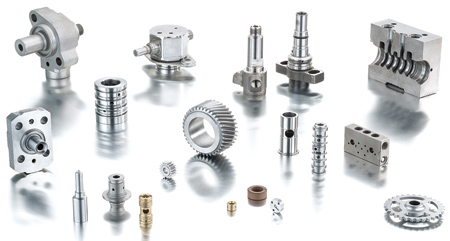
Typical parts for the E line: injection pumps, gear wheels, hydraulic components, turbochargers, small precision parts and aviation components.
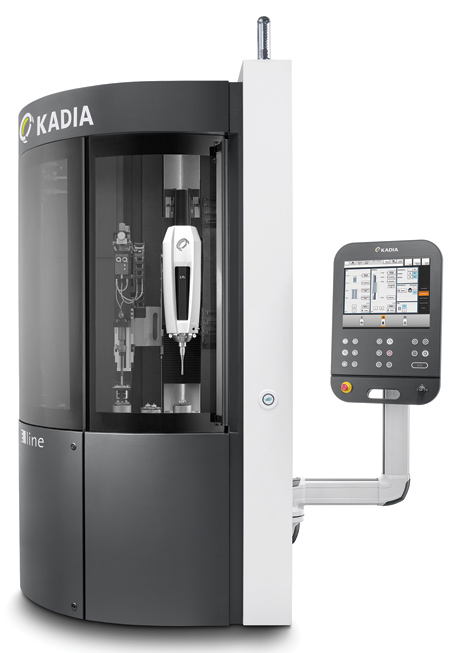
The E line is a compact honing machine that takes up just 2.5 sq. m of space.
"Manufacturing companies that produce highly precise bores in small to medium batch sizes often hesitate to invest in their own precision honing machine," said a KADIA spokesperson. "The rate of utilization is simply too low. Such manufacturers might use a simpler machine that is less costly but often does not work precisely enough."
With its single-spindle Eco Honing Machine, KADIA now seeks to meet the needs of exactly these and similar user groups. The E line, as it is called, is engineered to be an ideal solution for entry into high-precision honing. In the event that production quantities rise, the machine concept offers options for series production.
"The single-spindle E line is a cost-effective, productive honing solution for the highest precision. With this machine we are rounding off our spectrum in the smaller range," said Executive Director Henning Klein. The machine is also compact and requires just 2.5 sq. m of floor space. The control cabinet is integrated into the side and all the components that require regular maintenance are easily accessible.
Up to now, the company has developed mostly multi-spindle machines for use in large series production, especially by automotive manufacturers and large suppliers. "The E line is aimed on one hand at these current customers, especially at prototype developers," Klein said. "We see the second user group as manufacturing companies that want to either produce small volumes especially flexibly or produce in series economically, all in the high-precision range."
Such companies then have two options: they either handle the honing themselves or they hand off the demanding precision work to external service providers. The latter lends itself well when the company does not view honing as one of its own core competencies but would still like to accept orders from customers with highly precise requirements for boring quality. Professional honing providers can carry out such tasks quickly and reliably.
"The new E line is the ideal alternative, especially when honing is a central part of the company's manufacturing competence and highly economical and precise work is important," said Klein. "The special entry-level features and the quality of output are not mutually exclusive, since the same components that KADIA uses in other types of machines ensure that the end quality is correct down to the micron: a highly dynamic, lean, high-speed honing spindle and intuitive high-performance control. Therefore, the E line is on the same level as our larger machines when it comes to quality."
KADIA also offers its second-generation LH spindles, the LH2 and LH3. The update includes a range of further developments that take into account current technology. The somewhat smaller LH2, with a material removal rate of up to 18 cubic mm/sec., performs its work in the eco machine. "It stands out due to its ultra-precise run-out and its highly dynamic nature," said the spokesperson. Inside, modern direct drives provide the rotation and strokes.
KADIA also offers the HMC100, a machine control system of its own development that is specifically tailored to honing. The control system features the newest technologies and measuring techniques and visually presents all processes on a large 19" panel. KADIA design engineers now integrate the HMC100 into all of their honing machines.
The two key components, the honing spindle and the honing control system, are important parts of the Smart Dynamic honing technology. "This is a concept that connects with Smart Manufacturing and follows the motto 'Less complexity. More efficiency,'" said Klein.
Like all KADIA honing machines, the E line is also available in a variety of configurations. In its basic configuration, the machine contains a fixed table; for prototype parts and small batches this is often sufficient. The option of installing a rotary table with multiple stations, usually honing, measuring and loading stations, is also possible. "Users have the option of integrating a handling system for automatic placement," said Klein. "This provides a productive honing solution for medium to large batches."
Depending on the number of units being produced, the provision of coolant may come into play. As a compact solution, an integrated coolant and extraction system is available to E line operators. This will almost always be sufficient for prototype or small batch production. For larger production volumes and fully automatic operation, an external coolant system may be advisable.
For more information contact:
KADIA Inc.
8070 Kensington Ct.
Brighton, MI 48116
248-446-1970
info@kadiausa.com
www.kadiausa.com