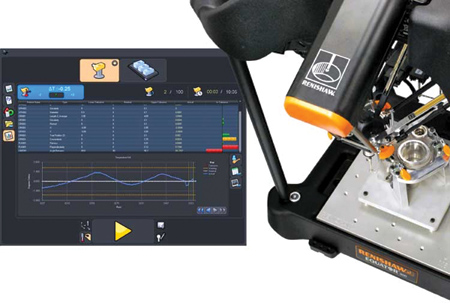
INTUO allows engineers to create simple gauging routines on Equator in minutes, with easy input of master part values. With Equator Button Interface, shop floor operators can start routines with a single button and also control other basic functions.
Renishaw's new INTUO software for the Equator flexible gauge simplifies the creation of programs for automated gauging of a variety of parts. The software uses intelligent functions to allow engineers to set up part programs in a matter of minutes, with minimal training. INTUO features a new Equator Button Interface (EBI) that allows machinists to operate the gauge with gloves or grimy hands, without a mouse and keyboard. The software is standard on new Equators and available as a paid upgrade for existing users.
With INTUO, programmers create gauging routines using only a part with an engineering drawing. When the Feature Predict function is activated, the programmer uses the joystick to take points on each feature while INTUO does most of the work by predicting the type of feature, the nominal value and a possible tolerance band. It is then easy to adjust the program to change the number of points taken or space them evenly, and match nominals and tolerances to the engineering drawing.
Easy Manual Input of Master Part Actuals
It is simple to input the actual values for features on a master part, which does not need to be a perfect part. In fact, it is preferable to use a production part manufactured with the same method and material. First the required features on the master are measured on a certified device, like a calibrated manual gauge or any coordinate measuring machine (CMM). These measurement values can then be manually added to a table in the Organizer software, or to the corresponding field in INTUO - changing one will update the other.
Programmers can be trained to use it in just a few hours with hands-on training, using the joystick to take points while interacting with icon based menus and a graphical workspace to rapidly build up the features to be gauged. Training includes instruction on the four-stage INTUO process of Align - Measure - Dimension - Report.
Equator Button Interface
Customer feedback indicated desire for an alternative to the keyboard and mouse, so Renishaw responded with the EBI, which works directly with the Organizer software. The EBI uses large push buttons that can be operated while wearing gloves, and is not affected by shop floor contamination. It can be mounted on the front of the Equator or on the framework of a table or enclosure. At the most basic level it can be used to start gauging programs, but can also be used to stop those programs mid-cycle, select other programs and navigate the Organizer environment. Equator can be moved using the jog keys if necessary, and there are buttons for initial alignment, switching between master/measure modes, changing view screens and easy error recovery.
Control the Process, Replace Manual Gauges, Reduce Ongoing Costs
"INTUO with Equator is an ideal alternative to multiple manual devices, such as vernier or digital callipers, micrometers and plug gauges," said a company spokesperson. "Automated gauging with the Equator eliminates the inconsistencies of manual gauging and ensures that out-of-tolerance parts are always identified. Equator is fast, automated and highly repeatable, reducing the cost of labor and manual gauges."
Shop floor operators can select and run those programs with the user-friendly Renishaw Organizer front-end software. Equator has various reporting options, including simple pass/fail, a more detailed view in Process Monitor (a process monitoring window for the user interface) or automatic data capture for updating machine tool offsets.
Process Monitor provides a chart showing the history of feature measurements, and an easy graphical view of proportion of tolerance for each feature. "Being able to view the inspection data history of a part is an invaluable function for controlling manufacturing processes. This is not possible when using a go/no-go gauge, which can only indicate the state of each feature," said the spokesperson.
Process Monitor also enables shop floor management of the mastering process according to temperature, time or number of parts measured. Use of a calibrated master part allows the system to be re-zeroed whenever shop floor conditions change, meaning Equator can cope with a rapidly changing thermal environment.
For more information contact:
Renishaw, Inc.
5277 Trillium Blvd.
Hoffman Estates, IL 60192
847-286-9953
usa@renishaw.com
www.renishaw.com