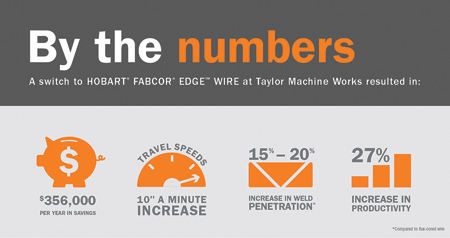
Taylor Machine Works saved money and improved productivity by converting to Hobart welding wire.
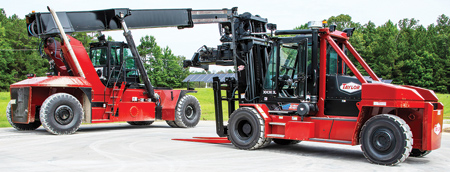
Taylor is a manufacturer of more than 85 models of powered industrial trucks such as forklifts and material handling equipment for customers across North America and internationally in the shipping, marina, steel and aluminum industries.
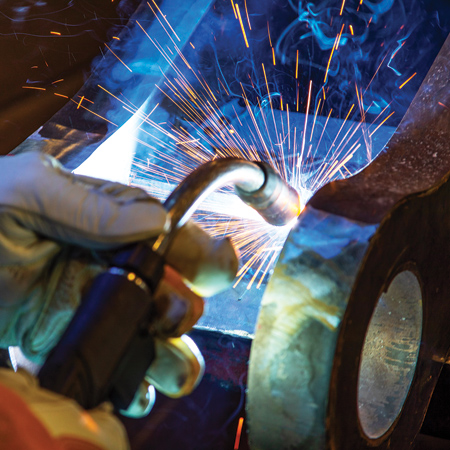
In a test of the metal-cored wires, Taylor saw an immediate impact on productivity and weld quality when using the wires on T-1 steel due to faster speeds, higher deposition rates and less post-weld cleaning.
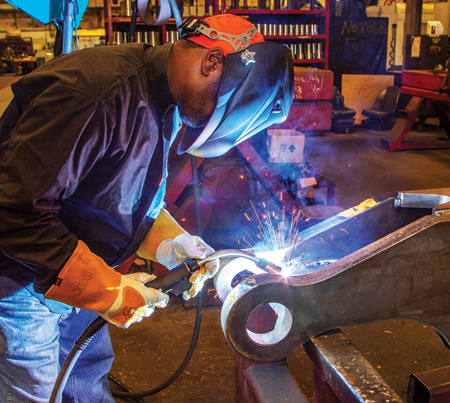
"Once they get familiar with it and you show them the correct way to weld with metal-cored, they love it," Kurt Glenn, fitter welder, says of training new welders. "It is a quicker, better and cleaner job with the metal-cored wire."
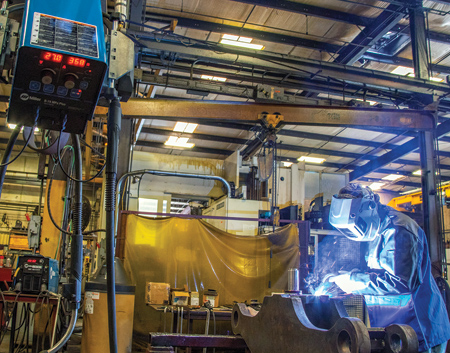
In addition to the filler metal change, Taylor is converting its welding fleet to Miller XMT 450 multiprocess welders-replacing power sources that were as old as 15 years. The more compact XMT 450 welders reduce the amount of space the machines take up in the shop.
When Taylor Machine Works was founded as a family-owned automotive and repair business in Louisville, MS, in 1927, the company motto was painted on the building's sign: "We engineer and build what you need." More than 90 years later, the company produces much bigger machines, but that motto still holds true.
"Taylor's name and reputation were built on customization. Between 40 and 50% percent of what we build has engineering or research and development applied to it in some way," said Matt Hillyer, Director of Engineering, Taylor Machine Works. "The forklifts and equipment we design and build are integral to our customers' needs. Answering those needs is all about knowing the customer very closely, and them knowing us."
Along with the commitment to customization, the company has stayed consistent in many other ways through the years. The same family that started Taylor Machine Works is still at the helm today, with the third and fourth generations involved. The company also remains in Louisville-population about 6,300-because that is where its roots are. That legacy lets customers know they can "Depend on Big Red" and the machines Taylor produces.
"Customers can count on us to have a piece of equipment that is going to be in operation for the long haul, and it will serve the needs of their business," Hillyer said.
"The Taylor legacy also includes a commitment to innovation and improvement," said a company spokesperson. Founder W.A. Taylor Sr. produced his first conventional timber skidder in 1937, a pioneering machine that was later developed into a mobile skidder and loader. Product development and innovation is still a constant.
Today, Taylor is a leading manufacturing of more than 85 models of powered industrial trucks such as forklifts and material handling equipment for customers across North America and internationally in the shipping, marina, steel and aluminum industries. Many of these machines are highly customized to meet specific customer needs.
As part of the drive for innovation, Taylor is always looking for technologies that help the company improve. A recent change to the welding filler metal used for equipment fabrication at Taylor significantly increased productivity and decreased costs-allowing the company to be even more nimble in responding to customers and meeting deadlines.
"The benefits were immediate," said Steve Nazary, Quality Assurance Supervisor. "We have really improved our quality and our productivity by using Hobart wire."
Welding Heavy-Duty Products
Taylor's production is driven by market demand. When the market is up and customers need equipment, they do not want to wait for development or research. Taylor works to respond quickly with a solution for customers.
Equipment durability and dependability are also key drivers for Taylor's customers. If a customer is a small lumber mill with only three pieces of equipment, that business cannot afford to have one machine go down for repairs.
"That is a large part of their ability to produce and run the business," Hillyer said. "So, we need to make advanced, innovative products that are also simple, durable, easy to work on and provide constant uptime."
Taylor produced roughly 750 pieces of rolling stock in 2017 that went out the door to customers. Welding is a critical part of that manufacturing operation.
"Welding technology and filler metals are key to us providing a quality product," Hillyer said. "It has to stand the test of the customer's application and the test of time."
Metal-Cored Wire Saves $365,000 a Year
The company previously used flux-cored wire in its welding operation but made a filler metal change after Taylor's welding distributor suggested that Hobart FabCOR Edge and FabCOR Edge D2 metal-cored wires could help improve welding performance. In a test of the metal-cored wires, Taylor saw an immediate impact on productivity and weld quality when using the wires on T-1 steel due to faster speeds, higher deposition rates and less post-weld cleaning. "It increased our speed probably 10 inches a minute," Nazary said.
Taylor has since standardized to the 1/16" FabCOR Edge wire for all its welding applications on materials more than 1/2" thick, including mild steels and high-strength steels with tensile strength of 70,000 pounds. They use the 1/16" wire to weld metals up to 5" thick. When working with materials less than 1/2" thick, the shop uses .035" Hobart solid wire.
"We did a study when we first changed the wire and we came up with $365,000 worth of savings per year," Nazary said. "That is huge. The more Hobart wire we use, the more cost savings will add up."
In addition to the filler metal change, Taylor is converting its welding fleet to Miller XMT 450 multiprocess welders. These compact XMT 450 welders reduce the amount of space the machines take up in the shop.
"The XMTs are really smooth and the wire rolls through smoothly. You can adjust welds perfectly," said Adam Eubanks, a fitter welder with Taylor. "It puts down a better-quality weld, and just makes it easier for welders."
Productivity Gains of 27%
The substantial annual cost savings for Taylor are due in part to the significant productivity increases from the Hobart FabCOR Edge wire. It welds faster and delivers better penetration-about 15 to 20% greater weld penetration compared to flux-cored wire-so more filler metal can be deposited in less time. That means more equipment can be completed and out the door faster for customers.
"By switching to Hobart metal-cored wire, we increased productivity 27%," Nazary said. "That is a big improvement. That is a big cost savings." The metal-cored wire also delivers easy weldability.
"I like it because it burns a little hotter, and most of what we weld is thicker material. It is a more efficient wire," said Eubanks. "It puts a better weld down, even on material that is not perfectly cleaned."
Reduced Spatter and Less Cleanup
"Because the FabCOR Edge wire does not produce a slag on the weld bead, it greatly reduces the time and money Taylor spends on interpass and post-weld cleanup. There is no need for welders to remove slag between weld passes," said the spokesperson.
Previously, the operators used a chipper hammer to remove slag and spatter between passes, which added time and hassle to their process.
"Once we got the metal-cored wire, it eliminated that," said Kurt Glenn, a fitter welder and robot operator. "There was no more spatter or slag. It was a clean weld. It stacked a lot better."
In addition to saving time in weld cleaning between passes, it also saves time in cleaning up around the shop and money in equipment maintenance.
"We quit buying air chippers and we do less maintenance on the chippers now," Nazary said. "We quit having to sweep the floor as often, and there is less cleanup in the paint shop. These were all immediate benefits of using the Hobart wire."
The reduced spatter of the metal-cored wire also makes cleaning and painting the parts easier and faster, allowing Taylor to get parts from the production cell to the paint cell much faster.
Better Looking, High-Quality Welds
The aesthetics of the finished welds on the equipment Taylor produces is another important consideration. The company conducts visual weld checks and sometimes dye penetrant checks on restricted weld joints.
"The welds look smoother. They have a lot better eye appeal and that is very important," Nazary said. "We had a lot less cracking issues with the wire, also. I have more people pass the test with this wire than I did with a flux-cored wire."
The wire is more forgiving, so it is easier for even less experienced welders to produce a quality weld.
"Once they get familiar with it and you show them the correct way to weld with metal-cored, they love it," Glenn said of training new welders. "It is a quicker, better and cleaner job with the metal-cored wire."
Save Time and Money with Metal-Cored Wire
The forklifts and material handling equipment built by Taylor Machine Works must be tough and durable enough to take on heavy loads. The filler metal used by Taylor to fabricate its equipment must match that toughness.
"The weld filler metal strength is imperative. We need filler metal to be highly durable, high strength and handle stresses and high forces," Hillyer said. "We look to our suppliers like Hobart to provide us with the right technology."
The conversion to FabCOR Edge wire has significantly improved productivity and saves Taylor a significant amount of money while helping the company produce better-looking, higher-quality welds.
For more information contact:
Taylor Machine Works
3690 N. Church Ave.
Louisville, MS 39339
662-773-3421
www.taylorbigredforklifts.com
Hobart Brothers Company
101 Trade Square East
Troy, OH 45373
800-424-1543 / 937-332-4000
hobart@hobartbrothers.com
www.hobartbrothers.com