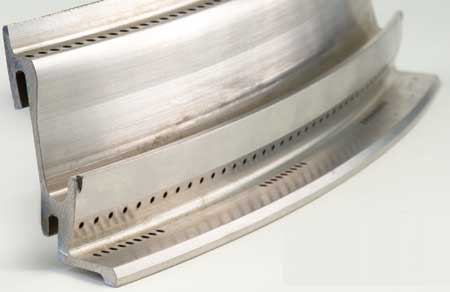
"Some engine combustor designs require a louver feature to direct cooling air at a right angle to the flow in order to cover a surface with air and more effectively cool the surface," said a company spokesperson. "It is often challenging to prevent back-wall damage when laser drilling these combustors. The LASERDYNE S94P control feature SmartStop minimizes and, in some cases, prevents this back-wall damage."
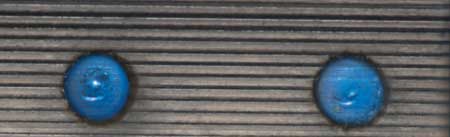
Damage (melting) of the back-wall (blue-colored region) occurred when 1 mm diameter holes were laser trepanned using Nd:YAG laser.
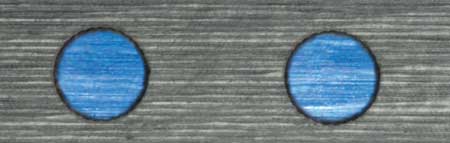
No damage (melting) of the back-wall (blue-colored region) occurred when 1 mm diameter holes were laser trepanned using fiber laser and proprietary LASERDYNE SmartStop.
Prima Power Laserdyne's latest S94P control feature SmartStop has been engineered to help prevent "back-wall" damage when trepan and percussion drilling turbine engine combustor components. According to the company, back-wall damage occurs when impingement of the laser beam on the part surface behind the one being drilled (referred to as the "back-wall") causes unacceptable melting of the surface of the back-wall. The feature is also designed to help minimize the buildup of debris on the back-wall.
"Based on advanced laser parameter control capability of the LASERDYNE S94P, it is possible to minimize and, in some applications, eliminate back-wall damage even in parts with small (1 mm) gaps between the back-wall and drilled surface," said a company spokesperson. "Back-wall protection is possible with the LASERDYNE S94P control used on LASERDYNE 795 and 430BD fiber laser systems where laser parameters are changed rapidly and consistently. Results using this recently developed macro provides reduced damage while maintaining throughput of 1.0 to 1.5 seconds per hole. Also, mapping of the actual workpiece surface using Prima Power Lasedyne's patented Optical Focus Control feature, for which there is no side sensing (as can be the case with capacitance-based focus control) ensures precise location of the holes whether they are perpendicular or at shallow angles to the surface. This is critical if there is another surface near that being laser drilled.
"It is a common practice to use materials such as Teflon or copper sheet to form a protective barrier to the laser energy that passes through the primary surface toward the back-wall. This has been marginally effective, sometimes allowing for back-wall damage as the laser beam penetrates the protection material. This is especially true when the back-wall is relatively close to the drilled surface. In other cases, the useful life of the barrier material may be short or the process results inconsistent. While protection material continues to be needed, the new LASERDYNE S94P feature control consistently prevents penetration of the protection material by the laser beam and extends the useful life of the material."
The LASERDYNE S94P control, which controls operation of the LASERDYNE 795 and LASERDYNE 430BD multi-axis fiber laser systems, is continually upgraded with new process features such as the one designed to control back-wall damage. According to the company, SmartStop will be a standard feature in upcoming versions of LASERDYNE S94P software and available as a standard feature on new systems. The software when released will also be available without charge to existing customers.
"Our goal at Prima Power Laserdyne is to continue to produce advancements that help expand the use of laser processing and make our customers to be more successful," said Terry L. VanderWert, President of Prima Power Laserdyne. "LASERDYNE products are enabling precision laser cutting, welding and drilling by system users around the world."
For more information contact:
Prima Power Laserdyne
8600 109th Ave. North, #400
Champlin, MN 55316
763-433-3700
lds.sales@primapower.com
www.primapower.com