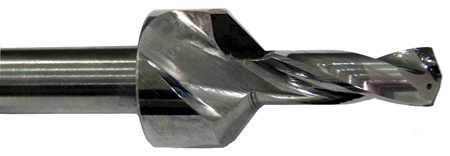
PCD Countersink Drill
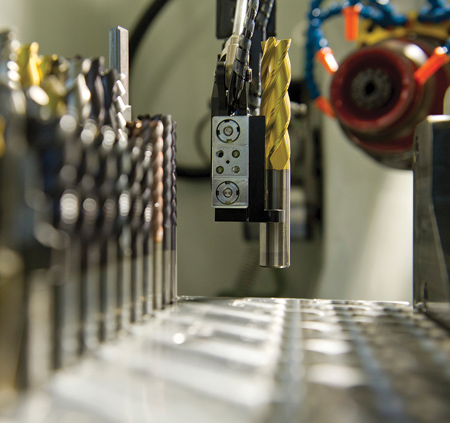
FastLoad on ANCA EDGe
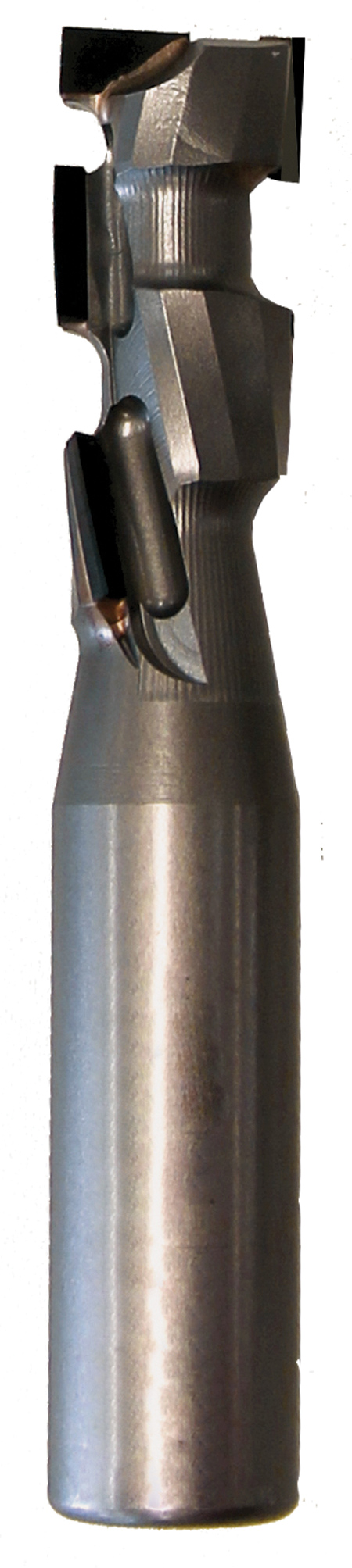
PCD Compression Router 1
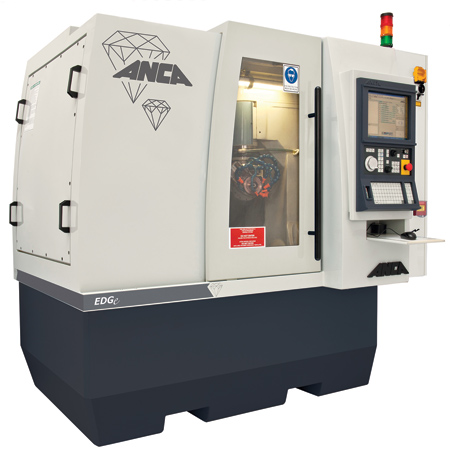
ANCA's EDGe-Spark Erosion Power Generator controls the energy level of the eroding spark for optimum surface finish, material removal and cycle time. It also enables a double-ended HSK wheel spindle for eroding PCD and grinding carbide and HSS.
According to ANCA, the ability to manufacture a variety of tools (up to 220 mm or 8.66" in diameter and up to 20 kg or 44 lbs. in weight) makes the EDGe suitable for users looking to reduce the risk associated with moving into the growing PCD-side of the tool grinding business and is suitable for a wide variety of tools and applications.
Another advantage of the EDGe is that it performs erosion and grinding operations on the one machine, which reduces machine set-up time. It is designed to improve tool accuracy due to a single set-up, and fewer machines required.
Duncan Thompson, EDGe Product Manager, ANCA, said, "The proprietary EDGe-Spark generator monitors and controls the energy level of every spark for the resistivity of the substrate, be it tungsten carbide, diamond or cobalt binder. It automatically detects the substrate and adaptively adjusts the gap distance for optimum surface finish, material removal and cycle time."
"Testing of tools eroded on the EDGe machine resulted with better figures for cutting force, exit burrs on CFRP and drill life than ground tools achieving a surface finish on tools of less than 0.2 microns Ra," said a company spokesperson.
ANCA, known for its ToolRoom design software, reported that the EDGe has a fast, easy-to-use interface for inputting tool geometry. The ANCA software includes integrated 3-D graphics, is used to adjust power generator settings and is designed to create programs for a wide range of tool types. ANCA's tool design software provides flexibility and user-friendliness for a wide range of tool types and applications for both erosion and grinding. In addition, ANCA can include its LaserPlus in-process tool measuring system to support accurate manufacture of PCD cutting tools.
"The process to manufacture a PCD tool is relatively unchanged: wire EDM the PCD segment to size and shape, pocket grind the tool body so the PCD segment can be located on the tool and braze the PCD segment to the tool body. The final stages of the PCD tool production can traditionally involve multiple machines to complete the tool to the finished requirement. The ANCA EDGe is ideal for the final stages of PCD tool production, resulting in an eroded finish with a surface roughness less than 0.2 microns Ra. Depending upon the surface roughness requirements and whether an eroded or ground surface is required, the EDGe machine can eliminate some of the grinding operations," said the spokesperson.
ANCA partnered with Precorp, a U.S. manufacturer of PCD cutting tools and a key supplier to companies such as Boeing, to develop the technology. "This partnership means the EDGe is perfect for grinding PCD tools that are essential for machining composite materials often used in aerospace application," said the spokesperson.
For more information contact:
ANCA Inc.
31129 Century Drive
Wixom, MI 48393
248-926-4466
usainfo@anca.com
www.anca.com