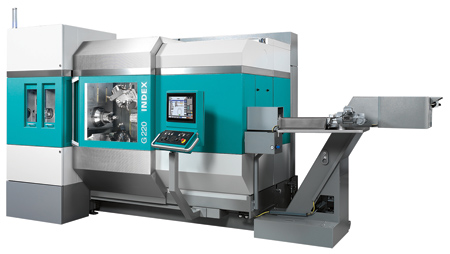
The G220 is designed to provide powerful turning and milling on one machine.
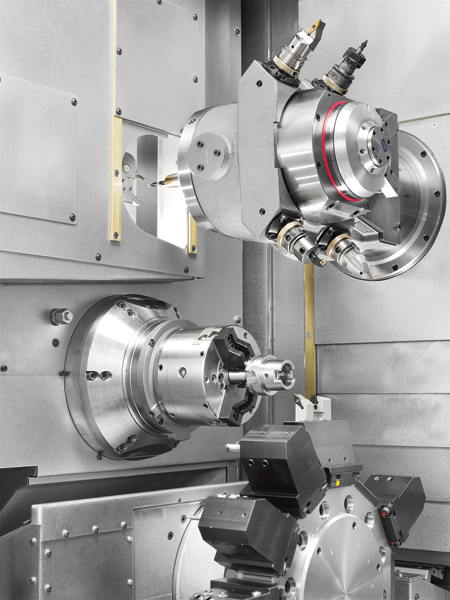
The motorized milling spindle is suitable for complex 5-axis milling.
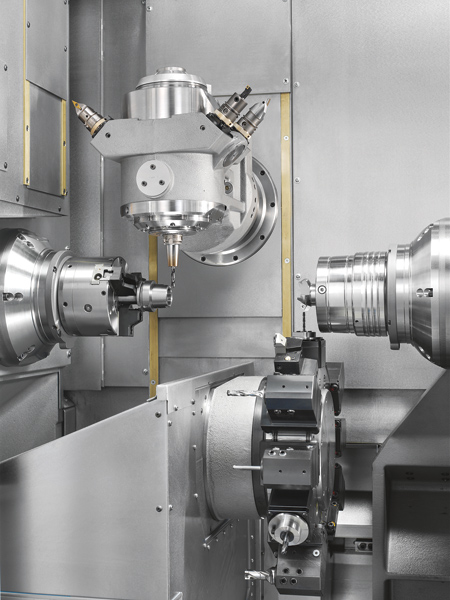
The tool turret is available with 18 or 12 stations and has a Y-axis with a traversing range of +/-50 mm.
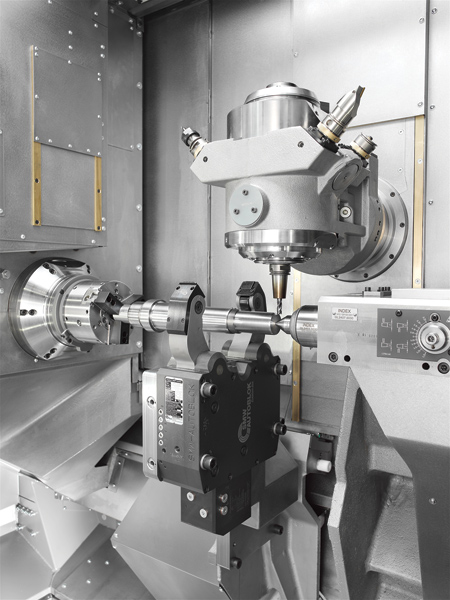
In addition to a CNC-controlled tailstock (pressing force max. 8,000 N, quill with mounting DIN 2079/SK30), a steady slide (steady head with clamping range 12-152 mm in diameter) is available, replacing the lower tool turret.
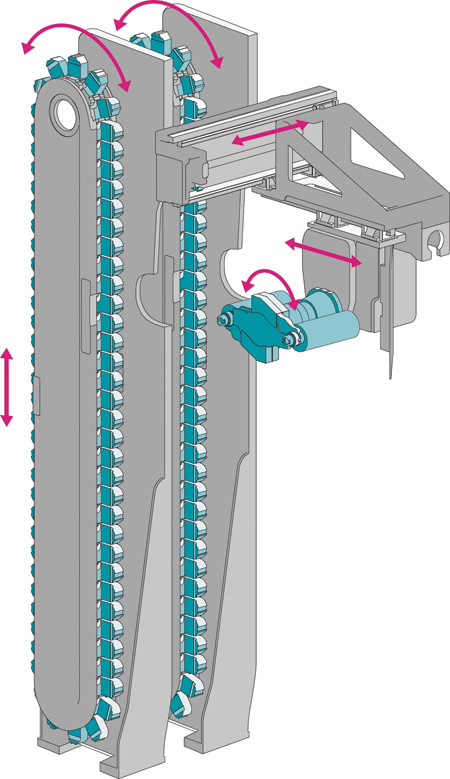
The tool magazine, designed with double rows, allows set-up during main time by using one chain for set-up and the other as the operational chain.
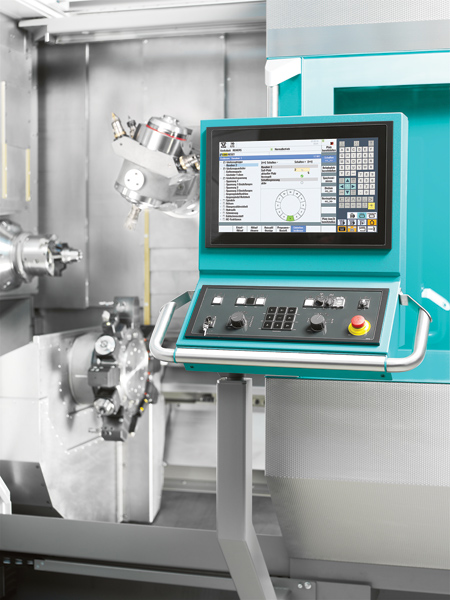
The latest INDEX C200 sl control generation is based on the Siemens Sinumerik 840D sl (solution line) and features an 18.5" touch-sensitive wide-screen monitor.
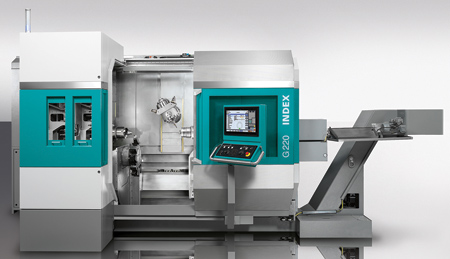
With the introduction of the turn/mill center G220, INDEX offers a complete redesign to its G-series. The series is designed to meet market requirements, such as increased complexity of components and decreased batch sizes. A motorized milling spindle capable of 5-axis milling and a tool turret with Y-axis provide increased flexibility.
The G220 is also available in a version with tailstock and steady slide, as well as optionally with a larger main and counter spindle (bar capacity 90 mm, spindle chuck diameter max. 210 mm, speed 3,500 RPM, power up to 40 kW).
A heavily ribbed cast iron machine bed and generously sized linear guides in the X- and Z-axis are designed to provide enhanced stability and damping properties. The vertical panels enclosing the work area are formed of a one-piece cover sheet in place of high-maintenance telescopic plates. The Z-axis slides with the motorized milling spindle and the Y/B-axis with hydrostatic bearing support are symmetrically arranged as a gantry. All key machine components have been optimized with the help of calculation and simulation models to help ensure both light and stable construction, improving the high dynamic response and cutting performance of the machine.
The turquoise "ergonomic belt" running around the machine enclosure marks out an area ideally accessible to the machine operator. All actions required to set up and operate the machine can be carried out under ergonomic conditions in this area, because all relevant components, such as main and counter spindles, turrets, motorized spindle and tool magazine or tailstock and steady slide, as well as the control panel of the machine, are located within this area.
The work spindles (main and counter spindles) are fluid cooled and have a bar capacity of 65 mm, optionally 90 mm (chuck up to 210 mm diameter). The distance between the spindles is 1,280 mm; maximum turning length is 1,000 mm. The motorized spindles of the main and counter spindles allow productive turning operations through their high dynamics, power and torque.
The spindle center is located 1,350 mm above the ground. The tool turret is located in the lower area, giving the customer the choice between VDI 25 or VDI 30 tool mountings. Accordingly, the tool turret has 18 or 12 stations, all of which can be equipped with individually driven tools (max. 6 kW, 18 Nm and up to 7,200 RPM).
The tool turret can move in the X and Z directions (index through space in Y 140/160 mm and in Z 150 mm) and it also has a linear Y-axis with a traversing range of +/-50 mm. "Due to the large work area and the distance between the main and counter spindles, simultaneous machining is possible with the motorized milling spindle and tool turret at the main and counter spindles - even on the face side - with no risk of collision," said a company spokesperson.
The fluid-cooled motorized milling spindle is arranged above the rotation axis. Its powerful drive (max. 11 kW, 30 Nm and 18,000 RPM) and B-axis, directly driven by a torque motor and running in hydrostatic bearings, are designed to make it possible to perform almost any drilling and milling operation due to high damping and stiffness.
"A Y stroke of +/-80 mm, a swivel range of the B-axis of -50/+230°, as well as a large X travel, which reaches 30 mm below the center of rotation, allow the operator to produce any geometry easily and productively with up to 5-axis machining," said the spokesperson. "The use of long projecting tools, particularly useful for multi-axis machining, also presents no problems."
The motorized spindle operates with a single or optional double-row tool chain magazine, which provides space for 70 or 140 tools (HSK-T40).
The stations feature a tilting basket design that protects the tools against contamination from oil and chips. Tools with dimensions of up to 50 mm diameter and 200 mm length can be used as standard. Alternatively, if adjacent spaces are free, tools of up to 120 mm diameter and 300 mm length can be used.
The double-row tool magazine with 140 spaces enables set-up during machining. This means that while the first magazine chain supports the current machining process, the machine operator can set up the second one with new tools.
A further benefit of the tool magazine in the G220 is the integrated drill breakage monitoring unit. Before a tool is returned to the tool magazine following use, an automatic check to determine if it is still fully available is performed using a light barrier. The unit can optionally be combined with a tool breakage and wear monitoring system that evaluates the axis drives' current motor consumption.
For effective complete machining of long or wavy workpieces, in addition to a CNC-controlled tailstock (pressing force max. 8,000 N, quill with mounting DIN 2079 / SK30), a steady slide (steady head with clamping range 12-152 mm in diameter) is available, replacing the lower tool turret.
INDEX has installed a CNC-controlled and CNC-programmable gantry-type removal unit for gentle removal of machined workpieces. It is capable of unloading both remnants from the main spindle and finished parts from the counter spindle (max. 7.5 kg weight). They are then placed on an integrated conveyor belt and discharged from the work area to the right of the machine.
In order to dissipate the heat produced in the fluid-cooled spindles and control cabinet, INDEX has integrated a hydraulic circuit with an interface enabling connection to a local cooling unit or a central cooling system. By implementing cooling functions away from the production area and eliminating the traditional fans, noise and heat emissions in the machine environment are reduced to a minimum.
The latest INDEX C200 SL control generation used in the G220 is based on the Siemens Sinumerik 840D sl (solution line) and features an 18.5" touchscreen monitor. This operating panel and the use of the latest capacitive touch technology - which can be used even when wearing gloves - makes it possible to move numerous rotary and touch buttons from the machine control panel directly to the screen. A touch of the finger is enough to activate functions, open files and folders or move entire display pages. This makes navigation easier than it was previously with a keyboard and mouse.
Buttons and switches available for selection, which apply to the current machine status and whose movements are released, are selectively backlit, while illegal ones remain dark. Flashing keys must be enabled by the operator, who is then guided through operations, preventing errors.
The operating panel can, however, do more than just operate the machine. It features a second input that INDEX uses for its Virtual Machine (VM) option. By pressing a button, the operator can switch to "VM on Board" and make use of simulation, regardless of current machine operations.
INDEX has utilized the new technical basis offered by the Siemens Sinumerik 840D sl to develop additional functions in the VM. CrashStop, for example, enables predictive simulation of the current workpiece program running on the machine. If it detects a collision, the function triggers a prompt machine stop before an actual crash occurs. Using RealTime, the machine program can be simulated on the operating panel simultaneously, thereby enabling real-time analysis of the machining sequence in difficult-to-access work area situations. With CAM on Board, the NX CAM system with INDEX post-processor can be used directly on the machine. This is particularly useful for extensive milling work. Another new feature is IT-FIT - INDEX-TRAUB Factory Information Technology - which allows the machine operator to retrieve information from the corporate network, for example, component drawings to set up the machine.
For more information contact:
INDEX Corporation
14700 North Pointe Blvd.
Noblesville, IN 46060
317-770-6300
sales@index-usa.com
www.indextraub.com
SOUTHWEST
N. TX
Prosper Machine Tools, LLC
7415 Whitehall Street, Suite 123
Richland Hills, TX 76118
682-626-5537
www.prospermt.com
S. TX
PD Browne South
440 Brenmar, Ste. 3150
Houston, TX 77060
281-405-9378
www.pdbrownesouth.com
NM
AME, Inc. (Adv. Mfg. Eng., Inc.)
5770 Clarkson Street #C
Denver, CO 80216
303-922-9266
www.amerm.com
OK
Gage Machine Tool
10668 Widmer Road
Lenexa, KS 66215
913-894-1233
www.gagemachinetool.com
SOUTHEAST
NC, SC, VA
Advance Machinery Sales, Inc.
416-C Gallimore Dairy Rd.
Greensboro, NC 27409
336-665-9114
www.am-sales.com
TN, AL, MS, FL (Panhandle)
Cardinal Machinery
7535 Appling Center Drive
Memphis, TN 38133
901-377-3107
www.cardinalmachinery.com
FL (except Panhandle)
Arthur Machinery
5903 Johns Rd
Tampa, FL 33634
813-887-4455
sales@arthurmachinery.com
www.arthurmachinery.com
NORTHEAST
N. NY
Britton Machinery Sales
330 Castlebar Rd.
Rochester, NY 14610
585-924-9335
www.brittonmachinery.com
W. PA
Marcus Machinery
106 Bellefield Court
Gibsonia, PA 15044
412-862-0803
info@marcusmachinery.com
www.marcusmachinery.com
MA, CT, RI, ME, NH, VT
High Performance Machinery
313 South Main St.
Orange, MA 01364
978-204-6501
hpm@mass.rr.com
www.highperformancemachinery.com
MD, E. PA, NJ, NY (Long Island, NYC), DE
Single Source Technologies, Inc.
2 Hagerty Blvd., Suite 300
West Chester, PA 19382
610-430-3670
www.singlesource.com
MIDWEST
KS, W. MO
Gage Machine Tool
10668 Widmer Rd.
Lenexa, KS 66215
913-894-1233
www.gagemachinetool.com
E. WI
Iverson & Company
441 North 3rd Ave.
Des Plaines, IL 60016
847-299-2461
sales@iversonandco.com
www.iversonandco.com
MI
Methods & Equipment Associates
31731 Glendale Ave.
Livonia, MI 48150
734-293-0660
sales@methods-equipment.com
www.methods-equipment.com
MN, IA, ND, SD, E. NE, W. WI
Hales Machine Tool, Inc.
2730 Niagara Lane North
Plymouth, MN 55447
763-553-1711
sales@halesmachinetool.com
www.halesmachinetool.com
WEST
OR, WA
Ellis Machinery & Equipment, Inc.
6225 20th Street E.
Fife, WA 98424
253-926-6868
sales@ellismachinery.com
www.ellismachinery.com
CO, WY
AME, Inc. (Adv. Mfg. Eng., Inc.)
5770 Clarkson Street #C
Denver, CO 80216
303-922-9266
www.amerm.com