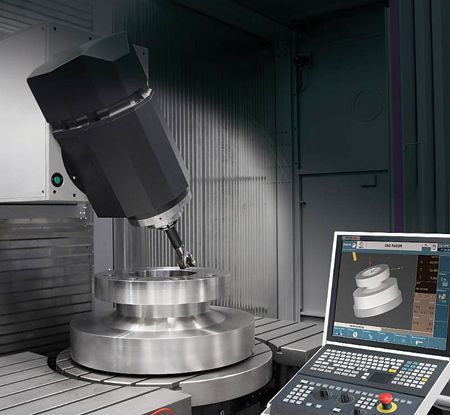
"The Fagor 8065 is a high performance CNC capable of up to 28 axes and 4 channels, but contains simple tools that allow for seamless operation no matter what the situation," said a company spokesperson.
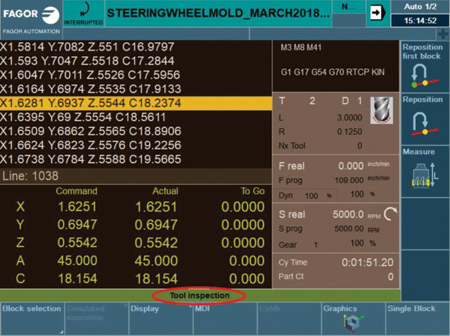
Fagor Tool Inspection Mode active screen
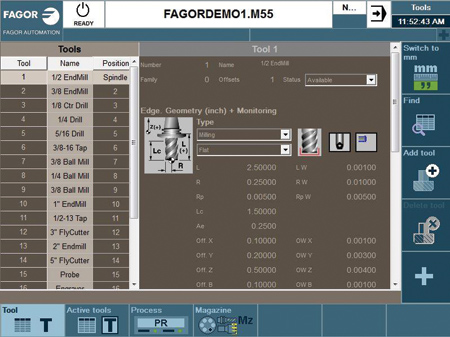
Jumping to the tool offset page and making modifications is accomplished easily within the Tool Inspection Mode.
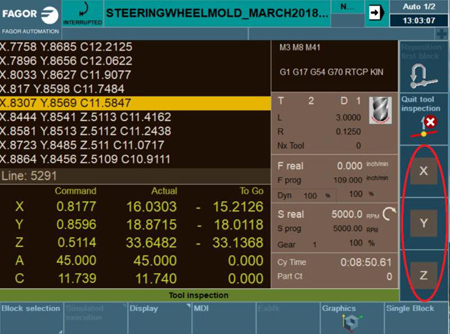
"In an ongoing quest to provide a solution for every situation a machine tool operator may encounter, Fagor Automation R&D has been focused on providing simple steps to get operators back on track during virtually any machining operation," said a company spokesperson.
According to Fagor, one of the features given a lot of focus in recent years is not so much a singular feature, but instead a whole mode of operation that lives within another mode of operation. The Tool Inspection Mode is contained within the Program Execution Mode. By pressing "cycle stop" within the Program Execution Mode, the user can interrupt the part program and the Tool Inspection soft key choice instantly becomes available. With the program stopped, the user is now able to enter into the Tool Inspection Mode.
Once in Tool Inspection Mode, the program is in an interrupt state. The operator can shut down the spindle and either jog or MDI to a safety position. When the operator is ready to resume, a simple Auto-Return via a soft key automatically repositions the axes to the interrupted axes positions of the program in reverse order in which they were positioned. Pressing Cycle Start will then resume the part program as normal from the point of interruption. "What is nice about the Auto-Return Mode is that it returns the user to the position hands-free in the reverse order in which the user pulled out of the part, assuring no part or tool collision on the position return," said the spokesperson.
If the operator had interrupted the part due to spindle chatter or part surface inconsistency, he could then, while in Tool Inspection Mode, modify tool wear. By simply choosing the Tool Offset soft key, the user's active tool parameters immediately appear on the screen, thus allowing for easy modification. In addition, at this time, or anytime during program execution, the operator can adjust the feedrate and spindle override for better part surface performance.
Another feature is the ability to actually change tools or perform a tool calibration offset directly in Tool Inspection Mode. A soft key appears that allows the user to jump directly into Tool Calibration Mode, allowing the user to then set a new tool. The user can return to the original position with Auto-Return or MDI when finished. "This is especially beneficial when the program interrupt was due to tool breakage. This allows the user to either call another tool or set an entirely new tool," said the spokesperson.
An advanced feature, called Cancel Continue, has also been implemented. This allows the operator, while in Tool Inspection Mode, to change the continuation point of the program from the interrupt position. After choosing the soft key Cancel Continue, a cursor appears over the program code stop block and allows the operator to scroll forward or backwards within the program to choose a new "resume program" position. This also comes in handy for tool breakage interrupt conditions, allowing the operator to return to the point of breakage. The CNC also has a Retrace feature capability, which allows the operator to interrupt the program, and then manually reverse to a previous position of up to 75 program blocks.
Another new feature is the custom ability to edit/modify the program being executed. If the customer chooses to allow these features, they simply name the program with the extension ".mod". Any program with this extension is allowed to be modified within execution mode. This allows an operator to tweak the part program during the cycle for maximum tool performance.
The Fagor 8065 CNC allows for custom screens, windows and even operator pop-ups, thus customer desired features of most any nature can be implemented. There is also a Simulation Mode that allows for the part program to be simulated in graphics or just main plane commands as they choose. Both High Definition Solid Graphics or Conventional Tool Path Line Graphics are available to the operator. Zoom or full part orientation and rotation is a standard Graphics Mode feature.
In addition, with Automatic Block Search, an operator can find any point in a program and resume the program from that position in a few seconds. In this Search Mode, the CNC activates the history of the program up to the block search point, thus no prior preparatory function adjustments are needed to enable program restart.
For more information contact:
Fagor Automation - USA
2250 Estes Avenue
Elk Grove Village, IL 60007
fagorusa@fagor-automation.com
www.fagorautomation.us