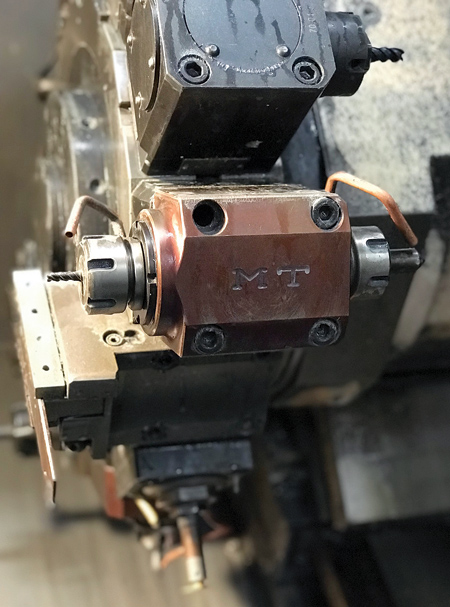
The ability to have two spindles in a single tool position (using a double spindle axial opposite face holder from MD Tooling) allows GMC to mill a small radius slot on the main body of the part. This is done while putting a large chamfer on the thumb side while in the sub-spindle.
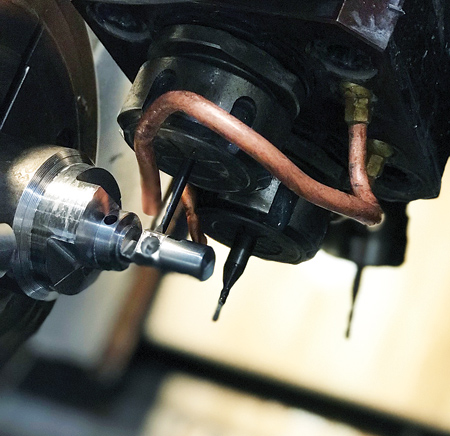
Shown are two sets of double spindle radial holders. One set drills four different holes using two custom made step drills. The other set uses two 1/8 end mills. These end mills rough and finish all slots on the Beretta M9 safety.
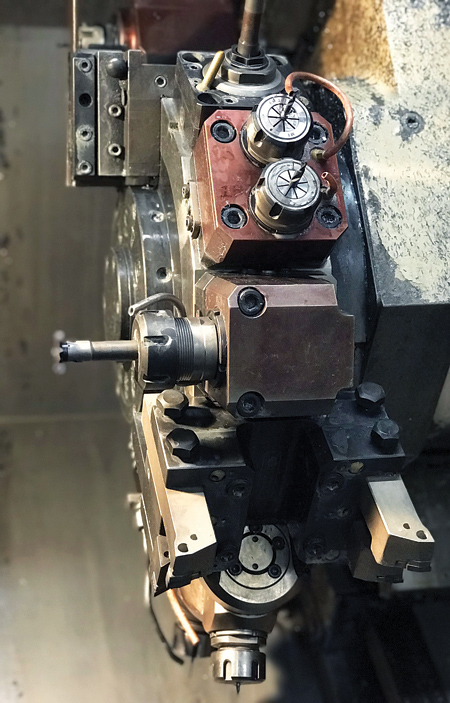
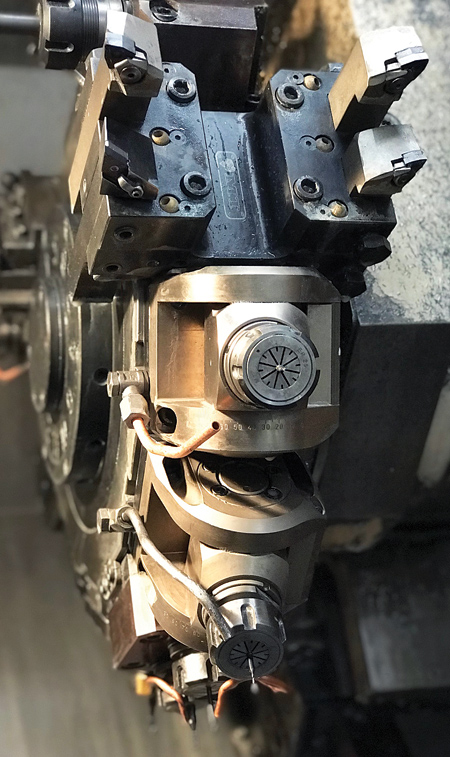
Two 0-180 adjustable holders are used here. The first incorporates a 1/16 end mill that simply creates a flat spot face for the next tool. The next tool is a 1.6 mm diameter drill that drills a through hole on an 8° angle.
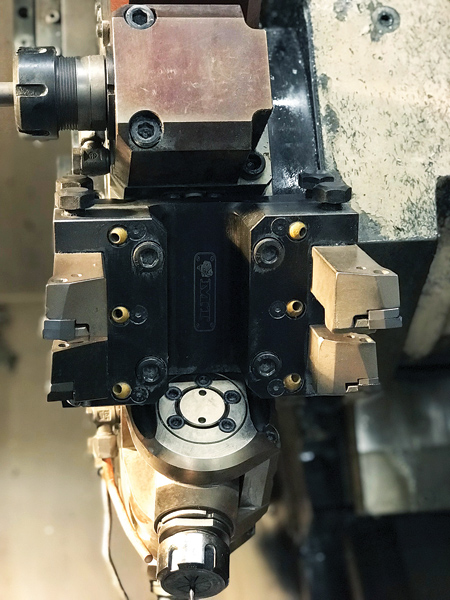
Using the Y-axis of the machine, this quad turning holder houses two roughing holders and two finishing tools. The body diameter of this item is held to a .0002" tolerance. This is done to prevent any distortion during the heat treating process.
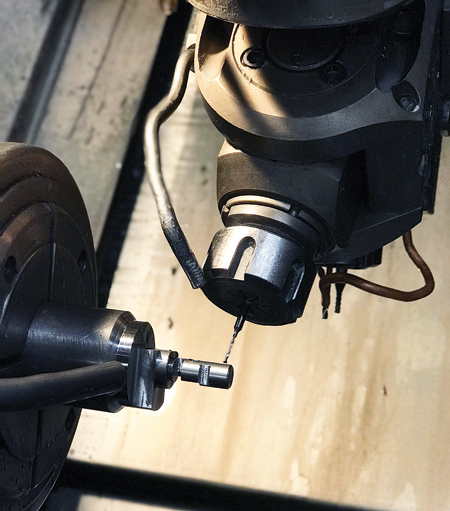
Using the adjustable angle holder from MD Tooling, GMC is able to drill a 1.6 mm diameter hole on an 8° angle.
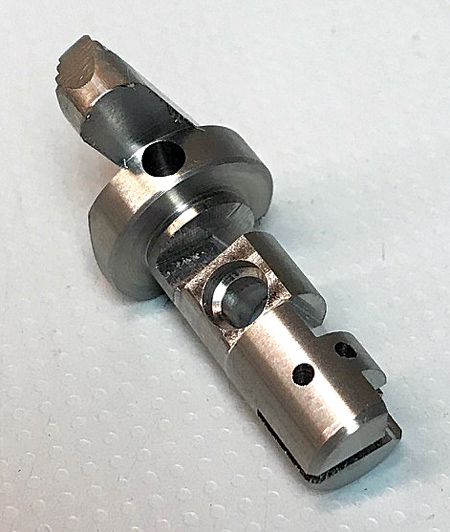
Beretta M9 safety after machining and prior to phosphate process and dry film lube coating.
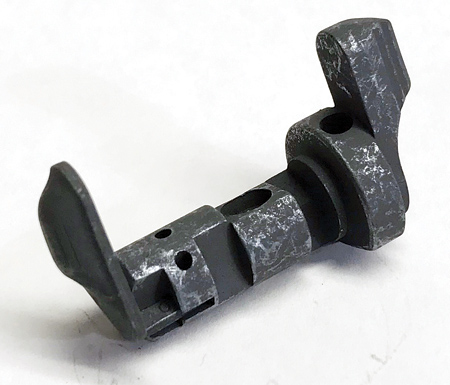
Beretta M9 safety with coating applied, along with the stamping process, which completes the assembly.
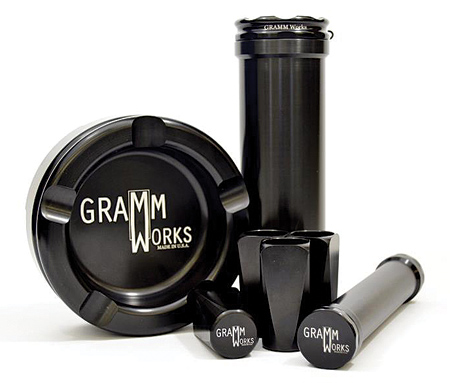
GMC has spawned a second company, GRAMM Works.
"The world of manufacturing is faced with challenges daily: the challenges of acquiring new work, increasing productivity or just trying to complete current work," said Mike Fastuca, General Manufacturing Company (GMC).
As a U.S. Department of Defense (DOD) contractor, GMC is faced with the challenges of manufacturing products better, less expensively and, most importantly to the government, faster.
This was the case several years ago when GMC was contacted by the government asking for help on several items that were considered "problem items." These were items that had reached the Top 5 back ordered items in the supply chain status. When an item in the supply chain reaches this level of need, it directly affects the end user, the warfighter, servicemen and servicewomen.
Each item presented to GMC had its own special challenges, from complexity to the time frame in which they were needed to be delivered to depot. One of the items on this short list was the safety for the Beretta M9 service pistol.
"This part is not very large or even overly complex, but there is a lot going on inside a small envelope," said Fastuca. "For example, there are holes drilled on an 8° angle, turned diameters held within a .0002 inch tolerance, slot locations and widths with very tight tolerances and true positions that are mind blowing. This item has a little bit of everything and requires both turning and milling work."
The print called for the use of either a casting or bar stock. "Just by looking at this item, our GMC team could tell that manufacturing it from a casting would be a nightmare, with several different operations needed for completion," said Fastuca. "As a company that loves to think out of the box with nearly every project, we accepted this challenge and began outlining the process."
With the challenge of manufacturing the safety in a large volume now in front of them, the GMC milling programmer and lathe programmer got together and decided that this item was best fit for one of their multi-axis Doosan turning centers. Going in this direction again opened up a new challenge because their lathes do not have articulating machining heads, and only have 12 tool locations on the turret. It was calculated that they would need to use at least 19 tools to complete this part in one smooth operation.
One company came to mind when in search of live tooling holders with multiple spindles: MD Tooling. MD Tooling, the exclusive importer of M.T. Marchetti tooling, is a supplier of precision live and static tooling for standard CNC lathes and multitasking turning centers that help improve productivity. It offers an extensive line of standard live tooling, as well as innovative specialty toolholders such as 0-90 and 0-180 adjustable angle toolholders, gear hobbers, slotting tools and even worm gear generators.
"We have been using MD Tooling's holders for several years in the manufacturing of small arms items and mortar mount items in our lathes," said Fastuca. "We knew that the products they offer would be the correct choice for this new part."
Having lathes equipped with a Y-axis allowed the team to utilize live toolholders with multiple spindles. These tools' spindle center line is roughly 1" in both the positive and negative direction in the Y-axis, which gave GMC the total travels needed to machine the slots and drill the holes. Once the lathe department decided how many live spindles and other holders would be needed, they placed the order for the new holders. "When the holders arrived, it was like Christmas morning," said Fastuca.
Not all of the challenges with this part stopped when the new orders were received, however. There was still the issue of making the part quickly and efficiently, and being able to run lights-out without producing scrap parts. Using live toolholders, both radial and axial, allowed for the use of redundant tools to be put into the program to capture any tool wear from one tool to the next. "With the simple addition of tool checks or broken tool detection to the program, we were off and running," said Fastuca.
Fastuca continued, "That was three years and 20,000 pieces ago, and the parts are still running strong today on our dedicated Doosan lathe, and will be running through FYI 19 to fulfill the current needs of our U.S. warfighter."
Family-owned General Manufacturing Company was founded in 1958 to produce items for steel mills in Pittsburgh, PA. Adapting to changing times, GMC has evolved from supporting Pittsburgh's original industries to supporting the U.S. as a Federal Contractor to the DOD. It has provided the Army, Navy and Air Force with high quality precision products, including replacement parts, kits, subassemblies and artillery mechanisms.
GMC continually invests in new machining capabilities and technology. It has even spawned off another company, GRAMM Works, that designs and brings to market a travel humidor that is 100% American made, from materials to coating. The same machinery, tooling and quality control used for its U.S. DOD products is used in GRAMM Works products, which sets the company apart.
"Life is full of challenges," said Fastuca. "In the manufacturing world, challenges are a good thing. They help us to grow and learn. Working with companies like MD Tooling helps us to successfully meet those challenges."
For more information contact:
General Manufacturing Company
3249 Industrial Blvd.
P.O. Box 115
Bethel Park, PA 15102
412-833-4300
generalmfgco@aol.com
www.generalmfg.net
MD Tooling
10139 Bergin Road
Howell, Michigan 48843
info@mdtooling.com
877-91-TOOLS / 810-632-4446
info@mdtooling.com
www.mdtooling.com