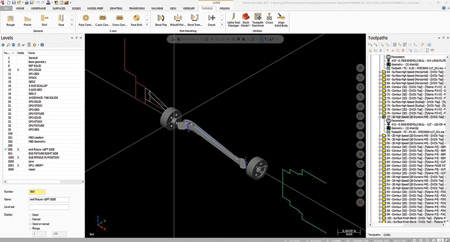
"Dynamic toolpaths give us constant radial engagement," said lead programmer Jesse Simmons. "Every time the tool goes into a corner, instead of plowing, it starts to loop. I no longer have to worry about setting my feedrate so that it does not blow up in the corners. Because the engagement is constant, I can use the chip thinning factor to reduce stepovers and increase speeds. With this approach to tool life, in many cases, cycles have improved by 50% or more."
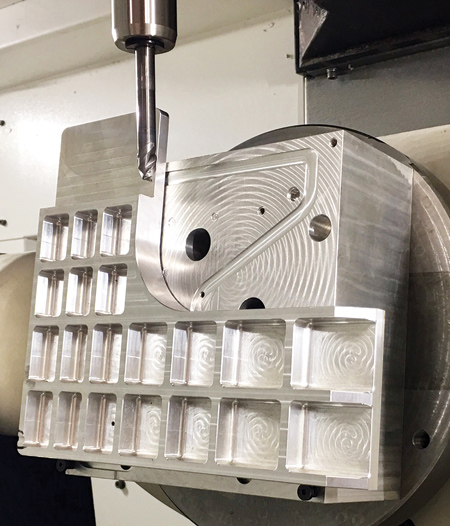
The CAM system is the backbone of scrap-free manufacturing strategies. It is the digital environment where 95% of the work is accomplished before the workpiece is set up on the machine. Parts, such as this aluminum drone part for the missile defense industry, are programmed into the CAM software and machined on a series of 3-D and 4-axis mills, high speed mills, a 5-axis machining center and a pallet loading HMC.
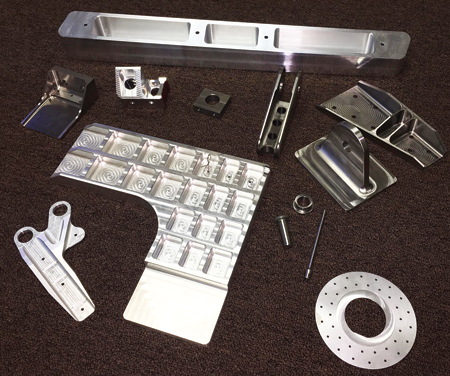
Verisurf, a module integrated within Mastercam, is used to visually analyze MBD data and determine how to machine difficult part dimensions and meet difficult dimensional requirements. Simmons says Verisurf is particularly useful for aligning hole axes and analyzing the thickness of walls coming in at odd angles.
When the automotive market was in the doldrums in 2012, Jake Brackett left the job shop where he had been working for more than a decade and started his own parts manufacturing business. His big idea was to tap into what appeared to be a substantial amount of aerospace manufacturing that was being lured into the Carolinas.
Brackett established a business plan and leveraged everything he owned to obtain a $250,000 loan that enabled his start-up to acquire a respectable 3-axis mill, a lathe and a computer system equipped with seats of SolidWorks and Mastercam (from CNC Software, Inc.). He launched Jacob Grey, Inc. with himself and two others as employees. Brackett began taking on projects making perishable tools (jigs and fixtures) for OEMs and small parts subcontracted from second and third tier aerospace suppliers.
Jacob Grey, Inc. was working its way up from the bottom of the supply chain. This did not come as a surprise to Brackett; he knew from consulting with his Mastercam reseller (Jimmy Wakeford of Barefoot CNC) and other trusted suppliers that aerospace assignments came as the result of the job shop's demonstrated merit based on quality and on-time deliveries. Over time, good work would be rewarded with additional assignments involving greater manufacturing complexity, unforgiving materials and tighter delivery schedules.
While Jacob Grey, Inc. was cutting its teeth making tooling for a wide spectrum of companies in South Carolina, Brackett was working with Wakeford's guidance to develop robust manufacturing processes capable of a much higher level of manufacturing complexity within his CAD/CAM software.
Breaking Through
This preparation led to the first major aerospace opportunity later in 2012, when Brackett met with a representative of a very large aircraft OEM and was given the opportunity to manufacture a number of small parts. That went so well that the local contact thought of Jacob Grey when an emergency arose that would cause the OEM to shut down a production operation unless a critical part were delivered over the weekend.
Brackett explained: "Our customer said they needed it by Sunday night and this was Friday afternoon. I got my guys together and told them what was needed and we agreed to do it on time. I did not think it was a difficult part for us, but it did have some complex features and tight tolerances. It also had to be cut from a large aluminum billet with a machining process that would relieve all of the stresses. We modeled the part in SolidWorks, analyzed it and used Mastercam to program the part and develop our workholding solutions. This was all done in just 12 hours. Then we went straight into set-up and machining. In all, we worked 48 hours straight and delivered the project on time."
Two weeks later, Brackett got a call from one of the OEM's supplier analysts. They were impressed by his company's crunch time performance. The OEM was willing to give Jacob Grey, Inc. more business if it could meet stringent aerospace model based definition (MBD) requirements. This took about six months and Jacob Grey, Inc. was set up as a secondary emergent offloading (EO) supplier and given a three-year contract.
"We were off and running," Brackett said. "Once you get inside the door, and you do a good job, OEMs will love you to death."
Jacob Grey, Inc.'s work volume began to increase steadily. So did the size, complexity and tolerances of what was being asked for. "Mastercam could do it, no problem," said Brackett, "but the machines were limited."
As a result, Brackett sold the shop's basic CNC mill and lathe and began acquiring a series of high-end CNC systems, including 3-D and 4-axis mills, high-speed mills, a 5-axis machining center and a pallet loading horizontal machining center (HMC). Four years into its start-up phase, Jacob Grey, Inc. was already knocking down walls and expanding into the next building.
Steadying Influence of CAM
Jacob Grey, Inc. is scrap averse. "Our attitude," said Brackett, "is no scrap parts. We machine 500-1,000 titanium parts a year and a lot are complicated. They cost $5-15,000 each. Our scrap rate is very low. We have had two scrap parts since January out of about 800. We check 100% of our parts. Even if it is 200 pieces, we check each of them completely. With that mind set, when a customer says that there is an issue, we are able to work with our customer and compare data to ensure our paperwork is right, our process is right and all of our SOPs are right. That sets us above some of the other shops as far as performance."
He indicated that the CAM system is the backbone of scrap-free manufacturing strategies. It is the digital environment where 95% of the work is accomplished before the workpiece is set up on the machine. To keep all of the digital work in a single environment he relies on a set of advanced tools that are part of the Mastercam software or that have been purchased from third party suppliers and integrated seamlessly within the CAD/CAM software via Mastercam's C-hook technology.
Lead programmer Jesse Simmons explained that this integration is vitally important because the two programmers are expected to begin programming within a few hours of the part arriving in their queue. He said, "The faster I can get the part programmed, the faster I can machine it. The part will come in, we analyze it, program it and start machining the same day."
These parts, which have been modeled in SolidWorks, are imported directly into Mastercam. A Mold-Plus software module is of use to all of the MBD data associated with the part. This saves a substantial amount of time because it eliminates the need to work back and forth between Mastercam and CATIA to access MBD.
Verisurf, another module integrated within Mastercam, is used to visually analyze MBD data and determine how to machine difficult part dimensions and meet difficult dimensional requirements. Simmons said Verisurf is particularly useful for aligning hole axes and analyzing the thickness of walls coming in at odd angles. Critical process variables identified with Verisurf trigger in-process gauging sessions on the shop floor using the machine's spindle probes.
The programmers also make extensive use of the X-Plus module within Mastercam. This allows them to design standalone set-up sheets for the operator. The operator can use the same sheet to send comments back to the program, where Simmons can take advantage of shop floor experience to further improve the CNC program.
Simmons also cited many features within Mastercam to improve workflow so that parts move from model to machine faster. These include model prep features that help him analyze the part and build workholding solutions faster; simulation to verify the accuracy of toolpaths; machine simulation to detect interferences within 5-axis toolpaths; and 5-axis toolpaths themselves, which Simmons believes have "come a long way" in terms of collision detection and tool control.
Unlocking Productivity
Shortly after Jacob Grey, Inc. acquired its 5-axis machining center, the company brought in a second Mastercam programmer with dedicated aerospace CNC machining experience. In addition to his 5-axis programming expertise, he was very adept at ferreting out "white time" in which the program was not operating as efficiently as it could. He could see that Mastercam was being used very effectively to achieve critical aerospace quality objectives, but as far as productivity was concerned, "it was all locked up." Brackett set his programmers out on a quest to reduce dead time so that machine cycles could be improved and lead times reduced.
A cornerstone of this initiative was to more fully implement Mastercam's Dynamic Motion Technology. Simmons explained that getting more speed is desirable, but it must come at the expense of smoothness, especially when working with materials like titanium. If higher speed means plowing into cuts and banging on the material, then you are introducing too much stress into the part. He said, "These toolpaths give us constant radial engagement. Every time the tool goes into a corner, instead of plowing, it starts to loop. I no longer have to worry about setting my feedrate so that it does not blow up in the corners." Because the engagement is constant, the programmers can use the chip thinning factor to reduce stepovers and increase speeds. With this approach to tool life, in many cases, cycles have improved by 50% or more.
The impact of introducing high-end equipment and systematically improving machining strategies has resulted in lead times that have gone from 15 weeks early in the company's history to four weeks five years later. On-time performance was an important factor in winning an additional 5-year OEM manufacturing contract. Expertise in complex super alloy manufacturing has attracted customers from other industries and has been instrumental in the launch of a successful custom firearms manufacturing business. In just five years, the company has grown from three to 10 employees, including two CAM programmers, and production output has grown more than 10-fold. The company continues to keep up with a steadily increasing flow of work.
For more information contact:
Jacob Grey Precision Machining
125A Queen Parkway
West Columbia, SC 29169
803-834-3017
www.jacob-grey.com
Michelle Nemeth
CNC Software, Inc.
671 Old Post Road
Tolland, CT 06084
info@mastercam.com
www.mastercam.com
SE ONLY
NC, SC
James Wakeford
Barefoot CNC
333 Sanford Dr.
Morganton, NC 28655
828-438-5038