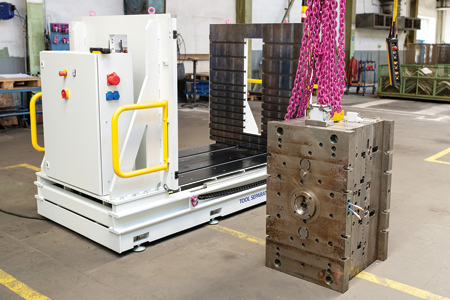
RUD's innovative Tool Separator.
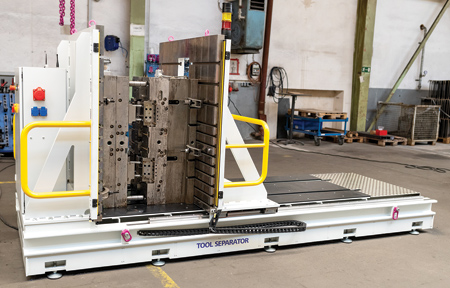
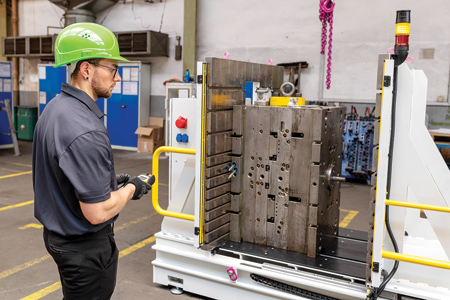
The Tool Separator separates tools quickly and accurately.
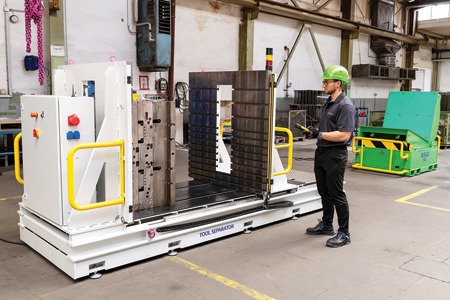
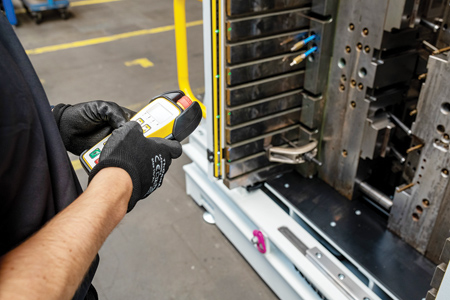
Tool Separator can be operated safely and conveniently using its radio-controlled operator devices.
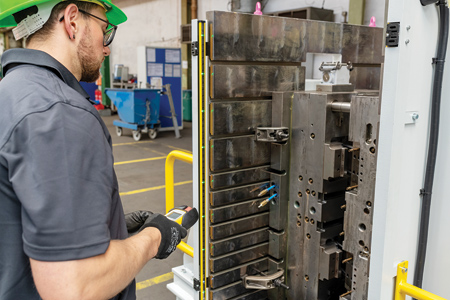
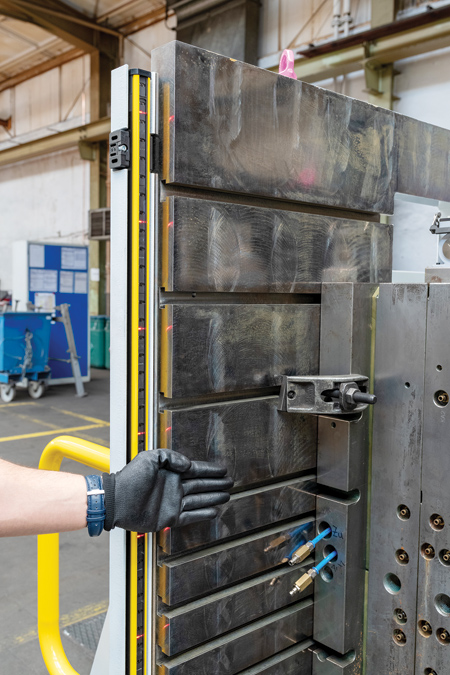
The safety light curtain protects operators who are working on or close to the Tool Separator.
RUD's new Tool Separator is designed to make tool handling safer and, importantly, much faster. "This latest innovation opens injection tools, punching tools and forming tools in a matter of seconds, optimizing the production, service and maintenance processes. Working with RUD's new Tool Separator is especially safe and ergonomic. This makes the Tool Separator the ideal companion to the Tool Mover Pro, RUD's tool-handling machine."
"The Tool Separator is a real milestone in the history of safe and efficient tool handling," stated Anne Kühling, Product Manager in RUD Ketten Rieger & Dietz GmbH u. Co. KG's Conveyor & Drive division. "The initiative for our latest development came directly from the market. Companies often have to separate massively heavy tools by hand using cranes, sledgehammers and tire irons. Depending on the tool, this can take between 30 minutes and three hours, and take up the time of up to three members of staff. Other machines, such as injection molding machines or die-spotting machines, might also be put to use to separate the tool. This is very inefficient and has a direct impact on operating costs. A solution to this problem had to be found urgently."
RUD's new Tool Separator needs a maximum of five minutes and one person to complete the entire process. RUD's Tool Separator operates with an opening and closing force of 50 kN (corresponds to 5-1/2 tons). A PLC control system helps ensure effective operation. Carefully controlled force and speed mean tool halves can be opened gently and closed accurately. Operators can set the degree of force from a theoretical 0 to 55 kN, and set speeds from 0 to 2,000 mm per minute.
Using the Tool Separator not only protects expensive tools, but also safeguards the joints and vertebrae of operators. At only 380 mm high, the contact surface allows work to be performed safely and ergonomically. After opening, the operator can work directly on both halves of the tool, to perform minor repairs or maintenance tasks, while it is held securely in the Tool Separator. This reduces the downtimes required for maintenance. It is not possible to operate the Tool Separator, either by pressing buttons on the machine itself or by remote control, if anyone is standing between the two halves of the tool.
The Tool Separator is driven electrically by RUD's TECDOS Pi-Gamma 2-in-1 chain drive system, which was specially developed for horizontal and vertical applications. This system is based on a high performance round steel chain, also developed by RUD. The drive system is designed to be robust and low-maintenance with a long service life.
"The Tool Separator's electrical drive is its distinctive feature, because it operates entirely without hydraulics. A hydraulic drive not only needs more maintenance, but also takes up more space because of the additional hydraulic unit. In contrast, the Tool Separator is a compact all-in-one system," explained Walter Lais, Designer at RUD Ketten Rieger & Dietz GmbH u. Co. KG. "Its compact construction means we have been able to bring its contact surface down to 380 mm, which is very low. That makes it an excellent, ergonomic working height for operators."
RUD's custom-made Tool Separator machines are made in Germany. The prototype is sized for tools weighing up to 11 tons, but can also handle lighter or heavier tools with ease. The Tool Separator has a 1,300 mm x 1,300 mm clamping plate and a sliding and contact surface at a height of 380 mm. "Theoretically, anything is possible here: we can adjust the machine to handle lighter or heavier tools, greater or lesser forces and smaller or greater distances between the clamping plates. We can also modify the plates themselves, depending on what is required," said Lais. The Tool Separator can also be moved by crane, so it can be used just where it is needed.
To ensure safety in the workplace, optional add-on parts, such as a guard bracket, can be installed to complement the automatic stop function, which triggers as soon as anyone is detected on the Tool Separator. A light curtain or protective fence can also be supplied to optimize safety in the working environment. Due to its radio-controlled operator devices, the Tool Separator can also be operated safely and conveniently outside the danger zone.
"RUD's latest generation of tool separators, the Tool Mover Pro, has already revolutionized the way in which tools are serviced and maintained. The Tool Separator is the logical addition to the range," said the spokesperson. With the Tool Mover Pro and the Tool Separator we really can offer the dream team for optimizing costs and processes, ensuring that tools are handled safely and ergonomically. And that applies across the most diverse applications: from tool manufacturing to metal stamping and bending technology, aluminum die casting and injection molding to the automotive industry and the packaging and container industries. Having two separate machines also helps reduce the waiting time for employees because they can work independently of each other."
For more information contact:
RUD Ketten Rieger & Dietz GmbH u. Co. KG
Conveyor & Drive division
salesfa@rud.com
www.rud.com