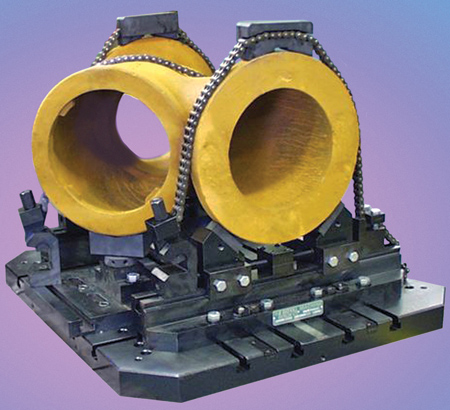
Large three flange valve body gripped on a special chain fixture over each flange area being modified.
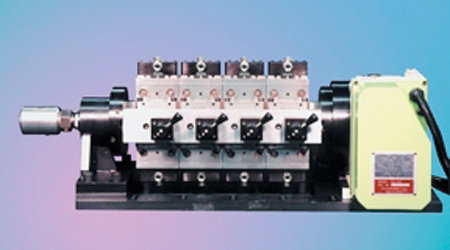
trunnion fixture
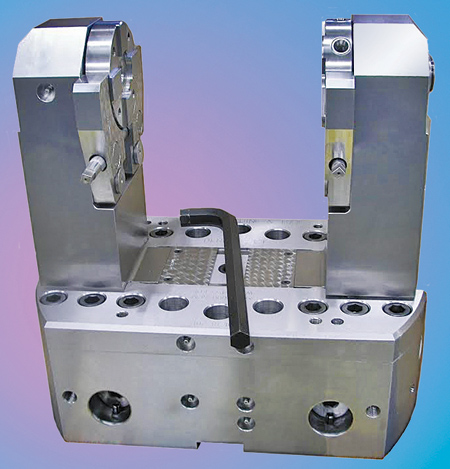
manual index chuck 801
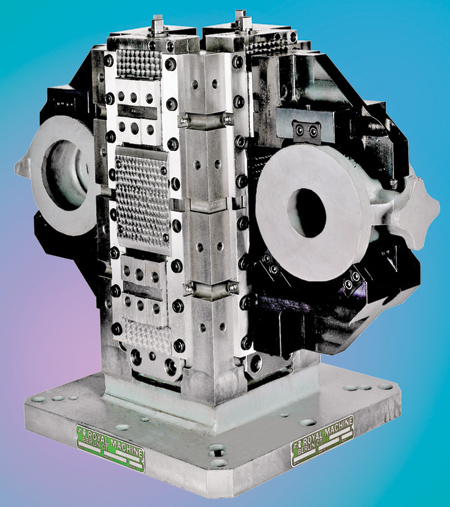
vertical vise
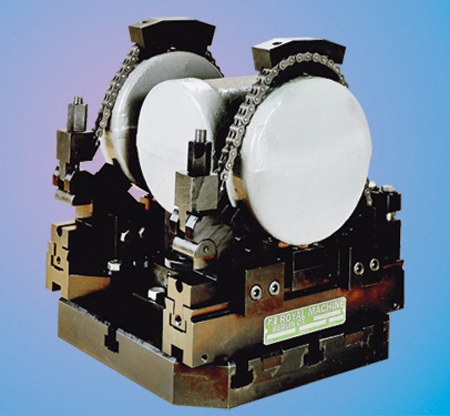
modular chain fixture
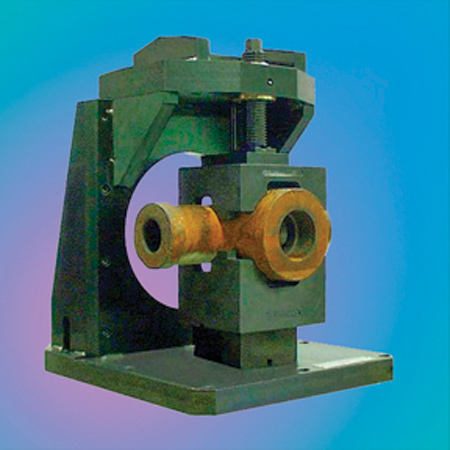
C-frame fixture
Flow control valves are available in various sizes and shapes and are probably the most diverse of any manufactured product. Available sizes range from a 1/8" up to 10' diameter and can take on various shapes such as a tee, cross tee, elbow, lateral or wye or simply a straight diameter.
When selecting the correct workholding device for a flow control valve, this same diversity also holds true because there are various workholding methods used today. Selecting the proper method can be determined based on many variables to the application, such as: the volume being produced, the changeover requirements, the size and configuration of the valve and the families of parts or just a single part.
Smaller Valve Bodies
Higher volume small valve bodies are usually done on automatic index chucks, reducing load/unload times, improving repeatability and reducing downtime. Also, the valves can be run on a machining center with a number of them stacked on a trunnion or tombstone, thus freeing up the operator to load/unload parts while the machine is running.
Lower volume valves in the small valve category are usually done, as mentioned earlier, on single jaw, anvil type, manual index chucks or 2 jaw or 2/3 jaw chucks. Changeover is not as critical, and a variety of parts can be machined on the same chuck by simply changing the top jaws. The machining process may require a number of operations since all machined areas are not accessible to be machined in these types of set-ups, other than an index chuck.
Another method is to grip the valves in a 2-jaw vertical vise situated on all four sides of a tombstone, which allows access to three sides of the valve for machining.
Large Valve Bodies
These bodies usually have a much smaller volume and are done mostly on machining centers. One of the biggest issues is in the handling, which usually requires an overhead crane or some type of load assist device. In some cases index chucks are used on turning centers, which reduces the handling between operations, which could be timely and cumbersome. Because of the large mass, the spindle RPM is sometimes limited as well.
Another means of clamping on machining centers is chain fixtures, which offer great latitude in gripping diameters and easy access to all the machining areas in a single set-up. The chain provides a complete wrap-around gripping area. Another option is using a strap clamp arrangement in lieu of the chain. This may be sufficient in most cases, but does not give the most gripping area that a chain would give.
Another approach is to use a C-frame fixture concept, where similar to the chain fixture, the part sits in a work nest. Instead of a chain clamp there is a top clamp configured to the contour of the part. The C-frame also allows complete access to all the machining areas.
In addition to being found in manufacturing facilities, oil rigs, treatment facilities and industrial equipment, flow control valves can be found almost everywhere including households, large buildings and shipping vessels, to name a few. They come in a variety of shapes and sizes made of castings, forgings, investment casting and even plastics. The workholding described above only scratches the surface of the methods to hold these parts for machining.
Authored by Albert Tessman, Manufacturing Engineer, Royal Machine & Tool Corp.
For more information contact:
Lynn Lozinski
Royal Machine & Tool Corp.
P.O. Box Y
4 Willow Brook Drive
Berlin, CT 06037
860-828-6555
lynnl@royalworkholding.com
www.royalworkholding.com