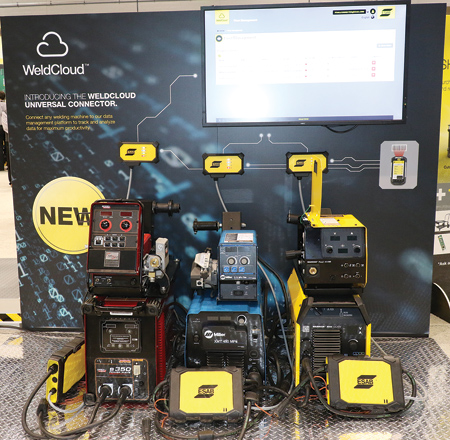
FABTECH 2017 witnessed the introduction of universal connectivity modules that connect any welding machine to a data management platform, regardless of make, model or year.
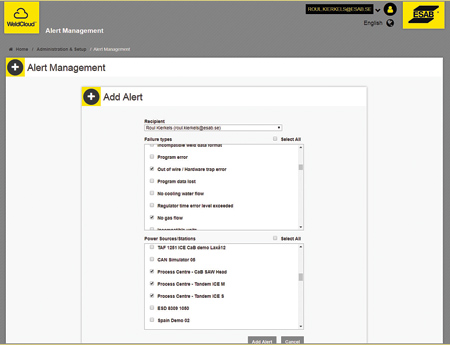
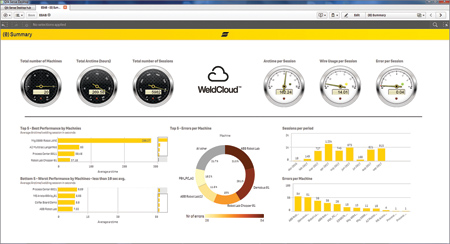

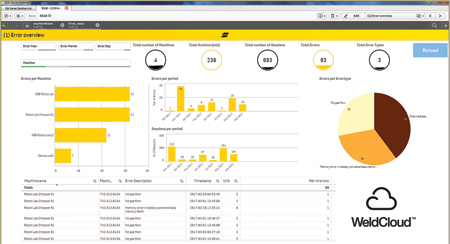
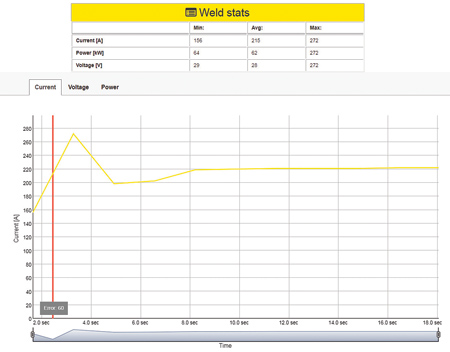
Visitors attend the annual FABTECH Expo in search of innovations that improve productivity. Historically, advancements came from welding processes that increased welding speed and consumables that reduced cleaning and rework. Now and in the future, the biggest technologies breakthroughs will most likely come from software and hardware that enables connectivity and apps for smart devices that give users a data-driven advantage.
Data gathering starts with connectivity, such as through WiFi, Ethernet or Bluetooth technology. Most of the major welding and cutting equipment suppliers demonstrated power sources with built-in connectivity, typically for their advanced equipment. The good news from FABTECH 2017 is that add-on communication modules are now available for use with any welding power source of any age, a great benefit to managers of older fleets.
By connecting to the positive and negative welding terminals, these universal connectivity modules enable the reading of amps, volts, arc-on time and the number of starts and stops. Even such basic data creates a direct line to productivity when paired with dashboards or apps that show:
- Operator productivity and the ability to show how an operator compares to others within a particular division or the entire enterprise.
- Weld procedure compliance/non-compliance. The ability to identify operators that need additional training can eliminate the root cause of rework. As an example, consistently high voltage levels may indicate that the operator holds the gun too far from the joint.
- Welding parameter documentation adds a layer of traceability to welds by logging relevant parameters.
Universal connectivity modules also enable capturing and communicating ancillary information associated with the power source when connected to another FABTECH 2017 product preview: a smart scanner app. By installing the smart scanner app on a smart device, it can scan bar codes associated with the power source, operator, parts, gas cylinder and filler metal. After scanning, the app pushes the information to the module so that data stays paired with the welding power source. In the future, the app could enable the operator to confirm proper consumables, or more likely, create an alert for use of the wrong consumable, a common source of errors.
The smart scanner app does not require cloud access, benefitting situations where the power sources and connectivity modules are located inside a ship, tank, underground or other locations prohibitive to WiFi communication. ESAB envisions smart scanners as one tool that will soon revolutionize supply chain management by removing tedious (and error-prone) manual work. Traditionally, manufacturers relied on personal relationships with suppliers, especially for commodities. By becoming an early adaptor of smart technologies, suppliers can add real value while differentiating themselves.
Automated consumables replenishment is the low-hanging fruit, but analyzing consumable use takes service a step further. For example, a supplier or a maintenance manager could notice that one system uses more MIG welding tips and MIG gun liners compared to others. They could then examine the system. The cause might be as simple as the operator over-tensioning drive rolls, deforming a Flux-Cored wire and generating excess wire shavings.
Everywhere an App
Look for new apps within the welding data management software as a key resource for continuous improvement. Basic apps, such as those for weld parameter settings, have been available for a few years, as have those for heat input and interpass temperatures, carbon equivalent, weld terminology, symbols, scheduling and more. These apps do not depend on connectivity. As manufacturers and fabricators recognize the value of connecting, and especially with the ability to connect any power source, app availability and use will increase greatly in the future.
A current source of app development comes from the ability of open-source online data management systems to connect to existing enterprise software reporting tools, such as ClickView, Qlik, SAS and Tableau and Microsoft's Power BI. Rather than re-invent new dashboards, select welding data management systems enable users to perform familiar analyses and data drill downs by allowing these tools to directly but securely connect to the customer's welding database. Further, users can create customized dashboards with drag-and-drop simplicity. Want to combine a welding productivity matrix with gas usage at all plants? No problem. Thus, different constituencies can focus on only the data relevant to their needs. Further, all the data being used comes from within a company's own database, secured by its firewall. Now it is just accessible via users' preferred smart device, often a mobile phone in the case of maintenance, sales, service and field personnel.
Authored by Roul Kierkels, Global Product Manager DDA & WeldCloud, ESAB Welding & Cutting Products.
For more information contact:
ESAB Welding & Cutting Products
256 Midway Drive
Union, SC 29379
800-ESAB-123 / 864-466-0921
www.esabna.com