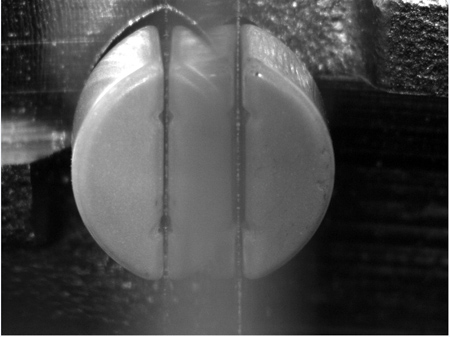
An example of a good part: the pivot point is whole on both sides of the plate.
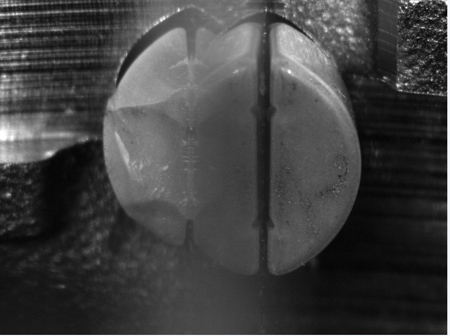
The left side of the pin is broken.

The right side of the pin is broken.
With so many parts required to make the average automobile run, even the slightest defect can cause a dangerous situation. That is why numerous suppliers and automakers have implemented machine vision for 100% quality inspection.
A supplier of automotive exhaust system components realized the need for such inspection when an end customer reported that some parts were flawed upon delivery. The supplier did not have a process in place to detect defects on the part in question - a butterfly valve - so the company reached out to Neff Group Distributors to develop a machine vision inspection system that verified not only the integrity of the valve but also its proper assembly prior to shipment.
Because the part inspection took place in a space-constrained workstation, Neff designed a compact, all-inclusive machine vision system. The company selected a Cognex In-Sight 7200 smart camera equipped with PatMax pattern detection, as well as two LM45 lights from the Smart Vision Lights Mini-Lini product family.
At one end of the butterfly valve is the point where the rotating closure plate, or vane, pivots. That pivot point is critical to the function of the valve. A misshapen, broken or otherwise damaged pivot can hinder the valve's operation.
At the inspection station, the valve is manually placed into a fixture, and prior to the final assembly/weld application, the camera and lights are triggered to inspect its internal integrity. The camera and lights sit just above the side of the valve body, looking directly at the pivot point. The closure plate is placed in the completely open position so as not to obscure the pivot point. The two LM45 lights are placed on either side of the closure plate because the plate bisects the image.
The machine vision system uses two Cognex PatMax tools, one on each "half-moon" side of the part. Neff taught the pattern on the full, intact part and set the match percentage high enough to fail any defective parts. Parts that pass inspection are welded and sent on to the next operation. Failed parts are manually removed and placed into a "failed" containment system for future rework.
SVL's Mini Linear lights proved to be the suitable size and brightness for the application, according to Kerry Whitt, Field Application Engineer for Neff Group Distributors. "They are rugged enough for the metalworking environment in which they were installed," Whitt said. "Being able to control them both with one output from the camera made the application much simpler."
For more information contact:
Neff Automation
www.neffautomation.com