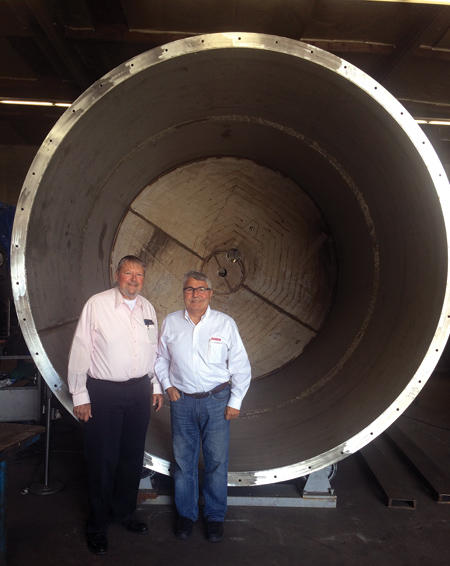
Wallace Cook, General Manager at Royal Welding, and Gary Mergeanian, Regional Sales Manager for Suhner, in front of a typical containment vessel fabricated at Royal. Suhner tools and abrasives are used to finish the job.
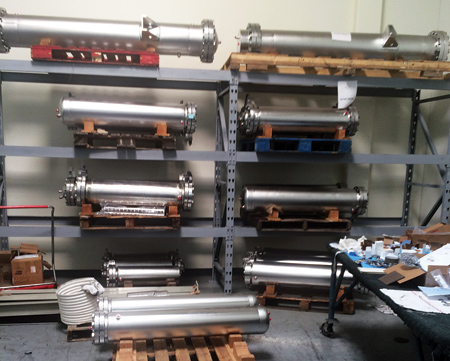
Extractors for the agricultural industry protected in a cleanroom at Royal Welding
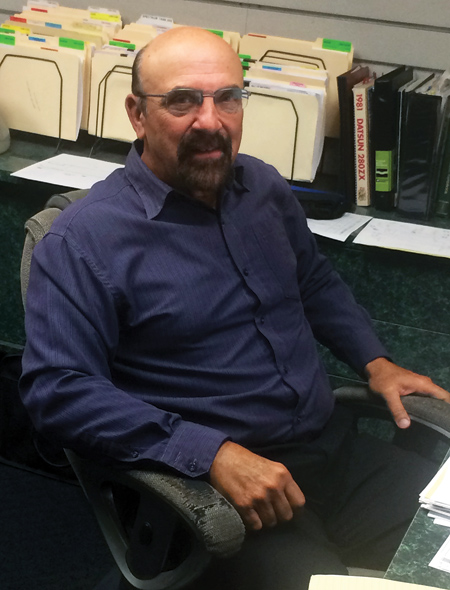
Brad Card, Director of Engineering at Royal Welding, maintains an impressive library of the company's unique fabrication successes.
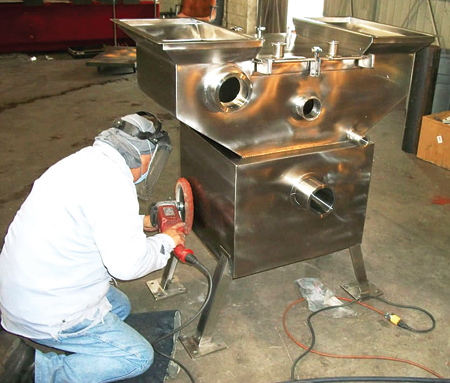
Operators benefit from the external motor drive and flex shaft arrangement of Suhner tools. The weight carried on the job is far lighter, making the work easier.
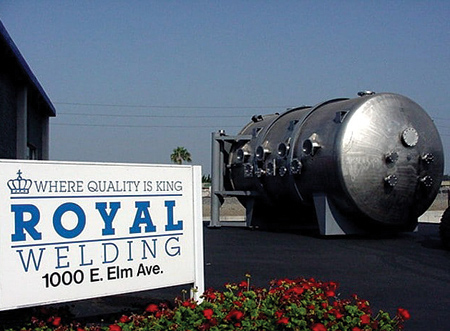
Royal Welding has a nationwide reputation as a fully integrated, high-quality fabricator of pressure vessels, containment vessels, vacuum chambers, high-pressure tanks, storage tanks, reactors and other products, most being custom designs for application-specific uses.
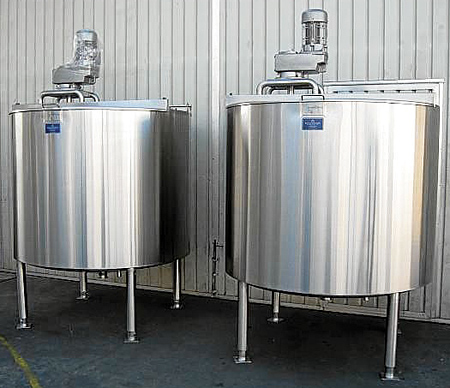
Assortment of the fabrications made at Royal Welding & Fabricating, most of them designed, engineered, produced and fully tested at the shop.
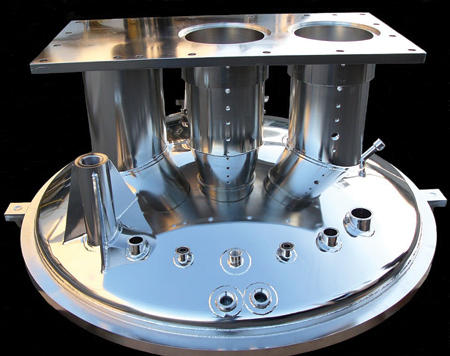
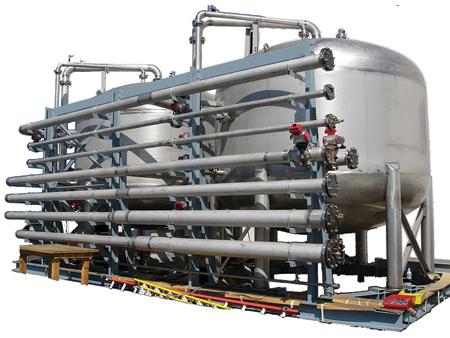
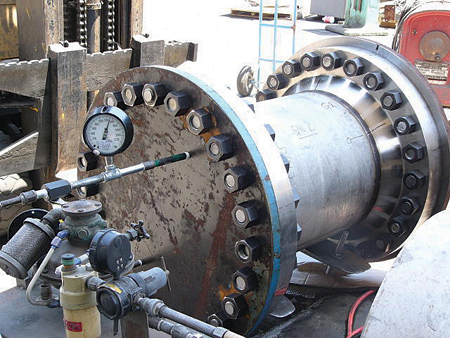
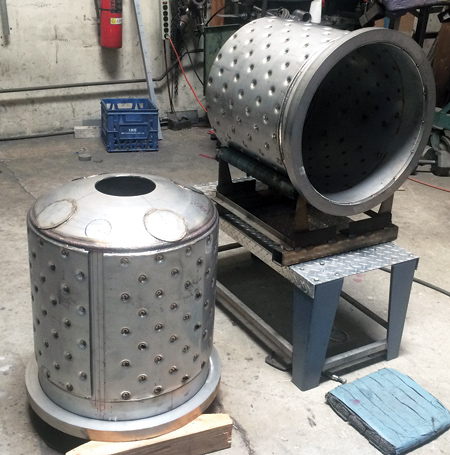
Royal's dimple jacketed stainless steel design for mixing tanks and reactors
Royal Welding & Fabricating prides itself on two basic tenets. As General Manger Wallace Cook explained, "We specialize in stainless steel and aluminum welding, often with mirror finish, plus we can offer complete turn-key operation for the highly challenging jobs, with design, engineering, most component production, all assembly, welding, grinding, fine finish and full testing capability, all in-house. That means customers can bring their jobs to us with complete confidence and know they will get quick response, should any changes be required." Cook also takes pride in the high quality of the products the company produces. He originated the company's slogan, "Where Quality is King."
In business over 50 years, this Los Angeles-area shop produces a wide assortment of tanks, mixers, chambers and extractors for myriad industrial, medical and commercial uses. All the welders are ASME certified and Royal conforms to all necessary standards for the aerospace, nuclear and other high-precision markets.
Royal produces units to withstand extreme pressures, high vacuum processing and high and low temperatures for hazardous chemical extraction processing, providing customers with often unique, application-specific designs. The company's dimpled plate designs, for example, are renowned for their superior heat dissipation and cost savings, and as an alternative to partial or full metal jacket heat exchangers. Royal also fabricates a variety of custom tube and shell heat exchangers, centrifugal pump vessels, agitators, autoclaves, hydroclaves, high-volume cooking kettles, high-pressure tanks for reverse osmosis, extreme environment vessels and vacuum chambers to all applicable ASME, TEMA and 3A standards. Units produced at Royal are in use for water conditioning on the space station.
The Royal customer list ranges from leading pharmaceutical and food companies to the aerospace, oil/gas and chemical industries, plus government concerns. The shop is becoming a leading supplier to emerging markets on the West Coast. Director of Engineering Brad Card said, "We have done everything from fusion reactors for particle acceleration to cleaning reactors for laundering (the legal kind) money, gel reactors for vitamin supplements, paint formulation tanks, vacuum chambers for paralyne coatings, environmental chambers for silicon wafer tests, vessels for dark matter research and fuel tanks for rocket launch vehicles."
All work begins in the design department, where the latest CAD technology produces designs for the various machine shop operations located in-house at Royal. These include metal bending, conventional chip-cutting machine tool work, forming and fabrication, final assembly and performance testing plus a key area of this shop, the grinding and finishing department. Every weld and surface finishing job at Royal is done to the highest quality specifications and the abrasives used must match the materials, job requirements and appearance standards set by the customer and by Royal.
A key partner in this latter department is the Abrasive Power Tool Division of Suhner. This supplier's local representative is Regional Sales Manager Gary Mergeanian, who has served Royal for over 25 years. As he observed, "Few customers present me with the daily challenges I get from Royal, but these are the moments that make doing business so rewarding. When I can bring a solution to the job at hand, whether it is a special abrasive pad or a full power tool assembly, it is exciting. The satisfaction of the Royal welding and finishing operator teams is my goal, and getting it is very important to me. Making the jobs easier and less fatiguing for these guys, while at the same time helping them produce the highest quality finish possible, is a challenge we at Suhner welcome." Mergeanian has worked for Suhner for over 30 years and brings a thorough knowledge of the company's tool and abrasive technologies to the team at Royal Welding.
One of the newer Suhner developments used on the job every day at Royal is the Roto family of products, where the motor drive, flex shaft and handheld adapter unit are integrated into a powerful and flexible tool package. By separating the weight of the motor and mechanical drive components from the hand tool, plus incorporating highly flexible adapters into the handheld unit, Suhner allows the operators much greater flexibility in performing their work. "Our operators have less fatigue and greater freedom of movement with these units, which allow long periods of work in tight spaces or inside large containment vessels," said Cook. "That is a real plus for the guys in the shop. And Suhner, through Gary Mergeanian, is always bringing us new and better ways to grind welds and finish surfaces on stainless and aluminum."
Belt and pad abrasive work can be done on the same tool using the Roto family, which further speeds the work at Royal. The shop recently built its own polishing machine set-up for internal tank head polishing using a variety of Suhner components.
Shop Supervisor Ricardo Guerrero said, "The tools are very good, easy to handle and the guys do not get worn out. We can do faster finishing with less abrasive, and that means money saved."
Mergeanian further noted, "We have taken feedback from the operators here at Royal and made specific changes in the design and manufacture of our tools in response. Since these guys are also working with stainless, high-performance aluminum alloys, heat-treated Inconel and other challenging materials, they have also provided valuable input for our abrasives engineering team at Suhner."
Sidebar
Dimple Jacket Design for Stainless Tanks and Reactors
More Insulation, Same Space
A unique feature of Royal Welding engineering is the company's dimple jacketed stainless steel design for mixing tanks and reactors. The jackets on such tanks can be ASME code stamped for high- or low-pressure service. Dimple jackets can be supplied as individually shaped units to install on existing equipment in a retrofit operation or as an OEM component.
According to General Manager Wallace Cook, "The dimple plate design is more efficient in promoting heat transfer through the tank wall, since the dimples generate turbulence in the flow through the jacket. Because of the low profile, more insulation can be used in the same space."
For more information contact:
Wallace Cook, General Manager
Royal Welding & Fabricating
1000 E. Elm Ave.
Fullerton, CA 92831
714-680-6669
info@royalwelding.com
www.royalwelding.com
Aaron Beck, General Manager
Suhner Industrial Products Corporation
Abrasive Power Tool Division
Hwy 411 S./Suhner Drive
P.O. Box 1234
Rome, GA 30162
706-235-8046
info.usa@suhner.com
www.suhner-abrasive-expert.com