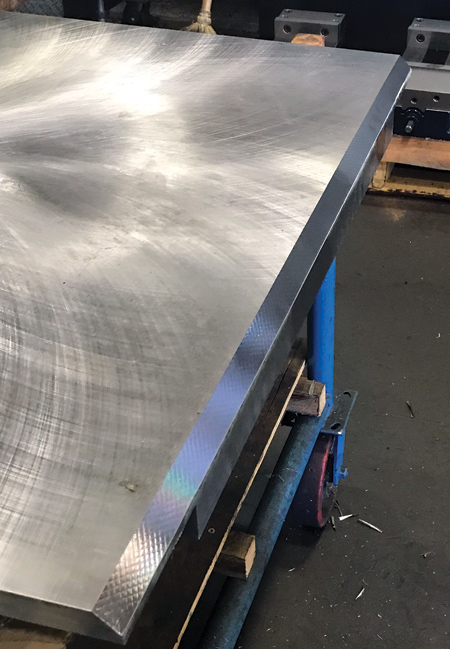
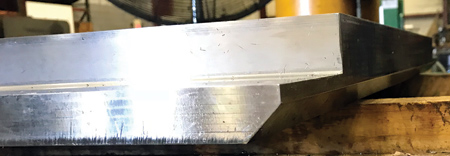
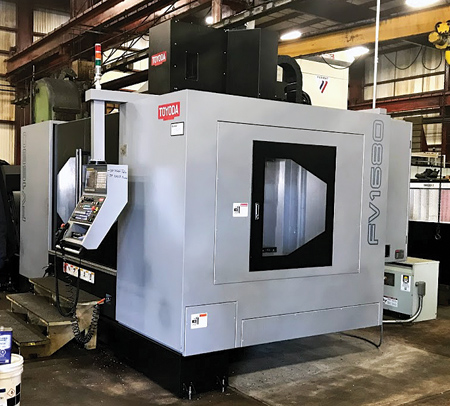
The Toyoda FV1680, a geared head, box way VMC.
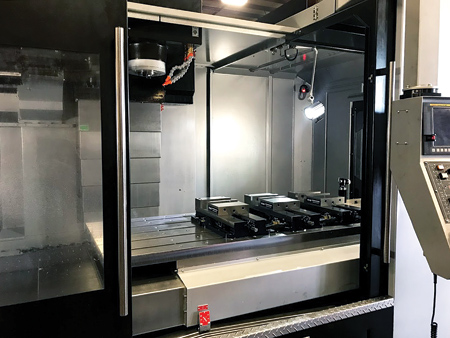
Lange said that features necessary for their processes-such as washing hose, oil skimmer, through spindle air, through spindle coolant, etc.-came standard on Toyoda's machine, whereas the same competitor options would have added tens of thousands of dollars.
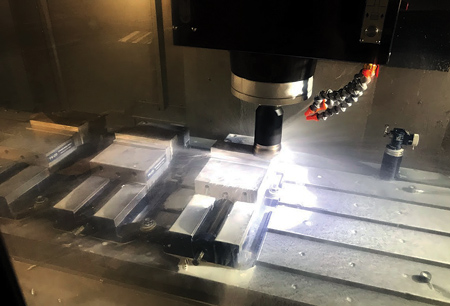
"Dual heavy-duty chip augurs parallel to the Y-axis, and high-pressure coolant-through spindle, means chips are immediately evacuated," said Lange. "The rigidity and power give us the highest confidence when machining 55 Rc while maintaining tight tolerances of less than one thousandth."
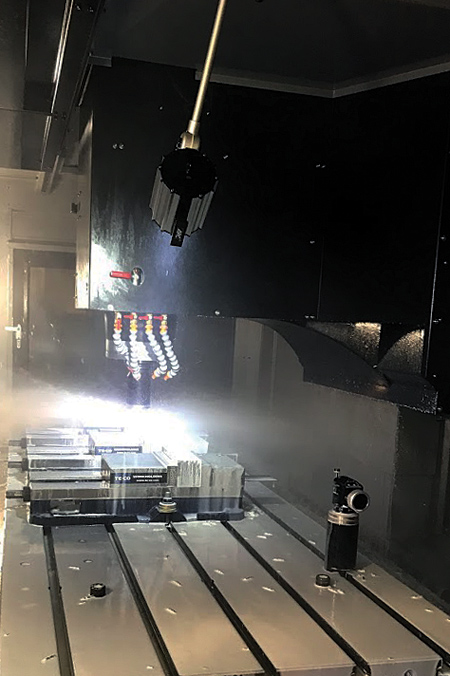
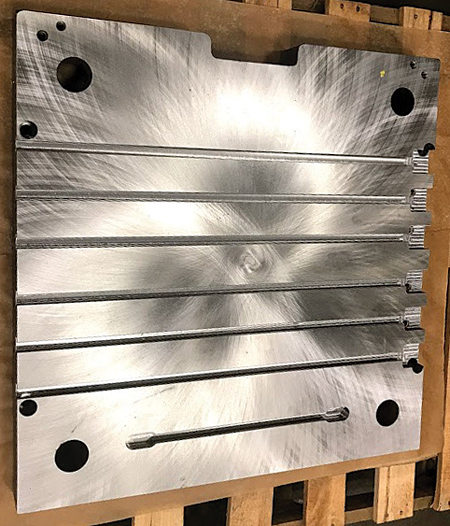
The Toyoda FV1680 meets tolerances of one thousandth with ease. It can handle vibration and heat generated interchangeably from hardened materials to aluminum without breakage.
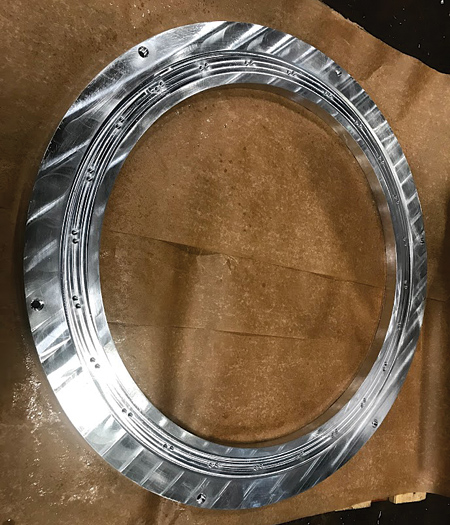
Richard Lange opened Lange Grinding and Machining, a 40,000 sq. ft. Streetsboro, OH, shop, in 1989 with only a few 1940s vintage grinders. Since then it has become known across the United States and Canada for specialized craftsmanship in large Blanchard and surface grinding.
Primarily a commercial and industrial precision grinding shop, 70% of Lange Grinding and Machining's workload encompasses hardened materials AR500, AR400 and H13. The company's typical work cycle involves steel, power generation and oil & gas customer prints. These are accompanied by raw materials, which are ground and then shipped to a third party to complete the machining process.
The Challenge
By having one of the country's largest Blanchard (ranging from 36" to 164") and surface grinding (up to 84" x 200") capabilities, Lange Grinding and Machining has long benefited from minimal competition. While it has achieved record turnover rates for ground products, outsourcing chamfering and hole making operations got Adam Lange to thinking of a customer-focused, streamlined solution. As a determined family-owned business, the evolution towards becoming a multi-faceted shop was the obvious next step.
"Our 'Aha!' moment took us realizing that we did not always know the final result of these parts," said Lange. "Often, contract manufacturing shops are only seeing a fraction of the machining required prior to final assembly. We thought, why not offer customers the opportunity to have all their work done here, and save them the cost and hassle of transportation?"
Current customers immediately backed Lange's expansion plan. The first non-grinding work-scope broadening investment was a large boring mill (X-axis, 157"; Y-axis, 98"), which allowed them to become competitive in large part machining. Lange's next step would be high performance milling of smaller armor plate products.
The Solution
Through much investigation, Lange narrowed his CNC prospects to eight machines. Because of the use of hardened materials and variety of workflow, Lange required a rigid box way CNC machine with solid cast iron construction to eliminate chatter, provide thermal stability and fight cutting forces. Addressing torque, Lange needed to be confident in a machine's spindle performance so that surface finish, material integrity and tool life would not be compromised.
Enter Toyoda's FV1680, a geared head, box way vertical machining center (VMC). "The horsepower, torque and the shear rigidity of the machine are impressive," said Lange. "Toyoda machines provide rigid and reliable machining of hardened materials." Lange also pointed out that features necessary for their processes-such as washing hose, oil skimmer, through spindle air, through spindle coolant, etc.-came standard on Toyoda's machine, whereas the same competitor options would have added tens of thousands of dollars.
Lange's new Toyoda FV1680 box way VMC features a #50 taper, 35 HP, 6,000 RPM geared head spindle with FANUC control system and 4th axis preparation. An FEM analyzed, heavy-duty, stress-relieved Meehanite casting supports a saddle with no overhang-providing the low center of gravity needed for enhanced rigidity.
"Identifying the biggest CNC motor was a deciding factor," said Lange. "No other brand compared to the FV geared head spindle's ability to sustain higher load capacities. Dual heavy-duty chip augurs parallel to the Y-axis, and high-pressure coolant-through spindle, means chips are immediately evacuated. The rigidity and power give us the highest confidence when machining 55 Rc while maintaining tight tolerances of less than one thousandth."
It was Toyoda's Regional Sales Manager Frank Madore who secured Lange's confidence as a long-term manufacturing partner. "Frank saw who we had been and where our sights were set within the new venture," Lange said. "He understood the chance we were taking and said, `I do not think you guys are done growing; Toyoda offers a lot of different machines to grow with you.' It made us feel comfortable knowing we had made the right choice in purchasing our first vertical."
The Results
The learning curve of a new box way VMC was not a hindrance. Lange valued a steady learning pace that embraced the FV1680's full breadth of capabilities. Knowing that rushed machining of hardened materials produces shattered taps and cracked products, their educational approach paid off.
"Toyoda is very straightforward, so learning the machine was easy," said Lange. "Producing a high-quality AR part is difficult. It requires steady milling, a lot of torque and a wise approach to proper tool utilization. We invested time in learning how the machine interacts with hardened materials."
AR400 and AR500 used in Lange's shop are abrasion-resistant steels (477-550 BHN). They withstand high impact stresses due to their outstanding wear, impact, fatigue and corrosion resistance. Patience and rigidity are required to prevent hardening and chipping where coolant use is increased and milling speeds are reduced. The material's hardness usually meets that of HSS tooling, so low machining and a powerful spindle minimize shattered tap occurrences.
Lange Grinding and Machining now runs the FV1680 every day, first shift, where it meets tolerances of one thousandth with ease. The machine's ability to handle vibration and heat generated interchangeably from hardened materials to aluminum without breakage has impressed the Ohio manufacturer the most.
"The FV1680is a very good job shop machine," Lange said. "The machine has handled anything we have thrown at it so far, which is imperative to our growth. We never know what is coming down the pipeline and we need to be readily capable."
With minimal advertising, Lange has been able to bring in new business from mining and steel customers, as well as smaller milling work. Prior to the FV1680 purchase, Lange's boring mill only allowed for competition in large part machining. By becoming more competitive in small-to-medium parts and offering a full-service shop, Lange has seen a heavy increase in work from current clientele.
"By adding the Toyoda FV1680 VMC, we are another step closer to becoming a multi-faceted shop. Now our eyes are set on turning, fabricating and painting," said Lange. "We have transformed the company from a specialized grinding-only shop, and in the process we have come to appreciate the versatility of Toyoda."
For more information contact:
Lange Grinding and Machining
10165 Philipp Parkway
Streetsboro, OH 44241
330-463-3500
sales@langegrinding.com
www.langegrinding.com
JTEKT Toyoda Americas Corporation
316 W. University Dr.
Arlington Heights, IL 60004
847-253-0340
info@toyoda.com
www.toyoda.com