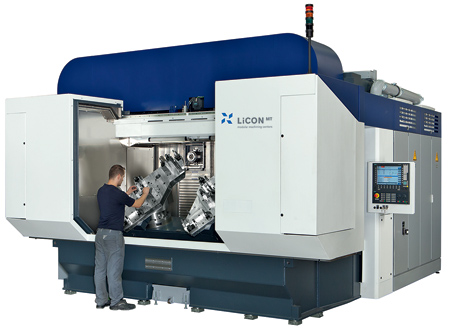
Double-spindle 5-axis LiFLEX II 1066 i HMC
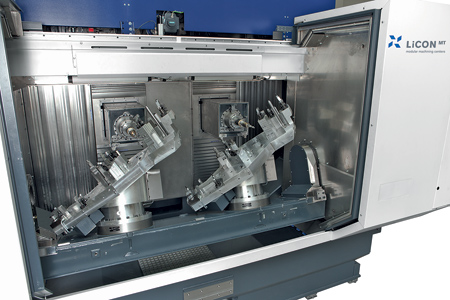
Workspace of the LiFLEX II 1066 i with clamping fixture for a structural component
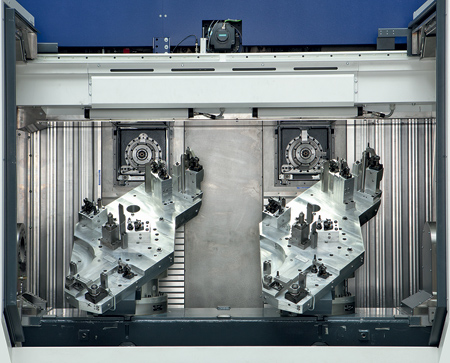
Workspace of the LiFLEX II 1066 i with clamping fixture for a structural component
The sum of small but significant differences can make a crucial difference in part cost. "For a long time, maximum possible dynamic values paired with a more rigid design, per the motto `the more, the better,' were considered to be the argument that could decide a sale for machine tools," said a Licon spokesperson. "However, stiffness is frequently only specified statically and not dynamically. Detailed analyses and the established lean efforts of many users draw a more differentiated picture of the aspects that influence the performance of a machine tool, and hence the unit costs." Some examples are described in this article.
"Liflex represents a broad modular system that contains all of the relevant modules that determine the performance of a machine tool," said the spokesperson. Single-spindle - and especially twin-spindle - machining centers can be configured according to requirements. Liflex offers sustainability and a holistic approach with the objective of exercising maximum impact on minimizing the unit costs. Users attest to the crucial long-term accuracy of the Liflex machining centers in daily use."
Besides the permanent optimization of the modules themselves, understanding the interaction between the modules within the machine tool is of paramount importance. "Licon develops all of the main components installed in a Liflex machine. The developments are targeted at a lasting contribution that is as large as possible with regard to the performance of the machining center," said the spokesperson.
Dynamics and Robustness
"Despite supposed similar functional principals and similar technical data, a closer look reveals clear performance disparities between the machines of different manufacturers," said the spokesperson. "Using a car as an example, the client can determine the driving behavior of vehicles from various manufacturers in an extensive test drive. Machine tools require an intensive, detailed field comparison. For the purchase decision, the unit costs at which his components can be produced with the machine are frequently only known in theory to the user. To refer to the comparison with the car again: the horsepower must be applied effectively to the road. In addition, both car and machine must be suitable for everyday use. These aspects, among others, restrict the use of linear drives in machining centers. Therefore, Liflex machines have high - but not the highest - dynamic values. The development engineers have deliberately given the dynamics and robustness, longevity and process reliability equal importance - which is highly valued by the users."
Action and Reaction are Equal and Opposite
An example of machine tool robustness is the selection of the spindle. A sure sign of this is an HSK 100 spindle. Performance and torque are also parameters that influence the purchasing decision. Most of the solutions in the market demonstrate good static and dynamic stiffness values in the axes on the spindle side. "However, the question regarding the stiffness value on the workpiece side (action and reaction are equal and opposite) automatically arises," said the spokesperson. "Because of its two spindles, the highly efficient double-spindle machine places great demands on the design of the swinging bridge system. Any underestimation of the stiffness requirements would result in greater tool wear and the tendency to oscillate. For these reasons, the project engineer can select different swing axis types from the Liflex configurator. Also, with relatively high clamping pressures, Liflex machines can provide process-reliable machining at 500 Nm torque per spindle." This corresponds to an overall removal rate at 1,000 Nm on the 5-axis bridge.
Swing Bridge Systems
High requirements on the system are well known from steel and cast iron, but even in aluminum machining there are cases where swing axes are tested to the extreme. Greater tool wear or additional machining cycles negatively influence the unit costs. Both are avoided by selecting the appropriate version. With the double swing axis, the version with double swivel trunnion (DT) can only be used to a limited extent in terms of dynamic stiffness. For heavy-duty machining, the directly loaded machine (DL) - which offers significant advantages due to the dynamic stiffness on the workpiece side - is used for this purpose. After all, the bridge must be designed for the machining forces of both spindles. For loading in parallel to the machining time at the same time as heavy-duty machining, the PC version is recommended. This version uses the robust swing bridge of the DL version with an additional upstream device for loading: the pallet changer.
Challenges with Light Machining
An example of the other side of the machining spectrum is tool breakage monitoring when machining aluminum. Usually, systems that detect tool breakages by controlling the drive currents of the main spindle are used. At lower cutting capacities, significant process uncertainties occur in these systems. "Alternatively, tactile or optical test systems continue to be used even today, which are mostly at the cost of the support cycle time and, hence, the productivity of the machine," said the spokesperson. "Too often the fact that the functional reliability of these electronic monitoring systems depends crucially on the smooth running of the spindle goes unmentioned. Even at a cutting capacity of only 15 watts, Licon spindles guarantee the safe detection of tool breakages which corresponds to machining with a tool diameter of only 2 mm." Downtimes due to a false alarm from the tool breakage monitoring or because of crashes in the wake of undetected tool breakages are also ever recurrent waste topics in lean analyses.
Simplifying Double-Spindle Machining Center Operation
Although the economic advantage of the double-spindle machines is obvious in direct comparison with single-spindle machines, some users have respect for the requirements when adjusting the machines. As soon as tolerances become demanding, correction options are required in order to keep the machining of the spindles within the required tolerance windows. Independently correctable spindles in Z (Liflex i technology) are in use in many places. Liflex i3 technology enables the two spindles to even make corrections in all three axes (XYZ) independently. Thus components are machined on Liflex machines that have a tolerance window of only 10 µm in the X and Y coordinates. "In addition, the formerly typical warm-up phases of the machines at the beginning of the shift or at least at the beginning of the week on grounds of cost are now a thing of the past," said the spokesperson. "If these requirements come together, any quality and adjustment problems are avoided with the correction function of the i3 technology. The i3 technology of the correction in X, Y and Z is the most advanced solution currently on the market."
MQL: Energy Efficiency + Tool Service Life + Longevity
Besides the robustness described above, tool wear and longevity also play increasingly important roles in the course of integrated approaches to the valuation of production systems. In addition, the increase in energy prices means the energy costs per assembly part are no longer negligible and can be higher than tool consumption costs. "Although reservations against the use of the minimum quantity lubrication (MQL) still exist, this technology is continuing to gain ground," said the spokesperson.
The prime reasons are:
- Significantly lower energy costs due to elimination of the cooling system
- No machine wear due to coolant
- Longer tool life.
The requirement for successful use of MQL technology is optimum chip disposal in the machining center. In conventional 4-axis machines with a vertically arranged fourth axis, this was not structurally possible. However, all Liflex machines have a machine bed optimized in this respect, combined with the possibility of turning the swing axis to free the fixtures from chips.
Creating Quality in a Clamp - 5-Axis Machining
Machining components completely in a single clamping process instead of multiple operations reduces quality issues and production downtimes. For this reason, 5-axis machines are often required, depending on the complexity of the component. Investment in the fifth axis soon pays for itself. It also simplifies the operational sequences enormously. Re-clamping for an additional operation is dispensed with entirely.
Tool Magazine
Components have different machining steps. This means that the requirements for the number of tools are also dependent on the application. The Liflex configurator provides solutions for 30 to 240 tools. If this is not enough, complementary magazines can be used - even with a cleaning device on request. This solution is especially in demand where the machine is used for machining a variety of workpieces. The tools can then remain in the machine and are immediately ready for use again for the machining of the next batch. This is mostly combined with the pallet changer where the changing of the clamping fixture is realized especially easily and quickly due to good access via the zero point clamping system.
For more information contact:
Licon mt L.P.
2135 Bishop Circle-East
Unit 1
Dexter, MI 48130
734-426-2240
lothar.koerner@licon.com
www.licon.com