

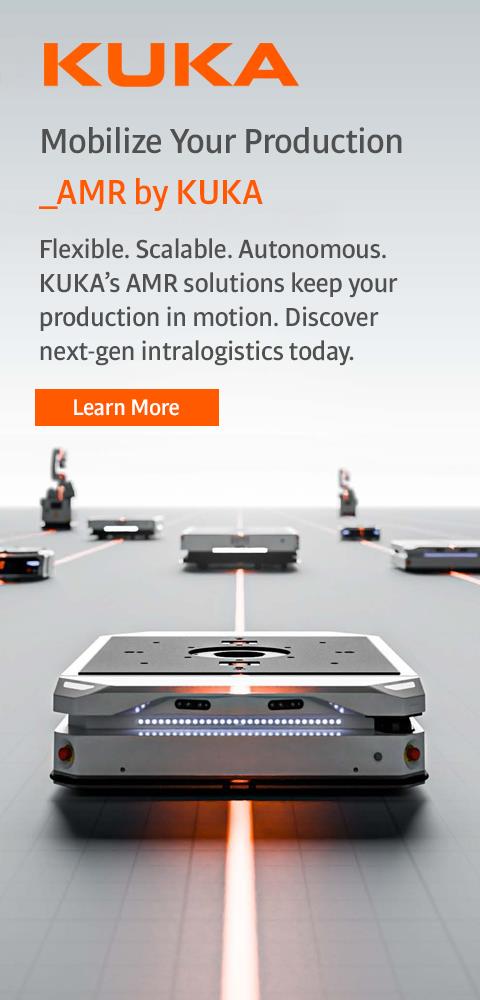
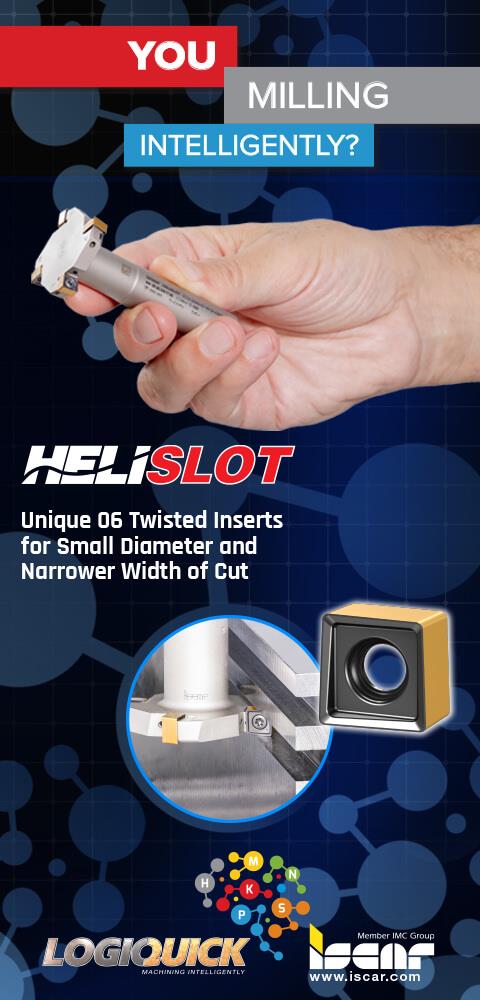
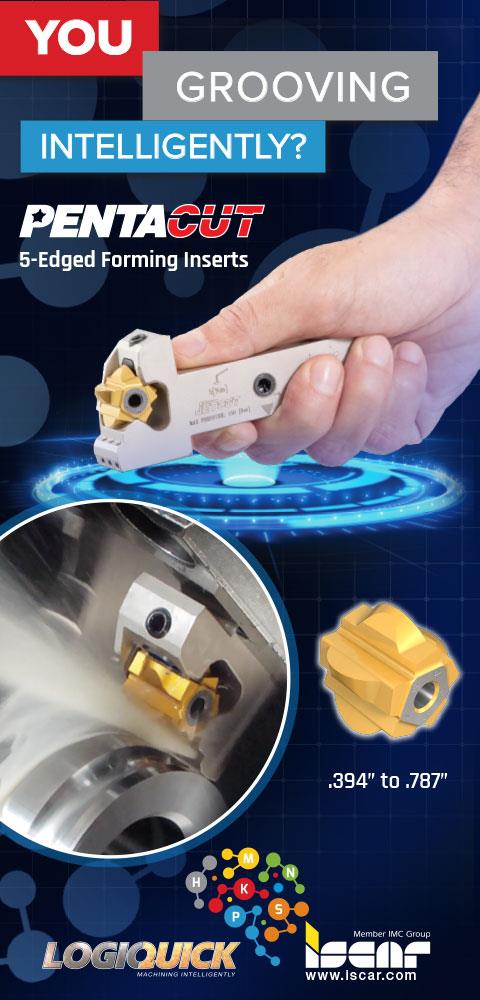
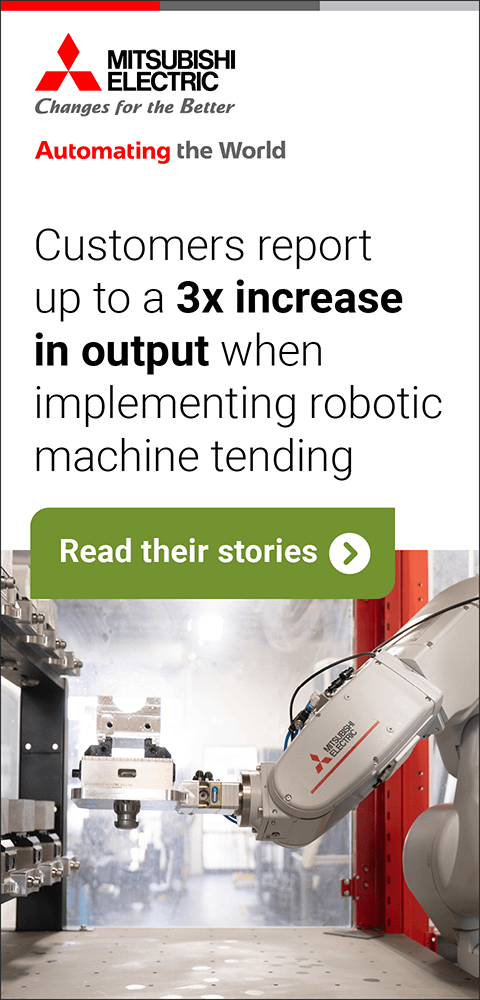
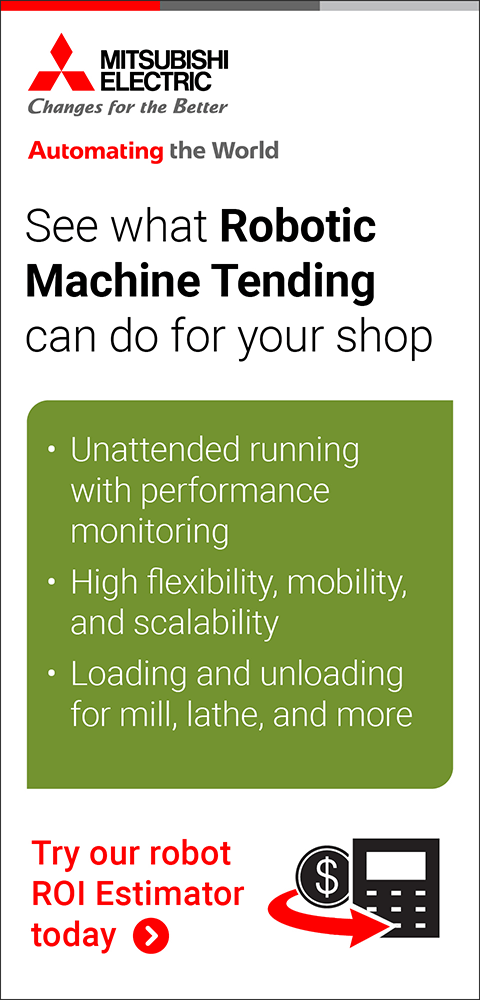
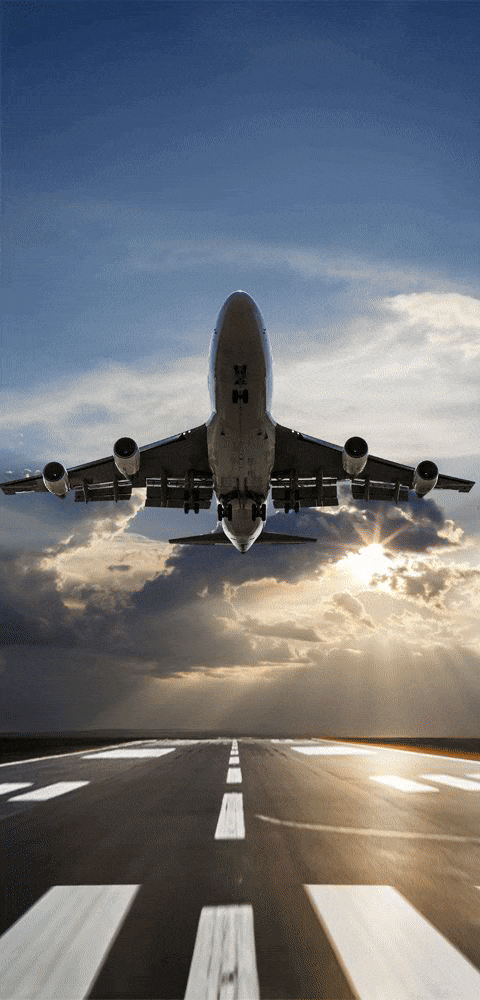
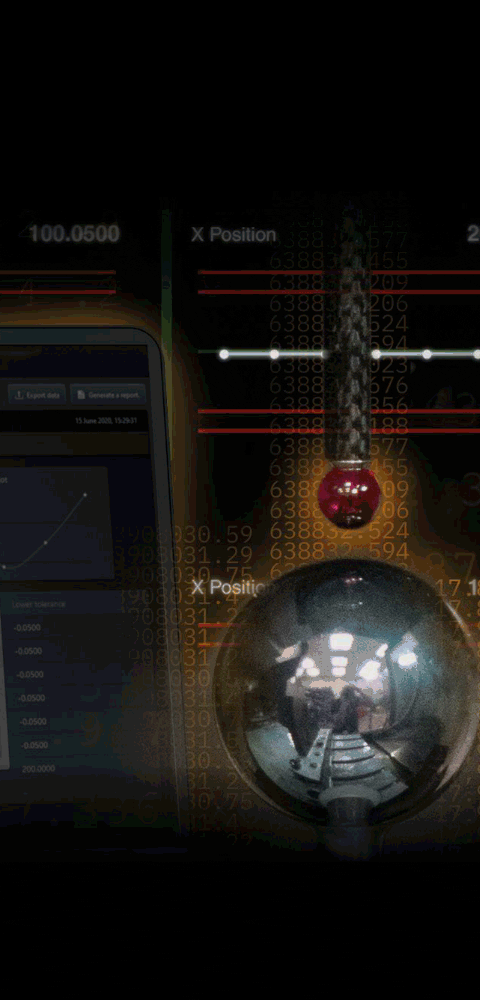
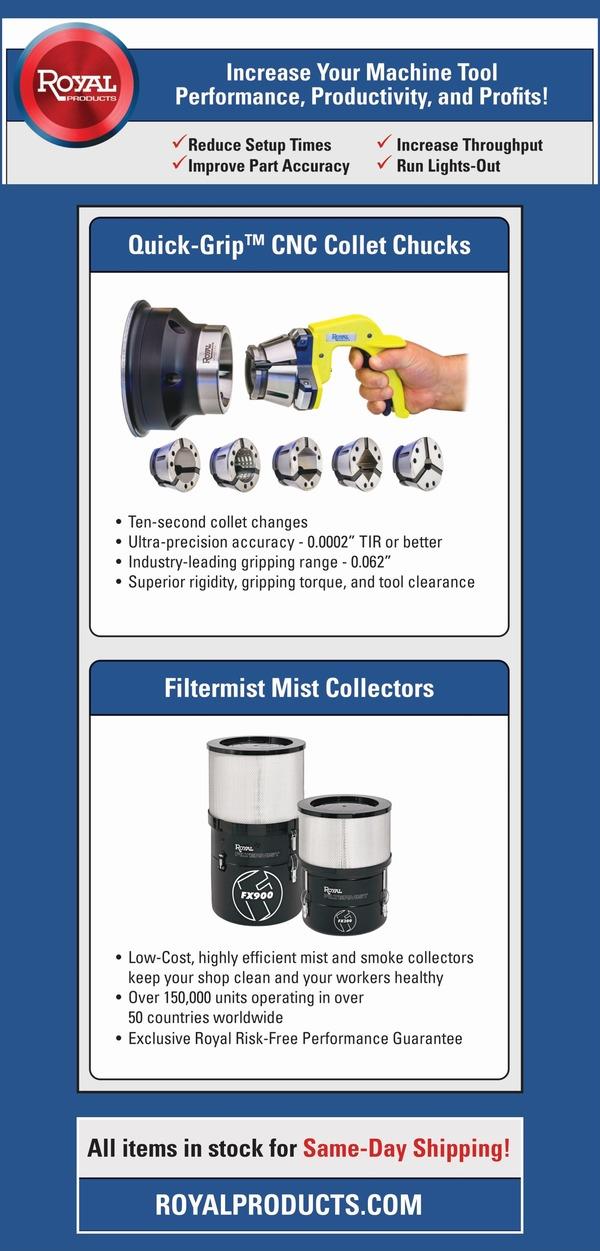
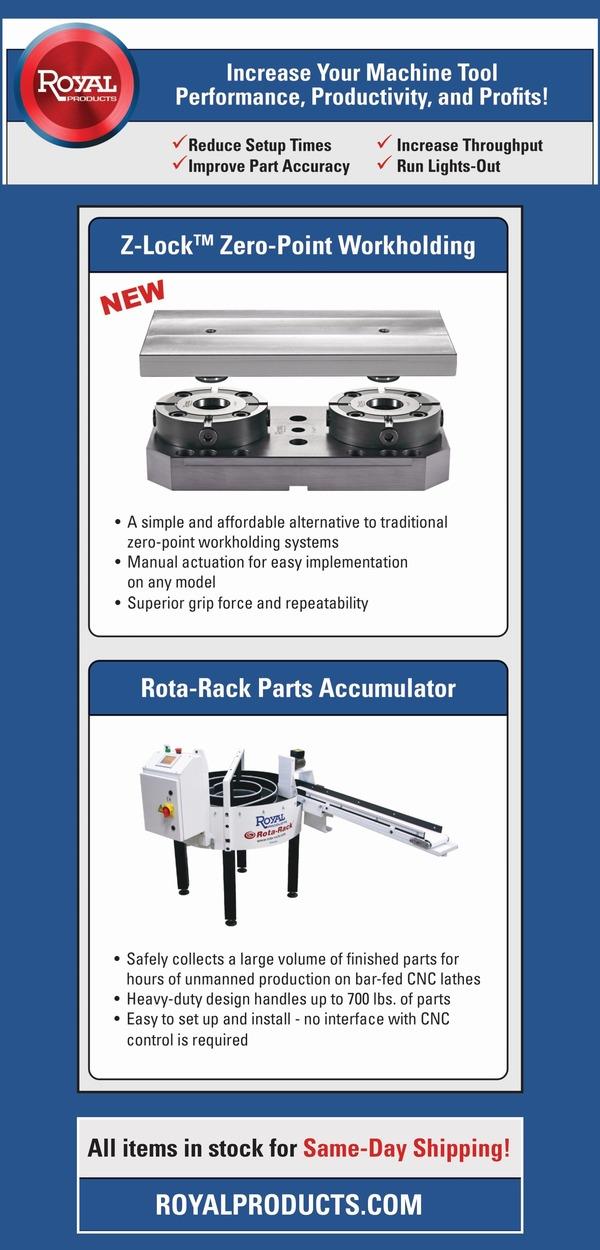
New Lightweighting Innovation Projects
December 1, 2018
LIFT - Lightweight Innovations For Tomorrow, a Manufacturing USA institute, has launched its third round of technology projects.
This round of projects will total more than $6.5 million in combined federal and industry investment to enable a number of critical lightweight solutions.
"We are very pleased to launch these new projects with our partners to invigorate new innovation in lightweighting," said Nigel Francis, CEO and Executive Director, LIFT. "At any moment in time, there are nearly 600 industry and academic experts working on LIFT-related projects to revolutionize lightweight manufacturing here in the U.S., and these projects are an example of that work."
The new round of projects and partners involved include:
- High-temperature gas forming and simulation - Led by GKN Aerospace, along with other industry members Interlaken and American Axle and research partners Notre Dame, University of Michigan and EWI, this $1.87 million project will develop hot metal gas forming technology and predictive analytical modeling capability, with the goal of improving dimensional accuracy and mechanical properties of complex lightweight formed components. The predictive models resulting from this project will also enable systemic improvements in the overall design process, expected to reduce production costs by decreasing tooling development time and the number of iterations needed to produce an acceptable production part.
- Systems approach for evaluation, selection and implementation of chromate-free coating systems for aluminum alloys: Led by United Technologies, along with industry partners Lockheed Martin, Boeing and Materion and research partners Michigan State University and the Ohio State University, this $900,000 project will develop an alternative to coatings relying on hexavalent chrome for corrosion resistance of selected aluminum alloys. This environmentally friendly approach will expand the use of lightweight materials. The technology for this project relates to the understanding and methodology for assessment of undesirable interactions and early-onset corrosion of selected aluminum substrates for several "non-hexavalent chromium" coating chemistries and combined systems.
- Knowledge based automated assembly of complex structures: Led by GKN Aerospace, along with industry members United Technologies, Lockheed Martin and Comau and research partners Notre Dame and EWI, this $1.45 million project will demonstrate the ability to automatically weld complex thin sheet metal structures. To date, automated welding of complex sheet metal shapes has proven extremely difficult. This project will develop a fully automatic robotic gas tungsten arc welding capability where the weld parameters can be continuously adjusted along the length of the joint to accommodate suboptimum and variable fit-up.
- Friction stir welding (FSW) of complex structures: Led by Boeing, with industry members GKN Aerospace and MTI along with research partners EWI, University of North Texas and PNNL, this $881,00 project will advance the FSW process for hermetically sealed joints, offering the opportunity to replace vacuum brazing or use of sealants and adhesives. The project will deliver optimal processing methods and test data of components in butt, lap and integrated butt-lap configurations. The project will provide a database of mechanical properties of FSW specific to sealed joints that can be used by designers on future applications.
- Friction stir welding of dissimilar and complex aluminum-based materials: Led by Boeing, with industry partners GKN Aerospace and Materion and research partners University of Michigan, University of North Texas, Case Western Reserve University and EWI, this $1.44 million project will expand the use of friction stir welding to advanced metal matrix aluminum composites. The team will utilize experimental validation of modeling results with subsequent optimization of both tool geometries and processing conditions. Those results will be used to establish recommended practices for these material/geometry combinations. The approach will be validated on a demonstrator application.
For more information contact:
LIFT
1400 Rosa Parks Blvd.
Detroit, MI 48216
313-309-9003
www.lift.technology
< back